SERVICE
Production Goods & Services
28hits
Narrow by category
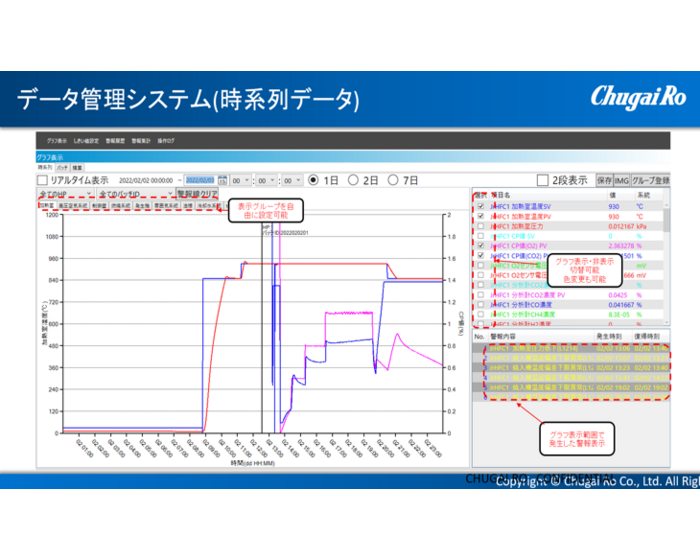
CRism®: Smart Facility Operations with Remote Monitoring and Data Analysis
This advanced system enables remote facility monitoring and supports efficiency in facility management with threshold settings and a variety of data analysis capabilities. The CRism® Maintenance System is a remote monitoring system developed to enhance the efficiency of facility management. It allows for real-time remote monitoring of facility operations, enabling administrators to effectively manage and understand the status of equipment. Equipped with data visualization capabilities, it allows for intuitive understanding of operational statuses, facilitating rapid decision-making. Additionally, setting thresholds enhances anomaly detection and preventive maintenance. Through various data analysis options, deep understanding of facility data and optimal maintenance planning are possible. ■ Features - Visualization capabilities: Visually displays numerical data, allowing for a concise grasp of the facility’s condition. - Threshold setting capabilities: Easy to set thresholds enable proactive responses before anomalies occur. - Diverse data analysis: Detailed analysis of facility data contributes to optimizing operational efficiency and maintenance plans. - Remote monitoring: Monitor the condition of facilities from remote locations without the need to visit, enabling faster responses. ■ Specifications - System name: CRism® Maintenance System - Key functions: Data visualization, threshold setting, data analysis, remote monitoring - Target equipment: Various industrial facilities ■ Applications The CRism® Maintenance System is suitable for a wide range of industrial facilities, particularly for the following applications: - Preventive maintenance: Reduces the risk of equipment failure through anomaly detection and preventive maintenance responses. - Operational optimization: Supports efficient operation plans through monitoring of operational statuses and data analysis. - Cost reduction: Remote monitoring reduces labor costs and local response costs in facility management. By implementing the CRism® Maintenance System, the burden of maintenance work can be reduced, and both the operation rate and lifespan of facilities can be improved. CHUGAI RO (THAILAND) CO., LTD. is based in Bangkok, Thailand, and provides services throughout the country. ■ For more details, please download the PDF or feel free to contact us.
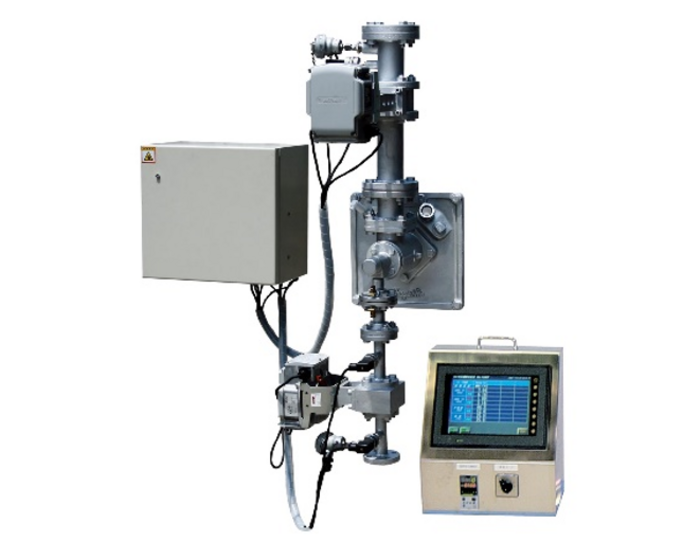
EBC-i Automatic Air-Fuel Ratio Control System: Combustion Efficiency Through Precise Flow Control
The EBC-i Automatic Air Ratio Control System utilizes temperature and pressure correction functions to achieve high-precision flow control, supporting stable combustion and improved efficiency in industrial furnaces. The EBC-i Automatic Air Ratio Control System is an advanced control system developed to achieve optimal combustion efficiency in industrial furnaces. Equipped with correction functions to accommodate fluctuations in temperature and pressure, it enables highly precise flow control and measurement. This ensures that the air ratio remains consistent regardless of changes in combustion volume, maintaining a stable furnace atmosphere and supporting improved combustion efficiency and stable operation. Designed to perform in high-temperature and high-pressure environments, it also contributes to enhanced reliability for long-term operation in industrial furnaces. ■ Features - High-precision flow control and measurement: Achieves stable flow control adapted to changes in external conditions with temperature and pressure correction functions. - Prevention of air ratio deviations: Maintains a consistent air ratio even during changes in combustion volume. - Stable furnace atmosphere maintenance: Enables efficient combustion by maintaining a constant atmosphere within industrial furnaces. - Flexible burner settings: Allows configuration of up to eight patterns for burner combustion volumes and air ratios, enhancing operational flexibility. - Abnormality memory and output functions: Records and outputs system abnormalities, ensuring reliability as a safety measure. ■ Specifications - Product name: EBC-i Automatic Air Ratio Control System - Key functions: Temperature and pressure correction, high-precision flow control, furnace atmosphere management - Configurable patterns: Burner control with up to 8 patterns - Safety features: Abnormality memory and output functions ■ Applications The EBC-i Automatic Air Ratio Control System is suitable for various industrial furnaces and is particularly beneficial for the following applications: - Preventive maintenance: Prevents combustion abnormalities in furnaces by maintaining a stable air ratio. - Efficient operational management: Optimizes combustion efficiency through high-precision flow control and measurement. - Enhanced safety: Strengthens safety management systems with abnormality memory and output functions. The introduction of the EBC-i Automatic Air Ratio Control System improves the combustion efficiency and stability of industrial furnaces and contributes to the reduction of long-term operational costs. CHUGAI RO (THAILAND) CO., LTD. is based in Bangkok, Thailand, and provides services throughout the country. ■ For more details, please download the PDF or feel free to contact us.
