PRODUCTS
Technology / product information
20hits
Narrow by Industry Category
Narrow by material Category
Narrow by accuracy
Narrow by lot number
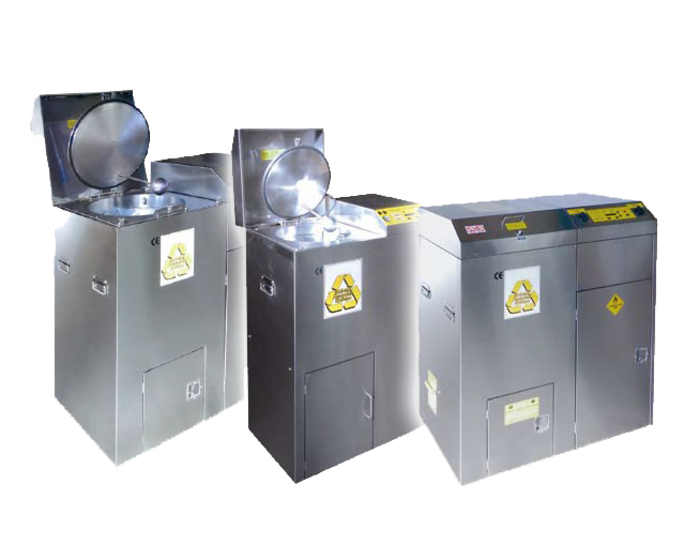
What is an automatic solvent recycler? The secret to effective solvent reuse
■ What is an Automatic Solvent Recycler? An automatic solvent recycler is a device that efficiently regenerates used solvents, returning them to a reusable state. It is widely used across various industries to reduce environmental impact and lower operational costs by enabling solvent reuse. ■ Regenerable Solvents This advanced device supports the regeneration of various solvents, including: - Hydrocarbon Solvents: Toluene, Xylene, Solvent naphtha, Normal hexane, Isohexane - Alcohol-Based Solvents: Methanol, Ethanol, Butanol, Isopropyl alcohol (IPA) - Ketone-Based Solvents: Acetone, Methyl ethyl ketone (MEK), Methyl isobutyl ketone (MIBK) - Ester-Based Solvents: Ethyl acetate, Butyl acetate, Methoxybutyl acetate, Normal propyl acetate - Halogen-Based, Fluorine-Based, and Chlorine-Based Solvents This flexibility ensures suitability for a wide range of industrial applications. ■ How It Works The solvent recycler utilizes a combination of distillation and purification technologies: - Heating and Vaporization: Solvents are heated and vaporized. - Cooling and Reliquefaction: The vaporized solvents are cooled and condensed back into liquid form. - Impurity Removal: The process eliminates impurities, resulting in high-purity, reusable solvents. This method maximizes efficiency and resource utilization. ■ Benefits of Implementation - Cost Efficiency: Reduces frequent purchases of new solvents. - Environmental Impact Reduction: Minimizes waste solvent discharge. - Resource Optimization: Promotes effective resource reuse. - Regulatory Compliance: Facilitates adherence to waste disposal regulations. ■ Why Choose Morikawa? Morikawa's automatic solvent recycler integrates state-of-the-art technology to ensure high regeneration efficiency. It is compatible with a variety of solvents and serves diverse industry needs. By balancing environmental sustainability with cost efficiency, it is the ideal solution for forward-thinking businesses. In addition, Morikawa also supports sales within Thailand. Our distributor, T.I.T. ELECTRONICS CO., LTD., provides nationwide service from its base in Bangkok, ensuring prompt support. For further details, please download the PDF or contact us directly.
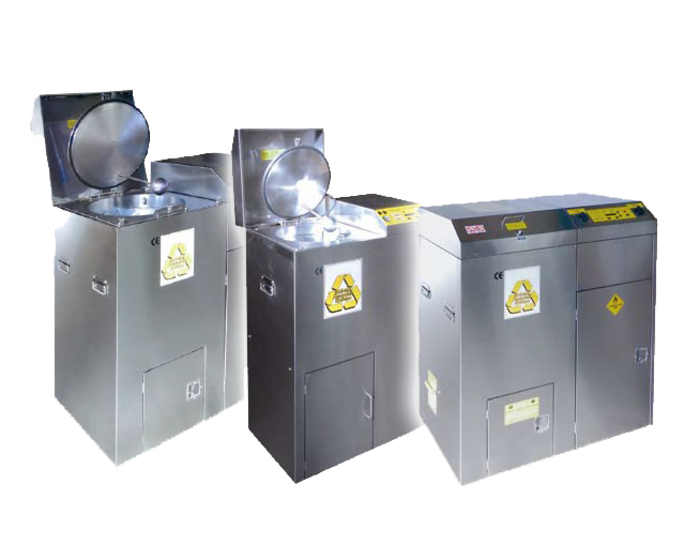
Main uses and scope of application of automatic solvent regeneration equipment
■ What is Automatic Solvent Regeneration Equipment? Automatic solvent regeneration equipment is designed to restore used solvents to a reusable state. This eliminates the need to purchase new solvents, significantly reducing costs. Additionally, it minimizes waste solvent generation, reducing environmental impact, and contributes to sustainable business practices. ■ Applications in the Chemical Industry In the chemical industry, solvents play a critical role in various processes, and their regeneration is a key challenge. Automatic solvent regeneration equipment addresses this challenge in the following ways: - Regeneration of Reaction Solvents: Reusing solvents from chemical reactions can result in substantial cost savings. - Reuse of Cleaning Solvents: Solvents used for cleaning equipment and pipelines can be regenerated and reused. - Reuse of Extraction Solvents: By regenerating solvents used in extraction processes, material costs can be significantly reduced. ■ Applications in the Manufacturing Industry Automatic solvent regeneration equipment is widely utilized in the manufacturing sector for a variety of purposes: - Cleaning of Metal Parts: Regenerating solvents used in cleaning metal components can lower cleaning costs. - Solvent Regeneration in the Painting Process: Restoring used solvents from painting processes reduces both costs and environmental impact. - Plastic Manufacturing: Solvents used in the production of plastic goods can be regenerated and reused efficiently. ■ Use in the Printing Industry Automatic solvent regeneration equipment also serves important functions in the printing industry: - Printing Machine Cleaning: Regenerated solvents used for cleaning printing machines help to reduce cleaning costs. - Ink Solvent Reuse: Ink solvents from printing processes can be restored and reused, leading to material cost savings. - Plate Cleaning: Solvents for cleaning printing plates can be regenerated, reducing associated cleaning costs. ■ Why Choose Morikawa Sangyo's Automatic Solvent Regeneration Equipment? - Highly Efficient Regeneration: Advanced technology ensures exceptional solvent regeneration efficiency. - Easy Operation: Automated systems are user-friendly and require minimal maintenance. - Environmental Protection: Substantially reduces waste generation and environmental impact. - Proven Reliability: Trusted by numerous companies, with an extensive track record of successful implementation. In addition, Morikawa also supports sales within Thailand. Our distributor, T.I.T. ELECTRONICS CO., LTD., provides nationwide service from its base in Bangkok, ensuring prompt support. For more details, please download the PDF or contact us directly.
