PRODUCTS
Technology / product information
14hits
Narrow by Industry Category
Narrow by material Category
Narrow by accuracy
Narrow by lot number
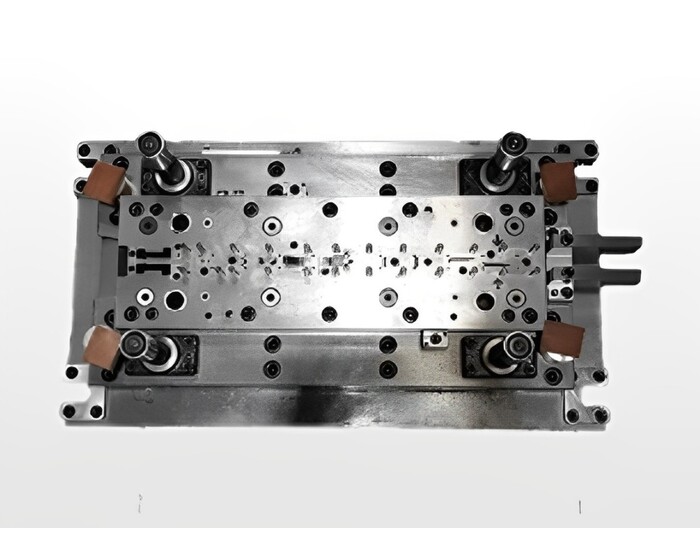
High-Precision Mold Manufacturing Service: From Grinding to Wire Cutting
Leverage leading technology in mold manufacturing, from grinding, milling, EDM, wire cutting, to lapping, creating comprehensive high quality. Our company offers high-precision mold manufacturing services, including grinding, milling, precision grinding for Shoulder Punch parts, EDM (Electrical Discharge Machining), wire cutting, lapping, and TAC SHIM production. These technologies combined enable the production of molds with high precision and quality, meeting the diverse needs of our customers. ■ Features Grinding: Achieving smooth surfaces and high precision. Milling: Precisely manufacturing complex-shaped molds. Precision Grinding for Shoulder Punch Parts: Grinding for specially shaped parts. EDM: Precision machining technology for intricate shapes. Wire Cutting: Ideal for complex detailed parts. Lapping: Creating the smoothest surfaces. TAC SHIM: Manufacturing parts for high-precision gap adjustment. ■ Specifications Manufacturing Technologies: Grinding, milling, EDM, wire cutting, lapping, TAC SHIM. Materials Used: Metals (steel, aluminum, etc.), synthetic materials. Applications: Manufacturing automotive spare parts, electronic devices, medical device components. SIMA Technology Co., Ltd. is located in Nakhon Ratchasima, Thailand. Additionally, SIMA works closely with METCO Factory 1 (Bangkok), Factory 2, and Factory 3 (Samut Prakan) to offer comprehensive services for both domestic and international markets. For more details, please download the PDF or contact us.
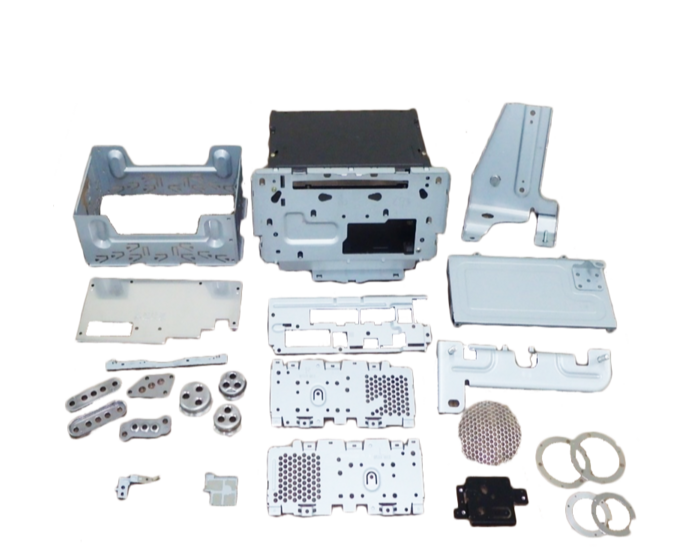
Precision Press Technology Supporting Automotive, Optics, and Electronics Industries
Parts produced by pressing, or known as precision pressed parts, play a significant role in various industries by providing components with high precision and consistency, essential for the assembly and functioning of complex products. These industries include automotive, optics (including lenses), home appliances, etc. This process involves reshaping metal sheets or other materials using a press, which applies force to cut or shape the material into the desired form. ■ Automotive Industry In the automotive sector, precision pressed parts are crucial for the creation and operation of vehicles. These parts range from structural elements like car frames and body panels to smaller, more complex components like engine parts, brackets, and various types of gears and screws. The precision required for these parts is vital in ensuring vehicle safety, performance, and lifespan. The automotive industry benefits from the efficiency of the pressing process, which allows for the mass production of parts with consistent quality and high precision. ■ Optics and Lenses The optics industry, especially in lens production, requires high precision to ensure that optical components correctly refract and focus light. Although traditional glass lenses were not produced through pressing, advancements in material science have led to the use of polymers that can be precision pressed to create complex lens shapes for cameras, glasses, and other optical instruments. This method is particularly valuable for mass-producing lenses with consistent optical properties. ■ Home Appliances Precision pressed parts are also essential in manufacturing home appliances, serving both structural and functional roles, from the outer casings of washing machines and refrigerators to the intricate internal components of microwaves and toasters. Parts produced through pressing are necessary for assembly, durability, and operation of these devices. The ability to efficiently produce large numbers of precise parts makes the pressing process a preferred method in the home appliance industry. ■ Pressing Process The pressing process includes several steps: 1. Design and Engineering: Initially, component designs are finalized, and suitable materials are selected. This step involves detailed planning to ensure that parts meet all functional and aesthetic requirements. 2. Tool and Die Making: Custom tools and dies are created based on part designs. These tools and dies are used in presses to shape materials. 3. Pressing: Material (typically metal sheets or polymers) is placed in the press, where tools and dies apply force to cut or shape the material into parts. This process can include punching, bending, embossing, and other shaping methods. 4. Finishing: After pressing, parts may undergo finishing processes like trimming, polishing, or coating to improve appearance, corrosion resistance, or other surface properties. ■ Advantages of Precision Pressed Parts 1. Consistency and Quality: The pressing process guarantees that every part is identical, meeting the stringent requirements necessary for high-performance applications. 