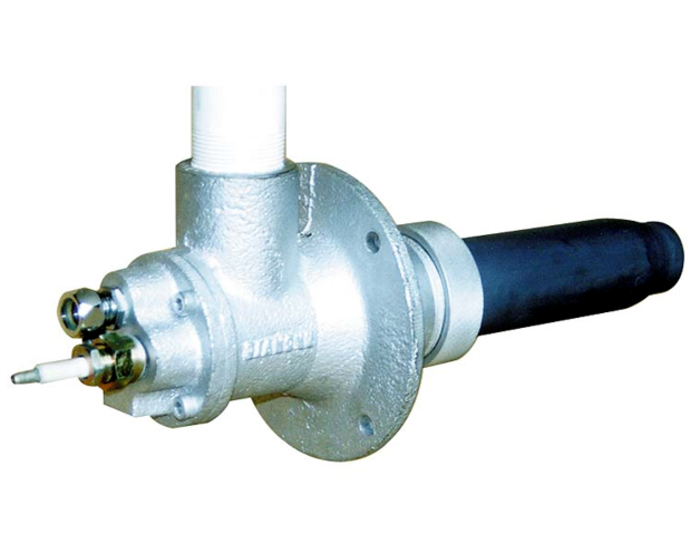
Hydrogen Burner Series: Zero CO2 Emissions for an Eco-Friendly Heat Source Solution
The Hydrogen Burner Series delivers a next-generation thermal energy solution with zero CO2 emissions, low NOx emissions, and high safety, offering an environmentally friendly option. The Hydrogen Burner Series is a next-generation burner developed to achieve clean thermal processing with minimal environmental impact. By completely eliminating the use of fossil fuels, it achieves zero CO2 emissions, contributing significantly to global warming countermeasures. Additionally, its low NOx technology reduces the emission of harmful substances, making it suitable for use in regions with stringent environmental regulations. Designed with a focus on safety, it features multiple safety functions to ensure secure and stable operation. As a burner that supports sustainable energy supply, it is widely applicable across various industrial sectors. ■ Features - Zero CO2 emissions: Designed to operate without fossil fuels, achieving zero CO2 emissions to prioritize environmental protection. - Low NOx technology: Significantly reduces harmful substances in exhaust gases for environmentally friendly operation. - High safety: Equipped with multiple safety functions, including anomaly detection and shutdown features, to ensure operational safety. - Clean energy utilization: Contributes to the realization of clean energy systems by using hydrogen fuel. - Wide applicability: Complies with strict environmental standards, suitable for industrial furnaces, power generation facilities, and other systems. ■ Specifications - Model: Hydrogen Burner Series - Key features: Zero CO2 emissions, low NOx emissions - Safety features: Equipped with a multi-layer safety system - Applications: Industrial furnaces, power generation, and other thermal energy demands ■ Applications The Hydrogen Burner Series is suitable for industrial furnaces, power generation facilities, and processes requiring thermal energy. It is particularly effective in the following applications: - Industrial furnaces: Provides stable heating within industrial furnaces with clean combustion. - Power generation: Achieves zero CO2 emissions by utilizing hydrogen fuel, reducing environmental impact at power plants. - Other thermal energy demands: Supports sustainable energy supply in industries such as manufacturing and chemical processing. The Hydrogen Burner Series is an optimal solution for addressing global warming and reducing the environmental impact of the industrial sector, meeting the needs of many businesses. CHUGAI RO (THAILAND) CO., LTD. is based in Bangkok, Thailand, and provides services throughout the country. ■ For more details, please download the PDF or feel free to contact us.
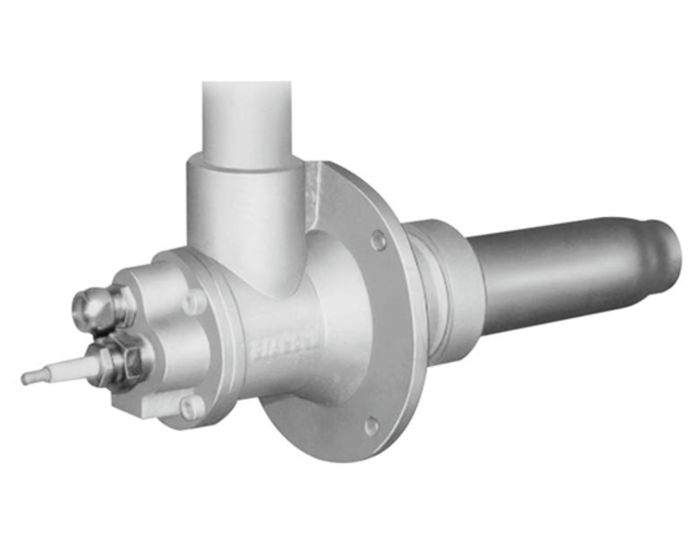
HSGB Gas Burner: Easy Installation and Simple Maintenance
The HSGB High-Speed Gas Burner combines easy installation and high flame speed, offering a compact design for direct ignition burners that meet diverse furnace heating needs. The HSGB High-Speed Gas Burner is a compact and lightweight direct ignition burner with high flame speed and flexible combustion options. Designed as an efficient heat source for furnaces, it supports a wide range of combustion modes, from low air ratio combustion to ultra-excess air combustion, meeting the demands of various heat treatment processes. Its flexibility makes it suitable for diverse applications. Additionally, its compact design and easy installation reduce time and costs for setup and maintenance. This burner is ideal for industries such as ceramics, metal processing, and glass treatment. ■ Features - Adjustable high flame speed: Flame speed can be adjusted from low to high, accommodating diverse heating requirements. - Combustion flexibility: Supports a wide range of combustion modes, from low air ratio to ultra-excess air combustion. - High thermal efficiency: Achieves high thermal efficiency despite its compact design. - Easy installation: Allows for quick setup, reducing workload. - Simple maintenance: Designed for easy routine inspections and maintenance. ■ Specifications - Model: HSGB - Design: Slim, tile-less construction - Ignition method: Direct ignition - Fuel type: Gas - Applications: Continuous kilns for ceramics, batch furnaces, metal heating furnaces, glass heating furnaces ■ Applications The HSGB High-Speed Gas Burner is suitable for various furnace types and ideal for the following applications: - Ceramic continuous kilns: Roller hearth kilns, tunnel kilns - Batch furnaces: Shuttle kilns, corner jet kilns - Metal heating and heat treatment furnaces: Perfect for heating and heat treatment processes of metal materials. - Glass heating and processing furnaces: Serves as an efficient heat source for glass processing and heat treatment. The HSGB High-Speed Gas Burner is the ideal solution for customers seeking improved thermal efficiency and operational flexibility. CHUGAI RO (THAILAND) CO., LTD. is based in Bangkok, Thailand, and provides services throughout the country. ■ For more details, please download the PDF or feel free to contact us.
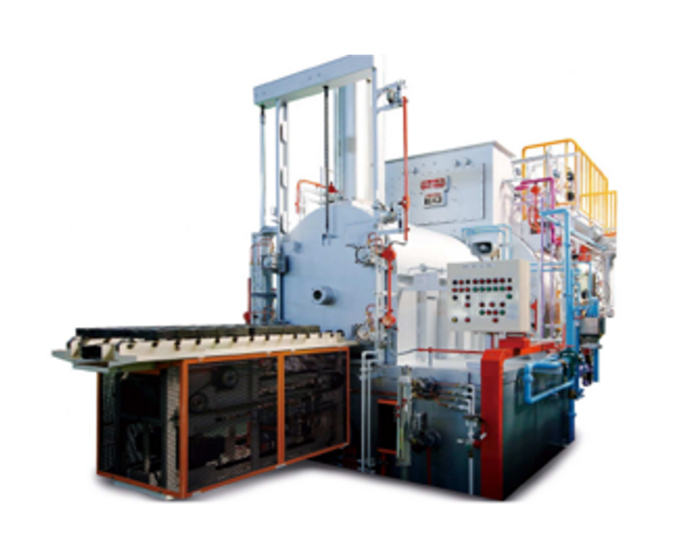
HI-SHIFTER™ Batch Type Gas Carburizing Furnaces
HI-SHIFTER™ is a batch-type gas carburizing furnace that combines high efficiency and safety, designed to meet diverse heat treatment needs. Developed as Japan's first gas carburizing machine, HI-SHIFTER™ is a batch-type gas carburizing furnace capable of accommodating various heat treatment processes. It expands its application range beyond carburizing to include clean heat treatment, meeting the varied demands of modern factories. The latest model, “Flameless HI-SHIFTER™,” is equipped with a vacuum chamber and an advanced vacuum exhaust system, further enhancing safety and energy efficiency. This enables reduced operational workload and efficient process management. ■ Features - Supports various heat treatment processes: Capable of both carburizing and clean heat treatment processes. - Market-leading reliability: High reliability with a proven track record in Japan’s gas carburizing furnace market. - Enhanced safety: Vacuum chamber implementation ensures worker safety. - Labor and energy savings: Adoption of the latest technology enables efficient operation and resource savings. - Flameless design: The “Flameless HI-SHIFTER™” enhances safety and environmental performance. ■ Specifications - Type: General-purpose batch type - Applicable processes: Gas carburizing, clean heat treatment - Features: Equipped with a vacuum chamber and vacuum exhaust system - Purpose: Improved efficiency, safety, and energy performance ■ Applications HI-SHIFTER™ is suitable for the following applications: - Metal processing industry: High-precision and efficient carburizing processes. - Automotive parts manufacturing: Heat treatment to enhance the durability of gears, shafts, and other components. - Aircraft manufacturing: Processing of parts requiring high quality and safety standards. - Clean energy sector: Environmentally friendly heat treatment processes. HI-SHIFTER™ is an optimal solution for modern manufacturing industries that seek efficient and safe heat treatment. It is highly regarded by many companies as a key device supporting future heat treatment processes. CHUGAI RO (THAILAND) CO., LTD. is based in Bangkok, Thailand, and provides services throughout the country. ■ For more details, please download the PDF or feel free to contact us.
