SERVICE
Production Goods & Services
33hits
Narrow by category
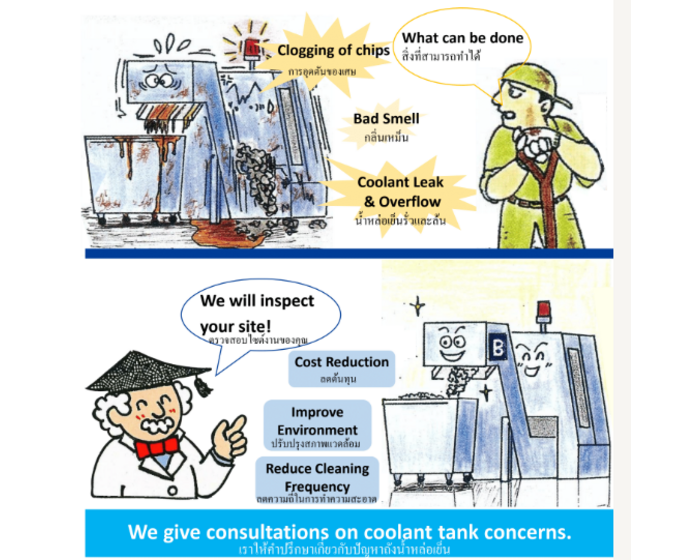
The Best Coolant Management Solution! Coolant Filtration System from BUNRI
Coolant management in production lines is a key factor influencing production efficiency. However, the accumulation of debris and impurities in coolant can lead to various issues, such as unpleasant odors, reduced operational efficiency, and increased operational costs. BUNRI's coolant filtration system effectively addresses these problems, enhancing productivity and improving the work environment while supporting cost reduction and environmental conservation through efficient cleaning and reuse of coolant. ■ Key Features BUNRI's coolant filtration system offers the following features: ・Cost Efficiency Equipped with high-performance filters, it increases the reuse rate of used coolant, reducing the expense of purchasing new coolant. ・Environmental Improvement Minimizes unpleasant odors from coolant, creating a more pleasant and safer work environment. ・Easy Maintenance Its simple structure reduces the complexity of cleaning and allows for easy daily maintenance. ・Compatibility with Various Machinery Compatible with a wide range of machinery, including grinders, machining centers, and lathes. ■ System Specifications ・Supported Coolants: Water-soluble and oil-based coolants ・Filter Types: Magnetic separator, conveyor type, cyclone ・Supported Materials: Steel, cast iron, aluminum, copper, stainless steel BUNRI's coolant filtration system not only boosts productivity but is also environmentally friendly, making it the ideal choice for production lines aiming for efficient coolant management. For more details, please download the PDF or contact us for further consultation!
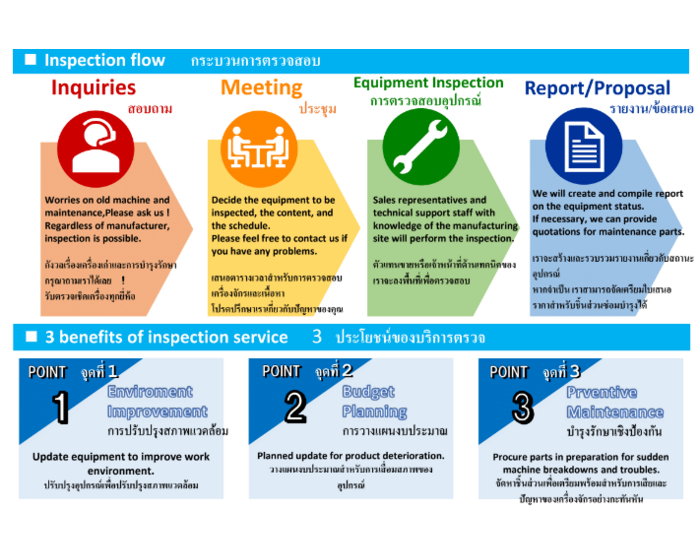
Protect Your Production Line! Coolant System Inspection Services from BUNRI
Coolant systems play a crucial role in production lines, but prolonged use can lead to deterioration and reduced performance. This may result in unexpected issues that could affect the entire production process. BUNRI's coolant system inspection services are designed to address these challenges. Regular inspections by our team of experts help maintain optimal equipment performance and prevent potential problems in advance. ■ Key Features BUNRI's coolant system inspection services offer the following benefits: ・Preventive Maintenance Regular inspections allow for early detection of minor issues, preventing major breakdowns. ・Cost Reduction Minimizes the need for emergency part replacements or large-scale repairs, reducing operational expenses. ・Performance Preservation Maintains equipment in optimal condition, maximizing production efficiency. ・Expert Support BUNRI's technical team utilizes the latest technology and expertise to deliver precise and reliable inspections. ■ Service Details ・Inspection Items Condition of press rollers Accumulation of floating oil Wear and tear of belts and chains ・Supported Equipment Magnetic separators Oil skimmers Coolant filtration systems from other manufacturers ・Service Scope Preparation of status inspection reports Recommendations for necessary spare parts as needed BUNRI's inspection services ensure equipment performance and improve the production environment, making it the ideal solution for manufacturing facilities seeking safe and efficient operations. For more information, please download the PDF or contact us for further consultation!
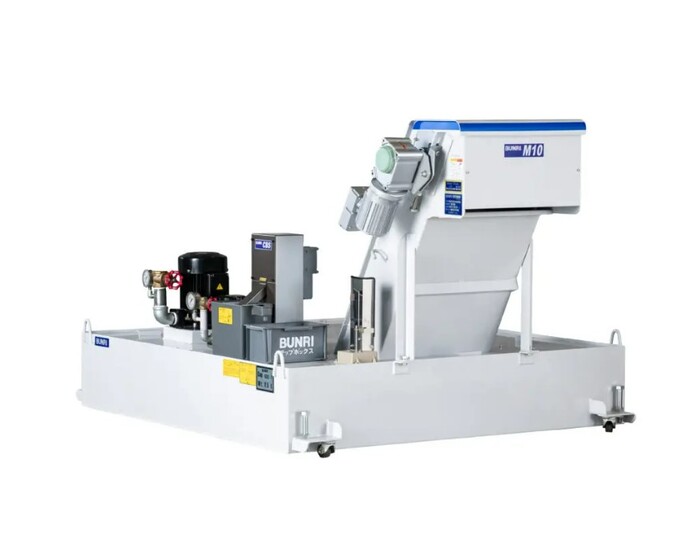
Powerful Magnetic Conveyor | Optimal Transportation System with High-Performance Magnets "MMS"
The "MMS" powerful magnetic drum conveyor is designed to enhance the efficiency of separating and transporting metal fragments generated in manufacturing and recycling operations. Equipped with high-performance magnets integrated into the conveyor belt, it captures metal fragments precisely and swiftly transports them to designated pathways. This system is especially suitable for use in metal processing and recycling industries, enabling streamlined processes and improved work efficiency. ■ Key Features ・High Separation Capability The powerful magnetic force reliably captures metal fragments ranging from small particles to large pieces. ・Efficient Transport System Separated metal fragments are immediately moved to the next stage, reducing process time. ・Space-Saving Design Compact construction allows installation even in limited spaces. ・Durability and Safety Built with high-quality materials, ensuring long-lasting and stable performance. ・Environmental Consideration Improves metal recycling efficiency, reduces waste, and maximizes resource utilization. ■ Technical Specifications ・Magnetic Force: Customizable ・Supported Metal Fragment Sizes: From small particles to large pieces ・Sizes Available: Multiple variations to choose from ・Materials: High-quality, corrosion-resistant, and durable materials ・Power Requirements: Suitable for typical factory environments ■ Applications ・Metal Processing Industry: Separating and transporting metal fragments from cutting or grinding processes ・Recycling Industry: Efficiently collecting and sorting scrap metal ・Other Manufacturing Industries: Handling metal materials in powder or granule form "MMS" is designed to enhance the efficiency of metal separation and transportation, supporting productivity improvements in your operations. Experience the benefits of this system in your production processes. For more information, please download the PDF or contact us for consultation!