2. Efficiency: Pressing is suitable for mass production, making it a cost-effective choice for industries like automotive and home appliances. 3. Versatility: Advances in pressing technology allow for a variety of materials to be used and complex shapes to be created, meeting the needs of diverse industries. Precision pressed parts are a critical component of modern manufacturing, offering a combination of precision, efficiency, and versatility unmatched by other production methods. Their cross-industry application underscores the importance of the pressing process in today's technological and industrial landscape. For more details, please download the PDF or contact us.
High-Precision Metal Stamping Services: Supporting 10 to 300 Tons
Our company offers comprehensive metal stamping services using advanced technology. We operate 65 stamping machines capable of handling capacities from 10 to 300 tons. In addition to stamping, we provide secondary processing services such as cleaning, tapping, and spot welding, ensuring high-quality metal components. Our services cater to various industries, including automotive parts, electronic devices, and construction materials. ■ Features Diverse Range of Press Machines: We utilize high-speed, continuous, single, and robot-assisted press machines to meet all production needs. Comprehensive Services: From stamping to cleaning, tapping, and spot welding, we offer complete processing solutions. Capability for Projects of All Sizes: With press capacities ranging from 10 to 300 tons, we handle everything from small to large components. High Efficiency: Leveraging advanced machinery and experienced staff, we deliver high-quality products on tight schedules. Cost-Effective and Quality-Oriented: Our integrated production system reduces costs while maintaining top-notch quality. ■ Specifications Types of Press Machines: High-speed, continuous, single, and robot-assisted presses Press Capacity: 10 to 300 tons Materials Supported: Stainless steel, aluminum, and non-ferrous metals Secondary Processes: Cleaning, tapping, and spot welding ■ Applications Automotive Parts: Such as vehicle frames, engine components, and interior parts Electronic Devices: Including precision metal parts and device housings Construction Materials: Such as metal frames and mounting components ■ Strengths of SIMA Technology Co., Ltd. Located in Nakhon Ratchasima, Thailand, SIMA Technology Co., Ltd. operates 65 stamping machines to serve both domestic and international clients. With a strong production network, including METCO Factory 1 (Bangkok), Factory 2, and Factory 3 (Samut Prakan), we ensure fast and high-quality production. For more details, please download the PDF or contact us.

High-Precision Stamped Component Manufacturing Services: From Small to Large-Scale Production
Our company operates 65 press machines with capacities ranging from 10 to 300 tons, catering to a wide variety of production requirements. Our technology includes high-speed presses, progressive presses, single presses, and robotic production lines. Additionally, we provide auxiliary equipment such as cleaning machines, tapping machines, and spot welding machines to ensure a complete and streamlined production process from start to finish. ■ Features Versatile Press Options: Includes high-speed presses, progressive presses, single presses, and robotic production lines for efficient manufacturing. Comprehensive Auxiliary Equipment: Features cleaning machines, tapping machines, and spot welding machines to enhance production efficiency and product quality. Flexible Production Capabilities: Supports both low-volume trial runs and high-volume mass production with a flexible manufacturing approach. High Precision and Efficiency: Advanced technology and machinery ensure the production of complex and highly precise components. ■ Specifications Number of Press Machines: 65 Press Capacity: 10 to 300 tons Manufacturing Technologies: High-speed presses, progressive presses, single presses, robotic production lines Auxiliary Equipment: Cleaning machines, tapping machines, spot welding machines ■ Applications Automotive Components: Precision parts for the automotive industry Electronic Components: Components for home appliances and electronic devices Industrial Parts: Precision parts for machinery and equipment Others: Custom parts for various specialized applications ■ Strengths of SIMA Technology Co., Ltd. SIMA Technology Co., Ltd., located in Nakhon Ratchasima, Thailand, leverages its advanced press technology and facilities to meet diverse customer needs. With the support of METCO Factory 1 (Bangkok), Factory 2, and Factory 3 (Samut Prakan), we ensure fast and reliable delivery of high-quality products to both domestic and international markets. For more details, please download the PDF or contact us.
