YAMAGUCHI VIETNAM JOINT STOCK COMPANY
PRODUCTS
Technology / product information
15hits
Narrow by Industry Category
Narrow by material Category
Narrow by accuracy
Narrow by lot number
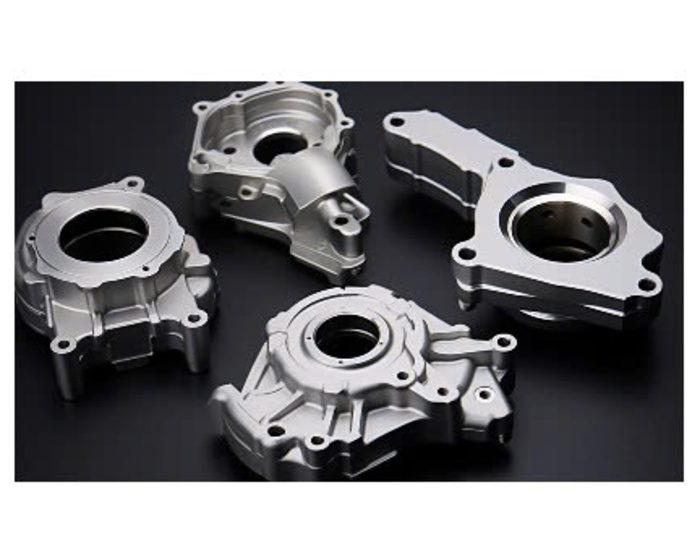
Precision Lathe Processing for Small Components
We are a specialized manufacturer providing high-precision lathe processing and mass production for small components. With years of collaboration with Japanese companies, we leverage our technical expertise and quality control know-how to achieve lathe machining with ±0.01mm accuracy. We specialize in lathe processing for various materials, including steel, stainless steel, aluminum, copper, and engineering plastics. Utilizing state-of-the-art CNC and automatic lathes, we can efficiently handle both small-lot prototyping and mass production with high flexibility. Below, we introduce the key features of our lathe processing technology, which is optimized for high-volume production. Key Features of Yamaguchi’s Lathe Processing - High-Precision Machining: Leveraging the expertise of skilled engineers and extensive experience with Japanese companies, we achieve ±0.01mm accuracy, ensuring consistent quality that meets strict industry requirements, including automotive applications. - Wide Material Compatibility: We support lathe processing for various materials, including: Iron (SS400) Stainless steel (SUS303, SUS304) Aluminum alloy (A5052) Copper (C2600) Engineering plastics - Large-Scale Production Capability: With approximately 250 lathes, including CNC lathes, general-purpose lathes, and automatic lathes, we can mass-produce small components efficiently using automated processes, ensuring time and cost savings. - Strict Quality Control: Using advanced CMM (3D measuring machines), contour measuring instruments, and surface roughness testers, we conduct thorough quality inspections. Our quality management system complies with ISO 9001 standards, ensuring strict control over dimensional tolerances, surface finish, and mechanical properties. Quality Assurance & Production System - Strict Quality Management We employ the latest 3D and 2D measurement equipment to maintain precision throughout each production stage. This ensures dimensional accuracy and surface quality, even in mass production, guaranteeing consistent and reliable output. - State-of-the-Art Equipment & Skilled Expertise: With around 250 lathes, we utilize optimized machining methods to achieve high-precision, high-efficiency production for each component. Our modern equipment allows for large-scale manufacturing, meeting tight tolerances and strict industry standards. - Flexible Delivery & Lead Times: From prototyping to large-scale production, our efficient production management system allows us to deliver products in a short timeframe. By optimizing lathe processing workflows, we maximize efficiency and provide tailored production scheduling to meet customer demands. - International Quality Standards: We implement a strict quality control system that complies with ISO 9001, ensuring rigorous inspections at every stage of material and product processing. Why Choose Yamaguchi for Small Component Lathe Processing? Our company specializes in high-precision lathe processing and mass production of small components in Vietnam. With cutting-edge equipment and experienced engineers, we ensure exceptional quality and efficiency. With over 250 lathes and an optimized production management system, we can accommodate both prototyping and large-scale manufacturing with short lead times. Our ISO 9001-compliant quality management system guarantees stable, high-quality products that meet global industry standards. We serve a wide range of industries, including automotive, and provide high-quality small components from Vietnam to the global market. If you are looking for a trusted partner for high-precision lathe processing of small components in Vietnam, contact Yamaguchi!