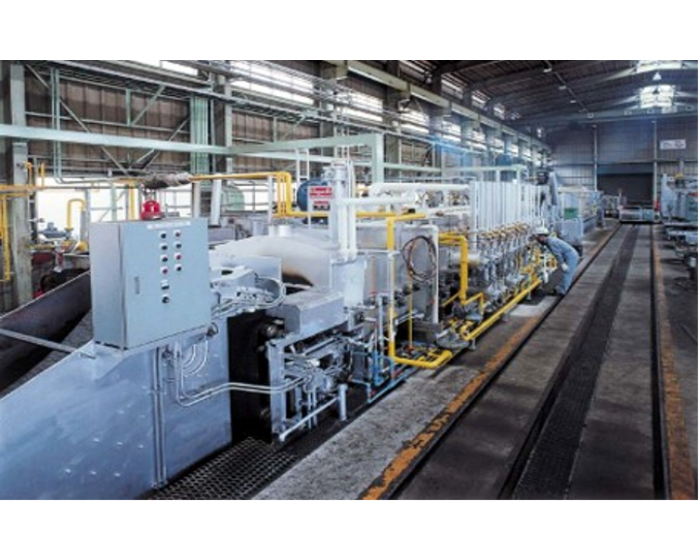
Mesh V-belt Furnace for Hardening: From Hardening to Tempering
The Mesh Belt Furnace is a fully automated device that performs heat treatment on small parts while maintaining their shape, achieving high energy efficiency to reduce costs. The Mesh Belt Furnace is a high-performance heat treatment device designed specifically for small parts, capable of supporting processes like hardening, tempering, and carburizing. It is equipped with multiple sizes of mesh belts to accommodate various parts, such as screws, irregularly shaped bearings, and needle bearings. Its unique natural hardening process helps maintain the shape of parts, minimizing deformation to ensure high quality. The fully automated process allows efficient operations from material loading to tempering, with excellent operability. Additionally, its design emphasizes energy efficiency, further reducing operational costs. ■ Features - Supports various parts: Specially designed for small parts, ideal for hardening, tempering, and carburizing processes. - Shape retention: The natural hardening process prevents deformation, ensuring high-precision processing. - Fully automated process: Automatically performs from material loading to tempering, improving work efficiency. - Improved energy efficiency: Designed for high energy efficiency to reduce operational costs. ■ Specifications - Functions: Hardening, tempering, carburizing - Type: Mesh Belt Furnace - Automation level: Fully automated - Energy efficiency measures: High-efficiency, energy-saving design ■ Applications The Mesh Belt Furnace is suitable for heat treatment of small parts in various industries, particularly for the following applications: - Heat treatment of screws and small metal parts: Achieves high-precision hardening and tempering. - Processing of bearings: Emphasizes shape retention for irregular and needle bearings. - Carburizing treatment of precision parts: Enhances the durability of high-quality parts. The Mesh Belt Furnace is the ideal heat treatment solution for companies aiming to maintain part shape and achieve high energy efficiency. CHUGAI RO (THAILAND) CO., LTD. is based in Bangkok, Thailand, and provides services throughout the country. ■ For more details, please download the PDF or feel free to contact us.
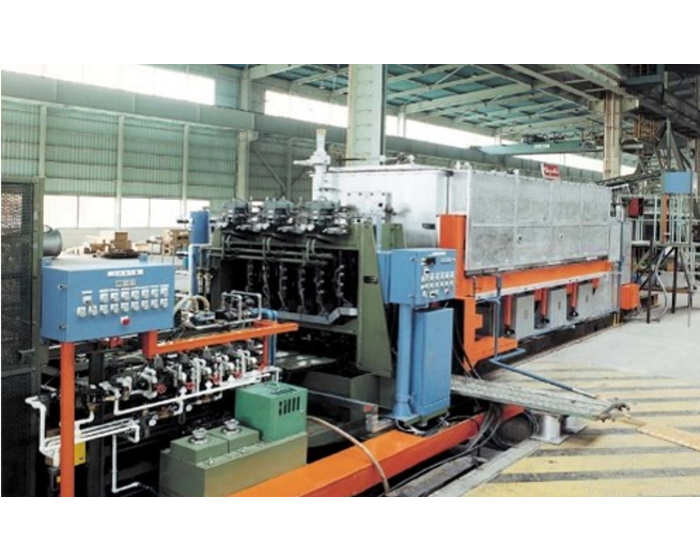
Press Quenching Equipment for High-Precision Parts
"The Press Hardening Equipment is designed to pursue dimensional accuracy for automotive parts, achieving high-quality finishes with rapid heat treatment following induction heating. Our Press Hardening Equipment is the ideal solution for heat treatment processes requiring high dimensional accuracy, such as those used in automotive parts. It supports parts like gears and bearings, where dimensional precision directly affects product quality, enabling rapid hardening after induction heating. This equipment is compatible with various furnace types, including mesh belt furnaces, rotary furnaces, and roller hearth furnaces, accommodating a wide range of heat treatment processes. Utilizing consistent quality control and the latest technology, it guarantees enhanced energy efficiency and high-precision results. ■ Features - Dimensional accuracy and precision: Ensures high dimensional accuracy for parts after heat treatment. - Compatibility with various furnaces: Can be combined with mesh belt furnaces, rotary furnaces, and roller hearth furnaces. - Induction heating capability: Allows rapid press hardening after induction heating, improving process efficiency. - High-quality assurance: Supports reliable parts manufacturing through consistent quality control. - Improved energy efficiency: Utilizes the latest technology to reduce operating costs with energy-efficient operation. ■ Specifications - Compatible furnace types: Mesh belt furnace, rotary furnace, roller hearth furnace - Suitable parts: Automotive gears, bearings, etc. - Function: Supports press hardening after induction heating - Heating system: Induction heating ■ Applications The Press Hardening Equipment is highly effective in the following applications: - Heat treatment of automotive parts: Maintains dimensional accuracy of gears and bearings, achieving high durability. - Processing of precision mechanical parts: Ideal for heat treatment processes where high precision is required. - Manufacturing of complex-shaped parts: Provides precise heat treatment with minimal deformation. Our Press Hardening Equipment is the ideal heat treatment solution for companies prioritizing dimensional accuracy. It balances energy efficiency with high product quality, meeting the needs of various industries. CHUGAI RO (THAILAND) CO., LTD. is based in Bangkok, Thailand, and provides services throughout the country. ■ For more details, please download the PDF or feel free to contact us."
