PRODUCTS
Technology / product information
6hits
Narrow by Industry Category
Narrow by material Category
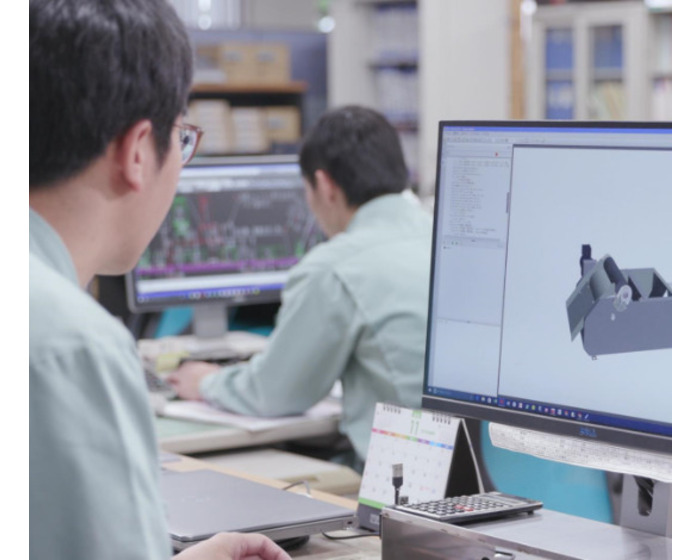
Cost Reduction and CO2 Emissions Reduction Achievements with Bunri Products (Bangkok, Thailand)
Bunri products achieve both economic efficiency and environmental load reduction, providing a high cost-effectiveness that allows for the recovery of the initial investment within one year of introduction. This significantly contributes to the reduction of running costs in production sites, while also contributing to environmental conservation through reduced CO2 emissions. Specific Examples of Running Cost Reduction By reducing running costs, the following savings can be expected within one year: When using paper filters: approximately ¥963,200 saved When using Autonics: approximately ¥1,103,400 saved When using Genex machines: approximately ¥648,000 saved When using machining centers: approximately ¥559,520 saved When using gantry machines: approximately ¥2,578,120 saved When using copying machines: approximately ¥878,400 saved In the long term (10 years), even more significant economic effects can be expected: When using paper filters: approximately ¥9,632,000 saved When using Autonics: approximately ¥11,034,000 saved When using Genex machines: approximately ¥6,480,000 saved When using machining centers: approximately ¥5,595,200 saved When using gantry machines: approximately ¥25,781,200 saved When using copying machines: approximately ¥8,784,000 saved Introducing Bunri products not only immediately enhances economic efficiency but also achieves continuous cost reduction over the long term, making it a critical investment for enhancing corporate competitiveness. For more details, please contact us.
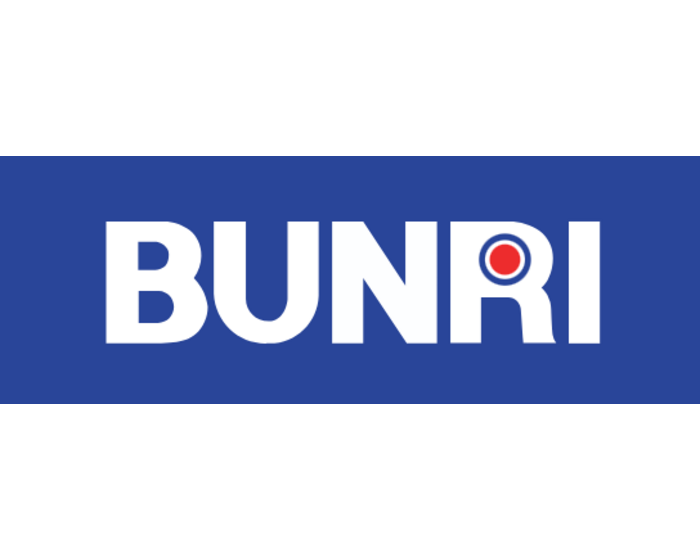
Implementation Effects: CO2 Emission Reduction with Bunri Products (Bangkok, Thailand)
Introducing Bunri products significantly reduces running costs and substantially lowers CO2 emissions, achieving both economic and environmental sustainability for companies. Our products are effective in reducing costs and carbon emissions over one year and ten years. CO2 Emission Reduction CO2 Reduction by Product (1 Year): Magnetic Drum System M100: Reduction of 4,200kg Coolant System for Precision Grinding Machines RTG: Reduction of 7,561kg Coolant System for Ultra-Precision Grinding SB Filter YAO: Reduction of 3,318kg Cyclone Filter Apollo S (APS): Reduction of 5,005kg CO2 Reduction by Product (10 Years): Magnetic Drum System M100: Reduction of 42,000kg Coolant System for Precision Grinding Machines RTG: Reduction of 75,610kg Coolant System for Ultra-Precision Grinding SB Filter YAO: Reduction of 33,180kg Cyclone Filter Apollo S (APS): Reduction of 50,050kg Implementing Bunri products allows you to immediately experience running cost reductions while demonstrating a proactive contribution to combating global warming. In the global movement toward decarbonization and carbon neutrality, our products help achieve these goals.
