PRODUCTS
Technology / product information
15hits
Narrow by Industry Category
Narrow by material Category
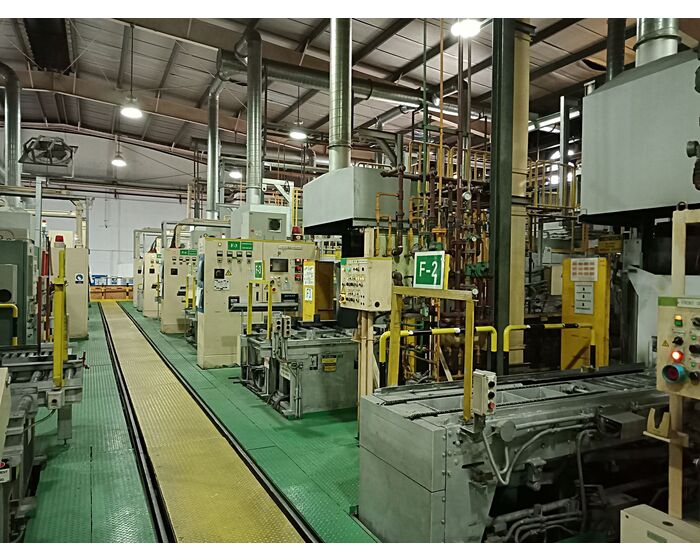
Metal Heat Treatment/Surface Treatment
DOWA Thermotech provides advanced heat treatment and surface treatment technologies to enhance the quality and performance of metal and stainless steel products. Through advanced processes such as quenching, tempering, and electropolishing, we optimize the properties of products. Our solutions are trusted across industries such as automotive, aerospace, construction, and medical devices. Additionally, we adopt energy-efficient and environmentally friendly technologies to support sustainable manufacturing. ■ Features Advanced Technology: Cutting-edge processing technologies to maximize the performance of metal materials. Customizable Solutions: Tailored processing to meet the specific requirements and applications of each industry. Quality Enhancement: Improves durability, corrosion resistance, and mechanical strength, extending product lifespan. Environmentally Friendly: Reduces energy consumption and employs low-impact processing methods. ■ Specifications Applicable Materials: All metals (with a focus on stainless steel) Heat Treatment Technologies: Quenching, tempering, annealing, normalizing, etc. Surface Treatment Technologies: Electropolishing, chemical polishing, coating formation, etc. Applicable Industries: Automotive, aerospace, construction, medical devices ■ Applications Automotive Components: Strengthening transmission gears and engine components. Aerospace Components: Processing specialized components that balance lightweight properties and durability. Medical Devices: Treating medical metal parts requiring high corrosion resistance and hygienic properties. Construction Materials: Treating structural materials for weather resistance and wear resistance. DOWA Thermotech's heat treatment and surface treatment technologies optimize the characteristics of metals and stainless steel, supporting advancements across all industries. ■ For more details, please contact us.
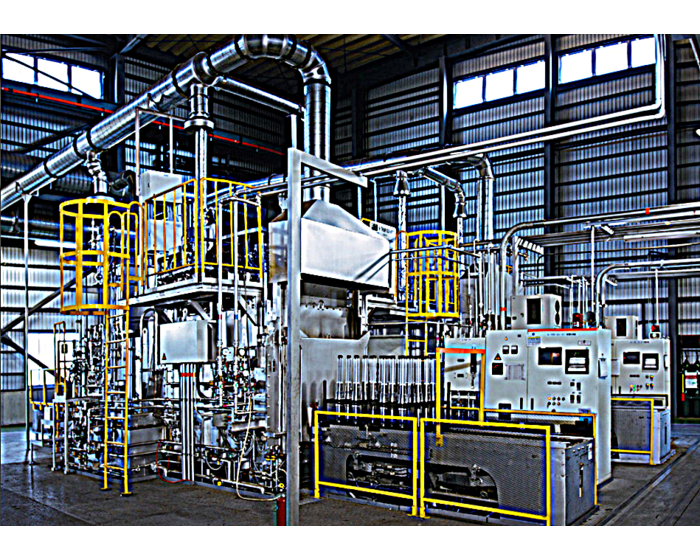
TKM Series Heat Treatment Furnace
The TKM Series heat treatment furnaces, developed by DOWA Thermotech, feature advanced energy-saving technologies and exceptional environmental performance. This series supports various heating methods such as carburizing furnaces, nitriding furnaces, and electric heating furnaces, making them suitable for a wide range of manufacturing industries, including automotive and industrial machinery parts. Notably, the TKM Series reduces CO2 emissions by over 30% compared to conventional models, promoting sustainable production processes. ■ Features Energy Efficiency: Incorporates high-efficiency regenerative gas burners to significantly reduce energy consumption. Environmental Consideration: New insulation structure lowers the furnace surface temperature and reduces CO2 emissions by more than 30%. Enhanced Productivity: Shortens total lead time by 20%, improving production efficiency. Versatility: Uniform heating, carburizing, and cooling performance cover a wide range of heat treatment processes. High Durability: Constructed with ceramic refractory materials for extended service life. ■ Specifications Model: TKM-40ERT to TKM-120ERT External Dimensions (mm): Length 6,980–9,500, Width 2,550–2,810, Height 3,460–4,310 Effective Furnace Dimensions (mm): Length 915–1,220, Width 510–760, Height 450–750 Operating Temperature: Up to 930°C Processing Capacity: Up to 820 kg per batch Heating Method: Gas heating Conveyance Method: Pusher type ■ Applications Automotive Industry: Carburizing treatments for engine and transmission components. Industrial Machinery Components: Precision heat treatment for bearings and gears. Aerospace Components: Surface treatments for weight reduction and durability improvements. Tool Manufacturing: Wear resistance enhancement for metal tools. The TKM Series achieves a balance between energy savings and high efficiency, supporting the optimization of your manufacturing processes. ■ For more details, please download the PDF or contact us.