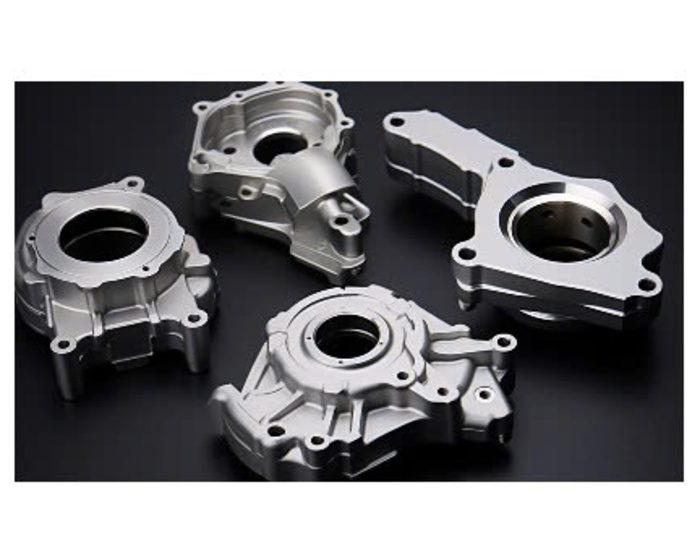
Milling and Lathe Machining of Stainless Steel Components
Our company specializes in high-precision machining, including milling and lathe processing, utilizing the latest equipment to handle various materials such as stainless steel (SUS303, SUS304), special steels, aluminum (A5052), copper (C2600, C1100), and resins. With extensive experience working with Japanese companies, we ensure high-quality standards in accordance with Japanese requirements while also accommodating short lead times. Specifications Materials: Various stainless steels, including SUS303, SUS304, SUS316, and SUS430 Processing Capabilities: Milling, lathe machining, drilling, threading, surface finishing Precision: ±0.01mm Production Lot Sizes: Flexible handling from small-lot prototypes to large-scale mass production Processable Sizes: NC Lathe (X-Z): 450×1,000 mm Milling Machine (X-Y-Z): 1,050×510×460 mm Production Capacity: Over 1 million parts per month Quality Management System Precision product inspection using high-accuracy measuring devices (3D and 2D coordinate measuring machines) Strict quality assurance process: Full inspection based on ISO 9001-compliant standards Production Equipment & Technical Capabilities Large-scale production capacity with 250 lathes and 100 milling machines Short lead-time options: Rapid response from prototyping to mass production Delivery Capability High production capacity enables short lead-time fulfillment for large-volume orders Flexible production line adjustments per project to ensure smooth shipments We leverage the latest equipment to achieve high-precision milling and lathe processing for various materials, including stainless steel (SUS303, SUS304). We flexibly accommodate orders from small-lot prototypes to large-scale mass production, boasting a production capacity of over 1 million parts per month. Additionally, we maintain an ISO 9001-compliant quality control system, implementing full inspections using precision measuring equipment. With 250 lathes and 100 milling machines, we handle mass production while ensuring short lead times from prototyping to mass production. For stainless steel milling and lathe processing in Vietnam, please contact Yamaguchi!