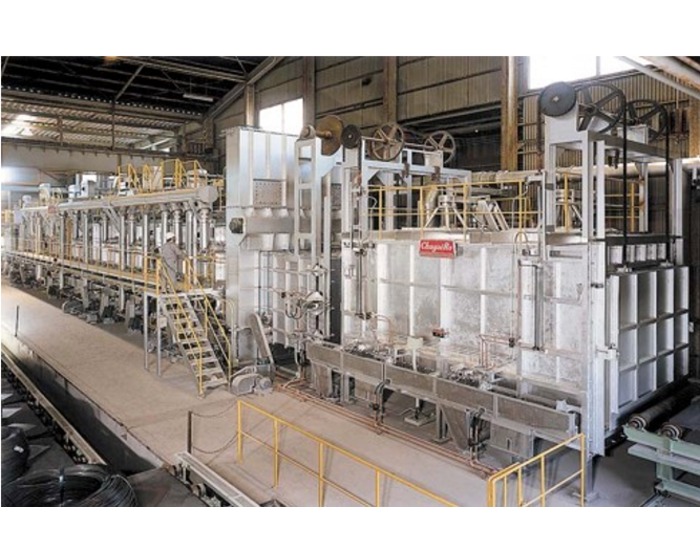
Wire Rod Coil Annealing Furnace: Energy-Efficient Quality Improvement Technology
Our dedicated annealing furnace for wire rod coils is an optimal solution that pursues quality improvement and energy efficiency, capable of handling both mass production and small-lot, multi-variety production. The annealing furnace developed by our company is optimized for the continuous annealing process of coils that have undergone hot rolling or cold drawing. This furnace uses N-gas, generated from the combustion exhaust gas of radiant tubes, as the atmosphere gas, achieving high-quality annealing. Additionally, with the adoption of a vacuum chamber and radiant tubes equipped with recuperators, energy efficiency is improved, contributing to reduced production costs. The furnace’s flexibility allows it to handle a wide range of needs, from mass production to small-lot, multi-variety production. ■ Features - Improved quality stability: Stabilizes annealing process quality using N-gas derived from radiant tube combustion exhaust gas. - Enhanced energy efficiency: Vacuum chamber and heat recovery design enable energy-efficient operation. - Accommodates diverse production needs: Flexible operation supports both mass production and small-lot, multi-variety production. - Reduced production costs: Overall cost reduction achieved through quality improvement and efficiency. ■ Specifications - Gas type: N-gas (derived from radiant tube combustion exhaust gas) - Vacuum chamber: Vacuum chamber design - Radiant tube: High-efficiency design utilizing heat recovery - Target products: Hot-rolled or cold-drawn steel wire coils ■ Applications The dedicated annealing furnace for wire rod coils is highly effective in the following applications: - Processing of hot-rolled coils: Ensures high-quality finish and stable processing. - Processing of cold-drawn coils: Enhances dimensional accuracy and durability. - Small-lot, multi-variety production: Flexible processing for coils of different specifications. The dedicated annealing furnace for wire rod coils is a reliable choice for manufacturers seeking quality improvement and energy efficiency. Through efficient heat treatment, it enables the production of better products more efficiently. CHUGAI RO (THAILAND) CO., LTD. is based in Bangkok, Thailand, and provides services throughout the country. ■ For more details, please download the PDF or feel free to contact us.
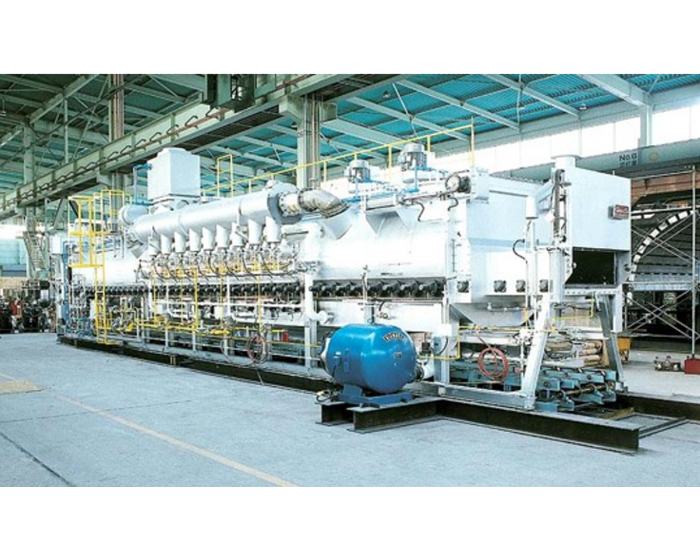
Radiant Tube Fired Annealing Furnaces for Cold Forming Materials
The Radiant Tube Kiln is a high-efficiency firing device that achieves a 20% reduction in fuel consumption, enhancing the quality of cold-formed materials and supporting a sustainable production process. Our Radiant Tube Kiln is specifically designed for the annealing process of cold-formed materials. By utilizing a Roller Hearth system and lightweight trays and baskets, it reduces fuel consumption by 20% compared to conventional systems. Additionally, it significantly improves overall energy efficiency by effectively utilizing the heat and combustion gases generated from the cooling process and hydrocarbon immersion zones. The vacuum chambers installed at the material loading and unloading areas further reduce atmospheric gas usage, supporting an energy-efficient and environmentally friendly production process. ■ Features - 20% reduction in fuel consumption: Adopts a Roller Hearth system and lightweight trays to cut fuel use. - Enhanced energy efficiency: Utilizes heat from the cooling process and combustion gases to reduce unnecessary energy usage. - Vacuum chamber installation: Reduces atmospheric gas usage, achieving further energy savings. - Improved quality: Optimal temperature control enhances the quality and durability of cold-formed materials. - Sustainable production: Efficient energy use supports a sustainable, environmentally conscious process. ■ Specifications - Material type: Cold-formed materials - Fuel reduction technology: Lightweight design in the Roller Hearth system - Energy recovery utilization: Heat recovery from the cooling process and combustion gases - Vacuum chamber installation: Vacuum chambers at material loading and unloading areas ■ Applications The Radiant Tube Kiln is ideal for the heat treatment process of cold-formed materials and is highly effective for the following applications: - Annealing of cold-formed materials: Maintains product durability and dimensional accuracy with stable quality control. - Production lines requiring energy cost reduction: Fuel-saving technology reduces operational costs, providing long-term cost benefits. - Environmentally friendly production processes: Energy-saving design enables sustainable production activities. The Radiant Tube Kiln ensures a high-quality finish for cold-formed materials and supports the establishment of an efficient, environmentally friendly production system. CHUGAI RO (THAILAND) CO., LTD. is based in Bangkok, Thailand, and provides services throughout the country. ■ For more details, please download the PDF or feel free to contact us.
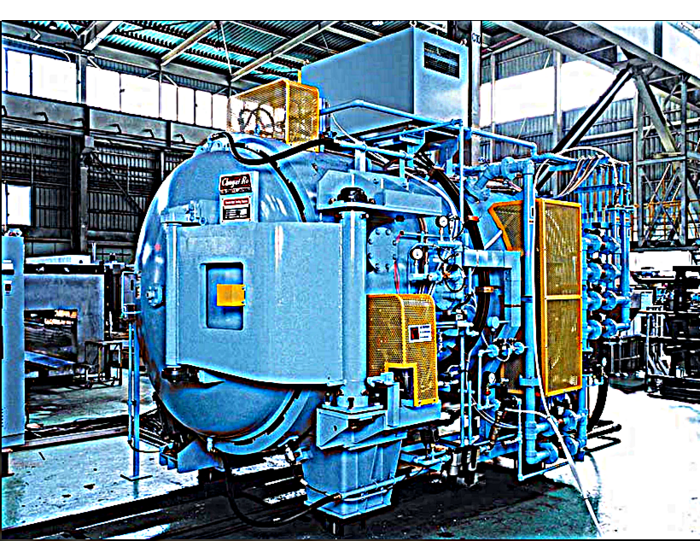
Vacuum Heat Treating Furnaces VF/VFV Series
The VF/VFV Series Vacuum Heat Treatment Furnace provides stable quality with high-performance cooling and space-saving design, accommodating various heat treatment processes. The VF/VFV Series Vacuum Heat Treatment Furnace is a multifunctional vacuum furnace that delivers high performance in a compact design. It supports a variety of heat treatment processes, including hardening, tempering, solution hardening, annealing, recrystallization, and brazing, offering the flexibility to meet diverse factory needs. Its integrated design allows heating and cooling in the same chamber, enabling efficient, space-saving installation. Additionally, it features gas cooling up to 1MPa and a patented cooling control function, ensuring rapid and stable cooling. The VF series (horizontal type) is suitable for standard heat treatments, while the VFV series (vertical type) is ideal for processing long materials. ■ Features - Supports various heat treatment processes: Suitable for hardening, tempering, solution hardening, annealing, recrystallization, brazing, and more - Space-saving design: Integrated heating and cooling reduces installation space requirements - High-performance cooling function: Efficient cooling with gas cooling up to 1MPa - Patented cooling control: Ensures consistent heating quality with patented cooling control functionality - Variety of models: VF series (horizontal) for standard heat treatment, VFV series (vertical) for long material processing ■ Specifications - Series: VF (horizontal), VFV (vertical) - Heating and cooling chamber: Integrated design - Cooling function: Gas cooling up to 1MPa - Patent: Patented cooling control function ■ Applications The VF/VFV Series Vacuum Heat Treatment Furnace performs excellently in the following applications: - Strengthening metal parts: Enhances strength through hardening and tempering - Manufacturing automotive parts: Provides high-precision heat treatment for gears, shafts, etc. - Manufacturing aircraft parts: Ideal for annealing and brazing high-quality parts - Processing long materials: Efficient heating and cooling of long materials using the VFV series The VF/VFV Series Vacuum Heat Treatment Furnace supports high-quality product manufacturing across industries by pursuing quality stability and energy efficiency. CHUGAI RO (THAILAND) CO., LTD. is based in Bangkok, Thailand, and provides services throughout the country. ■ For more details, please download the PDF or feel free to contact us.