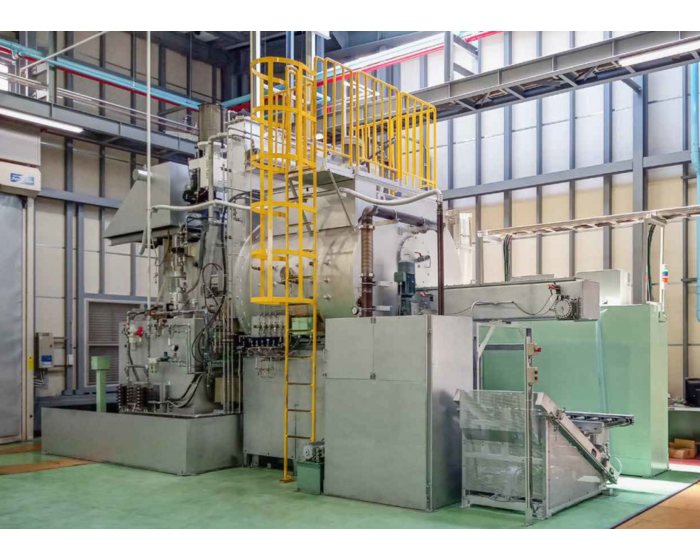
Z-TKM Series Next-generation Heat Treatment Furnace
The Z-TKM Series is a next-generation vacuum carburizing furnace developed by DOWA Thermotech. It retains the high-quality stability and cost efficiency of conventional atmospheric carburizing furnaces while achieving up to a 97% reduction in CO2 emissions within factories. Furthermore, by utilizing green energy, it is possible to reduce total CO2 emissions by over 60%. Designed to shorten lead times and enhance productivity, this furnace supports sustainable manufacturing practices that are essential in today's environmentally conscious era. ■ Features Environmentally Friendly Design: Reduces factory CO2 emissions by up to 97% and overall emissions by more than 60% with green energy compatibility. Improved Productivity: Significantly shortens lead times and increases space efficiency in production. Enhanced Safety: Flame-free design ensures intrinsic safety. High Compatibility: Fully compatible with the TKM Series, allowing for easy integration into existing production lines. Multiple Heat Source Options: Equipped with ammonia and hydrogen burners, enabling the use of green energy. ■ Specifications Maximum Tray Dimensions (mm): Width 760 × Length 1,230 × Height 720 Maximum Processing Weight: 720 kg Transport Method: Batch type, straight-through Maximum Temperature: 1,000°C Utilities Supported: Electricity, compressed air, cooling water, nitrogen gas, carburizing gas ■ Applications Automotive Parts Manufacturing: High-precision carburizing treatment for transmission gears and engine components. Aerospace Parts Manufacturing: Carburizing heat treatment for reducing the weight of components. Industrial Machinery Parts: Enhancing wear resistance for bearings and shafts. The Z-TKM Series combines environmental performance with productivity, supporting sustainable manufacturing. ■ For more information, please download the PDF or contact us.
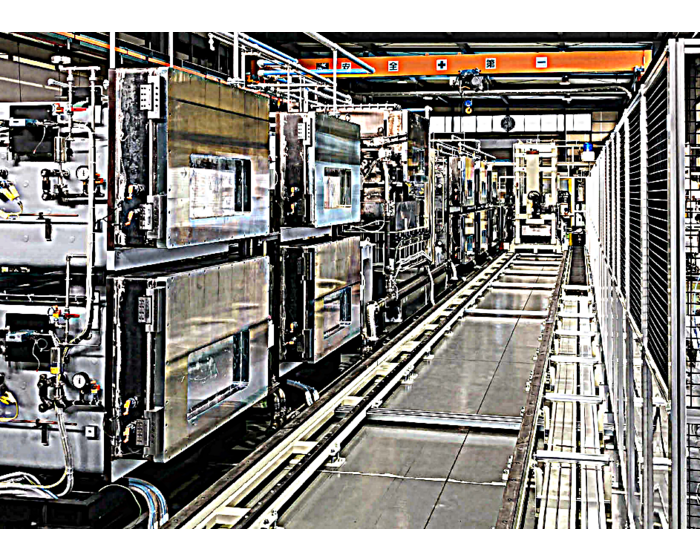
V-TKM Series Cellular in-line Heat Treatment Equipment
The "V-TKM Series" was developed in collaboration with Toyota Motor Corporation under the concept of "producing what is needed, when it is needed, and in the amount needed." This cell-type inline heat treatment system is optimized for small-batch production, achieving shorter lead times, improved quality, and reduced environmental impact. Capable of handling a wide range of processes such as sintering, carburizing, and brazing, it supports flexible operations as a next-generation heat treatment furnace. ■ Features Reduced Processing Time: Cuts lead time by 65%, significantly improving production efficiency. Environmentally Friendly: Reduces factory CO2 emissions by 97% and supports green energy use. High-Quality Production: Minimizes quality variation by 65%, making it ideal for small-batch production. Space-Saving Design: Reduces equipment space requirements by 47% compared to conventional systems. Fully Automated Transport: Fully automates vacuum-based transport, minimizing idle time losses. Versatility: In addition to carburizing, supports a variety of heat treatment processes, including sintering and brazing. Enhanced Safety: Flame-free design ensures a clean and safe working environment. ■ Specifications Maximum Tray Dimensions (mm): V-1: Width 200 × Length 300 × Height 50 (Max weight: 20 kg) V-2: Width 620 × Length 760 × Height 250 (Max weight: 120 kg) Transport Method: Automated cell-based transport Maximum Temperature: 1,100°C Quenching Methods: Oil quenching, gas quenching Utilities Supported: Electricity, compressed air, cooling water, nitrogen gas, carburizing gas ■ Applications Automotive Components: Carburizing and sintering treatments for transmission gears and engine components. Aerospace Components: Precision heat treatments for weight reduction. Industrial Machinery Components: Surface treatments for durable bearings and shafts. The "V-TKM Series" is the optimal solution for efficient and environmentally friendly production. ■ For more details, please download the PDF or contact us.