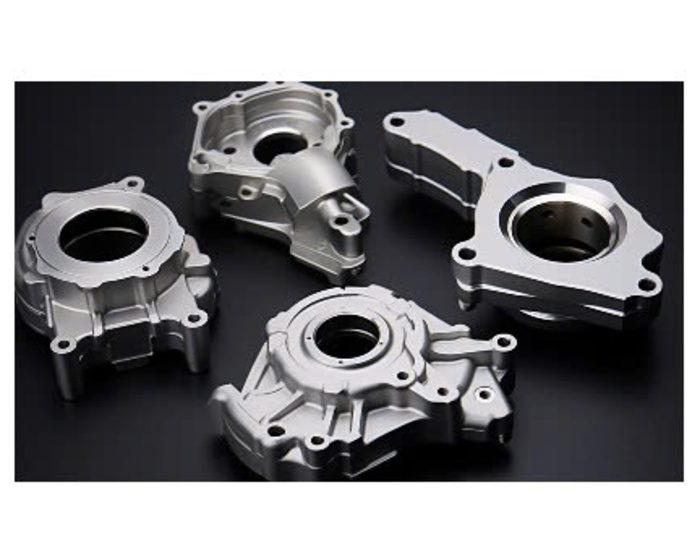
Aluminum Die Casting Technology for Small-sized Products Using the SD-420CH Machine
At Yamaguchi, we utilize the SD-420CH aluminum die casting machine to cast small-sized products ranging from 0.4 to 2.0 kg. 【Specifications】 Supported Weight: Aluminum products weighing 0.4 to 2.0 kg (smaller products can be cast using multi-cavity molds). Maximum Size: 450 × 400 × 250 mm Production Capacity: ~25,000 units per month 【Quality Assurance & Production System】 1. Quality Control System We develop Quality Control Plans (QC Plans) for each product code, ensuring strict quality management. 2. Equipment & Technical Capability - Our company has introduced state-of-the-art casting equipment, enabling the production of high-precision and stable aluminum die-cast components. - The SD-420CH machine enables fast production of products up to 450 × 400 × 250 mm. - Our multi-cavity mold support allows for efficient manufacturing of small components. - For medium-sized products, we employ the BD-V7EX 800T machine, capable of casting high quality products weighing 2.0 kg to 6.0 kg. - Our flexible production system allows us to meet diverse needs, from small to medium-sized products. 3. Delivery Capability We can accommodate short lead times and flexibly handle mass production. Our supply system is tailored to meet our customers' production plans. Our company leverages the SD-420CH machine to precisely cast small-sized aluminum die-cast products (0.4 - 2.0 kg). With multi-cavity mold support, we can also mass-produce even smaller components. Our monthly production capacity is approximately 25,000 units, and we excel in quick delivery. Furthermore, we have strengthened our quality management system, implementing thorough control based on QC plans. For medium-sized products, we utilize the BD-V7EX 800T, establishing a stable supply system capable of meeting a wide range of product needs.
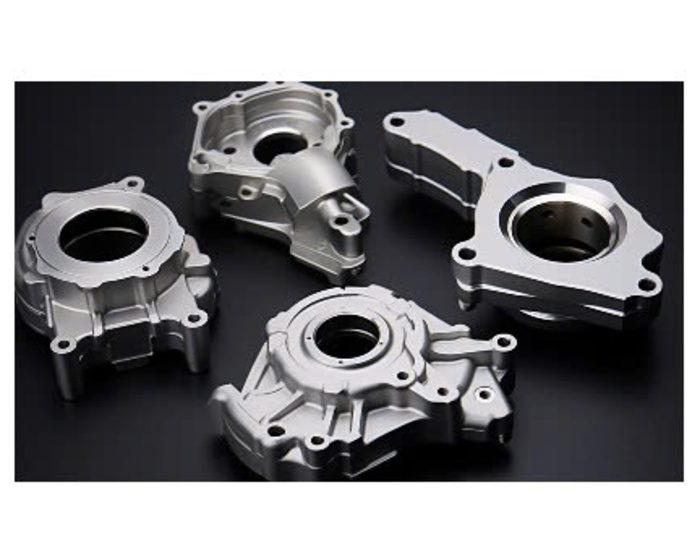
Aluminum Die Casting up to 6.5kg
Yamaguchi possesses advanced aluminum die-casting technology, capable of producing high-precision aluminum die-cast products weighing up to 6.5kg for the automotive industry and various other sectors. We meet mass production demands with a production capacity of 65,000 products per month. With cutting-edge equipment, Yamaguchi meets the diverse needs of various industries, providing both single-unit proudction and large-scale manufacturing. Our strength lies in the ability to produce components of various shapes and sizes, up to approximately 6.5kg. If you are looking for aluminum die-casting services in Vietnam, contact us! Features of Yamaguchi's Aluminum Die-Casting Technology: ✅ Support product weights up to 6.5 kg. ✅ Capable of thin-wall casting as thin as 2-3mm. ✅ Die-casting machines ranging from 420 tons to 800 tons, accommodating diverse manufacturing needs. ✅ Production capacity of approximately 65,000 units per month. ✅ Precision post-casting machining in-house, ensuring high quality and shorter delivery times. ✅ Supply components for various industries, especially the automotive sector. Equipment for Aluminum Die-Casting: 🔹 Aluminum die-casting machine BD-V7EX800T 🔹 Aluminum die-casting machine SD-420CH 🔹 Elemental Analyzer 🔹 Shot blasting machine At Yamaguchi, product quality is our top priority. We conduct thorough raw material inspections using elemental analyzer. Additionally, our shot blasting process enhances finishing precision, ensuring high uniformity even for complex-shaped components. With the capability to perform aluminum die-casting for products weighing up to 6.5kg, combined with modern equipment and advanced technology, Yamaguchi delivers high-quality components for the automotive industry and other sectors. Furthermore, our fully integrated in-house production system covers casting to precision machining, allowing us to meet the demands of complex designs and high-precision specifications.