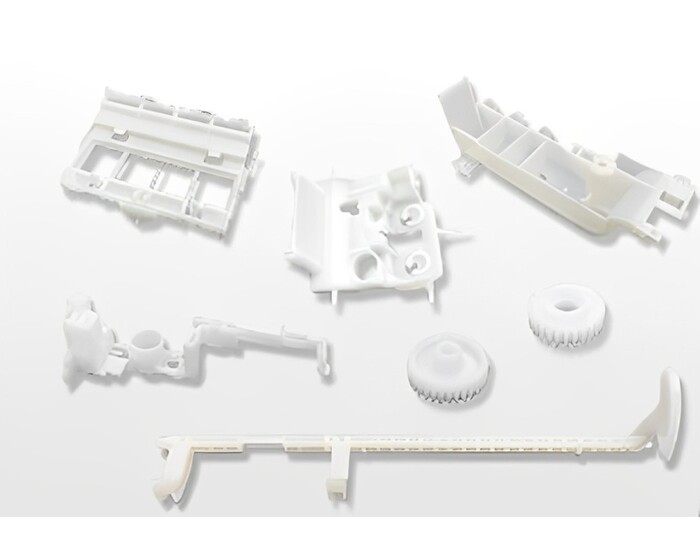
High-Quality Plastic Injection Molding Services for Precision Components
SIMA Technology Co., Ltd. is located in Nakhon Ratchasima, Thailand. Additionally, SIMA works closely with METCO Factory 1 (Bangkok), Factory 2, and Factory 3 (Samut Prakan) to offer comprehensive services for both domestic and international markets. Our company operates 22 injection molding machines ranging from 30 to 130 tons. Using various materials such as POM, ABS, PS, PE, and PP, we produce high-quality, precision plastic components. Our primary products include printer parts and medical device components. ■ Features Wide Range of Injection Machines: Machines ranging from 30 to 130 tons, supporting small to large part production Diverse Material Options: Materials such as POM, ABS, PS, PE, and PP to suit various applications Precision Products: Expertise in producing high-accuracy parts for printers and medical devices Strict Quality Control: Ensures high and consistent product quality Professional Engineering Team: Provides technical support and process improvements ■ Specifications Injection Machine Range: 30 to 130 tons, 22 machines Materials: POM, ABS, PS, PE, PP Products: Printer parts, medical device components ■ Geographical Advantage Located in Nakhon Ratchasima, SIMA provides efficient service for domestic and export markets. Collaboration with METCO Factory 1, 2, and 3, situated in Bangkok and Samut Prakan, ensures comprehensive production and export support. For more details, please download the PDF or contact us.
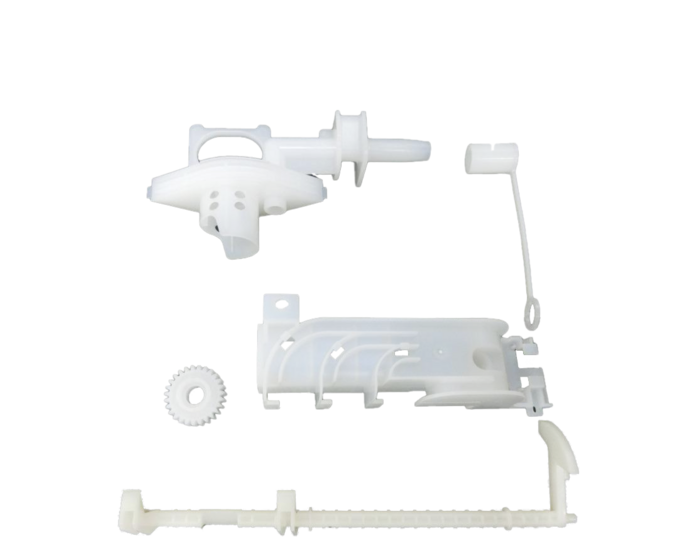
High-Quality Plastic Injection Molding Services: From Printer Parts to Medical Devices
SIMA Technology Co., Ltd., located in Nakhon Ratchasima, Thailand, leverages its geographical advantage to provide a wide range of manufacturing services. As the only Muramoto Group production base capable of performing metal plating and anodizing processes, SIMA is a vital hub for specialized manufacturing. Additionally, with other production bases such as METCO Factory 1 (Bangkok), Factory 2 (Samut Prakan), and Factory 3 (Samut Prakan), SIMA ensures comprehensive service coverage for both domestic and international customers. Specializing in precision injection-molded plastic components, we supply high-quality products for printer parts and medical devices, meeting stringent customer quality requirements with reliability. ■ Features Precision Injection Molding Technology: Advanced technology to meet complex design requirements. High-Quality Material Selection: Supports materials such as POM, ABS, PS, PE, and PP for enhanced product performance. Strict Quality Control: Adheres to rigorous quality management systems to ensure consistent product quality. Custom Product Development: Offers tailored manufacturing solutions to meet specific customer needs. ■ Specifications Supported Materials: POM, ABS, PS, PE, PP Product Applications: Printer parts, medical device components Injection Machine Types: High-speed, advanced, single-line, and robotic-integrated lines ■ Geographical Advantage SIMA Technology Co., Ltd., located in Nakhon Ratchasima, benefits from its strategic location to provide flexible services to both domestic and international clients. By coordinating with METCO Factory 1 (Bangkok) and Factories 2 and 3 (Samut Prakan), we ensure comprehensive manufacturing and export support. SIMA Technology Co., Ltd. is your trusted partner for high-precision plastic components. With cutting-edge technology and a broad production network, we deliver quality and efficiency tailored to your diverse needs. For more details, please download the PDF or contact us.