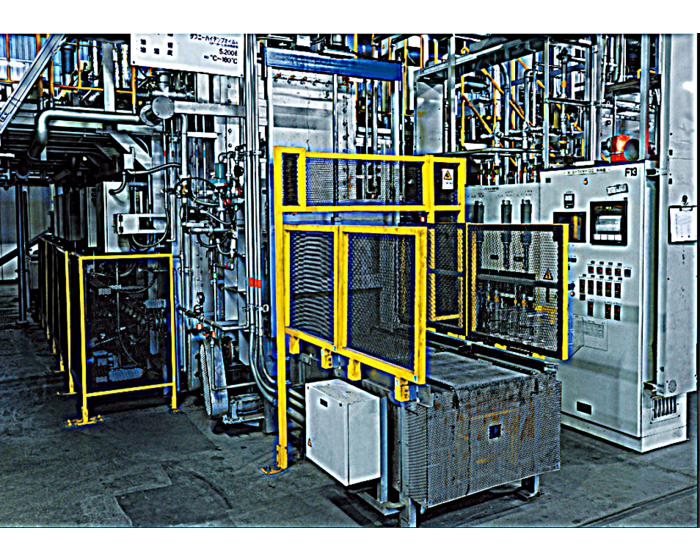
S-TKM Series Heat Treatment Furnace
The "S-TKM Series" is a next-generation continuous heat treatment furnace developed by DOWA Thermotech. This series achieves approximately three times the productivity of traditional batch furnaces while maintaining a space-saving design. It features high-performance regenerative gas burners and a new insulation structure that maximizes energy efficiency, reduces energy costs, and minimizes environmental impact. It is an optimal choice for heat treatment processes for automotive and mechanical components. ■ Features High Productivity: Achieves approximately three times the production output of conventional batch furnaces. Energy Efficiency: Significantly reduces heating energy costs with high-performance regenerative gas burners. Compact Design: Achieves space-saving installation with a new insulation structure. High-Temperature Capability: Enables uniform heating up to 930°C, supporting a wide range of heat treatment applications. Flexible Heating Methods: Compatible with both gas heating and electric heating. Enhanced Durability: Uses ceramic or brick refractory materials for longer operational life. ■ Specifications Models: STKM 80, STKM 100 External Dimensions (mm): Length 6876–6910, Width 2900–3000, Height 5074–6257 Effective Furnace Dimensions (mm): Length 3075 (615 × 5), Width 660–760, Height 600–720 Maximum Weight per Tray: Up to 360 kg Heating Methods: Gas heating or electric heating Conveyance System: Roller hearth ■ Applications Automotive Components: Carburizing processes for transmission gears, shafts, and more. Industrial Machinery Components: Wear-resistance enhancement for bearings and gears. Aerospace Components: Precision heat treatment for parts requiring high accuracy. The "S-TKM Series" is an ideal heat treatment furnace that combines enhanced production efficiency with environmental sustainability. ■ For more details, please download the PDF or feel free to contact us.
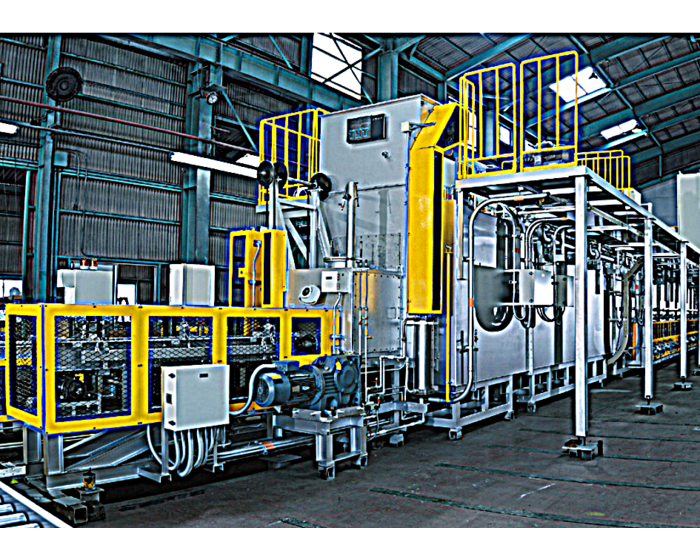
Hybrid type continuous gas carburizing furnace
The Hybrid Continuous Gas Carburizing Furnace is a world-standard continuous furnace developed by DOWA Thermotech. By combining the Trapezer system with the Roller Hearth system and incorporating high-performance regenerative gas burners in the heating zones, this furnace simultaneously achieves increased productivity and energy savings. It also features environmental performance that reduces CO2 emissions per unit weight by approximately 30% and contributes to space-saving in factories. With a significantly evolved design compared to traditional batch furnaces, it is capable of meeting diverse production needs. ■ Features Energy Efficiency: Reduces energy costs by approximately 40% with high-performance regenerative gas burners. CO2 Emission Reduction: Cuts CO2 emissions per unit weight by about 30%, minimizing environmental impact. Improved Productivity: Shortens furnace lead time by about 10%, enabling efficient production. Space-Saving Design: Reduces installation space by approximately 20% compared to conventional systems. Advanced Integrated Technology: A unique design that combines the Trapezer system and Roller Hearth system. ■ Specifications Heating Method: Electric or gas heating Conveyance System: Trapezer system, Roller Hearth system Refractory Material: Brick or ceramic Furnace Processes: Heating, carburizing/diffusion, quenching (oil tank) Environmental Performance: Significant reduction in CO2 emissions ■ Applications Automotive Parts: High-efficiency carburizing for transmission components and gears. Mechanical Parts: Surface strengthening of shafts and bearings. Aerospace Industry: Heat treatment for the production of lightweight, high-durability components. The Hybrid Continuous Gas Carburizing Furnace achieves both energy efficiency and environmental performance, supporting the manufacturing of the next generation. ■ For more details, please download the PDF or feel free to contact us.