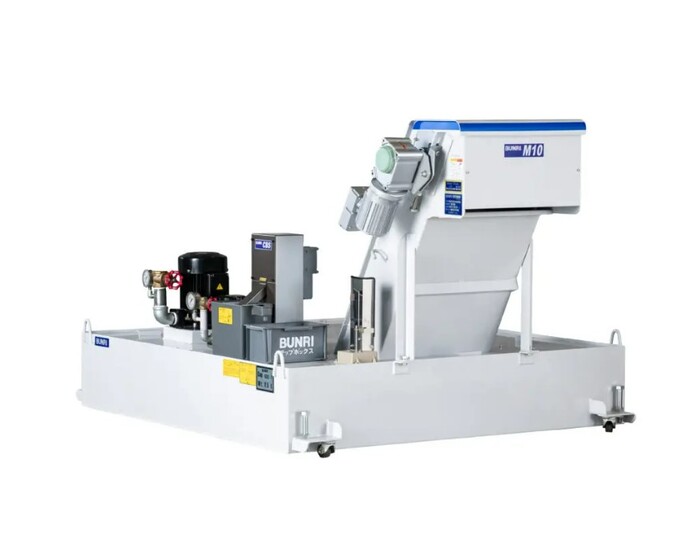
Powerful Magnetic Conveyor | Highly Efficient Conveyor System with Advanced Magnet Technology "M10"
The "M10" powerful magnetic drum conveyor is specifically designed for handling fine metal chips and coolant filtration in casting processes. Equipped with stronger magnetic force than previous models, the M10 achieves a filtration accuracy of 10 microns with over 90% efficiency. This helps simplify processes and reduce costs. Additionally, its compatibility with high-pressure pumps and compact design makes it ideal for factories with space limitations. ■ Key Features ・High-Power Magnetic Drum Efficiently captures fine metal chips, enhancing the productivity of casting processes. ・High-Precision Filtration Achieves a filtration accuracy of 10 microns with over 90% efficiency, eliminating the need for secondary processing. ・High-Pressure Pump Compatibility Supports high-pressure pumps up to 3 MPa, making it suitable for a wide range of applications. ・Space-Saving Design Compact yet highly efficient, suitable for facilities with limited space. ・Durability and Environmental Friendliness Its robust structure ensures long-lasting performance while improving metal recycling efficiency and reducing waste. ■ System Mechanism 1.Dirty Liquid Processing Dirty liquid flows into the system, with 80–90% of metal chips settling at the bottom. 2.Magnetic Capture Non-settling metal chips are captured by the magnetic drum and settle after demagnetization. 3.Clean Liquid Generation Liquid passing through the drum becomes clean and is supplied to the clean tank. 4.Metal Chip Removal Settled metal chips are transported out by a scraper, with liquid being filtered before discharge. ■ Specifications ・Filtration Accuracy: 10 microns with over 90% efficiency ・Supported Pump Pressure: Up to 3 MPa ・Supported Metal Chips: Fine metal chips (for casting processes) ・Size: Multiple variations available, customizable to fit space requirements ・Material: High-durability materials used "M10" is a high-performance system designed to enhance production efficiency and reduce environmental impact. Experience its superior performance in your manufacturing operations today. For more information, please download the PDF or contact us for consultation!
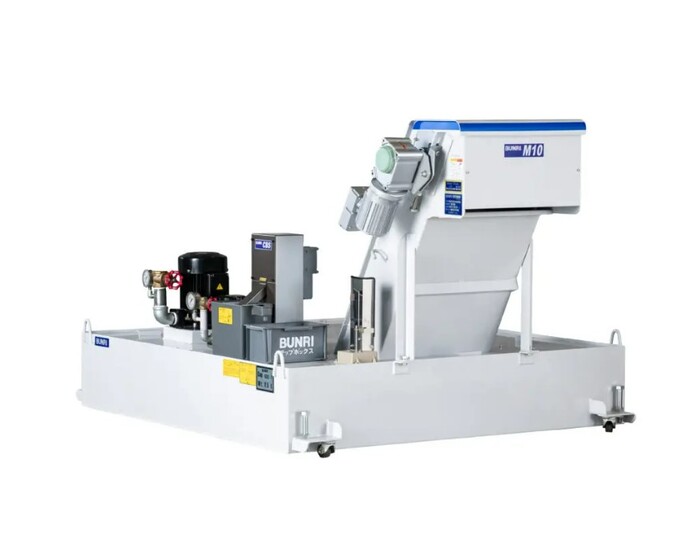
Powerful Magnetic Conveyor | High-Performance Metal Fragment Separation and Transport System "HMS"
The "HMS" powerful magnetic conveyor is designed for metal chip management in a low-profile and compact system. Magnets installed at the bottom of the conveyor capture metal chips with high filtration accuracy. This design is ideal for manufacturing lines with limited space and low-profile machinery. It efficiently transports and discharges metal chips, streamlining production processes and improving operational efficiency. ■ Key Features ・Low-Profile and Compact Design The compact structure allows for easy installation in confined spaces and low-profile machinery. ・High-Precision Filtration Offers filtration accuracy of 30 microns with over 90% capture efficiency, effectively removing fine metal chips. ・Easy Maintenance Equipped with a scraper mechanism to efficiently transport metal chips, reducing maintenance effort. ・Efficient Liquid Filtration Function Captured metal chips are filtered for liquid before discharge, allowing collection in a dry state. ・Environmentally Friendly Enhances metal recycling efficiency and contributes to waste reduction. ■ System Mechanism 1.Dirty Liquid Processing Dirty liquid flows into the conveyor, and the liquid containing metal chips is processed. 2.Magnetic Capture Magnets at the bottom of the conveyor capture metal chips. 3.Metal Chip Transport Captured metal chips are transported using a scraper. 4.Metal Chip Discharge At the conveyor's discharge point, metal chips are filtered for liquid before discharge and can be collected in a dry state. ■ Specifications ・Filtration Accuracy: 30 microns with over 90% efficiency ・Supported Liquids: Water-soluble and oil-based coolants ・Installation Environment: Suitable for confined spaces and low-profile setups ・Material: High-durability materials ・Power Supply: Compatible with general factory standards ■ Applications ・Metal Processing Industry: Managing metal chips generated from casting, precision cutting, and grinding processes ・Recycling Industry: Separation and transportation of metal materials The "HMS" is an optimal solution for manufacturing sites that demand efficient and cost-effective metal chip management. Experience its superior performance in your production facility. For more information, please download the PDF or contact us for further consultation!