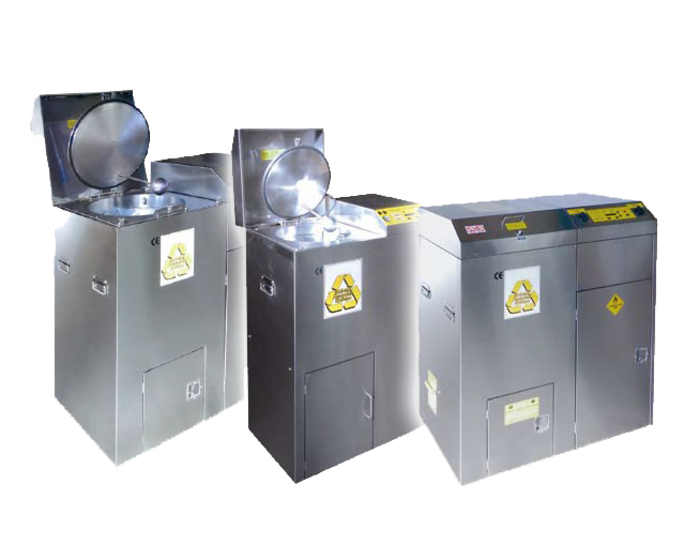
Cost Reduction Effects of Automatic Solvent Recycling Equipment
Implementing automatic solvent recycling equipment can reduce waste solvent treatment costs and achieve sustainable management. ■ What is Automatic Solvent Recycling Equipment? Automatic solvent recycling equipment is a device that regenerates used solvents to a reusable state. Industries such as chemical, manufacturing, and printing use large amounts of solvents, and the cost of processing them is a burden on businesses. By introducing automatic solvent recycling equipment, it is possible to reduce the amount of waste, contribute to environmental protection, and achieve cost savings. ■ Mechanisms of Cost Reduction Here’s how automatic solvent recycling equipment achieves cost reduction. First, by regenerating waste solvents, the frequency of purchasing new solvents can be significantly reduced. Additionally, the cost of waste disposal is reduced. Below are specific mechanisms of cost reduction: - Solvent Reuse: By regenerating and reusing waste solvents, the cost of purchasing new solvents is reduced. - Reduction in Waste Disposal Costs: Reducing the amount of waste solvents lowers disposal costs. - Reduction in Transportation Costs: With less waste solvent, transportation costs are also reduced. - Environmental Impact Reduction: Reducing the amount of waste lessens the environmental burden, improving the company's ecological image. ■ Actual Cost Reduction Effects - Annual Cost Savings: By introducing automatic solvent recycling equipment, it is possible to save several million yen annually. - Payback Period: The initial investment is usually recovered in 1-2 years, after which pure cost savings are realized. - Operating Costs: The operating costs of recycling equipment are low, enabling cost-effective operation. ■ Case Studies and Success Stories Introducing success stories from companies that have implemented automatic solvent recycling equipment: - Case 1: Chemical Plant: Achieved a 30% reduction in the cost of purchasing new solvents annually. - Case 2: Printing Plant: Reduced waste disposal costs by 50% and significantly lowered environmental impact. - Case 3: Manufacturing Plant: Cut transportation costs by 20%, leading to overall cost savings. ■ Reasons to Recommend Morikawa Industries' Automatic Solvent Recycling Equipment Morikawa Industries' automatic solvent recycling equipment is particularly recommended for the following reasons: - High Regeneration Efficiency: Equipped with the latest technology for efficient solvent regeneration. - Easy Operation: Automated systems make it easy to operate and maintain. - Environmental Consideration: Contributes to environmental protection, supporting the company's CSR activities. - Proven Track Record: Widely adopted by many companies, with high reliability and proven performance. In addition, Morikawa also supports sales within Thailand. Our distributor, T.I.T. ELECTRONICS CO., LTD., provides nationwide service from its base in Bangkok, ensuring prompt support. For more details, please download the PDF or feel free to contact us.
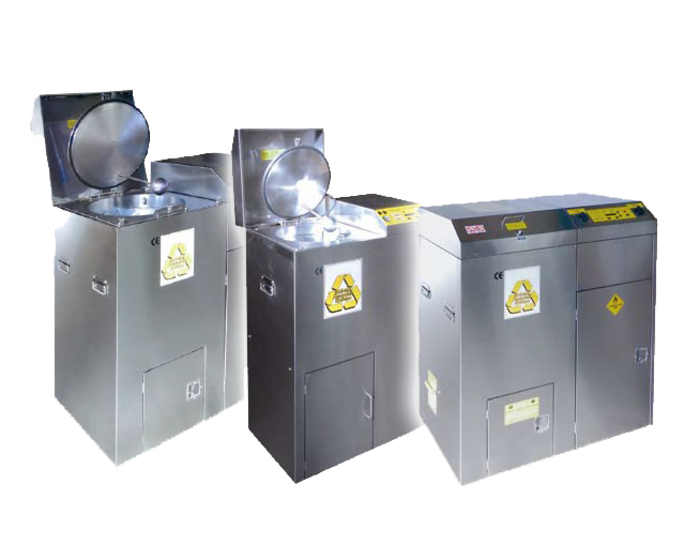
Morikawa Automatic Solvent Recycling Machine: Features and Effective Usage
Morikawa Automatic Solvent Recycling System is designed to process used solvents into reusable quality, reducing waste, minimizing environmental impact, and lowering purchasing costs. In Thailand, this system is distributed and supported by T.I.T. ELECTRONICS CO., LTD., with nationwide service coverage from its Bangkok headquarters. ■ Key Features - Automatic Operation: Fully automated process minimizes manual handling while maximizing efficiency. - Eco-Friendly: Reduces waste and contributes to environmental conservation. - Cost-Effective: Reduces the need for new solvent purchases, saving operational costs. - High Recycling Efficiency: Advanced technology maintains high-quality output for recycled solvents. - Safety-Oriented Design: Equipped with robust safety features for worry-free operation. - Fast Support: T.I.T. ELECTRONICS CO., LTD. provides comprehensive after-sales service across Thailand. ■ Specifications - Recycling Process: Automated heating and distillation system - Recycling Efficiency: Up to 90% (depending on solvent type and condition) - Supported Solvents: Industrial solvents like alcohols, toluene, acetone, etc. - Operation: Easy control with a user-friendly touch panel - Safety Features: Includes overheat prevention, leakage detection sensors, and automatic shutdown functions ■ Applications - Manufacturing: Suitable for processes like painting and component cleaning - Cleaning Industry: Recycles solvents used in cleaning processes - Research and Development: Recycles solvents for laboratory and experimental use Morikawa Automatic Solvent Recycling System is an eco-friendly, cost-efficient solution to reduce waste and operational expenses. It is now available in Thailand, with full sales and support provided by T.I.T. ELECTRONICS CO., LTD. For more details, download the PDF or feel free to contact us.