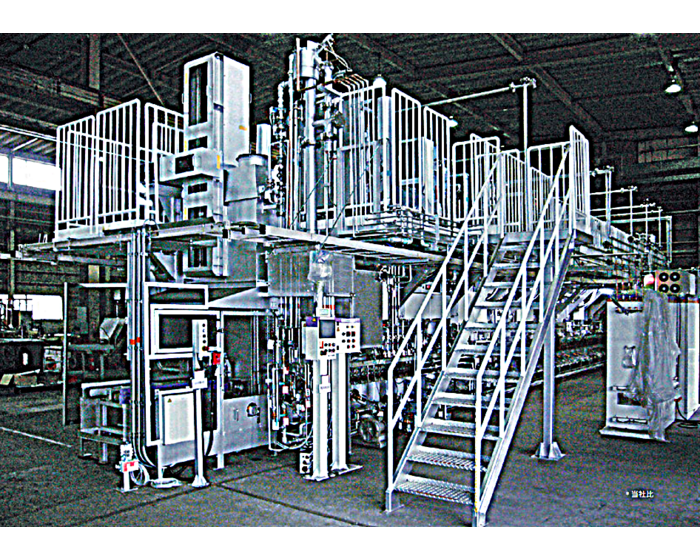
Roller Hearth Type Continuous High-Temperature Carburizing and Quenching Furnace
The Roller Hearth Type Continuous High-Temperature Carburizing and Quenching Furnace is a state-of-the-art continuous furnace offered by DOWA Thermotech. This furnace enables high-concentration carburizing with shorter carburizing times by utilizing uniform and rapid heating technology and minimized temperature distribution. Compared to conventional continuous furnaces, it significantly reduces lead time while simultaneously achieving cost reduction and high-quality heat treatment. It has received high acclaim, particularly in the manufacturing of automotive and precision machinery components. ■ Features Cost Reduction: Substantially lowers processing costs by reducing carburizing time. Uniform and Rapid Heating: Minimizes temperature distribution with high-capacity regenerative gas burners and high-flow agitation fans. High-Concentration Carburizing: Achieves quality equal to or better than traditional carburizing methods. Shortened Lead Time: Reduces in-furnace lead time by up to approximately 47%. Flexibility: Supports a wide range of processes, from high-temperature carburizing and diffusion to quenching. ■ Specifications Heating Method: Electric and gas heating Conveyance Method: Roller Hearth Refractory Material: Brick Supported Processes: Heating, carburizing/diffusion, quenching (oil bath) Lead Time: Reduces up to 53% compared to conventional continuous furnaces ■ Applications Automotive Parts: High-concentration carburizing for gears, shafts, and more. Precision Machinery Components: Surface treatment for components requiring durability. Aerospace Components: Heat treatment for lightweight, high-strength parts. The Roller Hearth Type Continuous High-Temperature Carburizing and Quenching Furnace is the optimal choice for facilities seeking cost reduction and efficient production. ■ For more details, please download the PDF or feel free to contact us.
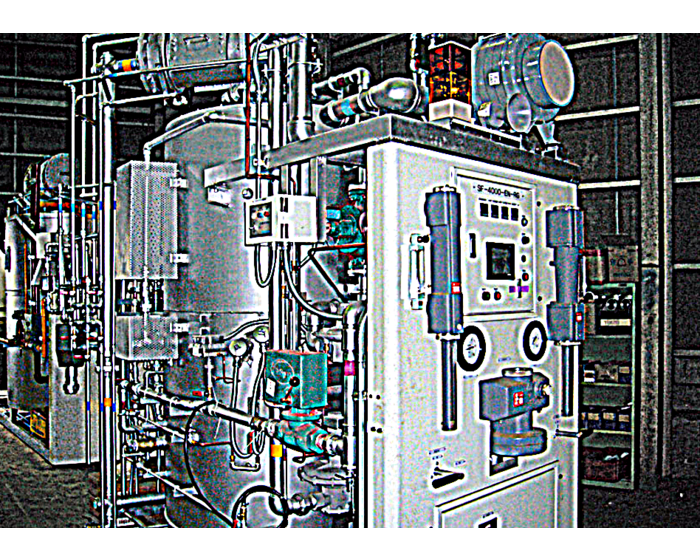
Soot Free Endothermic Gas Generator
The Soot Free Endothermic Gas Generator by DOWA Thermotech is an innovative product that significantly enhances environmental performance while requiring the same installation space as traditional electric-heated systems. This endothermic gas generator employs an efficient heating technology using swirl-type regenerative burners, effectively preventing soot generation. Additionally, it achieves reductions in CO2 emissions and energy costs. The incorporation of new mechanisms, such as a double-pass retort system and a pulseless blower, supports sustainable production processes. ■ Features Zero Soot Generation: The soot-free design prevents soot buildup almost entirely, eliminating the need for burn-out cleaning. CO2 Reduction: Reduces CO2 emissions to minimize environmental impact. Energy Efficiency: The swirl-type regenerative burner significantly lowers the cost of generating endothermic gas. Flexibility: Compatible with both gas and electric heating, adaptable to diverse installation environments. New Mechanisms: Features such as the double-pass retort system and specialized heating technology ensure high-efficiency operation. ■ Specifications Endothermic Gas Generation Capacity: 56–112 m³/h Raw Gas Types: 13A gas, propane, butane Combustion Gas Types: Also supports 13A gas, propane, and butane External Dimensions: Width 1162 mm, Depth 2480 mm, Height 3210 mm (same size for electric-heated models) Operating Temperature: Up to 1080°C ■ Applications Automotive Parts Manufacturing: Supplies endothermic gas for carburizing and quenching. Precision Machinery Processing: Provides uniform gas for surface treatment. Heat Treatment Equipment: Ensures stable gas supply for carburizing and diffusion processes. The Soot Free Endothermic Gas Generator is an optimal solution for manufacturing processes focused on environmental sustainability and operational efficiency. ■ For more details, please download the PDF or feel free to contact us.