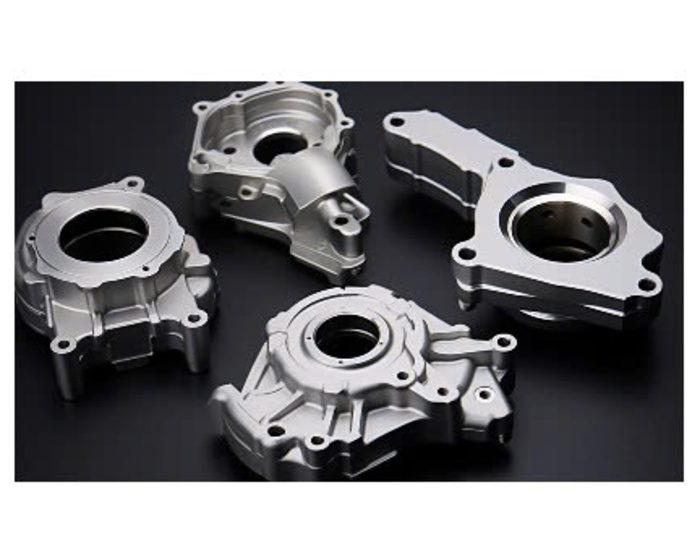
Aluminum Die Casting Technology to Minimize Flow Marks Caused by Metal flow
Aluminum die-casting is the ideal for products that require complex designs and high precision. We meet a wide range of customer needs with our advanced manufacturing technology, capable of producing products up to 6.5kg with a wall thickness of 2-3mm. Our proprietary casting technology minimizes defects, such as flow marks caused by metal flow, ensuring high-quality products. In recent years, the demand for lightweight aluminum components has been increasing in the automotive and home appliance industries, requiring a combination of high precision and superior production efficiency. However, defects like the flow marks in the manufacturing process poses a significant challenge. At Yamaguchi, we address this issue with advanced casting technology and a system of die-casting machines ranging from 420 tons to 800 tons. With a fully integrated production system, we provide high-quality die-cast products from design to completion. Key Features of Yamaguchi's Aluminum Die-Casting Technology: ✅ Technology to minimize flow marks Strict control of mold temperature and molten metal temperature to ensure product surface quality. Regular mold maintenance to prevent defects during the casting process. ✅ Diverse and flexible equipment system Equipped with die-casting machines from 420 tons to 800 tons, supporting a wide range of production, from large components (up to 6.5kg) to thin-walled designs (2-3mm). ✅ High-Efficiency Production with Integrated Manufacturing From design, casting, finishing, to quality inspection, all are performed in-house at Yamaguchi, helping to shorten delivery times and ensure consistent quality. Technical Specifications: ✔ Weight Capacity: Up to 6.5kg ✔ Product thickness: 2-3mm ✔ Equipment used: 800-ton die-casting machine BD-V7EX; 420-ton die-casting machine SD-420CH; Spraying robots; Vacuum machine; Mold release agent mixer; Shot blasting machine; Rotary electric furnace Quality Assurance & Production System: 🔹 Strict quality control Use of elemental analyzer to ensure the stability of raw materials. 🔹 Advanced technology Modern die-casting systems, vacuum equipment, and shot blasting machines, enabling manufacturing of complex-shaped components with high precision. 🔹 Fast & Reliabe Delivery With a fully integrated production system, we offer short lead times and on-time delivery, always adapting to customer schedules. Our aluminum die casting technology ensures minimal flow marks through precise control of mold and molten metal temperatures, as well as injection volume management. Equipped with 420T–800T die casting machines and advanced inspection systems, we cater to a wide range of industries, from automotive to industrial machinery. By handling everything from design to finishing in-house, we provide high-quality, cost-effective, and timely solutions.