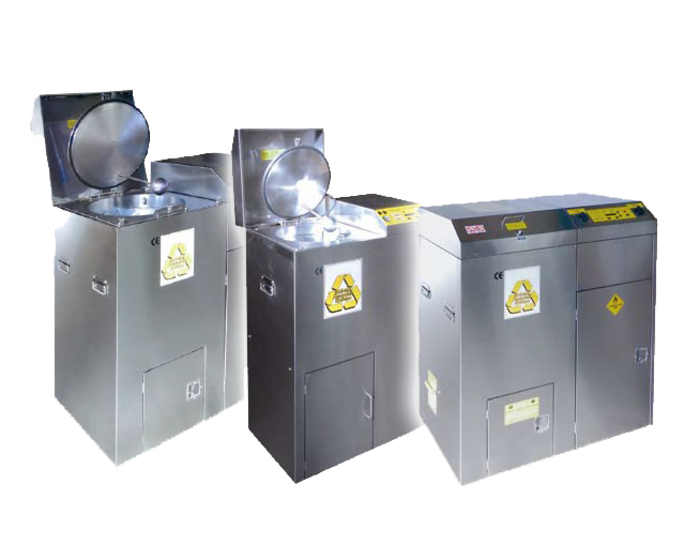
Automatic Solvent Recycling System: Morikawa's Strengths and Differentiators
Morikawa’s automatic solvent recycling system is designed to reprocess used solvents into reusable quality. This system reduces waste, minimizes environmental impact, and lowers procurement costs. In Thailand, the system is distributed and serviced by T.I.T. ELECTRONICS CO., LTD., which operates nationwide from its Bangkok headquarters with fast and reliable service. ■ Key Features - High-efficiency recycling technology: Maximizes solvent usage and reduces waste - Eco-friendly: Minimizes waste and supports environmental conservation - Ease of use: Intuitive interface simplifies operation and reduces training time - High durability: Made from high-quality materials for long-term use - Customizable: Adaptable design tailored to specific organizational needs - Quick support: Nationwide after-sales service by T.I.T. ELECTRONICS CO., LTD., backed by a professional team ■ Applications - Chemical industry: Recycling solvents generated from chemical manufacturing processes - Manufacturing: Utilized in painting and parts cleaning processes - Research and development: Recycling solvents used in laboratories and experiments Morikawa is committed not only to manufacturing recycling systems but also to reducing costs, enhancing sustainability, and delivering value through advanced technology and local services. For more details, download the PDF or contact us directly.
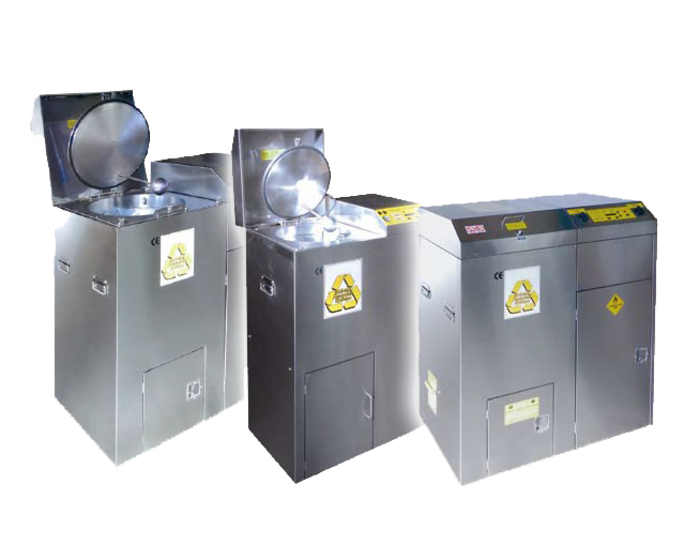
Automatic Solvent Recycling Machine Regenerator Features and Specifications
The Automatic Solvent Recycling Machine Regenerator (Automatic Solvent Recycling Machine Regenerator) helps reduce environmental impact and cut company costs by efficiently recycling used solvents. This equipment is widely used in various industries such as chemical industry, pharmaceutical industry, and automotive manufacturing, boasting a high recycling rate with advanced technology. ■ Specifications - Processing Capacity: Can recycle up to 100 liters of solvent per day - Recycling Rate: Recycling rate of over 95% - Operating Temperature: Adjustable from room temperature to 200℃ - Power Consumption: Average 1.5 kWh - Dimensions: Width 1.2m x Depth 1.0m x Height 2.0m - Weight: Approximately 500 kg ■ Applications - Chemical Industry: Recycling and reusing used solvents - Pharmaceutical Industry: Efficient recycling of solvents used in the manufacturing process - Automotive Manufacturing: Reusing solvents used in the painting process - Printing Industry: Recycling and reusing ink solvents In addition, Morikawa also supports sales within Thailand. Our distributor, T.I.T. ELECTRONICS CO., LTD., provides nationwide service from its base in Bangkok, ensuring prompt support. For more details, please download the PDF or feel free to contact us.
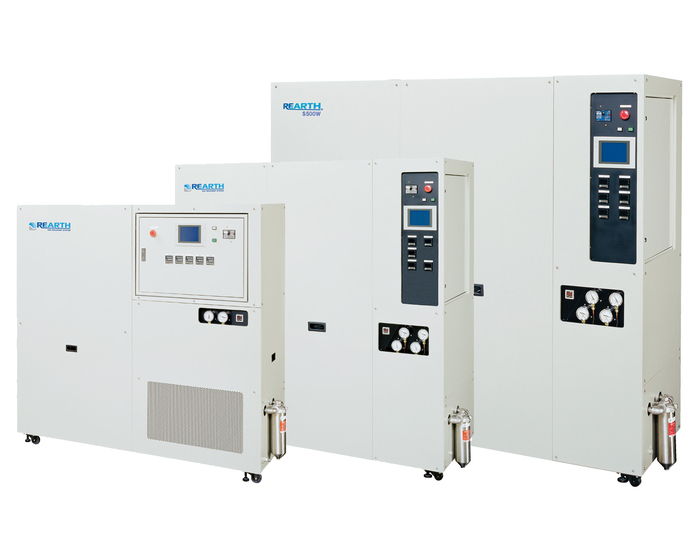
Reearth Series organic solvent gas recovery equipment for parts cleaning: Balancing cost and the environment
The Rearth series is an organic solvent gas recovery device that achieves high cost performance and environmental conservation. By efficiently liquefying and reusing organic solvent gas generated during the cleaning and coating process of precision parts, it is possible to reduce material costs and reduce environmental pollution. This device achieves significant cost reduction compared to conventional methods and also increases compliance with exhaust gas regulations. ■ Features - Cost reduction: The purchase cost of organic solvents can be significantly reduced. - Environmental measures: The emission concentration is significantly reduced and meets the standards of local regulations. - Efficient recovery: Organic solvent gas is efficiently liquefied and recovered by compression cooling. - Reuse of used solvents: The recovered solvent is returned to the process, achieving both economic benefits and environmental conservation. ■ Specifications - Target of use: Cleaning and coating process of precision parts. - Cooling method: Highly efficient compression cooling system. - Recovery efficiency: Reduces organic solvent by approximately 66%. - Compliance with environmental regulations: Reduces atmospheric emission concentration from 725 ppm to 15 ppm. In addition, Morikawa also supports sales within Thailand. Our distributor, T.I.T. ELECTRONICS CO., LTD., provides nationwide service from its base in Bangkok, ensuring prompt support. For details, please download the PDF or feel free to contact us.