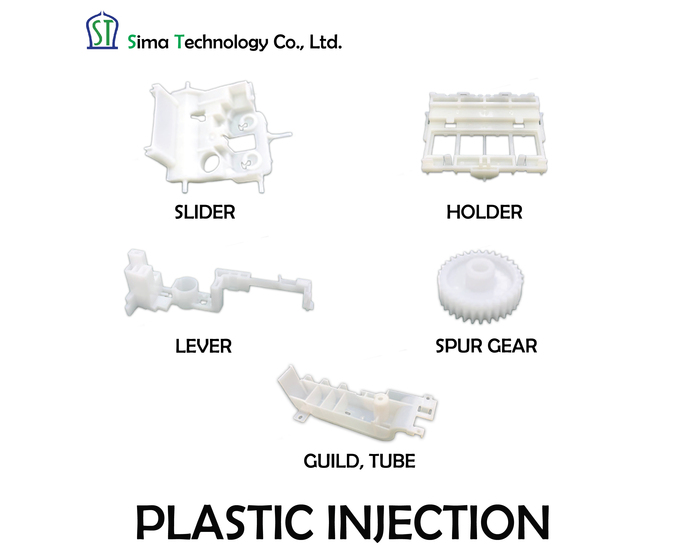
Injection Molding Service for PE and PP Materials: Ideal for Medical Equipment and Printer Parts
Our company offers cutting-edge injection molding technology using 22 machines ranging from 30 to 130 tons. We specialize in manufacturing medical equipment and printer parts, ensuring high-quality products that meet rigorous customer standards. ■ Features Wide Material Compatibility: Supports a variety of plastics such as POM, ABS, PS, PE, and PP, suitable for diverse applications. Precision Injection Molding: Capable of producing complex and highly accurate components. Industry Expertise: Specializes in manufacturing components for medical equipment and printers. Versatile Machinery: Equipped with 22 injection molding machines to accommodate various project sizes. Strict Quality Control: Ensures consistent quality throughout the production process. ■ Specifications Number of Machines: 22 Machine Capacity: 30 to 130 tons Supported Materials: POM, ABS, PS, PE, PP Example Products: Medical equipment parts, printer parts ■ Applications Medical Equipment: External components and internal mechanisms of medical devices Printer Parts: Internal structures and mechanical components Others: Custom parts for various industries ■ Strengths of SIMA Technology Co., Ltd. Located in Nakhon Ratchasima, Thailand, SIMA Technology Co., Ltd. leverages a robust production network, including METCO Factory 1 (Bangkok), Factory 2, and Factory 3 (Samut Prakan), to deliver high-quality products quickly to both domestic and international clients. For more details, please download the PDF or contact us.
