SERVICE
Production Goods & Services
3hits
Narrow by category
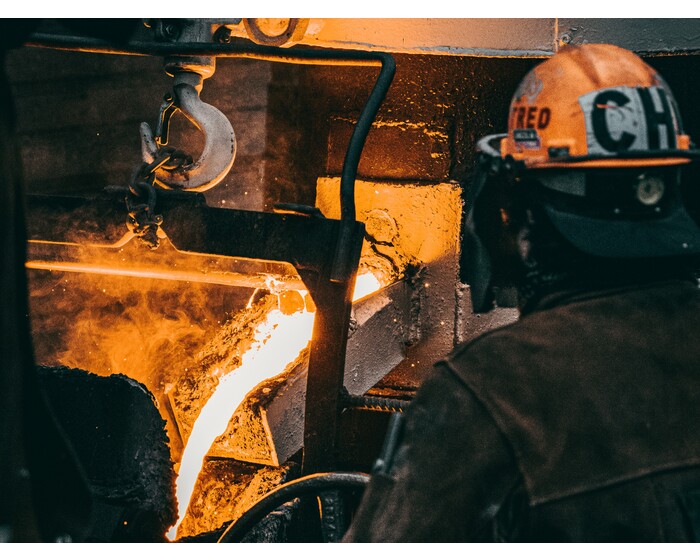
Understanding Heat Treatment: Types, Processes, and Applications
Heat treatment is a controlled process used to alter the physical and sometimes chemical properties of metals and alloys. By heating and cooling materials in a controlled manner, heat treatment enhances hardness, strength, ductility, and wear resistance. This process is widely used in manufacturing industries such as automotive, aerospace, toolmaking, and construction. 1. Types of Heat Treatment Heat treatment can be categorized into several types, each serving a unique purpose: 1.1 Annealing Annealing involves heating metal to a specific temperature and then cooling it slowly. This process: - Reduces hardness and improves ductility - Enhances machinability - Relieves internal stresses caused by machining or welding Common applications: Steel manufacturing, copper processing, and aluminum forming. 1.2 Normalizing Normalizing is similar to annealing but involves air cooling instead of slow cooling. It: - Refines grain structure - Improves toughness and strength - Reduces internal stresses Used in structural steel, railway tracks, and automotive components. 1.3 Hardening (Quenching) Quenching involves heating metal to a high temperature and rapidly cooling it in water, oil, or air. This results in: - Increased hardness and strength - Reduced ductility - Formation of a martensitic structure Common in tools, blades, and gears. 1.4 Tempering Tempering is performed after quenching to reduce brittleness. The process involves reheating the hardened metal to a lower temperature and then cooling it gradually. It: - Restores some ductility - Improves toughness - Reduces residual stress Essential for applications requiring both hardness and flexibility, such as springs and cutting tools. 1.5 Case Hardening (Surface Hardening) This method hardens only the surface of the metal while keeping the core soft. Techniques include: - Carburizing (introducing carbon into the surface) - Nitriding (introducing nitrogen) - Induction hardening (using electromagnetic fields) Used in automotive gears, bearings, and camshafts. 2. Heat Treatment Processes Each heat treatment type involves precise steps: 2.1 Heating The metal is heated to a specific temperature based on its composition and the desired property change. Proper heating prevents overheating or grain growth. 2.2 Holding (Soaking) Once the desired temperature is reached, the material is held at that temperature for a specific time. This allows atomic diffusion to occur, leading to structural changes. 2.3 Cooling Cooling can be done slowly (furnace cooling, air cooling) or rapidly (quenching in oil, water, or gas). The cooling rate determines the final properties of the metal. 3. Applications of Heat Treatment Heat treatment is essential in various industries: 3.1 Automotive Industry - Hardening of engine components like crankshafts and camshafts - Case hardening of transmission gears for durability - Tempering of suspension springs for flexibility 3.2 Aerospace Industry - Heat-treated turbine blades to withstand high temperatures - Strengthened landing gear components - Lightweight yet durable aluminum alloys 3.3 Tool and Die Making - Hardening of cutting tools like drill bits and saw blades - Surface hardening of molds for prolonged lifespan 3.4 Construction and Infrastructure - Reinforcement of steel beams for high-rise buildings - Normalized steel in bridges and railway tracks 4. Choosing the Right Heat Treatment Process Selecting the right heat treatment process depends on: - The material type (steel, aluminum, titanium, etc.) - The desired mechanical properties (hardness, toughness, flexibility) - The end-use application (automotive, aerospace, tools) Proper heat treatment enhances product performance, reduces failure rates, and extends the lifespan of components. Recommended Solution: Dowa Thermotech Heat Treatment Services For high-precision and reliable heat treatment solutions, Dowa Thermotech offers advanced thermal processing technologies. Our expertise in quenching, tempering, and case hardening ensures optimal material performance for various industries.