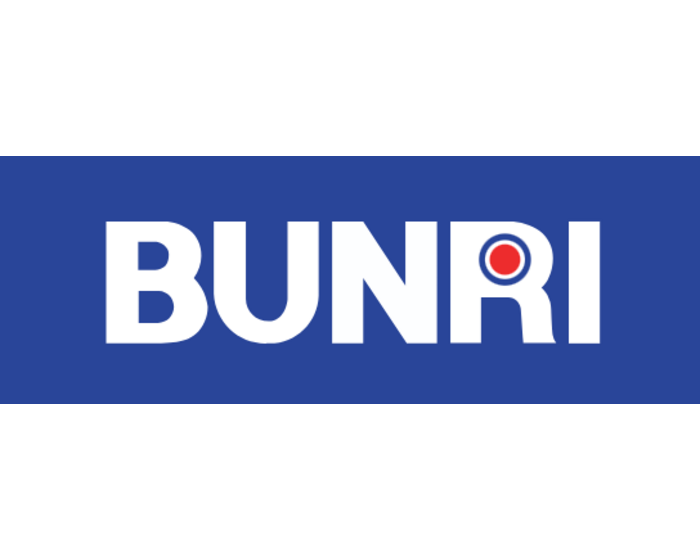
Implementation Case of Bunri's Chain Bucket Skimmer "CBS": Efficient Coolant Management by an Automotive Parts Manufacturer (Bangkok, Thailand)
Implementation Details Coolant Type: Water-soluble Classification: Non-magnetic material, floating oil, and scum Processing Content: Cutting Work Material: Aluminum Chip Shape: Cutting chips from non-magnetic material Machine Tool: Machining center Issues Before Implementation The automotive parts manufacturer was using a belt-type oil skimmer for coolant purification. However, the belt was frequently wearing out and breaking, rendering it ineffective. This situation caused inconvenience and inefficiency in the coolant purification process. Effects After Implementation With the introduction of Bunri's Chain Bucket Skimmer "CBS," the following benefits were observed: Improved Oil Recovery Efficiency: The bucket system achieved higher oil recovery efficiency compared to the belt-type skimmer. Simplified Maintenance: The concern of belt breakage was eliminated, reducing maintenance efforts. Ensured Continuous Operation: Efficient oil recovery improved coolant management for the machine tools, contributing to increased production efficiency.
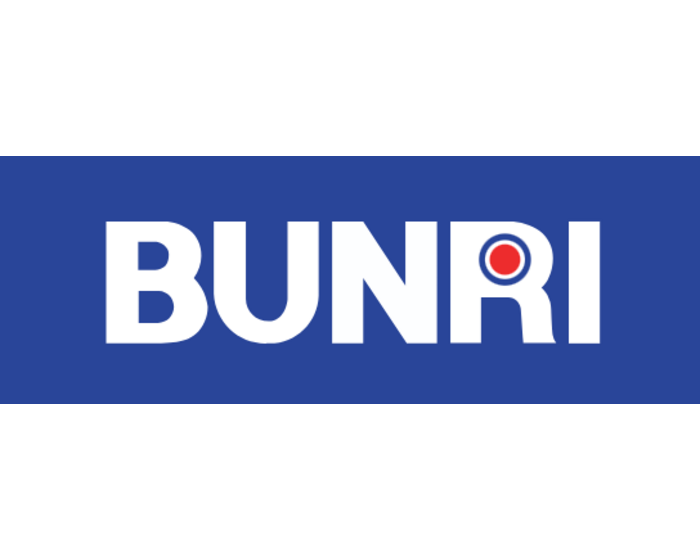
Introduction Case of "Compact" Coolant System for Grinding: Efficiency Improvement by a Special Steel Processing Manufacturer (Bangkok, Thailand)
A special steel processing manufacturer adopted the "Compact" coolant system as an efficient solution to replace bag filters. This system specializes in grinding non-magnetic materials using water-soluble coolant and is suitable for various work materials such as aluminum, stainless steel, and titanium. Issues Before Implementation The bag filters could only collect grinding sludge of 200μm, requiring frequent replacement due to clogging. Additionally, finer sludge accumulated at the bottom of the tank, necessitating regular cleaning. Effects After Implementation The introduction of the new coolant system resulted in the following benefits: Elimination of the need for regular bag filter replacement, leading to reduced running costs and less maintenance work. Effective collection of fine sludge by the system significantly reduced the frequency and effort required for cleaning the coolant tank.