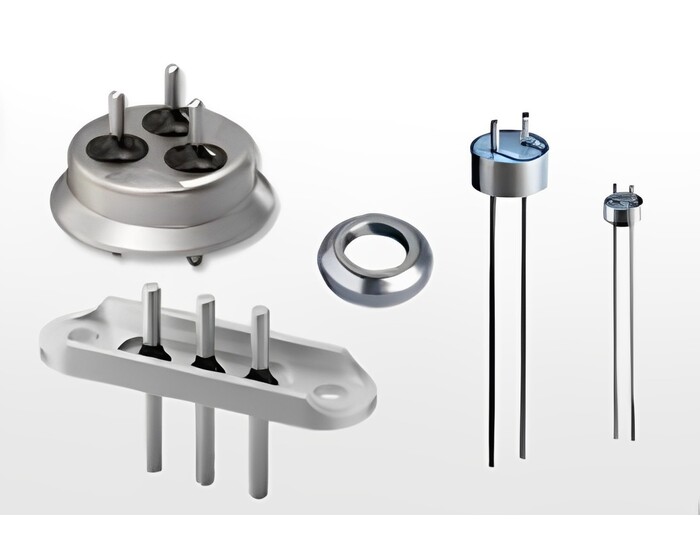
Electroplating & Electroless Plating Services: High-Quality Finishes from Nickel to Gold
Our company offers comprehensive metal plating services, including both electroless and electroplating options. Electroless plating includes nickel and gold finishes, while electroplating encompasses nickel, gold, lead, lead-free, and copper. These technologies are tailored to meet the demands of diverse industries such as automotive components, electronic devices, and jewelry, enhancing durability, corrosion resistance, and aesthetics. ■ Features Electroless Plating Nickel: Provides excellent wear resistance and corrosion protection. Gold: Offers superior conductivity and high resistance to corrosion. Electroplating Nickel: Ensures strong adhesion and high corrosion resistance. Gold: High-purity plating enhances the reliability of contact points. Lead (Pb): Traditional plating for increased wear resistance. Lead-Free (Pb-Free): Environmentally friendly and safe alternative. Copper: Offers excellent electrical conductivity and thermal transfer. ■ Specifications Electroless Plating: Utilizes chemical reactions to deposit uniform metal coatings without electricity. Suitable for complex-shaped parts. Electroplating: Applies electrical current for dense and even metal layers. Adjustable thickness and properties based on specific requirements. ■ Applications Automotive Industry: Components requiring high durability and corrosion resistance. Electronic Devices: Parts that demand superior conductivity and reliability. Jewelry: Decorative uses requiring beauty and durability. ■ Strengths of SIMA Technology Co., Ltd. SIMA Technology Co., Ltd. is based in Nakhon Ratchasima, Thailand, and specializes in high-quality metal plating services. Supported by METCO Factory 1 (Bangkok), Factory 2, and Factory 3 (Samut Prakan), we ensure fast and efficient production for domestic and international clients. For more details, please download the PDF or contact us.
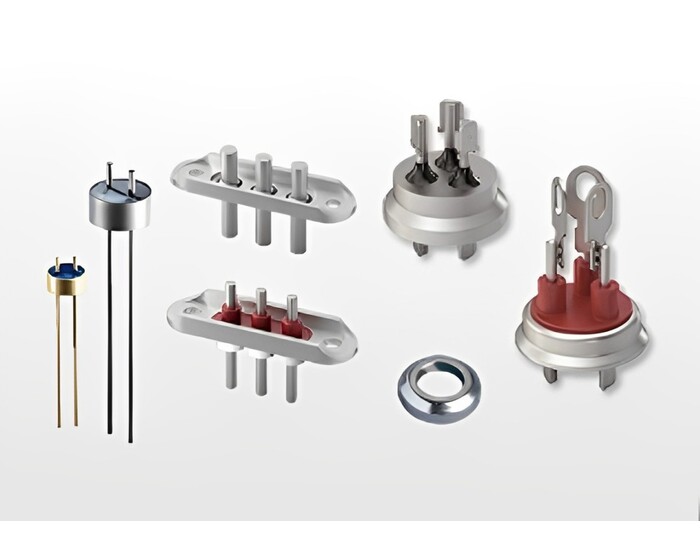
Glass-Metal Sealing Technology: Supporting Applications from Refrigerators to Automobiles
Our glass-metal seal components are designed for hermetic compressor terminals that demand high sealing performance. Available in three types—REF, Cylinder, and Automotive—they are particularly suited for refrigeration and automotive industries. These components withstand harsh environments, preventing leaks and contamination while ensuring stable equipment operation over an extended lifespan. ■ Features Superior Sealing Performance: Combines glass and metal to prevent leaks and contamination effectively. High-Temperature Resistance: Maintains performance in high-heat environments, enhancing safety. Corrosion Resistance: Uses materials resistant to chemicals and moisture. Versatility: Available in three types—REF, Cylinder, and Automotive—to meet diverse needs. Ease of Installation: Requires no special tools, making on-site setup simple and quick. ■ Specifications Types: REF, Cylinder, Automotive Materials: Special glass and heat-resistant metals Operating Temperature Range: -50℃ to +250℃ Pressure Tolerance: Up to 10MPa Product Sizes: Varies by type (customizable) ■ Applications Refrigeration Equipment: Such as compressor terminals for refrigerators and air conditioners Automotive Industry: Including engine components and critical electronic parts Electronic Devices: For industrial tools and precision equipment ■ Strengths of SIMA Technology Co., Ltd. Based in Nakhon Ratchasima, Thailand, SIMA Technology Co., Ltd. specializes in manufacturing high-quality glass-metal seal components. With support from METCO Factory 1 (Bangkok), Factory 2, and Factory 3 (Samut Prakan), we efficiently serve domestic and international clients. For more details, please download the PDF or contact us.