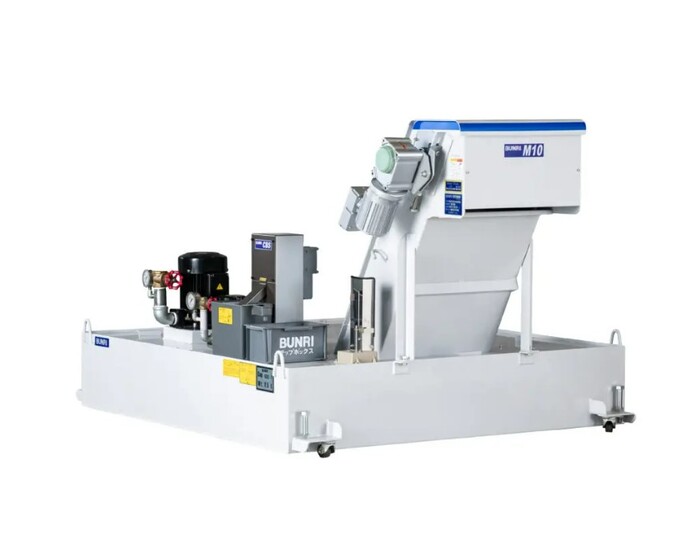
Powerful Magnetic Conveyor | High-Efficiency Metal Chip Separation and Transport System "#30 M10"
The "#30 M10" powerful magnetic drum conveyor is specifically designed for use with Machining Centers #30. It is a metal chip management system capable of filtering particles as small as 10 microns with an accuracy of over 90%, ensuring high-quality product output. Additionally, it supports high-pressure pumps up to 3 MPa, making it suitable for a wide range of production processes. Its compact design makes it ideal for limited spaces, helping to streamline production processes and improve efficiency. ■ Key Features ・Specialized Design Specifically designed for use with Machining Centers #30, delivering exceptional filtration performance. ・High-Precision Filtration Removes particles as small as 10 microns with an efficiency of over 90%, contributing to higher product quality. ・Streamlined Processes High-precision filtration eliminates the need for additional processing, improving operational efficiency. ・High-Pressure Pump Compatibility Supports high-pressure pumps up to 3 MPa, suitable for various production environments. ・Compact Design Flexible and easy to integrate into production facilities with limited space. ■ System Mechanism 1.Dirty Liquid Processing Dirty liquid flows into the system, with 80–90% of metal chips settling at the bottom. 2.Magnetic Capture Metal chips that do not settle are captured by the magnetic drum and settle again after demagnetization. 3.Clean Liquid Production Liquid passing through the magnetic drum is purified and supplied to the clean tank. 4.Metal Chip Discharge Settled metal chips are transported out by a scraper, with liquid filtered before discharge. ■ Specifications ・Filtration Accuracy: 10 microns (90% or more) ・Supported Pump Pressure: Up to 3 MPa ・Supported Metal Chips: Fine metal chips ・Installation Environment: Optimized for Machining Centers #30 ■ Applications ・Machining Centers: Managing metal chips generated from cutting processes. ・Precision Manufacturing: Enhancing the efficiency of coolant purification. The "#30 M10" is a high-precision and high-efficiency metal chip separation system, significantly boosting productivity in Machining Centers #30. Integrate it into your production line to experience its superior performance today. For more information, please download the PDF or contact us for further consultation!
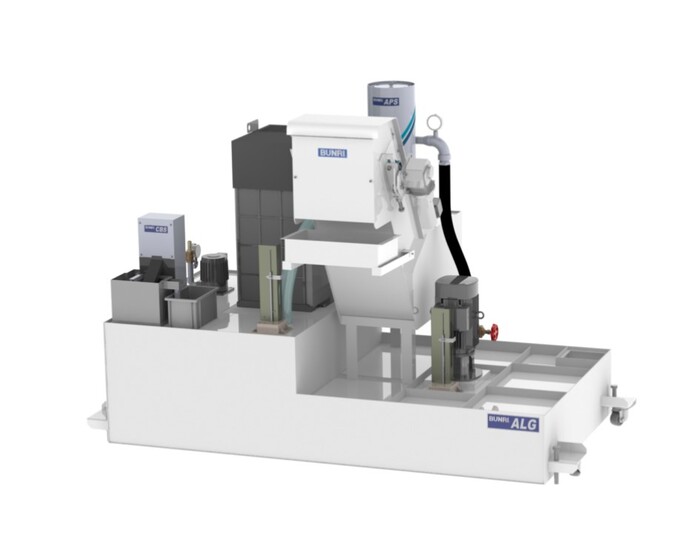
High-Performance Coolant Management System | Efficient Cooling and Management Solution "ALG"
The "ALG" coolant system is specifically designed for handling non-magnetic grinding sludge. It delivers high-precision filtration performance, capable of removing particles as small as 10 microns with over 90% efficiency, and effectively eliminates sludge. Equipped with a uniquely designed tank and a new cyclone filter, it significantly reduces cleaning workloads and maintenance costs while enhancing product quality in grinding processes. ■ Key Features ・Supports Non-Magnetic Sludge Efficiently processes sand-like non-magnetic sludge, improving production quality. ・Comprehensive Filtration Technology The cyclone filter ensures thorough filtration, delivering clean coolant and removing floating oil and scum with a chain bucket skimmer. ・Centrifugal Sludge Accumulation The vortex generated inside the tank efficiently accumulates sludge and abrasive grains at the center. ・Energy-Saving Design Eliminates the need for a shower pump, reducing power consumption while tripling the rotational flow rate compared to conventional systems. ・Environmentally Friendly Does not require consumables like cartridges or paper filters, reducing waste. ■ System Mechanism 1.Vortex Generation Contaminated liquid flows into the primary tank, creating a vortex that accumulates sludge at the center using centrifugal force. 2.Sludge Pumping Accumulated sludge is efficiently pumped out by the supply pump. 3.Cyclone Filtration The contaminated liquid passes through the cyclone filter, where it is filtered into clean coolant. 4.Clean Liquid Supply The filtered clean liquid is sent to the secondary tank for supply to the machine. 5.Sludge Discharge Filtered sludge is discharged via a scraper conveyor and can be collected in a dry state. ■ Specifications ・Filtration Accuracy: 10 microns (90% or more) ・Supported Coolants: Water-soluble ・Tank Capacity: High processing capability with a two-stage design ・Installation Environment: Grinding operations for non-magnetic materials ■ Applications ・Grinding Processes: Handling sludge from non-magnetic materials ・Precision Manufacturing: For production lines requiring high-precision finishing The "ALG" system addresses coolant management challenges in grinding operations while contributing to environmental sustainability. It is the ideal solution for companies seeking high-quality working environments. For more information, please download the PDF or contact us for further consultation!
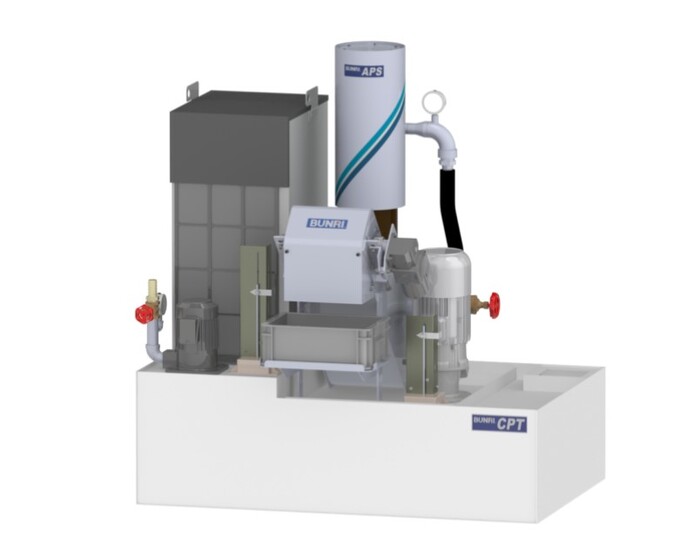
High-Performance Coolant Management System | The Optimal Cooling Solution "CPT"
The "CPT" coolant system is a compact solution designed to manage both magnetic and non-magnetic sludge. With a reduced installation footprint of 60% compared to previous models, it still delivers a high filtration precision of 10 microns with over 90% efficiency. Utilizing a new cyclone filter and an improved primary tank, it enhances sludge accumulation efficiency and reduces environmental impact. ■ Key Features ・Supports Magnetic and Non-Magnetic Sludge Compatible with a wide range of grinding materials, including sand-like sludge. ・Comprehensive Filtration The new cyclone filter provides complete filtration, supplying clean coolant suitable for various applications. ・Space-Saving Design Reduces installation space by 60%, making it ideal for production lines with limited space. ・Efficient Sludge Accumulation The tank's vortex and centrifugal force structure efficiently accumulates sludge and abrasive grains. ・Environmentally Friendly Designed without consumables, reducing industrial waste and environmental impact. ■ System Mechanism 1.Dirty Liquid Processing Contaminated liquid flows into the primary tank, generating a vortex to accumulate sludge at the center. 2.Sludge Accumulation and Pumping Sludge accumulated at the center is pumped out efficiently for further processing. 3.Cyclone Filtration The liquid is filtered through the cyclone filter, producing clean coolant. 4.Sludge Discharge Accumulated sludge is discharged via a conveyor from the sediment tank and can be collected in a dry state. 5.Clean Liquid Supply Filtered clean liquid is sent to the secondary tank for supply to the machinery. ■ System Specifications ・Filtration Precision: 10 microns (90% or more) ・Installation Space: Reduced by 60% compared to previous models ・Supported Coolant: Water-soluble ・Environmental Consideration: No consumables required ■ Applications ・Grinding Lines: Management of magnetic and non-magnetic sludge and coolant ・Precision Manufacturing Lines: For high-quality production processes "CPT" is a next-generation cooling solution that delivers high-efficiency coolant management in a compact design, making it perfect for modern factories. Experience its performance in your production facility today. For more information, please download the PDF or contact us for further consultation!