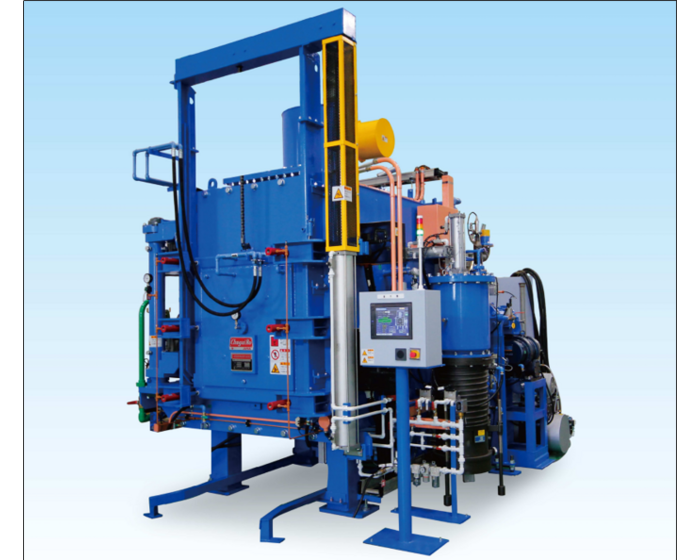
Low Pressure Vacuum Furnace VFL Series
The VFL Series Low-Pressure Vacuum Furnace is an efficient device that reduces gas usage by half with a square vacuum chamber, providing high-quality heat treatment in a space-saving design. The VFL Series Low-Pressure Vacuum Furnace is optimized for heat treatment of tool steel, alloy steel, stainless steel, and more, supporting a wide range of processes including hardening, brazing, and melting. Its square vacuum chamber design maximizes internal capacity, reducing gas usage by approximately half compared to conventional vacuum furnaces. Additionally, its compact design reduces installation area by about 50%, allowing for space-saving installation. Furthermore, the use of graphite insulation minimizes moisture absorption, reducing the risk of oxidation for materials such as SUS. ■ Features - Energy-saving design with a square vacuum chamber: Reduces gas usage by about half, achieving efficient gas consumption - Compact design: Reduces installation area by approximately 50% compared to conventional vacuum furnaces - Graphite insulation: Prevents moisture absorption, reducing oxidation risk - RC fan for improved heat distribution: Supports stable heating in low to medium temperature ranges - Inverter-controlled cooling fan: Adjusts fan speed for optimal cooling according to the workpiece ■ Specifications - Vacuum chamber shape: Square - Insulation material: Graphite - Heating method: Improved heat distribution with RC fan - Cooling method: Inverter-controlled cooling fan ■ Applications The VFL Series Low-Pressure Vacuum Furnace is well-suited for various high-precision heat treatment processes, excelling in the following applications: - Hardening and tempering of tool steel: Enhances durability of tool steel components - Brazing and melting of alloy and stainless steel: Achieves high-quality, uniform finishing - Oxidation risk reduction for precision parts: Graphite insulation helps prevent oxidation The VFL Series Low-Pressure Vacuum Furnace supports efficient production processes by balancing quality improvement and energy savings. CHUGAI RO (THAILAND) CO., LTD. is based in Bangkok, Thailand, and provides services throughout the country. ■ For more details, please download the PDF or feel free to contact us.
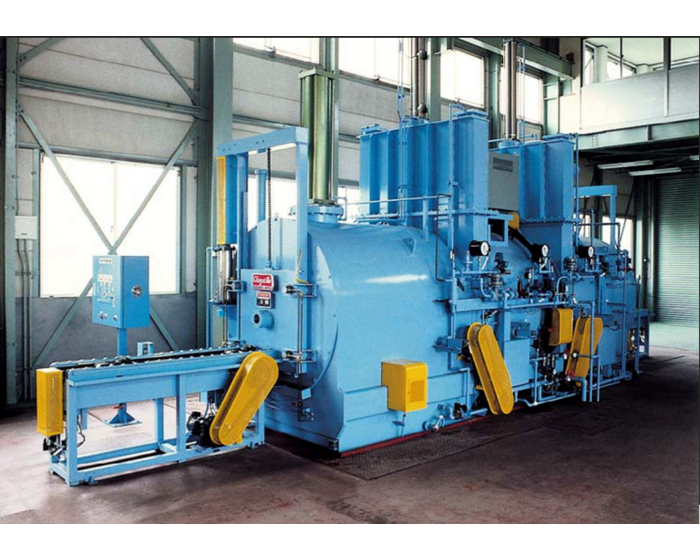
Vacuum Heat Treating Furnaces CF/QF Series for Tool Steel, Alloy Steel, and Stainless Steel
The CF/QF Series Vacuum Heat Treatment Furnace enables precision heat treatment of tool steel, alloy steel, and stainless steel, delivering high-quality finishes with flexible cooling options. The CF/QF Series Vacuum Heat Treatment Furnace is a high-performance heat treatment device specialized for the firing, brazing, and melting of tool steel, alloy steel, and stainless steel. It comes with a standard pre-chamber (gas-cooled), heating chamber, and oil cooling chamber, allowing the selection of an optimal model according to heat treatment needs. The CF model employs gas cooling, while the QF model offers both gas and oil cooling options. Additionally, the CF-Q model separates gas and oil cooling into different chambers, the CF-C model provides direct gas cooling, and the QF-C model supports direct gas and oil cooling. With various cooling options, it enables precise heat treatment tailored to different materials and processing requirements. ■ Features - Suitable for tool steel, alloy steel, and stainless steel, with applications in firing, brazing, and melting processes - Combination of gas and oil cooling offers flexible cooling options - CF, QF, CF-Q, CF-C, and QF-C models allow optimal selection based on heat treatment needs - High-precision temperature control ensures stable heat treatment quality and enhances processing accuracy ■ Specifications - Applicable materials: Tool steel, alloy steel, stainless steel - Supported heat treatment processes: Firing, brazing, melting - Model configurations: CF (gas cooling), QF (gas and oil cooling), CF-Q (gas and oil cooling in separate chambers), CF-C (direct gas cooling), QF-C (direct gas and oil cooling) ■ Applications The CF/QF Series Vacuum Heat Treatment Furnace achieves high-precision and stable heat treatment in the following applications: - Automotive parts manufacturing: Precision hardening and firing treatment for gears and shafts - Processing of tool steel and alloy steel: Suitable for tool manufacturing where high durability and accuracy are required - Brazing and melting of stainless steel parts: Ensures uniform, high-quality finishes while maintaining corrosion resistance The CF/QF Series Vacuum Heat Treatment Furnace is an ideal solution for manufacturing industries requiring precision heat treatment, offering flexible cooling options and high-quality control features. CHUGAI RO (THAILAND) CO., LTD. is based in Bangkok, Thailand, and provides services throughout the country. ■ For more details, please download the PDF or feel free to contact us.