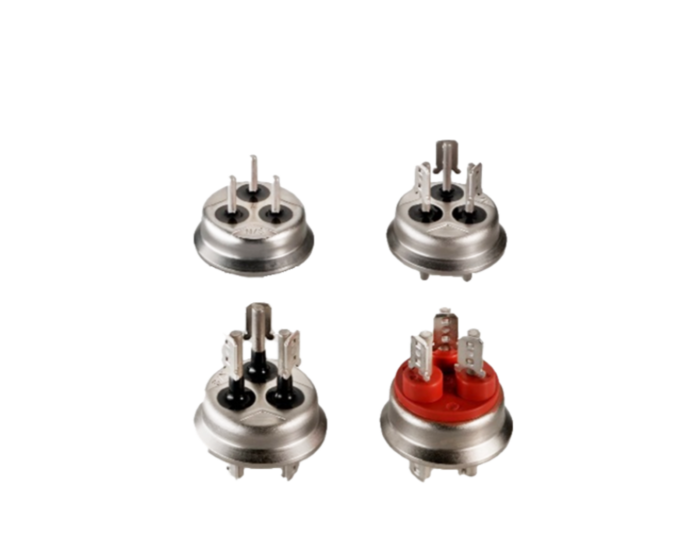
Hermetically Sealed Terminal for High-Temperature and High-Humidity Environments
Hermetically sealed terminals are designed to meet the demands of high-temperature and high-humidity environments, such as those in compressors, hard drives, and automotive electrical systems. By providing complete sealing, these terminals protect internal components from moisture, dust, and other external contaminants, enhancing the durability and stability of machines and systems. ■ Features Excellent Waterproof and Dustproof Performance: Prevents deterioration caused by environmental factors, ensuring long-term reliability. Wide Temperature Range: Operates effectively in both high and low temperatures. High Durability: Withstands physical stress and chemical exposure. Versatile Design: Suitable for cooling systems, data storage, and automotive electronics. Adaptable to Harsh Environments: Resistant to moisture, vibration, and corrosive elements. ■ Applications Cooling Systems: Usage: Refrigerators and air conditioning units Role: Prevents refrigerant leaks and moisture ingress Data Storage: Usage: High-reliability hard disk drives (HDDs) Role: Protects internal environments and ensures data stability Automotive Electrical Systems: Usage: Batteries, sensors, and control units Role: Provides reliability in extreme road conditions and temperature changes ■ Strengths of SIMA Technology Co., Ltd. Located in Nakhon Ratchasima, Thailand, SIMA Technology Co., Ltd. specializes in producing high-quality hermetically sealed terminals. With support from METCO Factory 1 (Bangkok), Factory 2, and Factory 3 (Samut Prakan), we efficiently serve customers locally and internationally. Hermetically sealed terminal technology is critical for ensuring machine reliability and safety, supporting diverse industries in harsh environments. For more details, please download the PDF or contact us.
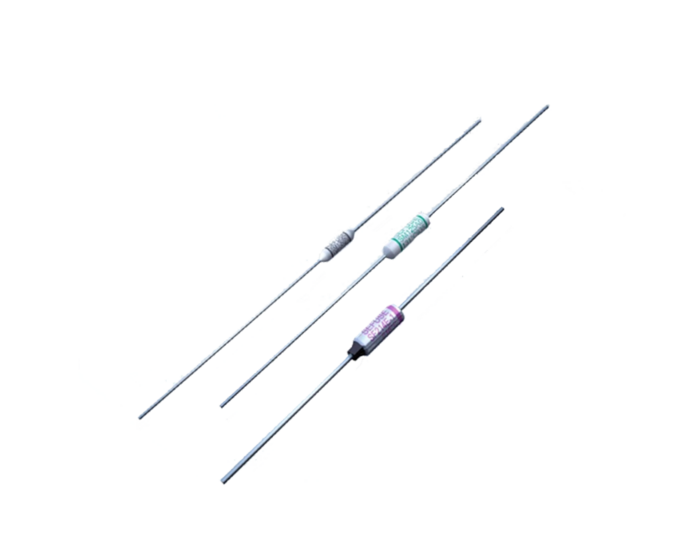
Thermal Fuses for the Protection of Electrical Appliances, Office Equipment, and Automotive Systems
SIMA Technology Co., Ltd. is located in Nakhon Ratchasima, Thailand, leveraging its geographical advantage to serve both domestic and international clients efficiently. Additionally, its collaboration with METCO Factory 1 (Bangkok), Factory 2, and Factory 3 (Samut Prakan) ensures streamlined production and delivery of high-quality products. Thermal fuses are essential safety devices that interrupt electrical circuits when temperatures exceed a preset threshold, making them indispensable for household appliances, office equipment, and automotive systems. ■ Features Enhanced Safety: Interrupts circuits during overheating, reducing fire risks High Reliability: Protects components from thermal damage and prolongs lifespan Flexibility: Customizable for different temperature ranges and applications Cost-Effective: Delivers high safety benefits at a low cost ■ Applications Home Appliances: Coffee makers, microwaves, hair dryers for overheat protection Office Equipment: Protecting motors in copiers and printers Automotive Systems: Ensuring safety in electric seats and window motors ■ Geographical Advantage of SIMA Located in Nakhon Ratchasima, SIMA leverages its strategic location and collaboration with METCO factories to deliver high-quality products and comprehensive solutions globally. Thermal fuse technology is a simple yet highly effective safety solution. Design and placement tailored to various applications greatly enhance the safety and performance of devices. For more details, please download the PDF or feel free to contact us.