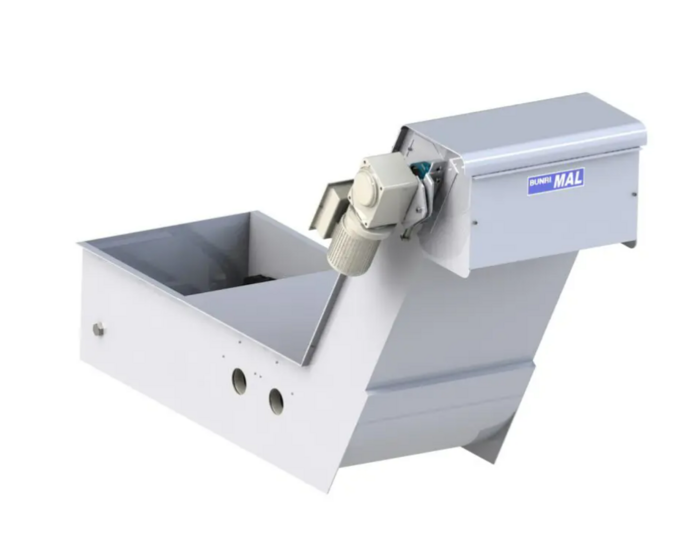
High-Performance Rolling Filter Conveyor | Efficient Filtering and Transport System "MAL"
The "MAL" rolling filter conveyor is an innovative conveyor system that combines the use of magnets and punching filters. It offers precise capture of both magnetic and non-magnetic metal chips, making it suitable for a wide range of applications with a single system. Featuring an auto-cleaning function, it minimizes maintenance requirements. The system provides clean liquids without the need for backwashing, contributing to reduced environmental impact. ■ Key Features ・Handles Magnetic and Non-Magnetic Metal Chips Captures magnetic metal chips with magnets and non-magnetic chips with a punching filter. ・Auto-Cleaning Function Maintains long-term filter performance through automatic cleaning, minimizing maintenance workload. ・Liquid Drainage Structure At the conveyor discharge point, metal chips are drained of liquid and can be collected in a dry state, reducing coolant loss. ・No Backwashing Required The efficient filtration process eliminates the need for backwashing, reducing operational costs. ・Compact Design Suitable for installation in confined spaces due to its compact structure. ・Environmentally Friendly Designed without consumables, reducing industrial waste. ■ System Mechanism 1.Dirty Liquid Processing Contaminated liquid flows into the system, where magnetic metal chips are captured by magnets at the bottom of the conveyor. 2.Punching Filter Filtration Non-magnetic metal chips are filtered through the punching filter, and clean liquid is supplied to the tank. 3.Chip Transport and Discharge Captured metal chips are transported by a scraper and discharged after liquid drainage. ■ System Specifications ・Filtration Precision: 200 microns (90% or more) ・Supported Metal Chips: Magnetic and non-magnetic ・Installation Environment: Compact design suitable for confined spaces ・Environmental Consideration: No consumables required ■ Applications ・Grinding and Cutting Operations: Simultaneous handling of magnetic and non-magnetic metal chips ・Precision Manufacturing Lines: For processes requiring high-quality coolant supply The "MAL" is a versatile conveyor system that combines efficient filtration with easy maintenance, enhancing productivity in manufacturing processes. For more information, please download the PDF or contact us for further consultation!
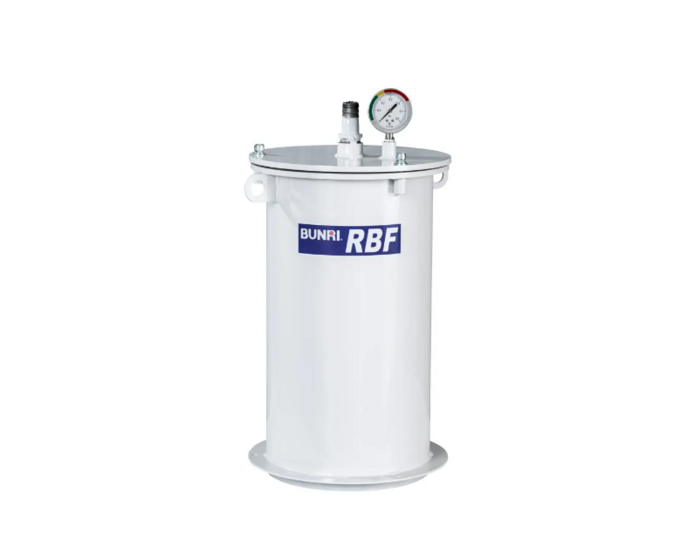
High-Performance Filter System | Efficient Filtration Solution "RBF"
The "RBF" is a bag filter system designed for the precise filtration of coolants and other industrial liquids. Despite its simple structure, it offers exceptional filtration performance, making it ideal for secondary filtration in cutting and grinding processes. Its continuous operation design minimizes production downtime and allows for efficient maintenance. ■ Key Features ・Continuous Operation Capability The dual-unit setup allows for fluid flow to be switched using a three-way valve during filter clogging, enabling maintenance without halting production. ・High-Precision Filtration Effectively removes fine metal chips and sludge, supplying clean liquid suitable for use. ・Easy Maintenance Clogging can be monitored via pressure gauges or pressure sensors, allowing for simple filter replacement or cleaning. ・Convenient Installation No need for clean liquid piping reduces installation complexity and enables quick startup. ■ System Specifications ・Weight: RBF-1: 25 kg RBF-2: 32 kg ・Filtration Mechanism:Contaminated liquid enters the top of the system, passes through the bag filter for filtration, and is discharged as clean liquid from the bottom. The "RBF" is a high-performance filtration system that supports production efficiency and enhances product quality. With its easy maintenance, convenient installation, and high-precision filtration, this system is an excellent choice for improving your manufacturing processes. For more information, please download the PDF or contact us for further consultation!