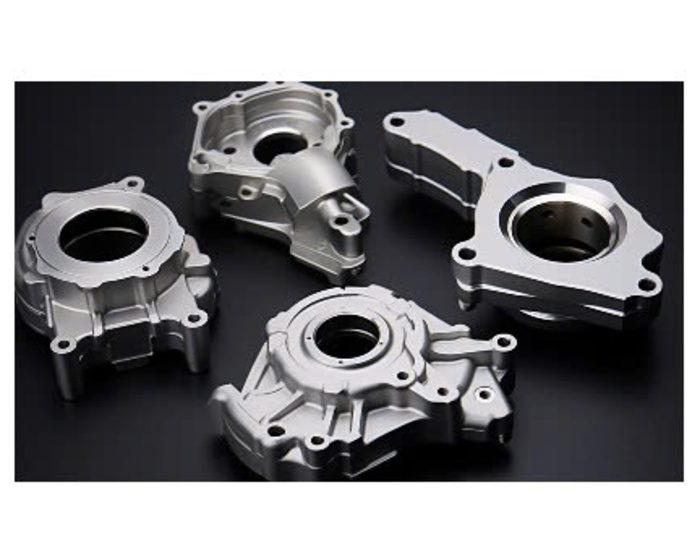
Aluminum Die-Casting Process Minimizes Mold Sticking Problems
"Sticking" refers to the phenomenon in die casting where molten aluminum adheres to the surface of the mold. This issue significantly impacts productivity and quality in die casting. Main Causes of Sticking: 🔹 Uneven Temperature Distribution If the mold temperature is not properly controlled, molten aluminum is more likely to adhere abnormally to the mold surface. 🔹 Improper Use of Release Agents Insufficient or improper application of release agents can cause the product to stick to the mold, making removal difficult. 🔹 Substandard Mold Material and Surface Treatment If the mold surface is not properly treated, the friction between the aluminum and the mold increases, leading to sticking. Problems Caused by Sticking: ❌ Reduced Product Quality Surface defects on finished products can deteriorate performance, which is especially critical for automotive parts and electronic control components requiring high precision. ❌ Reduced Production Efficiency Frequent mold cleaning to remove adhered aluminum buildup slows down production. ❌ Reduced Mold Lifespan Adhered aluminum layers can damage the mold, increasing maintenance and replacement costs. Our Sticking Prevention Measures: ✅ Optimized Release Agent Selection & Application We select the appropriate mold release agent for each product, ensuring even spraying across the entire mold surface to prevent aluminum from sticking. ✅ Automated Spraying with Robots Using spray robots ensures uniform coating of release agents, effectively preventing sticking and surface defects. ✅ Strict Mold Temperature Control We apply advanced mold temperature control systems to maintain stable temperatures and prevent aluminum from sticking or causing dimensional deformations. ✅ Mold Surface Treatment with Special Coatings We use anti-stick coatings to reduce friction between aluminum and the mold, minimizing sticking. ✅ Continuous Process Improvement We regularly review our production processes to identify and eliminate factors contributing to sticking. Outstanding Advantages of Yamaguchi's Aluminum Die-Casting Technology: 🔹 Equipped with 420T–800T die casting machines to meet diverse manufacturing needs. 🔹 Production of components weighing up to 6.5kg. 🔹 Monthly production capacity of approximately 65,000 units. 🔹 In-house finishing processing ensures high quality and fast delivery times. Sticking is a major issue in the aluminum die-casting industry, directly affecting product quality and production efficiency. At Yamaguchi, we minimize sticking by precise temperature control, optimized release agent application, and specialized mold coatings. As a result, we provide products with high precision and durability, meeting the stringent standards of the automotive and other industries.