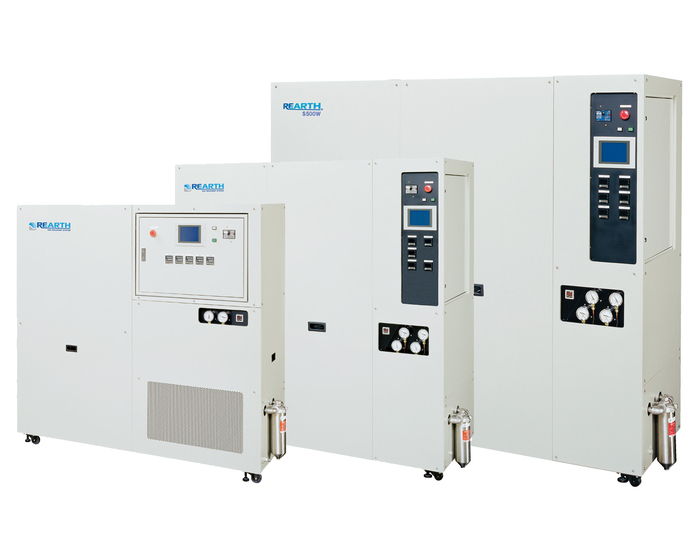
"REARTH S Series" Organic Solvent Gas Recovery Systems: Cost Reduction and Environmental Conservation through Compression Cooling
The REARTH® S Series is a device that contributes to both environmental and economic aspects by efficiently recovering and reusing organic solvent gases. It is specifically designed to target organic solvent gases produced in precision part cleaning and coating processes. Through compression cooling and liquefaction, it regenerates costly solvents and prevents their emission into the atmosphere. ■ Features - Utilizes a "deep freeze condensation method" that achieves a removal rate of over 99% - Highly versatile, adapting to various solvents and emission systems - Proven track record of installations ensures reliable performance and support - Economic efficiency and environmental consideration through efficient solvent use - Recovery of high-quality liquid solvents suitable for reuse - Space-efficient compact design ■ Specifications - Name: REARTH® S Series Organic Solvent Gas Recovery Systems - Recovery Technology: Deep Freeze Condensation Method - Applicable Solvents: Wide range of organic solvents - Installation Requirements: No drainage needed, compact design In addition, Morikawa also supports sales within Thailand. Our distributor, T.I.T. ELECTRONICS CO., LTD., provides nationwide service from its base in Bangkok, ensuring prompt support. For more details, please download the PDF or feel free to contact us.
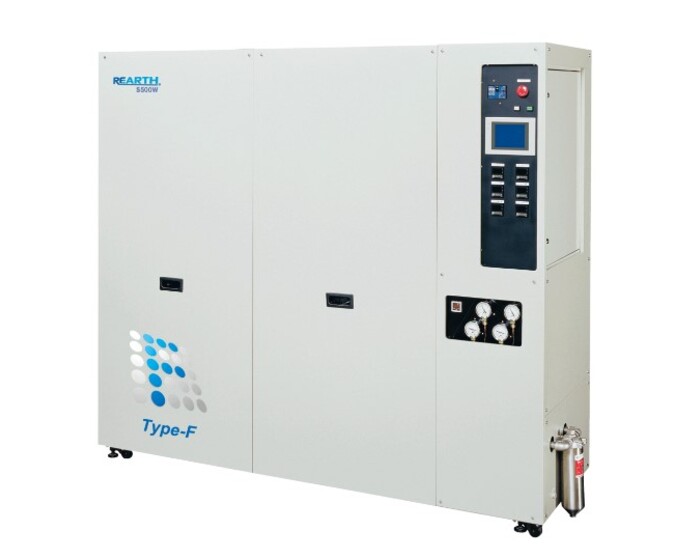
REARTH S-Series Type-F: Organic Solvent Gas Recovery Systems that Enhance Liquid Quality with Special Adsorbents
The "REARTH® S Series F Type" is the latest model that maintains the functionality of the existing S Series while improving liquid quality by introducing our proprietary special adsorbent. Furthermore, by expanding its compatibility with next-generation fluorinated solvents (HFOs), it will help companies protect the environment and improve their economic efficiency even in the midst of strict environmental regulations. ■ Features - Improved quality with adsorbent, recovers higher quality liquid products than conventional products: - S series users can upgrade to F type by simply replacing the adsorption unit - Flexible support for next-generation fluorine solvents (HFO type) and future environmental regulations - Maintains high removal rate of over 99% with compression cryogenic condensation method - Abundant track record of application to various discharge facilities - Efficient solvent use reduces costs and is economical - Compact design allows installation anywhere, no drainage equipment required ■ Specifications - Name: REARTH® S series F type - Recovery technology: compression cryogenic condensation method, special adsorbent - Compatible solvents: Various organic solvents, including next-generation fluorine solvents (HFO type) - Design: Compact design, no drainage equipment required The "REARTH S series F type" brings together advanced technologies to achieve high economic effect and environmental performance, strongly supporting your sustainability efforts. In addition, Morikawa also supports sales within Thailand. Our distributor, T.I.T. ELECTRONICS CO., LTD., provides nationwide service from its base in Bangkok, ensuring prompt support. For details, please download the PDF or feel free to contact us.
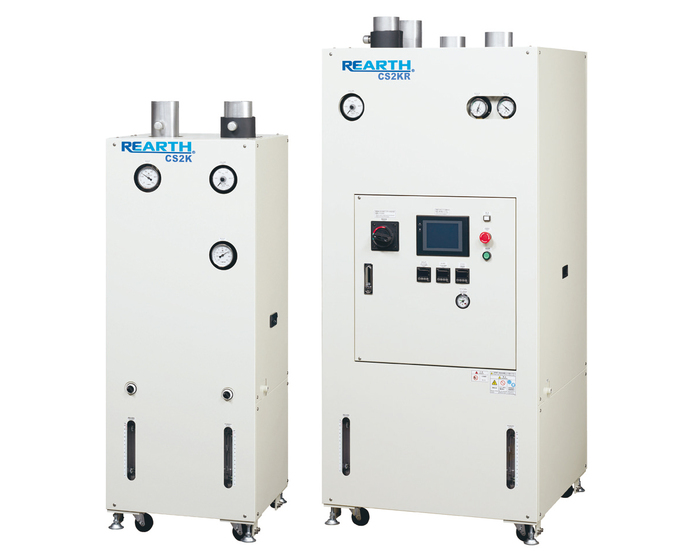
REARTH CS Series: Atmospheric Low-Temperature Condensation System for Flammable Organic Solvent Gases
The "REARTH® CS Series" is a recovery system that employs an atmospheric low-temperature condensation method for flammable organic solvent gases. Building on the technology of the traditional S Series, it has expanded the range of treatment-target solvents, making it suitable for a broader range of industrial facilities. ■ Features - Specialized design and functionality for the recovery of flammable organic solvent gases - Easy upgrade from the S Series to the CS Series for existing users - High liquefaction efficiency achieved through the atmospheric low-temperature condensation method - Compact equipment design reduces installation space - Reduced operational costs with a refrigerant exhaust reuse system - Efficient liquefaction and condensation process using cooling water and refrigeration equipment ■ Specifications - Name: REARTH® CS Series - Technology: Atmospheric Low-Temperature Condensation - Applicable Gases: Flammable Organic Solvent Gases - Structure: Compact design, equipped with a low-temperature cooler In addition, Morikawa also supports sales within Thailand. Our distributor, T.I.T. ELECTRONICS CO., LTD., provides nationwide service from its base in Bangkok, ensuring prompt support. For more details, please download the PDF or feel free to contact us.