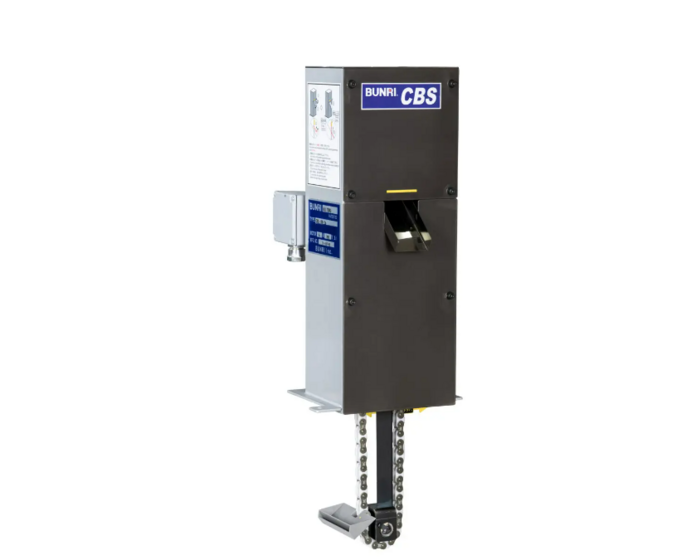
Innovative Oil Film Separator | Chain Bucket Skimmer "CBS"
The "CBS" Chain Bucket Skimmer is an advanced device designed to efficiently remove floating oil and scum from the surface of liquids. By eliminating oil and scum mixed in water-soluble coolant, it prevents liquid decay and unpleasant odors while enhancing workplace safety and cleanliness. With its superior recovery capabilities and versatility, the "CBS" has become the ideal solution for coolant management in manufacturing environments. ■ Key Features ・High Recovery Efficiency Approximately 7 times more efficient than belt skimmers in recovering floating oil and scum, significantly contributing to production efficiency and environmental improvement. ・Unique Bucket Design Specially designed buckets maximize the recovery of floating oil and scum for higher collection rates. ・Wide Applicability Supports low-viscosity floating oil and heated liquids, making it suitable for a variety of applications. ・Compact Design Simple structure ensures easy installation and seamless integration with existing equipment. ■ System Specifications ・Recovery Capacity: CBS-50: 365 cc/hour CBS-100: 730 cc/hour CBS-250: 2250 cc/hour ・Product Weight: CBS Series: 8 kg to 100 kg ・Drive Motor: CBS-50, CBS-100: 15W CBS-250: 40W ・Product Color: Body: Medium Metallic Cover: Dark Gray Metallic Customization available upon request ■ Applications ・Manufacturing Environments: Recovery of floating oil and scum mixed in water-soluble coolant. ・Precision Processing Industries: Liquid management to prevent decay and improve odor. ・Food and Chemical Industries: Processes requiring cleanliness of liquid surfaces. "CBS" is the ideal choice for improving efficiency and environmental sustainability in manufacturing environments. If you're seeking solutions for oil film removal and liquid management, consider the "CBS." For more information, please download the PDF or contact us for further consultation!
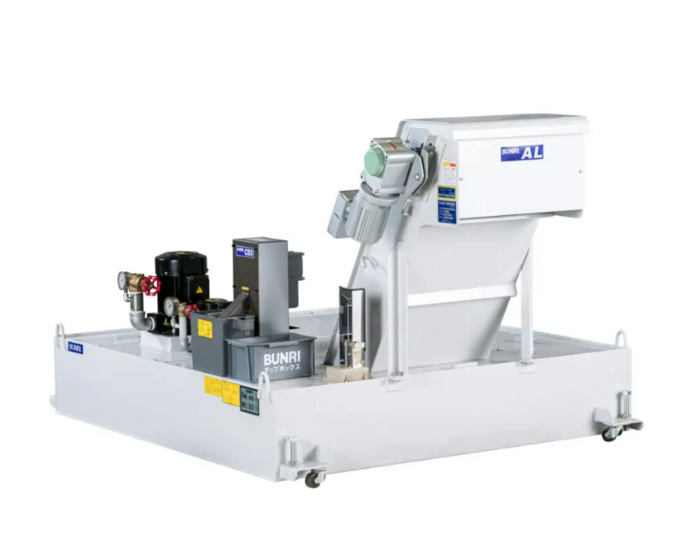
High-Performance Rolling Filter Conveyor "AL"
The "AL" Rolling Filter Conveyor is a high-performance filtration system designed to efficiently process non-magnetic metal chips. Equipped with a punching filter and an automatic cleaning function, it maintains filtration performance without requiring backwashing. Additionally, its liquid separation structure minimizes coolant loss and maintains a clean working environment. The "AL" is an ideal solution for improving manufacturing efficiency while reducing environmental impact. ■ Key Features ・Punching Filter with No Backwashing Required The automatic cleaning function prevents clogging and sustains high filtration performance. It also reduces mist generation, enhancing workplace cleanliness. ・Environmentally Friendly Design Does not require consumables, reducing industrial waste and supporting sustainable manufacturing processes. ・Liquid Separation Structure Efficiently separates chips from coolant at the outlet, discharging chips in a dry state and increasing coolant reuse rates. ・High-Precision Filtration Captures particles as small as 200 microns with over 90% efficiency, supporting the production of high-quality products. ■ System Mechanism 1.Filtration of Contaminated Liquid Contaminated liquid flows into the conveyor and is filtered through the rotating punching filter. 2.Supply of Clean Liquid The filtered liquid is discharged from inside the filter and can be reused as clean coolant. 3.Discharge of Metal Chips Metal chips are scraped off by wipers and transported by a scraper. The liquid separation structure allows chips to be discharged in a dry state. ■ System Specifications ・Filtration Accuracy: 200 microns (over 90% efficiency) ・Supported Metal Chips: Non-magnetic chips ・Installation: Compact design suitable for limited factory spaces ・Environmentally Friendly: No consumables required ■ Applications ・Precision Processing: Filtration and transportation of non-magnetic metal chips ・Coolant Management: Ideal for production lines aiming to improve coolant reuse efficiency The "AL" is a next-generation rolling filter conveyor that combines efficient chip management with reduced environmental impact. It offers an optimal solution for enhancing manufacturing environments and processes. For more information, please download the PDF or contact us for further consultation!
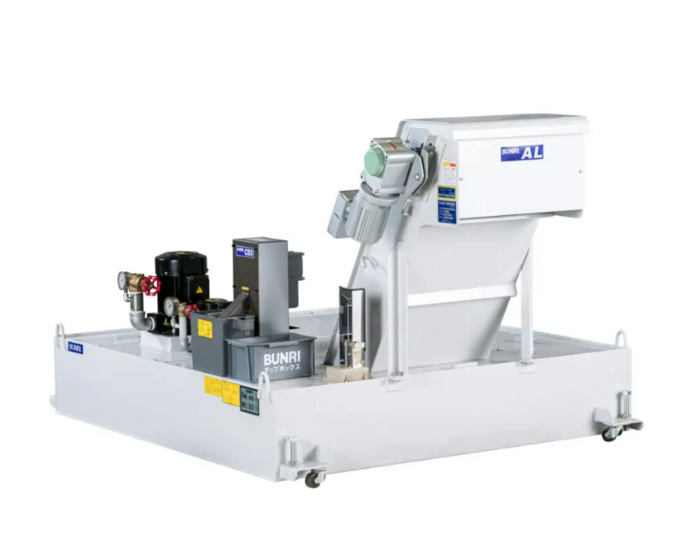
Rolling Filter Conveyor "ALL" | High-Efficiency Foreign Matter Removal System
The "ALL" Rolling Filter Conveyor is an advanced filtration system designed to efficiently remove non-magnetic metal chips. Featuring a robust punching filter that requires no backwashing, along with an automatic cleaning function, it ensures long-term filtration performance. Its liquid separation structure at the discharge point enhances coolant reuse rates while reducing environmental impact, making it an ideal solution for energy and space-saving in manufacturing facilities. ■ Key Features ・High-Durability Punching Filter Effectively processes non-magnetic metal chips while preventing clogging. ・Automatic Cleaning Function with No Backwashing Required Automatically cleans the filter, reducing mist generation and maintaining workplace cleanliness. ・Liquid Separation Structure at Discharge Discharges metal chips in a dry state, minimizing coolant waste and improving reuse rates. ・No Consumables Required Eliminates the need for cartridge or paper filters, reducing operational costs. ■ System Mechanism 1.Contaminated Liquid Processing Contaminated liquid flows into the conveyor and is filtered through the punching filter. 2.Chip Capture and Discharge Captured metal chips are scraped off and discharged in a dry state through the outlet. 3.Clean Liquid Supply Filtered liquid is supplied as clean coolant. ■ System Specifications ・Filtration Accuracy: 200 microns (over 90% efficiency) ・Supported Metal Chips: Non-magnetic chips ・Installation: Compact design suitable for limited spaces ・Environmentally Friendly: No consumables required ■ Applications ・Non-Magnetic Material Processing Sites: For chip management and coolant reuse ・Precision Manufacturing: Maintaining a clean working environment in demanding applications The "ALL" Rolling Filter Conveyor is a next-generation filtration system that combines high filtration performance with reduced environmental impact. Experience its efficiency in your manufacturing operations today. For more information, please download the PDF or contact us for further consultation!