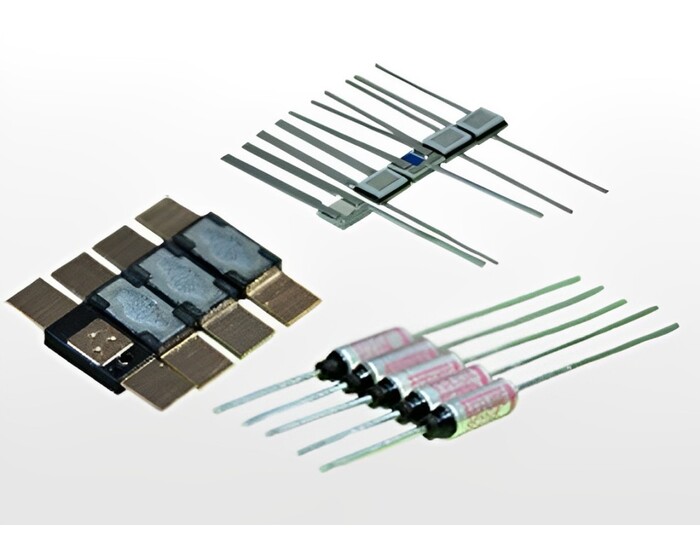
Thermal Fuses and Battery Fuses: Comprehensive Protection Solutions for Electronic Components
Our company manufactures thermal and battery fuses to protect electronic devices from overheating and overcharging. Thermal fuses are available in SF, SFH, and SM types, while battery fuses include D6S, D6, and SEREB models. These products are suitable for a wide range of applications, from consumer electronics to industrial equipment, enhancing the safety and reliability of electronic devices. ■ Features 1. Overheat Protection: Thermal Fuses: Automatically cut off circuits when a predefined temperature is reached, preventing overheating and fire. Supported Models: SF, SFH, SM 2. Overcharge Protection: Battery Fuses: Protect batteries from overcharging, overcurrent, and short circuits. Supported Models: D6S, D6, SEREB 3. Wide Temperature and Current Range: Flexible to support a variety of electronic device requirements. 4. Compact Design: Easy to integrate into electronic devices. 5. High Reliability: Delivers stable and long-lasting protection. ■ Specifications Thermal Fuses Models: SF: Operating temperature range 73℃~240℃ SFH: Operating temperature range 150℃~192℃ SM: Operating temperature range 98℃~260℃ Current: 1A~10A Battery Fuses Models: D6S: Current range 2A~10A D6: Current range 2A~20A SEREB: Current range 10A~60A Voltage: 32V~60V ■ Applications Consumer Electronics: Such as household appliances, mobile devices, and IT equipment Industrial Equipment: Including machinery and control systems Energy Devices: Such as battery management systems ■ Strengths of SIMA Technology Co., Ltd. Based in Nakhon Ratchasima, Thailand, SIMA Technology Co., Ltd. specializes in high-quality thermal and battery fuses. With support from METCO Factory 1 (Bangkok), Factory 2, and Factory 3 (Samut Prakan), we efficiently serve both domestic and international clients. For more details, please download the PDF or contact us.