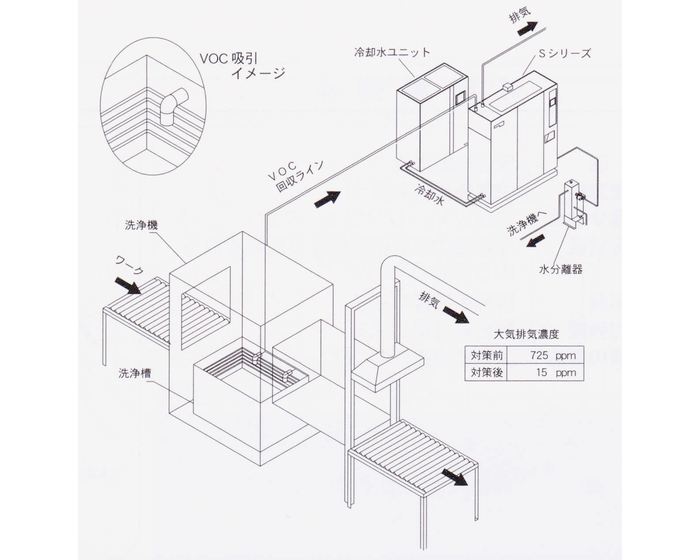
Case Study of Company A's Reearth Device Implementation: Reducing VOC Emissions in the Transport Machinery Manufacturing Industry
① Company A: Transport Machinery Manufacturing - Product Name: REARTH® S Series - Industry: Transport Machinery Manufacturing - Emission Facility: Cleaning Facility (Closed-type Single-tank Automatic Cleaning Machine) - Target VOC Gas: Trichloroethylene - Emission Situation: Vapor gas overflow from the cleaning equipment and diffusion inside the tank - Usage Before Measures: 2.5 tons/month (Atmospheric emissions: 1.8 tons/month) - Operating Hours: 24 hours/day, 22 days/month - Purpose of Measures: To meet prefectural emission standards Results of Measures: - Before Measures: Atmospheric Emission Concentration: 725 ppm, Usage: 2.5 tons/month - After Measures: 66% reduction achieved, Atmospheric Emission Concentration: 15 ppm, Usage: 0.85 tons/month ■ Overview In the transport machinery manufacturing industry, Company A faced issues with VOC (volatile organic compound) emissions. The installation of the REARTH® S Series system enabled efficient recovery of high-concentration VOCs, successfully reducing atmospheric emission concentrations from 725 ppm to just 15 ppm. This is significantly below the industry’s environmental standards, ensuring reduced environmental impact and compliance with regulations. ■ Highlights - VOC Emission Reduction: Company A’s case demonstrates a reduction from 725 ppm to 15 ppm - Compliance: Achieved emission levels far below regional regulations - High Efficiency: VOC recovery system with exceptional processing capabilities In addition, Morikawa also supports sales within Thailand. Our distributor, T.I.T. ELECTRONICS CO., LTD., provides nationwide service from its base in Bangkok, ensuring prompt support.
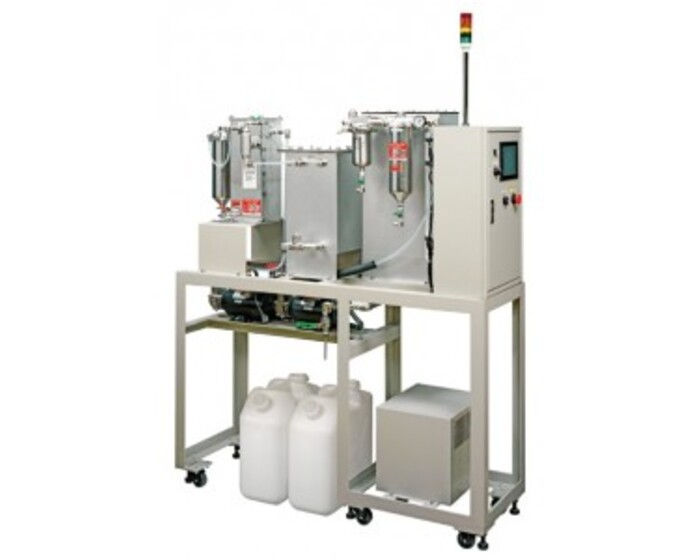
Purification Equipment: Solvents recovered by the S series are recycled to high quality
The "Purification Equipment" is an accessory device that works seamlessly with the REARTH® S series to further improve the quality of the recovered solvent. By circulating filtration using molecular sieves, even the finest residues are removed, producing high-purity solvents that are particularly required for precision part manufacturing. ■ Features - Highly efficient circulating filtration system using molecular sieves - Improves solvent quality when used in conjunction with the S series - Provides high-quality solvents required for precision part manufacturing - Quality assurance and cost reduction through purer solvent recovery - Contributes to environmental protection by continuously reusing solvents ■ Specifications - Name: Purification Equipment - Compatibility: Exclusively for the REARTH® S series - Filtration technology: Circulating filtration using molecular sieves - Features: High-quality solvents, removal of residues In addition, Morikawa also supports sales within Thailand. Our distributor, T.I.T. ELECTRONICS CO., LTD., provides nationwide service from its base in Bangkok, ensuring prompt support. For more details, please download the PDF or feel free to contact us.