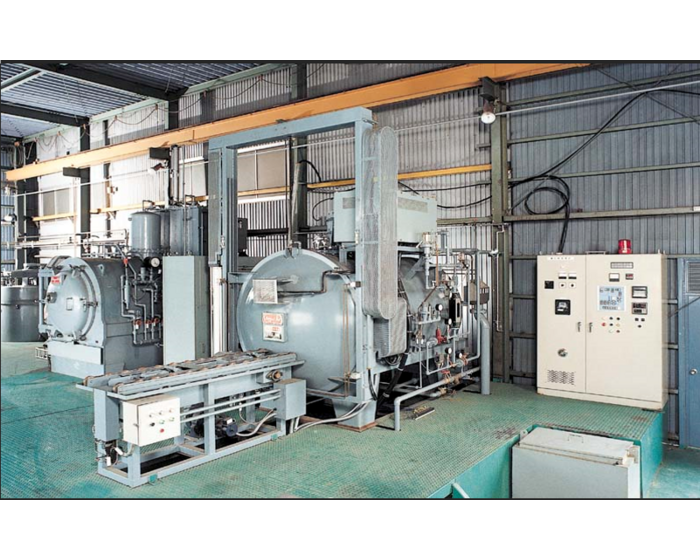
Low-Temperature Vacuum Furnaces T.VT Series
The T.VT Series Low-Temperature Vacuum Furnace shortens cooling time with its built-in inter-cooler, enabling efficient processing of cold-formed components and high-quality steel wires. The T.VT Series Low-Temperature Vacuum Furnace is designed for quality improvement and softening treatment of cold-formed components and high-quality steel wires. Optimized for use at working temperatures of up to 750°C, some models can handle temperatures as high as 950°C. Equipped with a built-in inter-cooler, this series significantly reduces cooling time, contributing to more efficient material processing and improved product quality. Additionally, its energy-efficient design reduces operational costs while maintaining high performance. ■ Features - Low-temperature operation design: Supports temperatures up to 750°C, with specific models capable of up to 950°C - Quality improvement for cold-formed components and high-quality steel wires: Suitable for low-temperature processes such as softening treatment - Built-in inter-cooler for reduced cooling time: Enhances cooling performance and supports efficient processing - High cooling performance: Optimizes material properties for superior quality - Energy-efficient design: Achieves high energy efficiency and reduces operational costs ■ Specifications - Operating temperature range: Room temperature to a maximum of 950°C (depending on the model) - Cooling method: Direct cooling with built-in inter-cooler - Target materials: Cold-formed components, high-quality steel wires, etc. - Applications: Quality improvement, softening treatment, and more ■ Applications The T.VT Series Low-Temperature Vacuum Furnace is ideal for rapid cooling and quality enhancement of cold-formed components and high-quality steel wires, excelling in the following applications: - Processing of cold-formed components: Supports efficient production by reducing cooling time - Quality improvement and softening of steel wires: Maximizes material properties and enhances quality - High-precision heat treatment: Ensures stable low-temperature heat treatment for processing accuracy and uniformity of products The T.VT Series Low-Temperature Vacuum Furnace contributes to the production of high-quality products in various industries by balancing cooling efficiency and quality control. CHUGAI RO (THAILAND) CO., LTD. is based in Bangkok, Thailand, and provides services throughout the country. ■ For more details, please download the PDF or feel free to contact us.
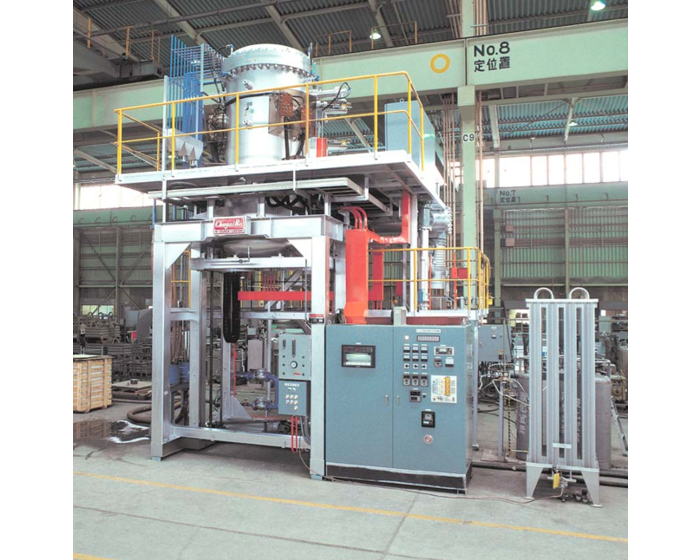
Multi-Function Pressurized Gas High-Temperature Furnaces Capable of Reaching up to 2800°C
The high-pressure gas high-temperature furnace, capable of reaching up to 2800°C and 0.99 MPa, is a reliable device ideal for the sintering and refining of ceramics and graphite. The high-pressure gas high-temperature furnace operates under a wide range of conditions, from high temperatures of up to 2800°C to pressures spanning from vacuum (0.01 Pa) to 0.99 MPa. It is especially suitable for the sintering and refining of ceramics and graphite, including materials with complex shapes created through injection molding. This furnace uses inert gases such as nitrogen, argon, and helium, providing an optimal processing environment tailored to the material. ■ Features - Supports high temperatures up to 2800°C - Operates under a wide range of conditions, from vacuum (0.01 Pa) to high pressure (0.99 MPa) - Ideal for sintering and refining ceramics and graphite - Uses inert gases such as nitrogen, argon, and helium - Simplifies processes such as wax removal and sintering - Optional support for halogen gases and low-pressure hot isostatic pressing (HIP) ■ Specifications - Temperature range: Room temperature to 2800°C - Pressure range: Vacuum (0.01 Pa) to 0.99 MPa - Usable gases: Nitrogen, argon, helium, air, oxygen - Applications: - Sintering and refining of ceramics and graphite - Wax removal - Process optimization for sintering ■ Applications This high-pressure gas high-temperature furnace is particularly suitable for the following applications in ceramics and graphite processing: - Manufacturing of industrial components - Sintering of electronic materials - Refining of materials for specialized applications Additionally, it is widely used in research and development, where high-quality material processing is required. Combining high performance and reliability, this device enables the high-quality processing of ceramics and graphite, contributing to improved manufacturing efficiency. CHUGAI RO (THAILAND) CO., LTD. is based in Bangkok, Thailand, and provides services throughout the country. ■ For more details, please download the PDF or feel free to contact us.