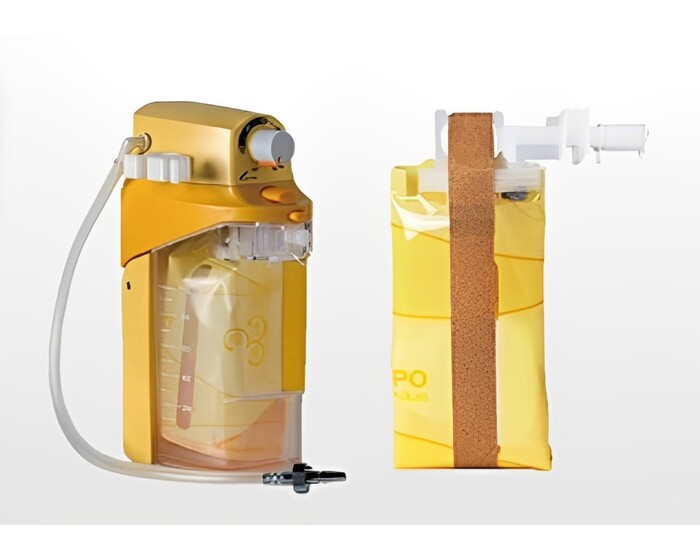
High-quality Fluid Collection Bags for Medical Settings: Safe and Hygienic Patient Care
High-quality Fluid Collection Bags: Protecting Safety and Hygiene in Medical Settings. Offering Optimal Solutions for Hospitals and Clinics ■ Overview This product is a collection of high-quality body fluid collection bags for safely and hygienically collecting and managing various fluids produced in medical settings (such as blood, pus, digestive fluids). They are durable and well-sealed to ensure precise collection of fluids expelled by patients. Additionally, they can be disposed of after use, reducing the risk of infection and increasing the efficiency of medical staff operations. ■ Features High Durability: Prevents leakage and bursting of fluids. Good Sealing: Reduces the risk of infection and maintains hygiene in medical settings. Designed for Post-use Disposal: Easy to manage after use and maintains a hygienic environment. Available in Various Sizes: Meets different medical situations and can be widely used. Easy to Install and Remove: Reduces the workload of medical staff. ■ Specifications Material: Medical-grade plastic. Capacity: 500ml, 1000ml, 2000ml. Packaging: Pack of 10 pieces per size. Color: Transparent (for easy inspection of fluid condition). Bag Opening: Compatible with standard medical devices. This product ensures the safe and hygienic management of body fluids in various situations in medical settings, whether during surgery, caring for critically ill patients, or managing long-term patients. It is an essential tool for medical staff and supports a comfortable environment for patient recovery. ■ Geographical Advantage SIMA Technology Co., Ltd., located in Nakhon Ratchasima, benefits from its strategic location to provide flexible services to both domestic and international clients. By coordinating with METCO Factory 1 (Bangkok) and Factories 2 and 3 (Samut Prakan), we ensure comprehensive manufacturing and export support. For more details, please download the PDF or contact us.
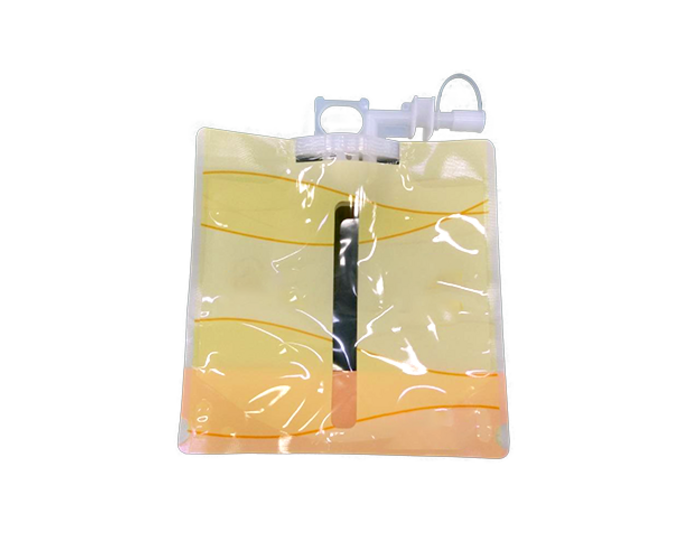
Medical Suction Liquid Collection Bags: Safely Managing Blood and Secretions
Liquid collection bags are essential components of medical devices, particularly in surgeries, postoperative care, and emergency medicine. These bags collect blood, mucus, and other fluids from patients, ensuring a clean and safe medical environment. Our collection bags are designed to be durable and user-friendly, minimizing contamination risks and facilitating safe disposal. ■ Features High Durability: Made from medical-grade plastic that resists leaks and pressure. Transparent or Semi-Transparent Design: Allows medical staff to easily monitor fluid levels. Secure Sealing System: Prevents leaks and contamination. Versatile Functionality: Optional additions include solidifiers and hydrophobic filters. Safe and Easy Disposal: Single-use design simplifies waste management. ■ Components Liquid Collection Bag: The main component for collecting fluids, made from strong materials. Tightly Sealed Cap: Ensures no leaks and facilitates safe disposal. Hydrophobic Filter (Optional): Prevents liquid leakage while allowing air passage. Liquid Solidifier (Optional): Converts liquid into a solid for safer disposal. Overflow Valve: Prevents spillage when the bag is full. ■ Applications Operating Rooms: For managing fluids during surgeries. Emergency Medicine: Safely collecting blood and fluids in critical situations. ICU or Patient Wards: Enhances safety and convenience in fluid management. ■ Advantages of SIMA Technology Co., Ltd. Located in Nakhon Ratchasima, Thailand, SIMA Technology Co., Ltd. leverages its strategic location to efficiently serve both domestic and international clients. Supported by METCO Factory 1 (Bangkok), Factory 2, and Factory 3 (Samut Prakan), we ensure swift production and delivery. Our liquid collection bags for medical devices offer reliable quality and practical designs to enhance safety and convenience in healthcare settings. For more details, please download the PDF or contact us.
CONTACT