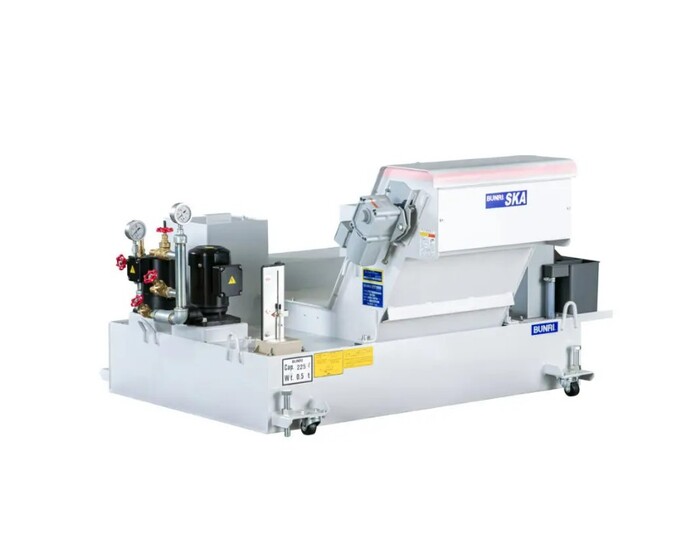
Rolling Filter Conveyor "SKA" | High-Efficiency Filtration System for Non-Magnetic Metal Chips
The "SKA" Rolling Filter Conveyor is a filtration system specifically designed to efficiently handle non-magnetic metal chips generated during cutting and grinding processes. Featuring a punching filter with an automatic cleaning function that requires no backwashing, it enhances operational efficiency while reducing environmental impact. Its space-saving design allows for installation in confined spaces, making it suitable for a wide range of manufacturing environments. ■ Key Features ・High-Precision Filtration Capability Captures particles as small as 400 microns with over 80% efficiency. ・Automatic Cleaning Function with No Backwashing Required The punching filter, continuously cleaned by a scraper, prevents clogging and maintains consistent filtration performance. ・Liquid Separation Structure at the Discharge Point Discharges metal chips in a dry state, minimizing coolant waste and maximizing reuse. ・Environmentally Friendly Design No consumables are required, reducing industrial waste and supporting sustainable operations. ■ System Specifications ・Filtration Accuracy: 400 microns (over 80% efficiency) ・Supported Metal Chips: Non-magnetic chips (sand-like and granular) ・Discharge Point: Liquid separation structure ・Maintenance: No backwashing required, with automatic cleaning function ■ Applications ・Automotive Parts Manufacturing Lines: Efficient management of non-magnetic metal chips ・Machining Facilities: Cleaning and maintenance of coolant liquids ・High-Precision Grinding Processes: For producing high-quality products requiring precision This system provides efficient handling of non-magnetic metal chips while ensuring long-term stable filtration performance. It supports productivity improvements and environmental conservation simultaneously. For more information, please download the PDF or contact us for further consultation!
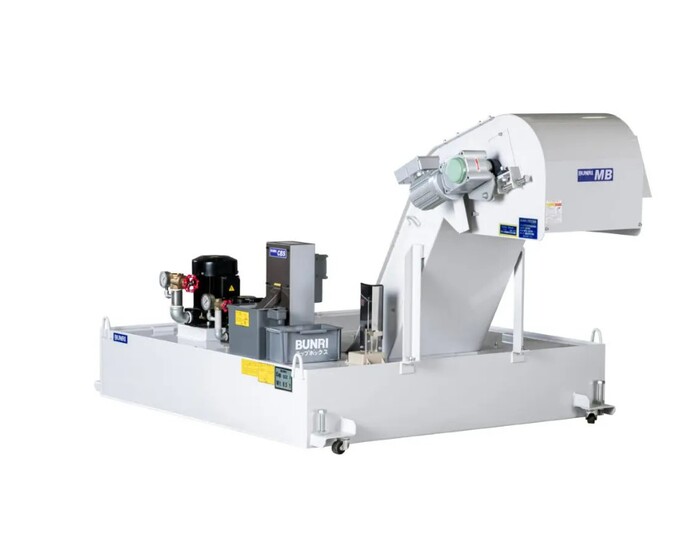
Powerful Magnetic Conveyor System "MB" | High-Efficiency Separation and Transport
The "MB" Magnetic Belt Conveyor is a high-performance system designed to efficiently separate and transport magnetic metal chips. Equipped with powerful magnets embedded within the belt, it securely captures magnetic chips, such as curled or clumped shapes. Its robust transport mechanism, featuring transfer drums and spike pins, ensures cleanliness in the working environment. This system is particularly suitable for handling fine magnetic chips generated in cutting and grinding processes, helping reduce waste and enhance productivity. ■ Key Features ・Powerful Magnetic Absorption Mechanism Internal magnets securely capture magnetic metal chips, including complex shapes like curls and clumps, ensuring smooth transport. ・Adaptability to Various Chip Shapes Spike pins effectively handle curled or clumped chips, preventing accumulation inside machinery. ・Comprehensive Chip Discharge The combination of magnetic drums and mechanical screws ensures complete removal of chips from the system. ・Environmentally Friendly Design A design free of consumables reduces industrial waste and operational costs. ■ System Mechanism 1.Chip Absorption and Transport Magnetic metal chips are absorbed by the belt's internal magnets in the contaminated liquid. 2.Use of Scrapers and Spike Pins Scrapers transport the chips while spike pins prevent tangling. 3.Chip Discharge Mechanism Internal magnets and mechanical screws discharge the chips externally, maintaining a clean conveyor. ■ System Specifications ・Filtration Precision: 100 microns (over 90% capture efficiency) ・Supported Metal Chips: Magnetic chips (clumped and curled) ・Environmentally Friendly Design: No consumables required ■ Applications ・Cutting and Grinding Sites: Efficiently manages clumped and fine magnetic chips. ・Precision Manufacturing Processes: Enhances coolant cleaning efficiency. With its powerful magnetic absorption and superior transport capabilities, the "MB" system offers the ultimate solution for handling magnetic chips. Experience improved efficiency and a cleaner working environment with this innovative system today. For more information, please download the PDF or contact us for further consultation!