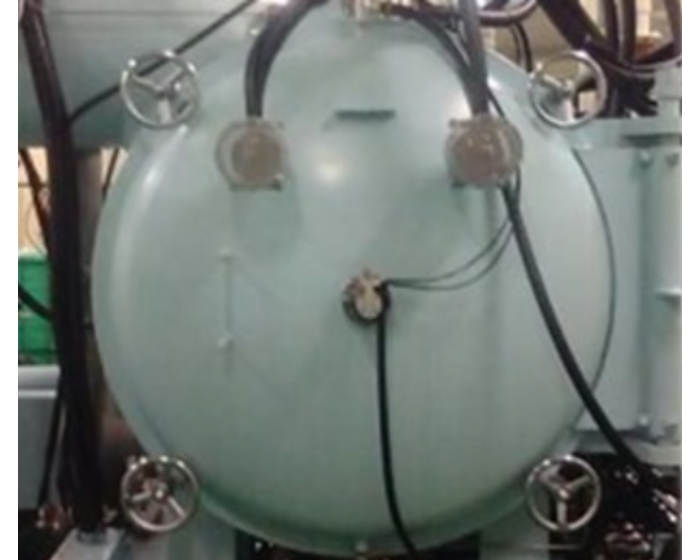
Metal Hot Zone High Temperature Vacuum Furnace
The Metal Hot Zone High-Temperature Vacuum Furnace by DOWA Thermotech is a high-precision heat treatment device designed for firing non-oxide fine ceramics. It resolves the carbon contamination issues caused by traditional graphite hot zones, enabling the production of high-purity products. Additionally, it supports operations in vacuum environments up to 2200°C and hydrogen atmospheres up to 1800°C, ensuring uniform temperature distribution for high-quality firing and sintering. This furnace is widely utilized in brazing and processing special ceramics as well. ■ Features High-Temperature Capability: Stable operation in vacuum environments at 2200°C and hydrogen atmospheres at 1800°C. Zero Carbon Contamination: Incorporates a metal hot zone to prevent carbon contamination of products. Uniform Heating: High-precision temperature distribution design ensures even heating throughout the product. Automatic Operation: Standard-equipped with fully automatic programmable operation. Reduced Maintenance Costs: Designed to minimize deformation and wear of the hot zone, reducing operational costs. Moist Atmosphere Compatibility: Flexible operation under special conditions for firing and sintering. ■ Specifications Maximum Temperature: 2200°C in vacuum, 1800°C in hydrogen atmosphere Effective Dimensions (mm): Model 1: Width 200 × Length 500 × Height 200 Model 2: Width 300 × Length 300 × Height 300 Model 3: Width 300 × Length 600 × Height 300 Processing Capacity: Up to 100–400 kg (varies by model) ■ Applications Fine Ceramics: Firing and sintering high-purity ceramics. Brazing: Ideal for high-precision brazing processes. Special Component Processing: High-temperature treatment and processing of non-oxide materials. The Metal Hot Zone High-Temperature Vacuum Furnace is the ideal device for contributing to next-generation precision heat treatment processes. ■ For more details, please contact us.