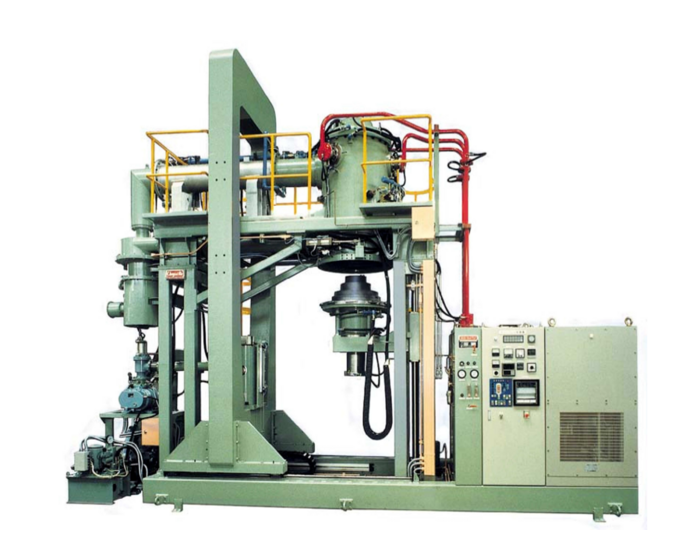
High-Pressure Hot Presses
The multifunctional high-pressure hot press, capable of continuous operation at high temperatures up to 2800°C and high pressure up to 0.99 MPa, is ideal for research, development, and material processing. The high-pressure hot press is a high-performance device supporting research, development, and specialized material processing. It operates continuously under conditions of up to 2800°C and 0.99 MPa, delivering stable performance over extended periods thanks to its precisely machined thick plates and proprietary press frame manufacturing technology. The well-designed assembly chamber enhances operability and safety. This device plays a vital role in material property evaluation and the development of new materials. ■ Features - Supports high temperatures up to 2800°C and high pressure up to 0.99 MPa, enabling a wide range of operations - Individual cylinder structure ensures precise density control - Continuous processing allows mass production, improving productivity - Designed for processing high-alloy steels and magnetic alloys, preventing evaporation of alloy components - Roller hearth transport system minimizes required space - Durable press frame prevents deformation or warping even with prolonged use ■ Specifications - Pressure: Up to 0.99 MPa - Temperature: Up to 2800°C - Models: Twin hot press (two furnaces, one press), single hot press (one furnace, one press), box-type transformer - Operation: High operability with movable assembly chamber - Safety: Designed for safe use under high-temperature and high-pressure conditions ■ Applications This high-pressure hot press is particularly effective in the following applications: - Development of new materials - Evaluation of material properties - Research on chemical reactions under high temperatures - Processing of high-alloy steels and magnetic alloys This multifunctional high-pressure hot press enhances operational efficiency and outcomes in research, development, and specialized material processing. CHUGAI RO (THAILAND) CO., LTD. is based in Bangkok, Thailand, and provides services throughout the country. ■ For more details, please download the PDF or feel free to contact us.
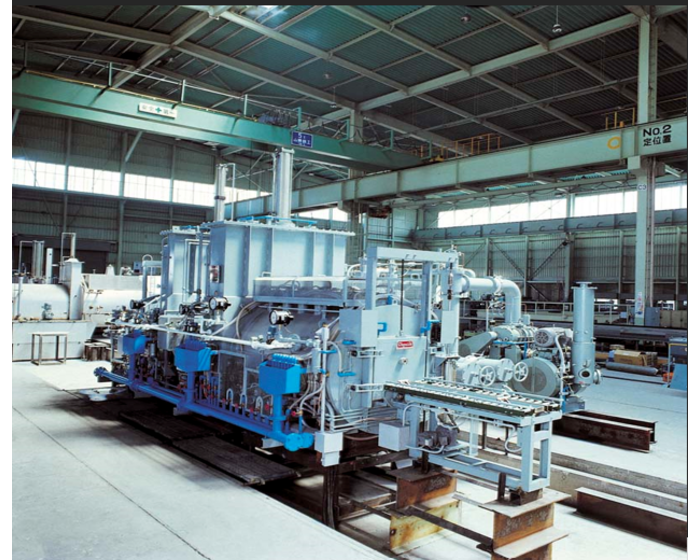
Vacuum Sintering Furnaces VS Series
The VS Series Vacuum Sintering Furnace achieves precise density control and high productivity while preventing oxidation of steel and high-alloy steel in high-temperature environments up to 2400°C. The VS Series Vacuum Sintering Furnace is designed to efficiently and reliably sinter materials such as steel, high-alloy steel, and magnetic alloys. Operating at temperatures of up to 2400°C, it minimizes oxidation and automates the entire process, from vacuum sintering to cooling. This device is also capable of processing complex-shaped materials produced through injection molding, simultaneously improving productivity and maintaining quality. ■ Features - Supports high temperatures up to 2400°C, enabling simultaneous processing of multiple tasks - Independent cylinder structure allows precise density control - Vacuum environment prevents oxidation during the sintering process - Special design prevents the volatilization of alloy components - Space-saving compact roller hearth transport system ■ Specifications - Processing temperature: Up to 2400°C - Target materials: Steel, high-alloy steel, magnetic alloys - Key functions: Oxidation prevention, vacuum sintering, continuous cooling - Characteristics: Precise density control, special design, compact design ■ Applications The VS Series Vacuum Sintering Furnace is suitable for manufacturing high-precision components used in the automotive and aerospace industries. It is also effective for processing products requiring high material properties, such as electronic devices and medical equipment. This furnace enables both improved product quality and efficient mass production. By utilizing the sintering technology of this device, new value can be provided to the manufacturing industry. CHUGAI RO (THAILAND) CO., LTD. is based in Bangkok, Thailand, and provides services throughout the country. ■ For more details, please download the PDF or feel free to contact us.
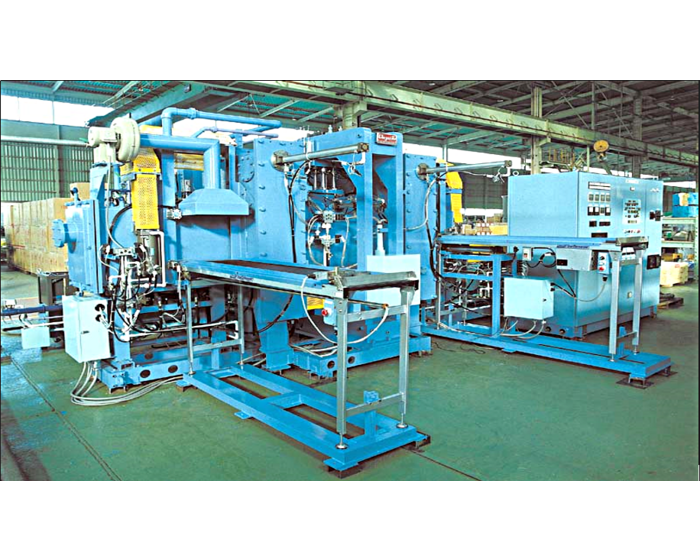
Continuous Hot Presses
The continuous hot press device, capable of processing at up to 2400°C, enables precise control of product density and contributes to improved quality and productivity. The continuous hot press is an advanced device capable of processing complex-shaped materials with high precision in high-temperature environments up to 2400°C. It is particularly suited for mass production of high-quality components required in industries such as automotive, electronics, and aerospace. This hot press technology employs individual cylinders for each task to precisely control product density, significantly enhancing production efficiency while consistently maintaining post-sintering quality. ■ Features - Enables continuous processing at high temperatures (up to 2400°C) - Uses individual cylinders for each task to achieve precise control of product density - Supports mass production through continuous processing, delivering excellent productivity - Stable operability under high-temperature and high-pressure conditions - High-precision component processing meeting the demands of automotive, electronics, and aerospace industries ■ Specifications - Maximum temperature: 2400°C - Processing method: Continuous hot press - Key functions: Precise pressing control using independent cylinders, consistent product density maintenance - Application fields: Component manufacturing for automotive, electronics, and aerospace industries ■ Applications This continuous hot press is ideal for manufacturing engine components and electronic parts in the automotive industry, as well as parts resistant to high-temperature environments in the aerospace sector. Additionally, it performs effectively in the electronics industry, where product stability and consistent quality are critical. The continuous hot press technology supports high-quality component manufacturing by balancing production efficiency and quality control. CHUGAI RO (THAILAND) CO., LTD. is based in Bangkok, Thailand, and provides services throughout the country. ■ For more details, please download the PDF or feel free to contact us.