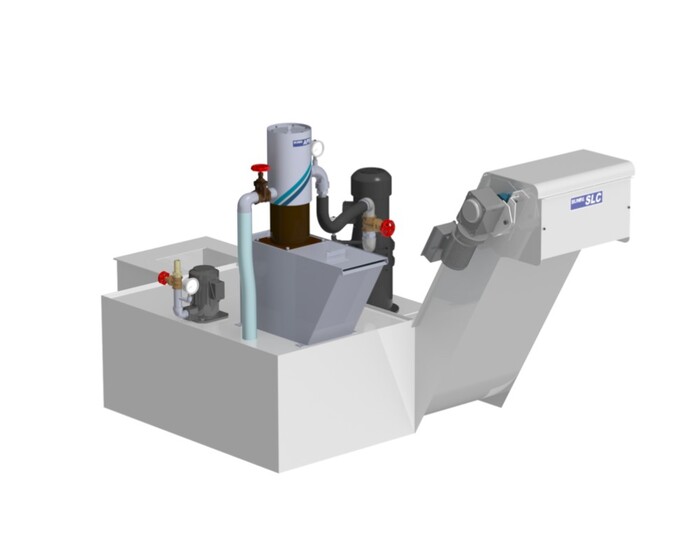
Cutting Coolant System "SLC" | High-Efficiency Cooling Solution
The "SLC" is a high-performance system designed to maintain the cleanliness of coolant in cutting operations. Combining primary filtration with a punching filter and secondary filtration with a new cyclone filter, it captures particles as small as 10 microns with over 90% efficiency. Its backwash-free design minimizes mist generation, improves the factory environment, and reduces operational costs by eliminating the need for consumables. ■ Key Features ・High-Precision Filtration The combination of punching and cyclone filters efficiently captures particles as small as 10 microns with over 90% efficiency. ・Efficient and Backwash-Free The automatic cleaning function ensures sustained filtration performance over time while maintaining a clean working environment. ・Clog-Prevention Design The rotating punching filter in constant contact with scrapers prevents clogging and efficiently captures chips. ・Environmentally Friendly No cartridge or paper filters are required, reducing industrial waste and supporting sustainable operations. ■ System Mechanism 1.Filtration of Contaminated Liquid Contaminated liquid is filtered through the punching filter, removing chips in the primary filtration stage. 2.High-Precision Secondary Filtration The liquid filtered in the first stage undergoes further filtration through the cyclone filter, supplying clean coolant. 3.Chip Removal Captured chips are transported via scrapers and discharged in a dry state. ■ System Specifications ・Filtration Accuracy: 10 microns (over 90% capture efficiency) ・Supported Chips: Non-magnetic metal chips ・Environmentally Friendly: Consumable-free design ・Applicable Processes: Suitable for cutting, grinding, and turning operations across various industries ■ Applications ・Cutting Operations: Coolant cleaning and chip removal ・Precision Manufacturing Lines: Ideal for environments requiring high-quality coolant The "SLC" is the optimal cooling solution that combines high-precision filtration with environmental improvements. Enhance your operational efficiency and reduce your environmental impact with this innovative system. For more information, please download the PDF or contact us for further consultation!
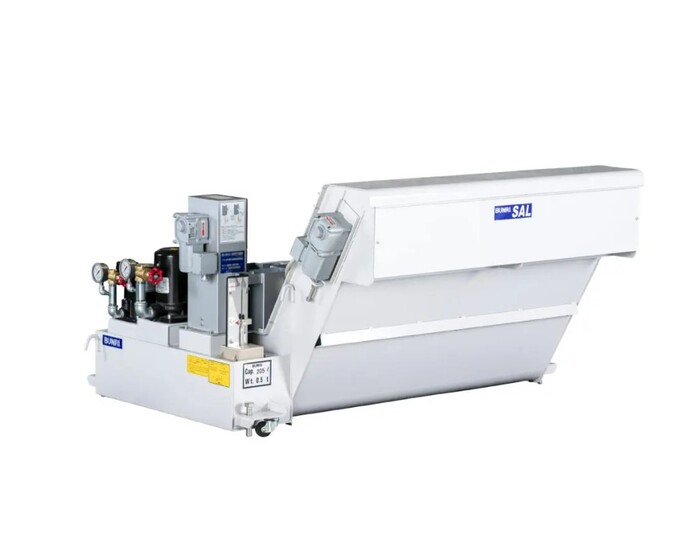
Rolling Filter Conveyor "SAL" | Efficient Foreign Matter Removal System
The "SAL Rolling Filter Conveyor" is an innovative system specifically designed for handling non-magnetic metal chips. With a unique parallel configuration combining a punching filter conveyor and a scraper conveyor, it enables efficient primary and secondary filtration, significantly reducing the frequency of tank cleaning and boosting productivity. Additionally, its backwash-free design and environmentally conscious structure help maintain air quality in the factory and support sustainable manufacturing processes. ■ Key Features ・High-Efficiency Primary and Secondary Filtration The punching filter captures large chips, while the scraper conveyor effectively handles fine chips. ・Clog-Prevention Design The rotating punching filter, in contact with a scraper, prevents clogging and ensures smooth filtration. ・Environmentally Friendly The backwash-free design reduces mist generation, and the consumable-free structure minimizes waste. ・Liquid Separation at the Outlet Efficiently separates coolant and chips, discharging chips in a dry state. ■ System Mechanism 1.Contaminated Liquid Inflow and Primary Filtration Contaminated liquid flows into the punching filter conveyor, where large chips are captured during primary filtration. 2.Secondary Filtration for Fine Chips The liquid filtered in the first stage undergoes further filtration by the scraper conveyor, where fine chips are settled and discharged. 3.Clean Liquid Supply The filtered liquid is pumped into the machine via the pump tank. ■ System Specifications ・Filtration Accuracy: 200 microns (over 90% capture efficiency) ・Supported Chips: Non-magnetic metal chips ・Structure: Parallel design of punching filter and scraper conveyor ・Environmentally Friendly: Consumable-free design ■ Applications ・Metal Cutting Processes: Efficiently handles large and fine metal chips ・Precision Manufacturing Lines: Ideal for environments requiring clean coolant The "SAL Rolling Filter Conveyor" is an innovative solution that simultaneously achieves efficient chip management and reduced environmental impact. It enhances productivity while providing a clean and sustainable manufacturing environment. For more information, please download the PDF or contact us for further consultation!