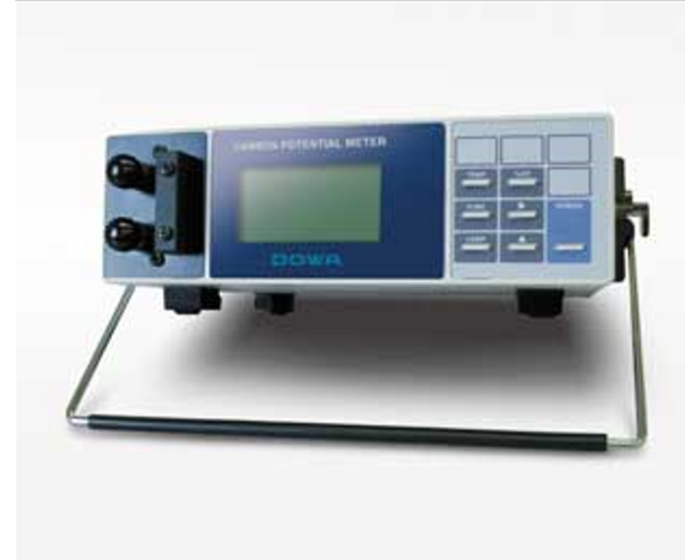
Carbon Potential Meter Rayong Thailand
The "CP Meter" is an instrument designed to accurately measure the carbon concentration in atmospheric gases during steel heat treatment processes (such as carburizing and tempering). With excellent operability and simple procedures, it ensures reliable measurement, streamlining the management of heat treatment processes. This advanced measuring device offers stable measurement accuracy and durability, making it ideal for on-site use. ■ Features Direct Measurement: Directly measures carbon concentration in atmospheric gases and displays results immediately. High Precision: Ensures strict management of heat treatment processes with high measurement accuracy. Easy Operation: User-friendly design enables intuitive operation. Durability: Robust design suitable for factory environments. Versatility: Applicable to various heat treatment processes such as carburizing, tempering, and annealing. ■ Specifications Measurement Target: Carbon concentration in atmospheric gases for heat treatment Applicable Processes: Carburizing, tempering, annealing, etc. Display Method: Digital display for real-time measurement results Installation Environment: Compatible with continuous use in factory settings ■ Applications Heat Treatment Process Management: Stabilizes product quality by measuring carbon concentration during carburizing and tempering processes. Product Accuracy Improvement: Ensures uniformity of products through high-precision measurements. Efficient Operation: Instantly retrieves measurement results, accelerating process adjustments. The "CP Meter" is the ideal solution for efficient carbon concentration management in steel heat treatment environments. ■ For more details, please contact us.
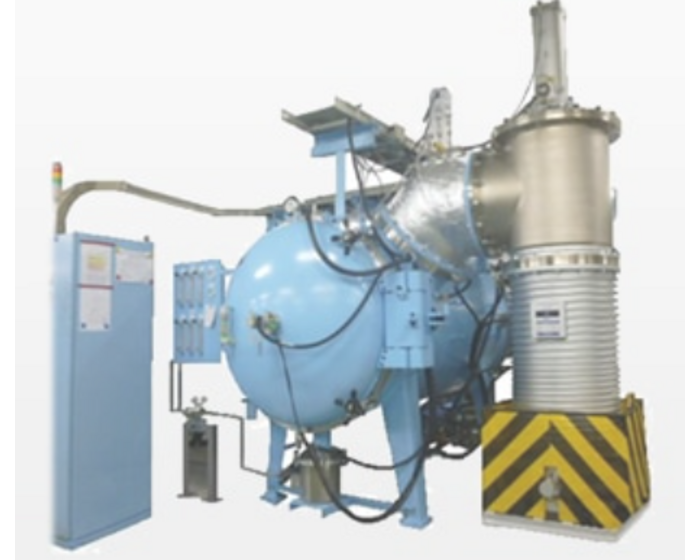
High Temperature Vacuum Degreasing Sintering Furnace
This High Temperature Vacuum Degreasing Sintering Furnace enables continuous processing from degreasing to pre-sintering and main sintering within the same batch. It supports a variety of atmospheres, including vacuum, inert gases like argon and nitrogen, and hydrogen environments, ensuring high-quality sintering. Featuring an energy-efficient heating chamber capable of uniform heating and a forced cooling mechanism, the furnace is optimized for a wide range of materials and applications. It accommodates structural fine ceramics, cemented carbides, high-speed powder steels, and more. ■ Key Features Multi-Environment Compatibility: Supports high-temperature sintering in vacuum, hydrogen, and inert gas atmospheres. Continuous Processing: Streamlined system processes from degreasing to sintering, improving work efficiency. Uniform Heating: Minimizes temperature distribution for consistent heating across the entire product. Forced Cooling Mechanism: Enables rapid cooling with high-speed blowers and heat exchangers. Advanced Control: Fine vacuum adjustment using partial pressure control. Safety Design: Equipped with standard safety mechanisms for hydrogen introduction. ■ Specifications Maximum Temperature: Vacuum: Up to 2,200°C Hydrogen Atmosphere: Up to 1,800°C Compatible Materials: High-speed powder steel, high-alloy steel, cemented carbides, structural fine ceramics Heating Method: Metal or graphite hot zone with 2-side, 4-side, or 6-side heating ■ Applications Powder Metallurgy: Sintering of MIM and CIM products Ceramic Processing: Firing of high-purity structural fine ceramics Tool Manufacturing: Heat treatment of high-hardness high-speed steel and cemented carbides The High Temperature Vacuum Degreasing Sintering Furnace is a reliable solution for versatile material processing and efficient production. ■ For more details, please download the PDF or contact us.