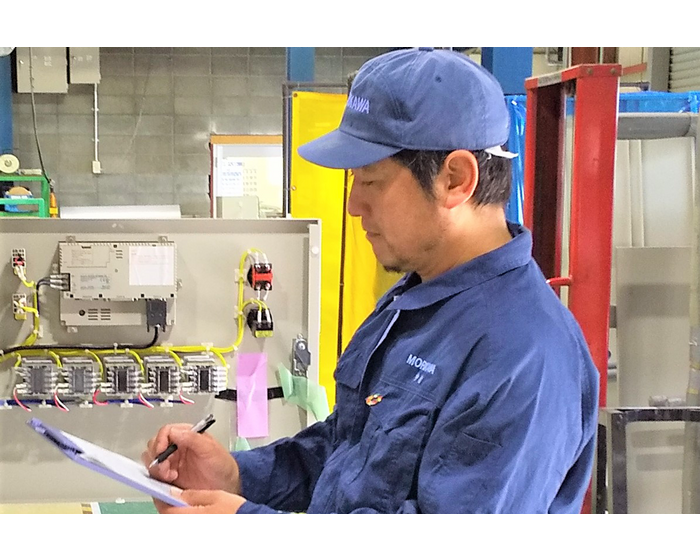
REARTH® SERVICE: High-performance Organic Solvent Gas Recovery Equipment Rental Service
REARTH® SERVICE is a rental service for high-performance organic solvent gas recovery equipment, requiring no initial investment. It helps reduce solvent costs and promotes environmental compliance. With comprehensive support, including equipment improvement, installation, and system optimization, we provide strong backing for your factory operations. ■ Service Details - Improvement of emission source equipment: Maximizing recovery efficiency through localized exhaust optimization and new jig installations - Installation and commissioning: Expert-led installation and trial operation to ensure optimal performance - Regular maintenance: Preventive maintenance tailored to equipment usage and operation time, ensuring consistent performance ■ Steps to Start REARTH® SERVICE 1. Begin with a technical inspection by our specialists 2. Propose a plan and provide a cost estimate 3. Explain the contract details and proceed with signing 4. Install the organic solvent (VOC) gas recovery system and carry out additional installations 5. Start the REARTH® SERVICE Note: This service was developed in collaboration with the Tokyo Metropolitan Industrial Technology Research Institute to promote environmental measures. ■ Specifications - Service Name: REARTH® SERVICE - Offered Content: Rental of organic solvent gas recovery equipment and comprehensive support - Benefits: No initial investment required, with support ranging from equipment improvement to maintenance REARTH® SERVICE allows you to start environmental measures and cost-saving initiatives effortlessly and quickly through a rental model. From installation to ongoing support, we fully back your company’s sustainable manufacturing efforts. In addition, Morikawa also supports sales within Thailand. Our distributor, T.I.T. ELECTRONICS CO., LTD., provides nationwide service from its base in Bangkok, ensuring prompt support. For more information, please contact us.
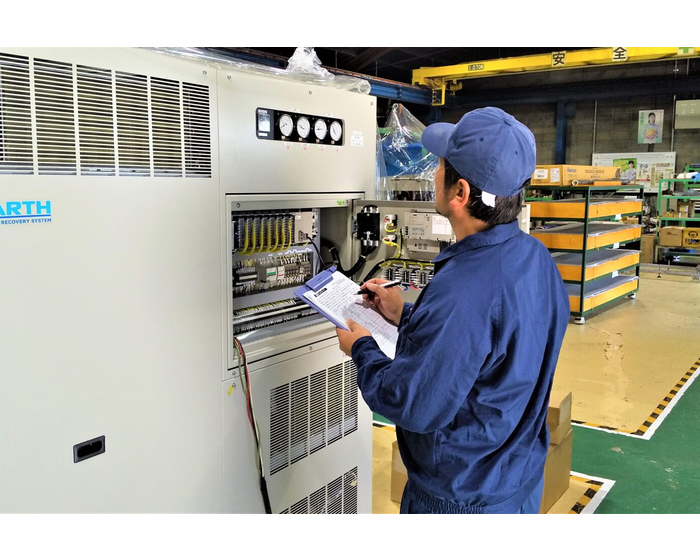
REARTH Service: Rent Organic Solvent Gas Recovery Equipment – No Upfront Cost, Cut Costs and Environmental Impact
REARTH Service offers an easy-to-implement service for organic solvent gas recovery devices through rental, requiring no initial investment. It enables immediate cost reduction on solvent purchases and addresses environmental emissions. By using the latest REARTH series devices, you can maintain quality while significantly improving cost performance. ■ Features - Zero Initial Investment: As a rental service, it does not require a high initial investment. - Solvent Cost Reduction: Reusing expensive organic solvents reduces purchase costs. - Enhanced Environmental Measures: Significantly reduces emissions, minimizing environmental impact. - Regular Maintenance: Skilled service personnel ensure the equipment is kept in optimal condition. ■ Specifications - Rental Model: Various devices from the REARTH series. - Maintenance: Regular professional maintenance is conducted. - Environmental Standards Compliance: Complies with local environmental regulations and standards. - Cost-effectiveness: Provides data-driven average cost reduction rates from practical examples. In addition, Morikawa also supports sales within Thailand. Our distributor, T.I.T. ELECTRONICS CO., LTD., provides nationwide service from its base in Bangkok, ensuring prompt support. For more details, please download the PDF or feel free to contact us.
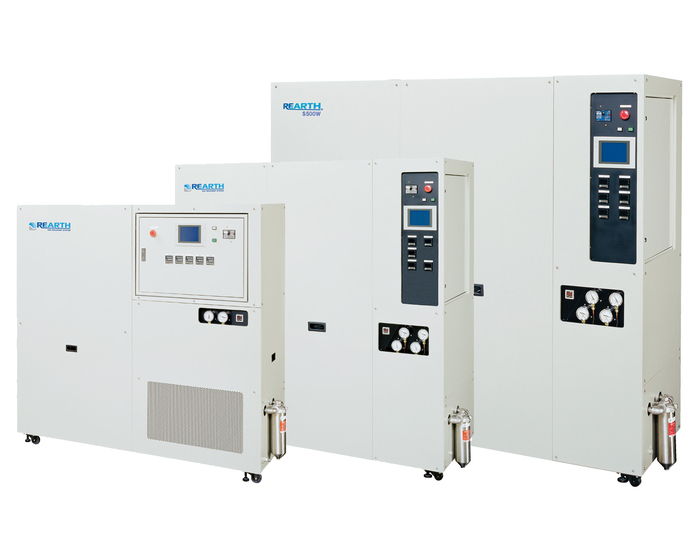
Environment Division History of Awards for VOC Gas Recovery Devices
1998 Won the Tokyo Industrial Technology Award (Product and technology contributing to the creation of an environmental circulation-type society) 1999 Received the 26th Outstanding Environmental Device, The Japan Society of Industrial Machinery Manufacturers Chairman Award 2008 Received the 11th Protection of Ozone Layer and Prevention of Global Warming Award, Minister of the Environment Award” 2013 Received the Resource Recirculation Technology and Systems, Japan Environmental Management Association for Industry Chairman Award This is a device that recovers organic solvent gases with high efficiency, and contributes to reducing VOC emissions, especially in fields such as printing, painting, and the chemical industry. Our technology, which combines environmental protection and cost reduction, has won numerous awards, including the Tokyo Industrial Technology Award in 1998, and its performance and reliability are highly regarded both inside and outside the industry. ■ Features - Highly acclaimed as a product that contributes to the creation of an environmentally circulating society - Reduction of operating costs through highly efficient gas recovery - Versatility and flexibility that can be used in multiple industrial fields - Long-life design achieves stable operation over a long period of time - A proven track record and reliability, with numerous awards including the Minister of the Environment Award In addition, Morikawa also supports sales within Thailand. Our distributor, T.I.T. ELECTRONICS CO., LTD., provides nationwide service from its base in Bangkok, ensuring prompt support. For more information, please contact us.