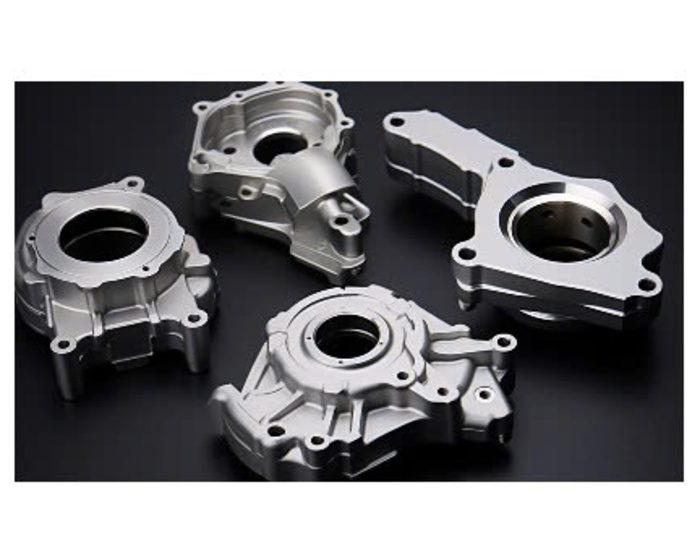
Aluminum Die Casting with Minimized Discoloration
"Discoloration" refers to changes in the surface color of a metal due to manufacturing processes or environmental factors. In aluminum die casting, discoloration can occur after casting, significantly impacting product quality and customer perception. This issue is particularly critical for products that require high aesthetic and surface finish standards. [Main Causes of Discoloration] Oxidation During Casting Aluminum is highly prone to oxidation. If the product surface comes into contact with oxygen during casting and cooling, an oxide layer forms, leading to color changes. Improper Use of Release Agents Release agents are essential for ensuring proper separation between the mold and the product. However, if the release agent contains incompatible chemical components, it can trigger undesirable reactions, causing discoloration. Cooling Process Issues Rapid or uneven cooling can alter the surface crystal structure, leading to color inconsistencies. [Yamaguchi’s Discoloration Control Solutions] Although discoloration is a major challenge in aluminum die casting, it can be effectively controlled through proper techniques and management. With years of expertise, Yamaguchi has developed a specialized manufacturing process that significantly minimizes discoloration, ensuring high-quality surface finishes that meet customer expectations. [Key Features of Our Aluminum Die Casting Technology] Discoloration Prevention Technology We carefully select and apply optimal release agents, significantly reducing discoloration during the casting process and achieving a high-quality finish. Versatile Manufacturing Capability Equipped with 420T to 800T die casting machines, we can accommodate a wide range of product sizes. Integrated Production System Our in-house manufacturing process, from casting to precision machining and final finishing, ensures both high quality and short lead times. [Equipment] BD-V7EX800T Aluminum Die Casting Machine SD-420CH Aluminum Die Casting Machine Shot Blasting Machine [Quality Assurance & Production System] Strict Quality Control We conduct thorough inspections at every stage, from casting to finishing, ensuring consistent appearance and precision. Advanced Equipment & Expertise Using cutting-edge die casting machines and shot blasting technology, we achieve high uniformity, even for complex-shaped products. Flexible & Fast Delivery By optimizing our production schedule, we offer rapid and adaptable delivery timelines to meet customer demands. [High-Quality, Aesthetically Superior Die Cast Products] Discoloration in aluminum die casting is caused by oxidation, cooling irregularities, and improper release agent use, affecting both appearance and quality. At Yamaguchi, we minimize discoloration through optimized release agents and precise process control, ensuring high-quality, visually appealing products. Our reliable die-cast components are widely used in industries such as automotive manufacturing, where both durability and aesthetics are paramount.
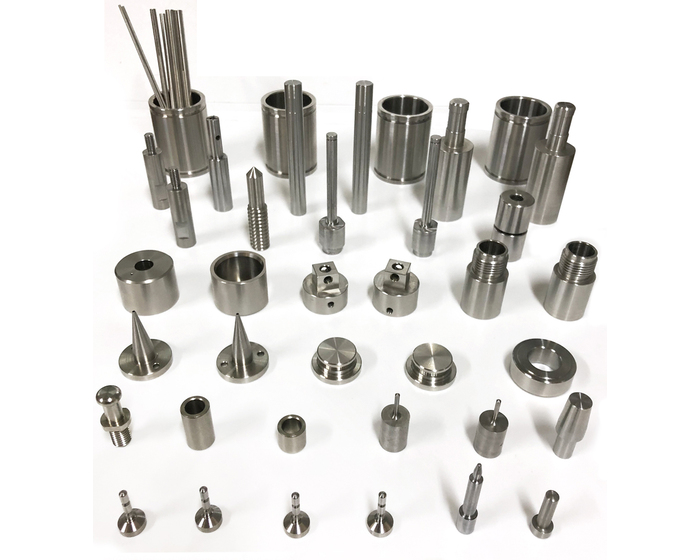
MACHINED PARTS
We offer a diverse range of CNC machining in single items as well as mass production, working with a variety of materials including: - Stainless steel SUS316, SUS304, SUS303, SUS440C,... One of the main advantages is our ability to machine on stainless steel material. - Steel S55C, S50C, S45C, SS400,... - Steel SKD11, SKD61, NAK80, P20,... - Aluminium A2017, A7075, A6061, A5052,... - Copper & Brass C3604, C1100, Becu,... - Plastic POM, MC, PMMA, PET, Peek, Bakelit,...