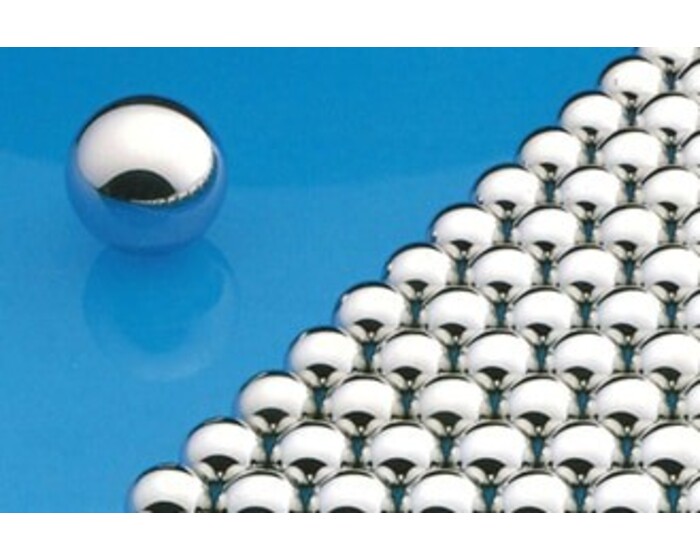
What is Shot Peening? A Surface Enhancement Technique to Improve Fatigue Strength
Shot peening is an industrial technology designed to enhance the structural strength of metal components by precisely applying controlled force to the surface. What is Shot Peening? Shot peening is a surface treatment process that improves metal surfaces by bombarding them with small spherical media such as steel shot or ceramic beads ("shots") at high velocity. This impact creates residual compressive stress in the surface layer of the metal, significantly improving its fatigue strength and wear resistance. This technique is commonly applied to components subject to cyclic loads—like those in aerospace, automotive, heavy machinery, and precision equipment—to extend their service life. Basic Principle of Shot Peening In this process, shot media are propelled at high speeds using compressed air or mechanical force, causing localized plastic deformation on the metal surface. The repeated impacts generate residual compressive stresses that counteract tensile stresses, reducing the likelihood of fatigue cracks and enhancing the component’s durability. Applications and Benefits Shot peening is widely used in various industries, such as: - Aerospace components (e.g., turbine blades, gears): Reduces fatigue from repetitive loading, significantly extending service life - Automotive parts (e.g., suspension springs, crankshafts): Increases fatigue strength and resistance to vibration-induced wear - Medical devices and precision machinery: Minimizes the risk of fractures and surface wear by precisely managing surface stress When properly optimized, shot peening can extend component lifespan by 1.5 to 2 times, offering greater design flexibility and improved safety. Process Conditions and Impact on Quality The effectiveness of shot peening depends on various parameters: - Shot material: Steel, stainless steel, ceramic, or glass—selected based on the application - Shot size: Smaller media produce smoother surfaces but shallower compressive layers - Peening intensity (Almen Intensity): Measured using an Almen strip to ensure processing quality Fine-tuning these parameters enables manufacturers to achieve the desired performance characteristics efficiently.
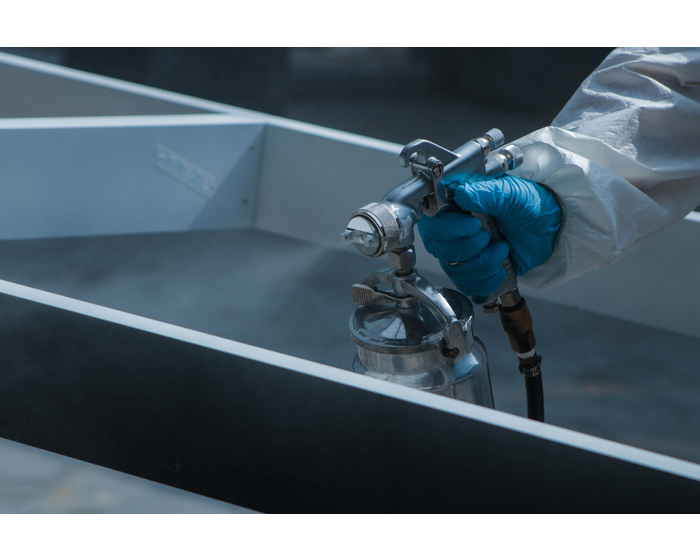
What is Metal Surface Coating? Protection, Enhancement, and Extended Lifespan for Metal Components
Metal Surface Coating is a process used to enhance the properties of metal, such as corrosion resistance, wear resistance, hardness, or even aesthetics. Coating can be applied in various ways, including plating, painting, chemical coating, or advanced technologies like thermal spray and PVD/CVD coatings. ■ Objectives of Metal Surface Coating - Enhance resistance to rust and corrosion - Improve hardness and resistance to friction - Add special properties such as heat resistance or non-stick surfaces - Improve appearance or for identification purposes - Reduce buildup of dirt or bacteria (especially in food/medical industries) ■ Popular Types of Metal Surface Coating - Galvanizing: Excellent rust protection, ideal for outdoor structures - Industrial Painting: Adds durability and color - Electroplating: Includes nickel or chrome plating for added strength and shine - Thermal Spray Coating: Used for high-durability parts like blades and pumps - PVD/CVD Coating: Suitable for precision components like molds and dies ■ Industries That Commonly Use Metal Coating - Automotive and auto parts industry - Mold and machinery industry - Aerospace industry - Electronics industry - Food and pharmaceutical industry ■ How to Choose the Right Coating Method Choosing the right coating method depends on several factors, such as: - The material of the component (steel, stainless steel, aluminum, etc.) - The working environment (indoor/outdoor, humidity, chemical exposure) - Aesthetic requirements or other specific functionalities - Budget and production volume Metal surface coating plays a crucial role in extending the service life of metal parts, reducing maintenance costs, and improving overall product quality.
CONTACT