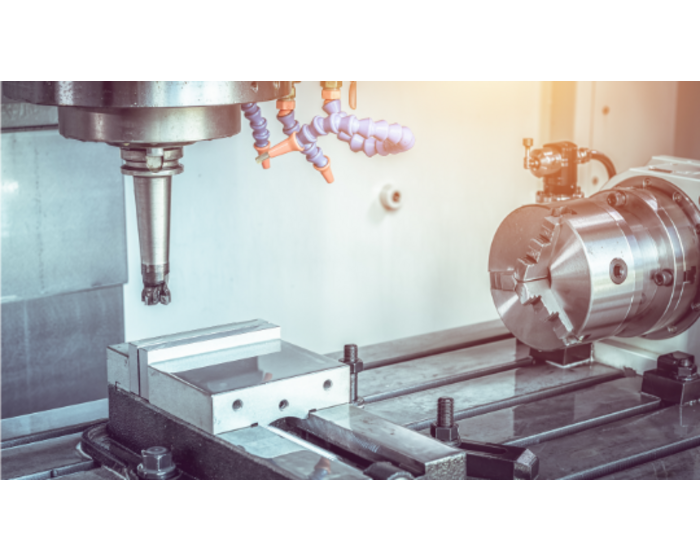
Techniques for Preventing Chip Troubles in Machining - Bangkok, Thailand
Chips vary in shape and color depending on the machining method and work material. Ideally, chips should have a "flowing" shape, smooth and continuous on the surface. On the other hand, sheared or torn chips indicate a decline in machining quality. The color and length of the chips are also important clues in judging the quality of machining. Troubles caused by chips include entanglement around tools or workpieces and drill breakage due to chip clogging. To prevent these, it is necessary to select the appropriate tools, adjust cutting conditions, and optimize coolant treatment. Countermeasures Effective chip countermeasures include using tools with chip breakers and devising cutting paths. Additionally, high-pressure coolant can wash away chips, and adjusting cutting conditions (spindle speed, feed rate, depth of cut) can help. By appropriately combining these methods, machining defects caused by chips can be effectively prevented. Chip control in the machining process is directly linked to increased productivity and high-quality product manufacturing. Controlling chips minimizes the risk of machining defects and achieves efficient production processes.
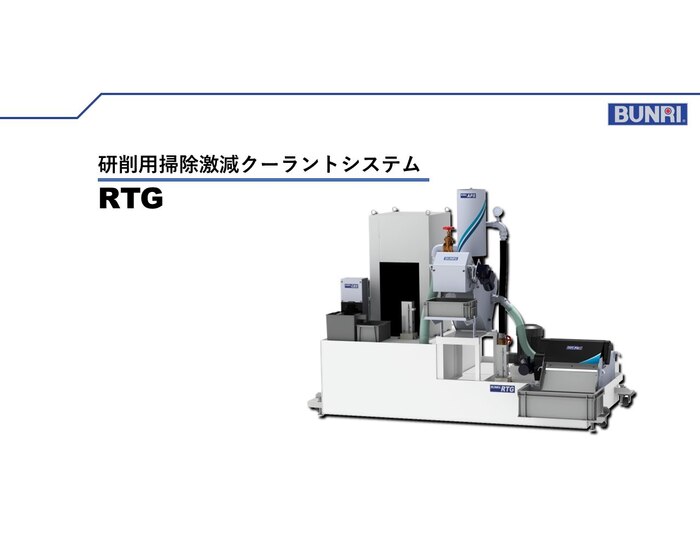
Secrets to Improving Machining Quality! How to Choose and Use Coolant Systems in Bangkok, Thailand
The main features of coolant treatment systems are maximizing tool cooling effects and quickly removing chips. This improves tool durability and stabilizes machining quality. Efficient chip removal also contributes to a better working environment and improves work efficiency. Additionally, selecting the optimal coolant treatment system can reduce the amount of coolant used, thereby minimizing environmental impact. Characteristics of Required High-Performance Coolant Treatment Systems Powerful Cooling Capability: Effectively cools cutting tools to prevent heat damage and wear. Efficient Chip Removal: Prevents chips from entangling with tools or workpieces, contributing to improved machining accuracy. Environmental Consideration: Optimizes the amount of coolant used and includes designs that consider waste fluid treatment. Ease of Maintenance: Facilitates regular maintenance, supporting long-term system operation. By selecting a coolant treatment system with these features, both the efficiency and quality of machining processes can be enhanced.
CONTACT