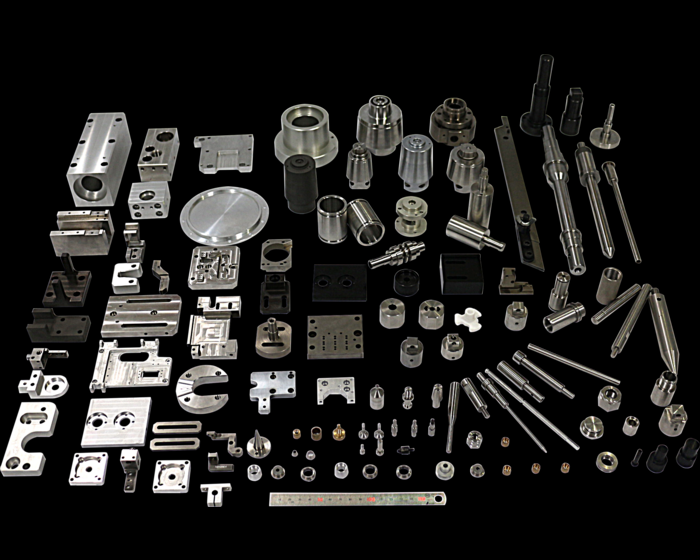
MACHINED PARTS
We offer a diverse range of CNC machining in single items as well as mass production, working with a variety of materials including: - Stainless steel SUS316, SUS304, SUS303, SUS440C,... One of the main advantages is our ability to machine on stainless steel material. - Steel S55C, S50C, S45C, SS400,... - Steel SKD11, SKD61, NAK80, P20,... - Aluminium A2017, A7075, A6061, A5052,... - Copper & Brass C3604, C1100, Becu,... - Plastic POM, MC, PMMA, PET, Peek, Bakelit,...
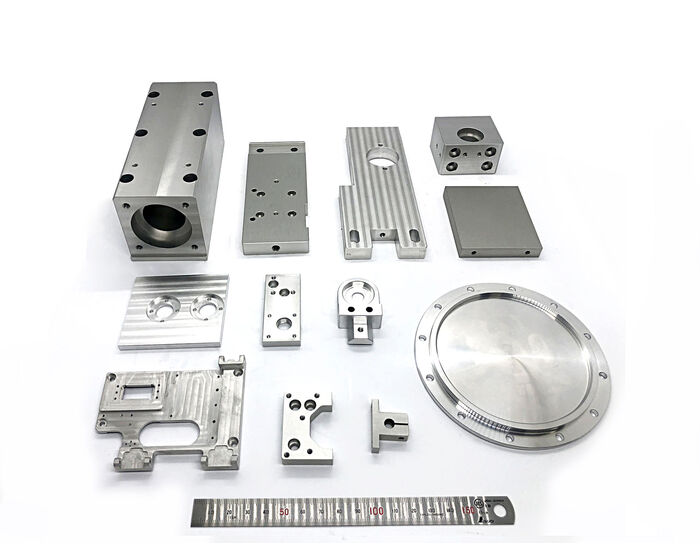
MACHINED PARTS
We offer a diverse range of CNC machining in single items as well as mass production, working with a variety of materials including: - Stainless steel SUS316, SUS304, SUS303, SUS440C,... One of the main advantages is our ability to machine on stainless steel material. - Steel S55C, S50C, S45C, SS400,... - Steel SKD11, SKD61, NAK80, P20,... - Aluminium A2017, A7075, A6061, A5052,... - Copper & Brass C3604, C1100, Becu,... - Plastic POM, MC, PMMA, PET, Peek, Bakelit,...
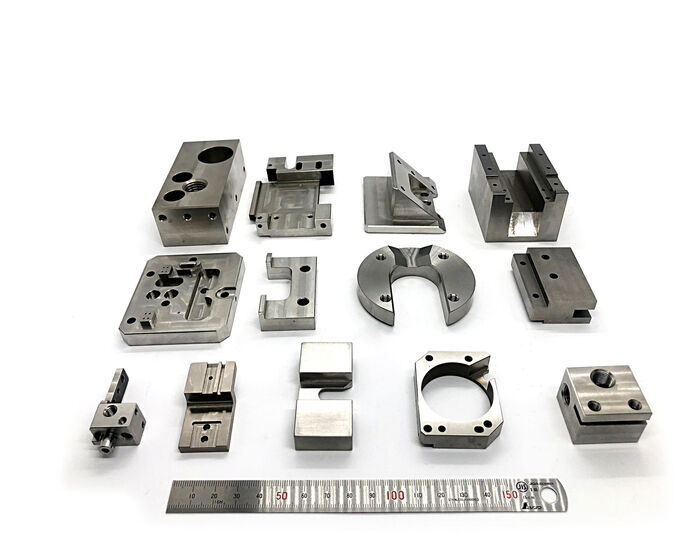
MACHINED PARTS
We offer a diverse range of CNC machining in single items as well as mass production, working with a variety of materials including: - Stainless steel SUS316, SUS304, SUS303, SUS440C,... One of the main advantages is our ability to machine on stainless steel material. - Steel S55C, S50C, S45C, SS400,... - Steel SKD11, SKD61, NAK80, P20,... - Aluminium A2017, A7075, A6061, A5052,... - Copper & Brass C3604, C1100, Becu,... - Plastic POM, MC, PMMA, PET, Peek, Bakelit,...