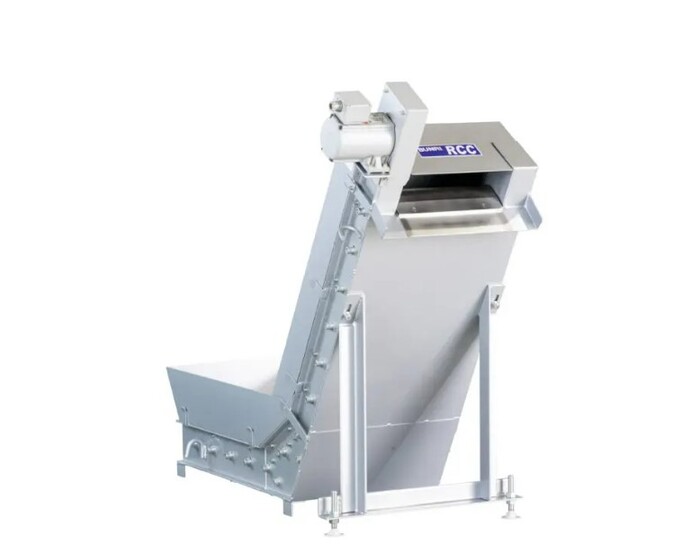
High-Performance Roller Conveyor "RCC" | Optimal Solution for Magnetic Chip Separation
The "RCC Roller Conveyor" is a high-performance system designed for the efficient separation and transport of magnetic metal chips. Equipped with a magnetic drum, it captures fine chips as small as 50 microns with over 90% efficiency. Its robust design accommodates hard and entangled chips, significantly reducing jamming issues. Additionally, the environmentally friendly design eliminates consumables, reducing industrial waste and optimizing operational costs. ■ Key Features ・Supports Various Chip Types Handles a wide range of chips, from fine particles as small as 50 microns to chips up to 100 mm in length. ・High-Precision Filtration The magnetic drum captures chips as small as 50 microns with over 90% efficiency, ensuring clean coolant. ・Environmentally Friendly The consumable-free design reduces industrial waste and supports sustainable operations. ・Reduced Jamming Issues A robust structure efficiently handles hard and entangled chips, minimizing operational disruptions. ■ System Mechanism 1.Filtration of Contaminated Liquid Contaminated liquid flows into the system, where magnetic chips are efficiently captured by the magnetic drum. 2.Chip Transport and Discharge Captured chips are transported by the drum's rotation and discharged at the top of the conveyor. 3.Clean Liquid Supply Filtered liquid is directed to the clean tank and supplied to the machine. ■ System Specifications ・Filtration Precision: 50 microns (over 90% capture efficiency) ・Supported Chips: Hard chips, entangled chips, fine chips ・Environmentally Friendly Design: Consumable-free ■ Applications ・Metal Cutting Processes: Efficient separation and transport of magnetic chips ・Coolant Management: Enhances coolant cleaning efficiency in production lines The "RCC Roller Conveyor" is the ideal solution for high-efficiency chip management and simultaneous improvement of workplace environments. It is the perfect choice for facilities aiming to boost productivity and reduce environmental impact. For more information, please download the PDF or contact us for further consultation!
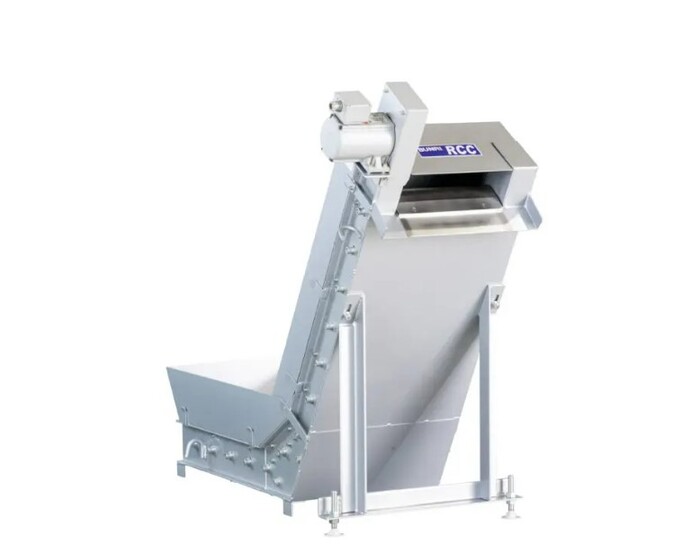
Powerful Magnetic Conveyor "RC" | Combining Durability and High Performance
The "RC Magnetic Conveyor" is a high-performance system designed for the efficient transport and filtration of magnetic chips. It handles a wide range of chip sizes, from fine particles to long chips of approximately 100 mm. Its robust design is ideal for processing hard chips, while the magnetic drum helps reduce industrial waste, maintain a clean working environment, and enhance production efficiency. ■ Key Features ・Supports Various Chip Types Efficiently captures and transports a wide variety of magnetic chips, from long to fine particles. ・High Filtration Precision The magnetic drum captures chips as small as 80 microns with over 90% efficiency, ensuring clean coolant supply. ・Environmentally Friendly Design Eliminates the need for cartridge or paper filters, significantly reducing industrial waste. ・Reduced Operational Issues The robust structure prevents jamming and is capable of handling hard chips efficiently, enhancing operational stability. ■ System Mechanism 1.Filtration of Contaminated Liquid Contaminated liquid flows into the system, where magnetic chips are captured by the magnetic drum as the liquid passes through. 2.Chip Transport and Discharge Captured chips are transported by the rotation of the magnetic drum and discharged at the top of the conveyor. 3.Clean Liquid Supply Filtered liquid passes through slits into the clean tank and is supplied to the machinery. ■ System Specifications ・Filtration Precision: 80 microns (over 90% capture efficiency) ・Supported Chips: Magnetic chips (from long to fine particles) ・Environmentally Friendly Design: Consumable-free ■ Applications ・Metal Cutting Processes: Efficient separation and transport of magnetic chips ・Coolant Cleaning: Ideal for production lines requiring clean working environments The "RC Magnetic Conveyor" is the ultimate solution for precise chip management and improved operational efficiency. Enhance your factory's productivity and maintain a cleaner workplace with this innovative system. For more information, please download the PDF or contact us for further consultation!
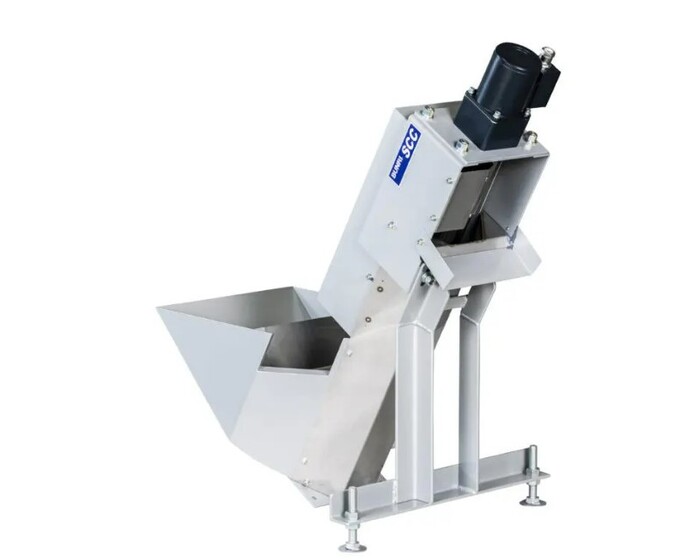
Powerful Magnetic Screw Conveyor "SCC" | High-Efficiency Transport System
The "SCC Magnetic Screw Conveyor" is designed to efficiently handle chips generated from precision machining processes such as gear cutting and broaching. Utilizing a magnetic screw transport mechanism, it supports various chip shapes and sizes. Its heat-resistant design makes it suitable for dry processing in high-temperature environments, providing a versatile solution for diverse machining sites. ■ Key Features ・Safe Design With no exposed rotating parts, it prevents chip entanglement accidents and ensures safe operation. ・Versatility in Chip Handling Capable of handling chips in various forms, including curls up to 50 mm and granular chips. ・Dry Processing Compatible Heat-resistant materials make it ideal for high-temperature dry processing applications. ・No Consumables Required Eliminates the need for cartridge or paper filters, reducing operational costs. ・Environmentally Friendly Minimizes industrial waste and supports sustainable operations. ■ System Specifications ・Filtration Precision: 80 microns (over 90% capture efficiency) ・Supported Chip Sizes: Curls and granular chips up to 50 mm ・Material: High-quality, heat-resistant, and anti-corrosion components ・Drive Mechanism: Internal magnetic rotating axis for efficient transport ■ Applications ・Gear Cutting and Broaching Machines: Efficient chip management in precision machining ・Dry Processing in High-Temperature Environments: Chip transport for dry machining applications ・Precision Machining Sites: Improved coolant cleaning and efficient chip disposal The "SCC Magnetic Screw Conveyor" is an ideal solution for enhancing operational efficiency in precision machining environments, while supporting clean and sustainable manufacturing processes. For more information, please download the PDF or contact us for further consultation!
CONTACT