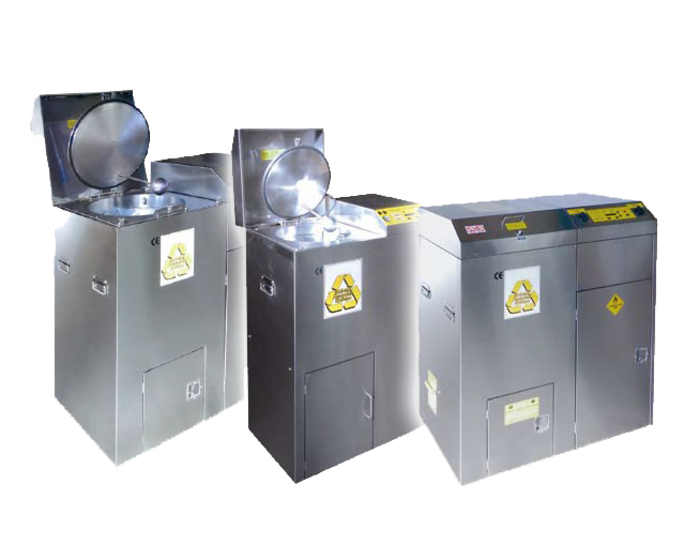
Solvent Recycler An automatic solvent regeneration device that uses distillation regeneration technology
The "Solvent Recycler" is an automatic solvent regeneration device that efficiently regenerates used waste solvents and revolutionizes waste liquid treatment in factories. This device reduces environmental impact and improves economic efficiency by distilling waste solvents into new solvents. ■ Features - Contributes to cost reduction by regenerating used solvents to the same quality as new solvents. - Can handle a variety of solvents (hydrocarbons, alcohols, ketones, esters, halogens). - Residues after distillation can be safely and cleanly discharged using special bags. - Can be selected from two types, continuous and batch, to enable processing according to needs. ■ Specifications ・ Continuous type: - Normal pressure type: Suitable for cases with small amounts of sludge, capable of treating waste liquid at 30 to 250 liters per day. - Reduced pressure type: Suitable for solvents with a boiling point of approximately 150°C or higher, allowing safe distillation. ・ Batch type: - Can handle solidifying sludge, capable of treating waste liquid at 10 to 150 liters per day. ■ Applications Treatment of waste solvents from solvent-using processes in chemical plants, paint factories, the printing industry, etc. Use in facilities that require waste liquid management in accordance with environmental standards. The "Solvent Recycler," which uses cutting-edge technology, is the ideal solution for manufacturing industries that aim to achieve both environmental protection and cost reduction. In addition, Morikawa also supports sales within Thailand. Our distributor, T.I.T. ELECTRONICS CO., LTD., provides nationwide service from its base in Bangkok, ensuring prompt support. For details, please download the PDF or feel free to contact us.
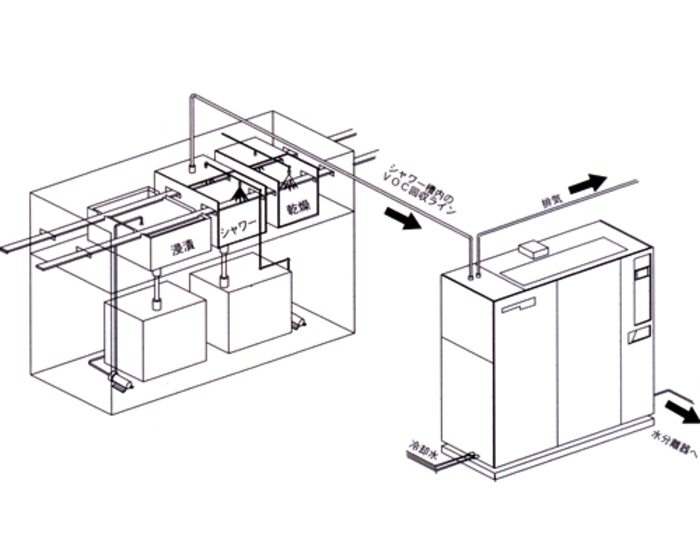
Case Study of Company B: Effects of Organic Solvent Gas Recovery and Cost Reduction in Connector Cleaning Processes
Company B Case Study: Highly efficient S-series equipment dramatically reduces solvent usage costs and reduces environmental impact. [Company B: Electrical parts manufacturing] - Product name: REARTH ®S series - Industry: Electronic parts manufacturing - Emission facility: Surface treatment tank (hoop-type sealing treatment) - Target VOC gas: 1-bromopropane (nPB) - Emission status: Emission from local exhaust in drying tank - Usage before countermeasures: 1.6t/month (air emissions 1.5t/month) - Operating hours: 24 hours/30 days/month - Purpose of countermeasures: Cost reduction and emission reduction by reducing consumption (environmental response) - Results of countermeasures: Usage before countermeasures: 1.6t/month, solvent purchase cost: ¥2,240,000 ↓Successfully reduced by 66% [Cost benefit of ¥1,470,000/month] Usage after countermeasures: 0.55t/month, solvent purchase cost: ¥770,000 Company B uses 1-bromopropane (nPB) in the cleaning process of connector terminals, which is essential for electrical parts manufacturing. The challenge was to reduce the cost of this organic solvent gas and the environmental impact. As a result of introducing the S series organic solvent gas recovery equipment, monthly solvent usage was significantly reduced from 1.6 tons to 0.55 tons, and purchase costs were significantly reduced from 2.24 million yen to 770,000 yen, achieving a 66% cost reduction. ■ Features ・ Significant reduction in usage: Monthly usage of 1.6 tons reduced to 0.55 tons. ・ Economic benefits: Monthly purchase costs reduced from 2.24 million yen to 770,000 yen. ・ Environmental friendliness: Efficient recovery of organic solvent gas reduces environmental impact. ■ Specifications ・ Target solvent: 1-bromopropane (nPB). ・ Target process: Cleaning of connector terminals. ・ Equipment model number: Organic solvent gas recovery equipment S series. Company B's implementation case proves the effectiveness of the S series equipment, which produces excellent results in both cost and environment. This shows the possibility of simultaneously promoting economical production activities and environmental considerations within the industry. In addition, Morikawa also supports sales within Thailand. Our distributor, T.I.T. ELECTRONICS CO., LTD., provides nationwide service from its base in Bangkok, ensuring prompt support. For more information, please contact us.