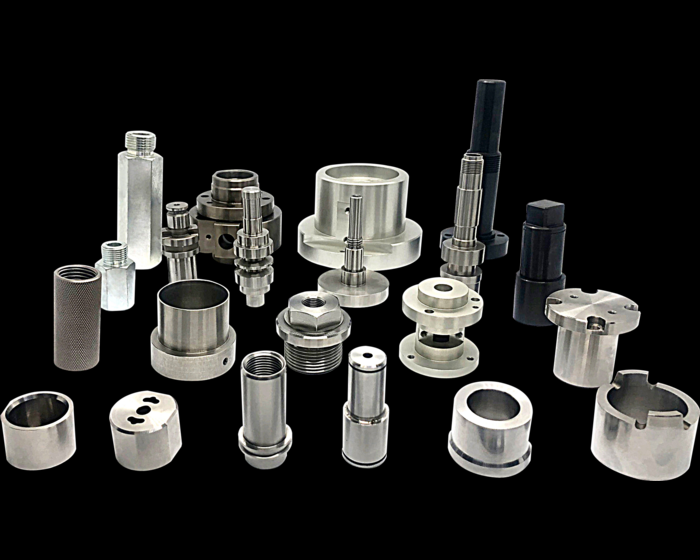
MACHINED PARTS
We offer a diverse range of CNC machining in single items as well as mass production, working with a variety of materials including: - Stainless steel SUS316, SUS304, SUS303, SUS440C,... One of the main advantages is our ability to machine on stainless steel material. - Steel S55C, S50C, S45C, SS400,... - Steel SKD11, SKD61, NAK80, P20,... - Aluminium A2017, A7075, A6061, A5052,... - Copper & Brass C3604, C1100, Becu,... - Plastic POM, MC, PMMA, PET, Peek, Bakelit,...
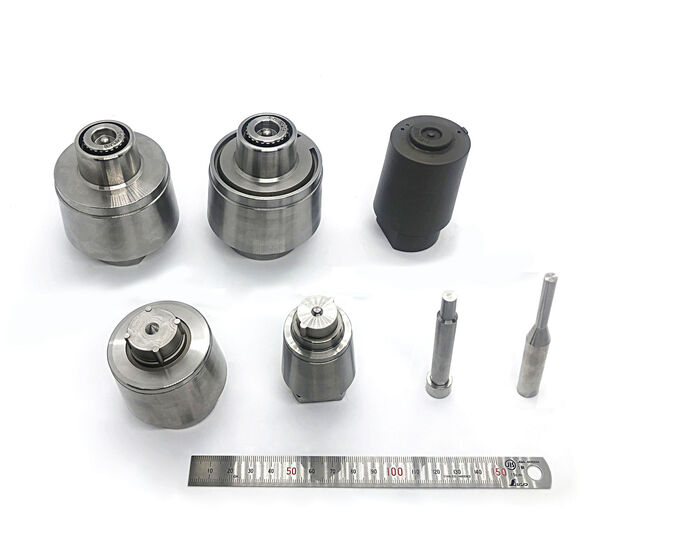
MACHINED PARTS
We offer a diverse range of CNC machining in single items as well as mass production, working with a variety of materials including: - Stainless steel SUS316, SUS304, SUS303, SUS440C,... One of the main advantages is our ability to machine on stainless steel material. - Steel S55C, S50C, S45C, SS400,... - Steel SKD11, SKD61, NAK80, P20,... - Aluminium A2017, A7075, A6061, A5052,... - Copper & Brass C3604, C1100, Becu,... - Plastic POM, MC, PMMA, PET, Peek, Bakelit,...
CONTACT