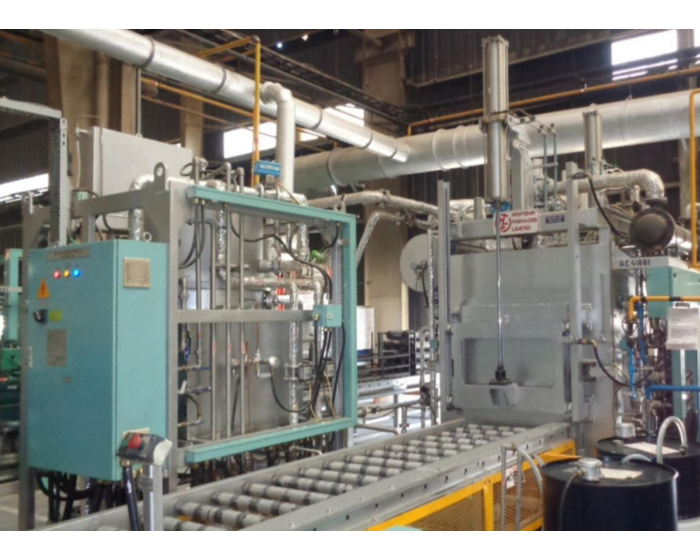
Vacuum Washer
The Vacuum Washer is manufactured at DOWA Thermotech's facility in India, delivering a cost-effective design while maintaining Japan’s high-quality standards. This equipment combines vacuum drying, vapor cleaning, and endless shower cleaning to efficiently clean parts with complex shapes. Additionally, its recycling system significantly reduces cleaning liquid consumption, thereby lowering operating costs. The machine also emphasizes safety by utilizing indirect heating to minimize fire risks and a simple structure to reduce potential operational issues. ■ Features Cost-effective Design: Cost savings through production in India and efficient operations. High-Quality Cleaning: Combines vapor cleaning and endless shower cleaning for superior performance. Energy-saving and Eco-friendly: Recycling system recovers over 99% of waste liquid. Safety: Indirect heating and a simple structure reduce fire risks and operational problems. Versatility: Designed for cleaning complex shapes and high-precision parts. ■ Specifications External Dimensions (mm): 80 Type: 3,650H × 2,600W × 8,240L 100 Type: 4,140H × 2,810W × 8,810L Effective Dimensions (mm): 80 Type: 600H × 660W × 1,230L 100 Type: 650H × 760W × 1,230L Maximum Processing Capacity: 80 Type: 550kg 100 Type: 720kg Cycle Time: 27±3 minutes Recycling Capacity: 300L/hour ■ Applications Automotive Part Cleaning: High-precision cleaning of engine and transmission components. Precision Machinery Parts: Surface cleaning of bearings and gears. Mold Cleaning: Removing contaminants and finishing surfaces of complex-shaped parts. The Vacuum Washer is designed to meet the cleaning needs of various industries with a focus on safety and cost efficiency. ■ For more details, please download the PDF or contact us.
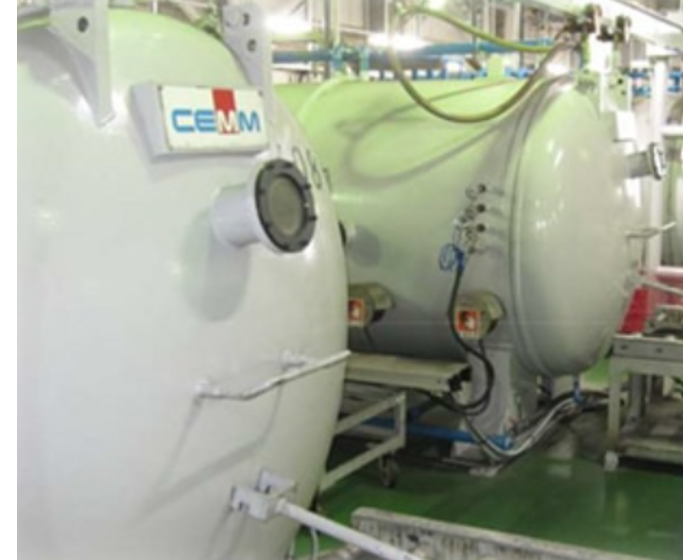
Horizontal Plasma Nitriding Furnace
The Horizontal Plasma Nitriding Furnace is a horizontal heat treatment furnace equipped with advanced plasma nitriding technology from DOWA Thermotech. It enables stable nitriding in low vacuum conditions (below 60 Pa) and achieves high-precision processing of entire parts through uniform temperature distribution. Despite its compact design, it is capable of handling large components, making it ideal for various industrial applications, including automotive parts and precision machined components. ■ Features High-Precision Nitriding: Achieves uniform surface hardening through plasma technology in a vacuum environment. Wide Temperature Range: Supports diverse materials with a temperature range of 350–570℃ (maximum 600℃). Large Component Handling: Offers effective heating dimensions up to 900mm diameter × 1500mm length. Low Vacuum Operation: Stable operation at a vacuum level of <60 Pa (0.5 Torr). Space-Saving Design: Horizontal layout optimizes installation space. High Durability: Features a robust furnace body and state-of-the-art control technology. ■ Specifications Vacuum Level: <60 Pa (0.5 Torr) Standard Processing Temperature: 350–570℃ (maximum 600℃) Effective Heating Dimensions (mm): DPN-5065: Φ500 × length 650 DPN-9150: Φ900 × length 1500 Maximum Load Capacity: DPN-5065: 600kg DPN-9150: 1000kg Installation Space (mm): DPN-5065: 2300W × 5350L × 3714H DPN-9150: 3080W × 4555L × 5100H ■ Applications Automotive Components: Surface hardening for gears, shafts, and bearings. Precision Machinery Parts: Nitriding of metal components requiring high durability. Aerospace Industry: Enhancing wear resistance and surface hardening of lightweight components. The Horizontal Plasma Nitriding Furnace provides the ideal solution for industries requiring high-precision surface treatment. ■ For more details, please download the PDF or contact us.