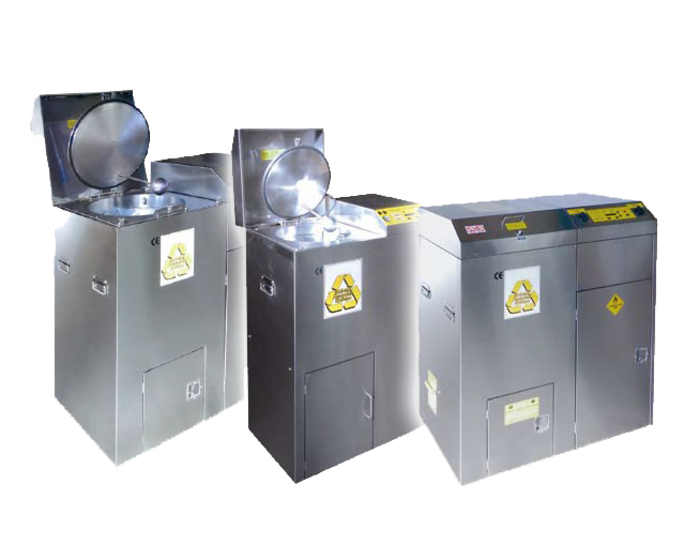
Morikawa's Automatic Solvent Recycler | From Hydrocarbons to Esters
The Solvent Recycler is a device that restores used solvents to a reusable state. It reduces waste solvent generation, protects the environment, and significantly lowers operational costs, providing comprehensive support for sustainable factory operations. Examples of recyclable solvents include: ● Hydrocarbon Solvents Examples: Toluene, Xylene, Solvent naphtha, Normal hexane, Isohexane ● Alcohol-Based Solvents Examples: Methanol, Ethanol, Butanol, Isopropyl alcohol (IPA) ● Ketone-Based Solvents Examples: Acetone, Methyl ethyl ketone (MEK), Methyl isobutyl ketone (MIBK) ● Ester-Based Solvents Examples: Ethyl acetate, Butyl acetate, Methoxybutyl acetate, Normal propyl acetate ● Other Solvents Halogen-based solvents, Fluorine-based solvents, Chlorine-based solvents *The above are examples of recyclable solvent types. For other solvents, please contact the Environmental Business Division. Morikawa's Solvent Recycler efficiently regenerates used solvents, reducing the need for frequent new solvent purchases and lowering operational costs. It enhances the purity of the recycled solvent, ensuring high performance in reuse. It is the ideal choice for companies aiming to achieve both environmental protection and cost savings. In addition, Morikawa supports sales within Thailand. Our distributor, T.I.T. ELECTRONICS CO., LTD., provides nationwide service from its base in Bangkok, ensuring prompt support. For more details, please download the PDF or contact us directly.
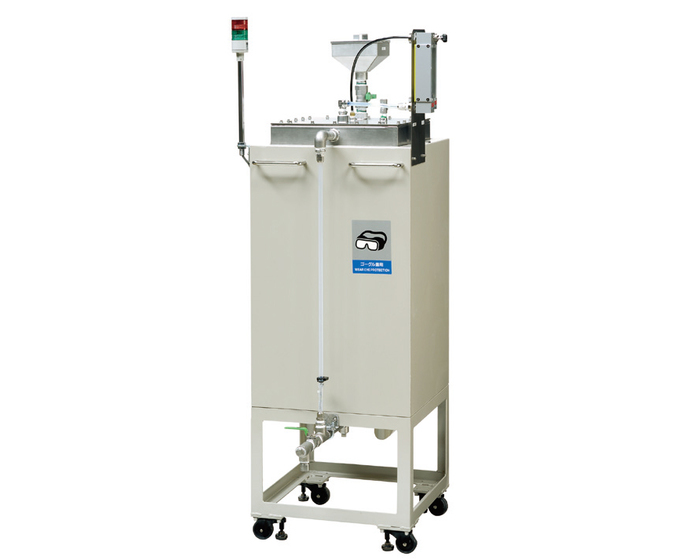
Simple Recycler Unit: Collaborates with S Series to Efficiently Recycle Solvent Waste
The "Simple Recycler Unit" is an auxiliary device that perfectly matches the S series organic solvent gas recovery device. Solvent waste liquid to be disposed of is bubbled by low-temperature indirect heating, and the vaporized gas is efficiently recovered and liquefied to restore it to a reusable state. This system reduces the amount of solvent used in cleaning and coating processes and minimizes the impact on the environment. ■ Features - Dedicated design for easy connection to the S series - Low-temperature indirect heating and bubbling method efficiently extract gas from solvent waste liquid - Extracted gas is recycled and converted into liquid solvent suitable for reuse - Reduces process waste and achieves economical solvent management - Energy-saving design contributes to reducing operating costs ■ Specifications - Name: Simple Regeneration Device - Compatibility: For REARTH® S series only - Heating method: Low-temperature indirect heating - Features: Recovers and liquefies gas from solvent waste liquid Effective use of solvent waste liquid generated in industrial processes is directly linked to cost reduction and environmental protection. This "Simple Recycler Unit" is an important step in supporting sustainable production activities. In addition, Morikawa also supports sales within Thailand. Our distributor, T.I.T. ELECTRONICS CO., LTD., provides nationwide service from its base in Bangkok, ensuring prompt support. For more details, please download the PDF or feel free to contact us.
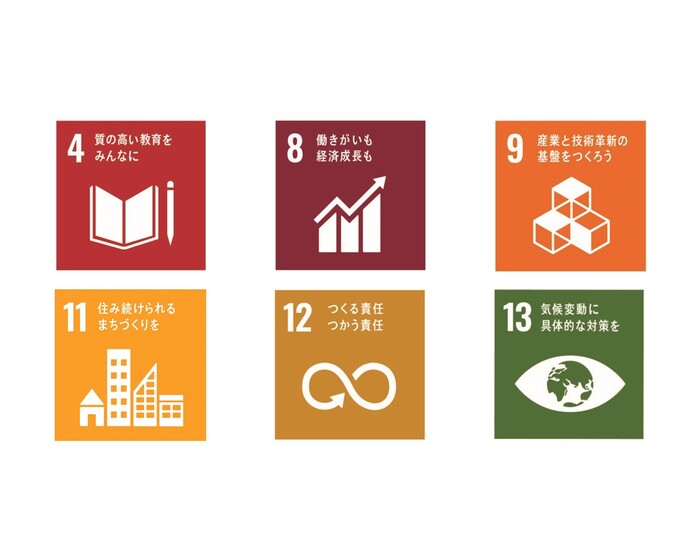
Automatic solvent regeneration equipment of Morikawa Co., Ltd. working together with SDGs
Morikawa's SDGs ■ Quality education for all (SDG Goal 4) [Provide inclusive and equitable quality education for all and promote lifelong learning opportunities] Implement employee education (through the web) (4.4) Sponsor related projects at nearby elementary and junior high schools (4.1) Continue to support NPOs in Nagano Prefecture (4.5) Support educational projects for children involving employees ■ Decent work and economic growth (SDG Goal 8) [Promote sustained, inclusive and sustainable economic growth, employment and decent work for all] Job creation through launch of new businesses (services) (8.5) Initiatives for equal pay for equal work (8.5) ■ Build infrastructure for industry and innovation (SDG Goal 9) [Build resilient infrastructure, promote sustainable industrialization and expand technological innovation] Expand Morikawa's environmental business overseas (9.4) ■ Create sustainable urban areas (SDGs Goal 11) [Make cities and human settlements inclusive, safe, resilient and sustainable] Continued cooperation with disaster response facilities in Chikuma City, Nagano Prefecture (11.5) Sponsorship of Chikuma City Living Guidebook (11.3) ■ Responsible Consumption and Production (SDGs Goal 12) [Ensure sustainable consumption and production patterns] Expansion of valve business (12.4) Expansion of environmental business (12.4) ■ Take concrete measures against climate change (SDGs Goal 13) [Take urgent measures to combat climate change and its effects] Continued cooperation with disaster response facilities in Chikuma City, Nagano Prefecture (13.1) Expansion of valve business (13.3) Expansion of environmental business (13.3)
CONTACT