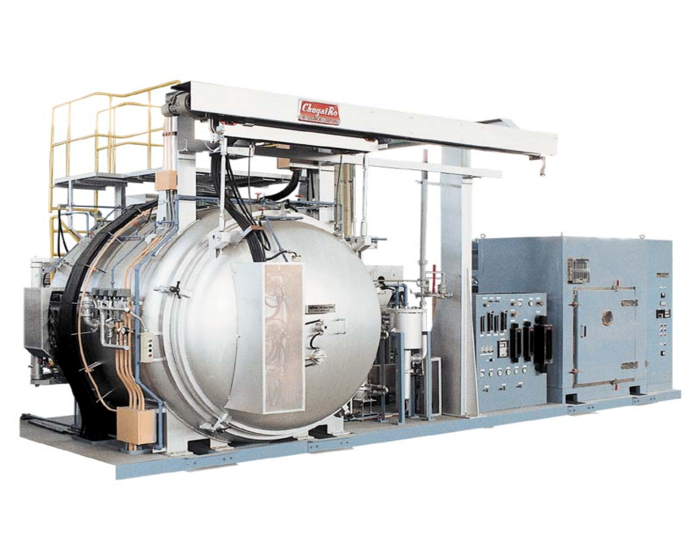
Atmosphere Sintering Furnaces
Our atmosphere sintering furnace sinters materials with complex shapes to a high density of over 95%, offering consistent quality through fully automated, precise temperature and pressure control. The atmosphere sintering furnace is designed for high-density sintering of materials with complex shapes, making it suitable for applications in the automotive, aerospace, and medical device industries. Materials manufactured through injection molding with intricate geometries can be sintered to over 95% density under standard atmospheric conditions. Computer-controlled precision management of temperature and pressure ensures a stable, high-quality sintering process. Additionally, it supports various finishing processes such as surface improvement, finishing treatment, HIP (hot isostatic pressing), and sizing. ■ Features - Enables sintering to a high density of over 95% - Computer-controlled precision management of temperature and pressure ensures stable quality - Fully automated operation provides an efficient sintering process - Supports surface improvement, finishing treatment, HIP processing, and sizing ■ Specifications - Sintering density: Over 95% - Control: Precision management of temperature and pressure via computer - Operation: Fully automated - Supported processes: Sintering, HIP, sizing, and other finishing processes ■ Applications This atmosphere sintering furnace is ideal for products requiring complex shapes and high density, widely used in the automotive, aerospace, and medical device industries. It is especially suited for products demanding surface improvement and precise finishing treatments. Our atmosphere sintering furnace improves both the quality and production efficiency of sintered products, delivering new value to the industrial sector. CHUGAI RO (THAILAND) CO., LTD. is based in Bangkok, Thailand, and provides services throughout the country. ■ For more details, please download the PDF or feel free to contact us.
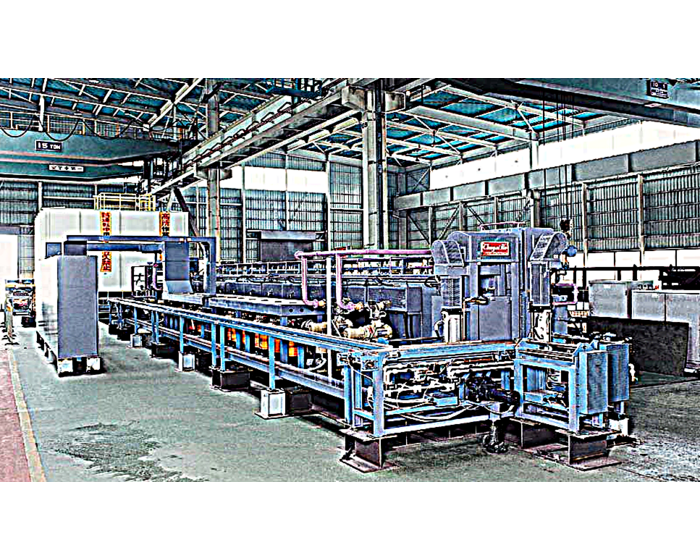
Continuous baking furnaces that meet diverse processing needs
The high-temperature continuous firing furnace, capable of handling diverse processes continuously at temperatures up to 2800°C, contributes to energy efficiency and rapid product delivery. The high-temperature continuous firing furnace is designed to handle various processes from degreasing to graphitization in a seamless manner. It supports multiple gas environments such as nitrogen, argon, air, and vacuum, enabling complex processing at temperatures up to 2800°C. By continuously managing processes like degreasing, de-rubberization, carbonization, and graphitization, it reduces lead times and energy consumption, thereby enhancing productivity and reducing costs in the manufacturing sector. ■ Features - Supports diverse gas environments (nitrogen, argon, air, vacuum) - High-temperature processing up to 2800°C - Improved energy efficiency through continuous processing - Enables rapid product delivery - Handles a wide range of processes from degreasing and firing to graphitization ■ Specifications - Temperature range: Room temperature to 2800°C - Supported gas environments: Nitrogen, argon, air, vacuum - Supported processes: Degreasing and firing, de-rubberization and firing, carbonization, graphitization ■ Applications This high-temperature continuous firing furnace is particularly suited for industries where reducing lead times and energy costs is critical, including: - Automotive industry - Aerospace industry - Electronics industry It enables the efficient production of complex, high-quality products. By implementing the high-temperature continuous firing furnace, manufacturing productivity and cost efficiency can be significantly enhanced. CHUGAI RO (THAILAND) CO., LTD. is based in Bangkok, Thailand, and provides services throughout the country. ■ For more details, please download the PDF or feel free to contact us.
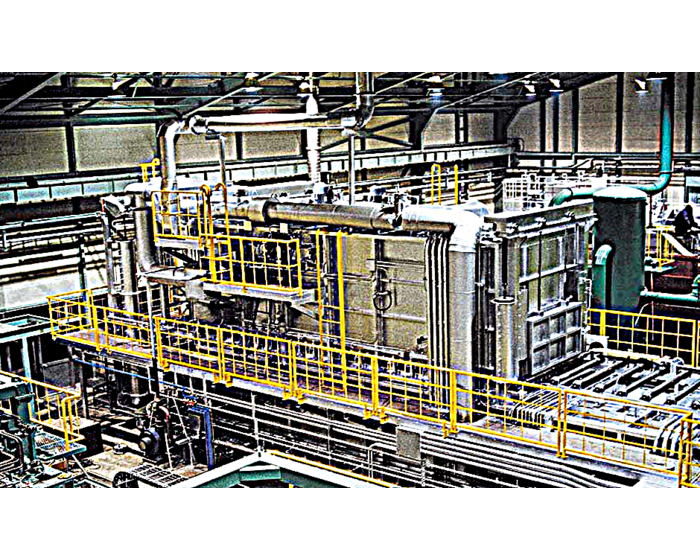
Aluminum Solution Heat Treating Furnaces
The heating furnace for aluminum, designed to enhance the performance of engine cylinder heads and automotive wheels, improves strength and durability while supporting mass production. The aluminum heating furnace for mass production is specifically designed to improve the performance of aluminum products such as engine cylinder heads and automotive wheels. It performs solution heat treatment to increase the strength and durability of these products. The roller hearth furnace is ideal for mass production and can handle long or thick products. Additionally, tray pusher furnaces and batch furnaces are available to accommodate special shapes and materials, offering flexibility to meet diverse product needs. ■ Features - Strength and durability improvement: Solution heat treatment enhances the strength and durability of aluminum products - Mass production capability: The roller hearth furnace meets the demands of mass production with an efficient heating process - Supports long and thick products: Flexible handling of various product shapes - Multiple furnace types: Tray pusher furnaces and batch furnaces are also available to meet special shape and material requirements ■ Specifications - Target products: Engine cylinder heads, automotive wheels, and other aluminum products - Heating method: Solution heat treatment - Main types: Roller hearth, tray pusher, batch furnaces - Application range: From mass production to special-shaped products ■ Applications This heating furnace is widely used in the automotive and aerospace industries, particularly for engine components, vehicle structural parts, and other products requiring high strength and durability. By stabilizing quality through solution heat treatment, it enhances the competitiveness of aluminum products and supports efficient manufacturing processes. Combining mass production capabilities with high quality, this heating furnace is an ideal choice for improving the performance and productivity of aluminum products. CHUGAI RO (THAILAND) CO., LTD. is based in Bangkok, Thailand, and provides services throughout the country. ■ For more details, please download the PDF or feel free to contact us.
CONTACT