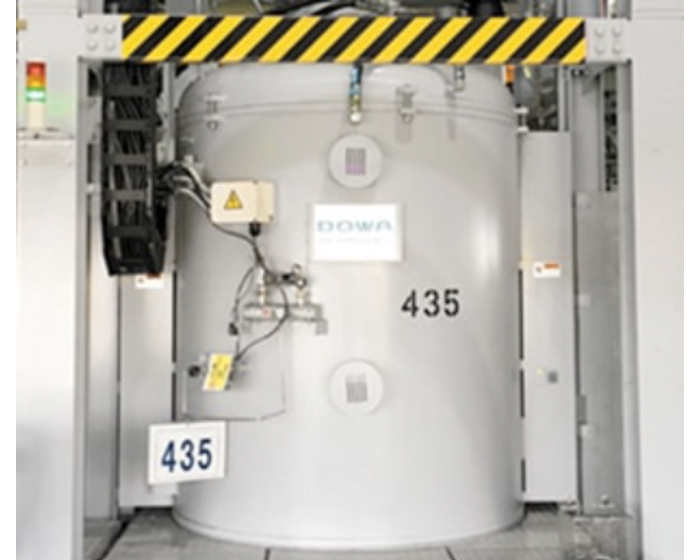
Vertical Plasma Nitriding Furnace
The Vertical Plasma Nitriding Furnace is a product that significantly enhances heating and cooling efficiency compared to conventional plasma nitriding furnaces. With built-in heaters enabling precise temperature zone control, it ensures uniform nitriding even for large or complex-shaped components. Its design prevents glow discharge from room temperature, reducing abnormal discharges (arcing) and stabilizing quality. This furnace is suitable for a wide range of applications, including automotive and aerospace components. ■ Features Reduction of Abnormal Discharges: Designed to prevent glow discharge from room temperature, minimizing arcing. Uniform Processing: Temperature zone control ensures stable quality without uneven treatment. High-Efficiency Operation: Built-in heaters shorten heating time, improving efficiency by up to 47% (compared to previous models). Energy Efficiency: Insulated with reflective panels, reducing energy consumption by 20% compared to conventional models. Versatile Applications: Allows mixed processing of components with varying masses and shapes. Rapid Cooling: Equipped with in-furnace cooling fans and heat exchangers to reduce cooling time. ■ Specifications Vacuum Level: <60 Pa (0.5 Torr) Standard Processing Temperature: 350–570℃ (maximum 600℃) Effective Heating Dimensions (mm): DPN-5065: Φ500 × height 650 DPN-9150: Φ900 × height 1500 DPN-13200: Φ1300 × height 2000 Maximum Load Capacity: DPN-5065: 600kg DPN-9150: 1000kg DPN-13200: 2000kg Installation Space (mm): DPN-5065: 2300W × 5350L × 3714H DPN-9150: 3080W × 4555L × 5100H DPN-13200: 3400W × 7720L × 5600H ■ Applications Automotive Components: Enhancing wear resistance for gears, shafts, and bearings. Aerospace Components: Surface hardening of high-precision parts. Precision Machinery Parts: Uniform nitriding of components with complex shapes. The Vertical Plasma Nitriding Furnace is an ideal heat treatment solution that combines reliable processing with energy efficiency. ■ For more details, please download the PDF or contact us.
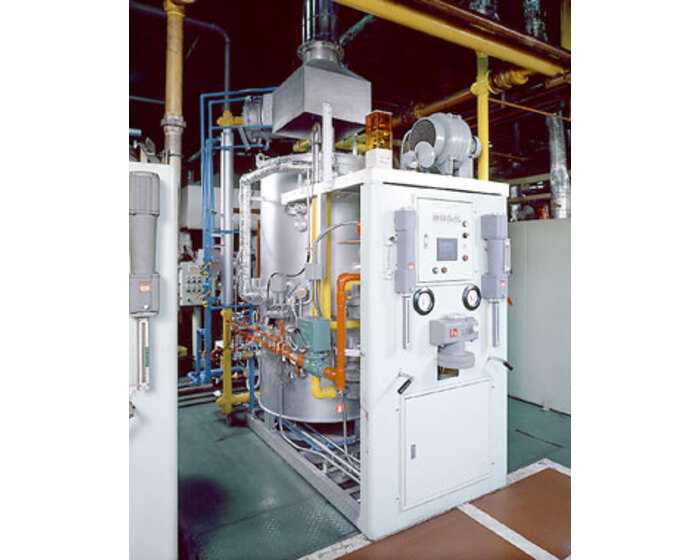
Industrial Furnaces
Industrial Furnaces are a range of products designed to enhance the efficiency and quality of heat treatment processes. These furnaces incorporate innovative technologies across the entire heat treatment process, from body design and heating structures to in-furnace transportation systems and auxiliary equipment. While focusing on energy efficiency and reducing environmental impact, they also achieve shorter processing times and space-saving designs. Furthermore, the furnaces can be customized to meet individual customer needs, offering a diverse lineup to support a wide range of industries. ■ Features Diverse Product Lineup: Offers a variety of industrial furnaces tailored to different heat treatment processes. Energy-Efficient Design: Incorporates high-efficiency heating structures and insulation technologies to reduce energy consumption. Reduced Environmental Impact: Achieves lower CO2 emissions and minimal waste generation. Faster Processing: Shortens heating and processing times, improving productivity. Space-Saving Design: Compact layouts optimized for installation areas. Customizable: Adaptable specifications for special materials and applications. ■ Applications Automotive Industry: Quenching and tempering of engine components and transmission gears. Aerospace Industry: Heat treatment and durability enhancement of lightweight components. Precision Machinery: Sintering and nitriding of high-precision parts. Tool Manufacturing: Hardening and surface treatment to improve wear resistance. ■ Examples of Technological Innovations High-Efficiency Regenerative Gas Burners: Significantly reduce energy costs. Fully Automated Transportation Systems: Enhance operational efficiency and reduce defect rates. Environmentally Friendly Design: Utilize low-NOx combustion technology. The Industrial Furnaces provide high-quality and efficient heat treatment solutions tailored to meet customer needs. ■ For more details, please contact us.
CONTACT