PRODUCTS
Technology / product information
9hits
Narrow by Industry Category
Narrow by material Category
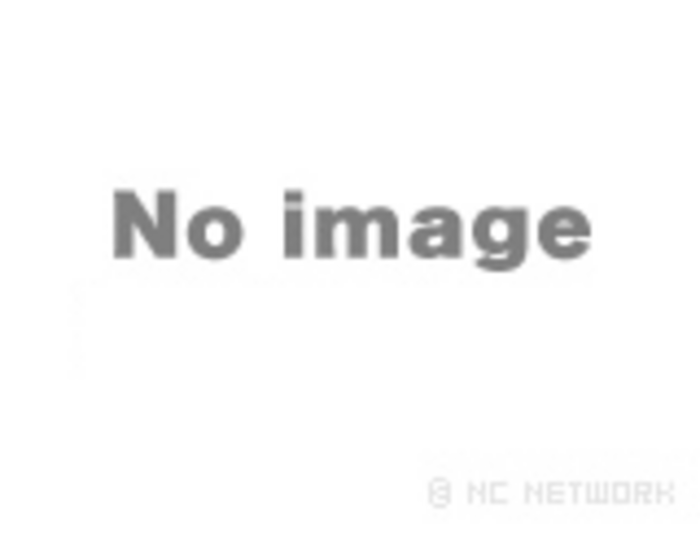
Fabrication and Installation of Ship Lock Gates – Advanced Thick Steel Plate Fabrication Technology in Vietnam
Ship Locks are critical structures in canal construction and marine projects, ensuring the safe navigation of vessels. The manufacturing and installation of ship locks require high strength, durability, and adaptability to on-site environmental conditions. Leveraging specialized manufacturing facilities for thick plates and large-scale products, as well as the expertise of skilled welding technicians, our company delivers high-quality products that meet stringent standards. 【Features】 Proven experience in major canal projects in Vietnam. High manufacturing precision by 398 skilled welding technicians. Technicians with in-depth knowledge of welding processes ensure the highest quality welding. Our welding technology is ISO 3834 certified, ensuring processes are managed in compliance with international standards. Capability to handle thick plates and large-scale products. Utilization of 50–600t crane equipment enables the production of heavy and large structures. Simulation from the design stage. Through calculations and simulations during the product design phase, we propose optimal welding methods and provide customized solutions tailored to customer requirements. 【Applications】 Canal Construction: Our durable ship locks are essential for canal and water gate projects and have been adopted in numerous domestic projects. In 2023, Lilama completed the Giao Thuy Canal Project in Nam Dinh Province. This project features the largest ship lock in Vietnam, supporting the passage of vessels weighing over 2,650 tons. Marine Structures: Ship locks with anti-corrosion treatments suitable for marine conditions are also applicable to port facilities and river structures. Industrial Infrastructure: Our products demonstrate high reliability in industrial waterways and drainage systems. 【Quality Assurance and Production System】 LILAMA10 applies ESHS standards to all projects it participates in. We have obtained certifications for steel structure manufacturing quality management systems compliant with European standard EN 1090-EXC3 (CE marking) and welding quality certification based on ISO 3834. We adopt flexible production schedules tailored to project needs, ensuring high quality even with short delivery times. 【Summary】 Our company achieves high durability and strength in the manufacturing of ship locks, supporting safe vessel navigation in canal construction and marine projects. Specializing in thick plates and large-scale products, our 398 skilled welding technicians guarantee high-precision welding under ISO 3834 certification. Utilizing 50–600t crane equipment and simulation technology, we provide optimal products tailored to on-site requirements. With extensive experience in domestic and international projects, such as the Gia Khuan Canal Project, we also apply anti-rust coatings and other surface treatments. We offer flexible solutions for short delivery times while ensuring high quality. For more details, please download the PDF or feel free to contact us.
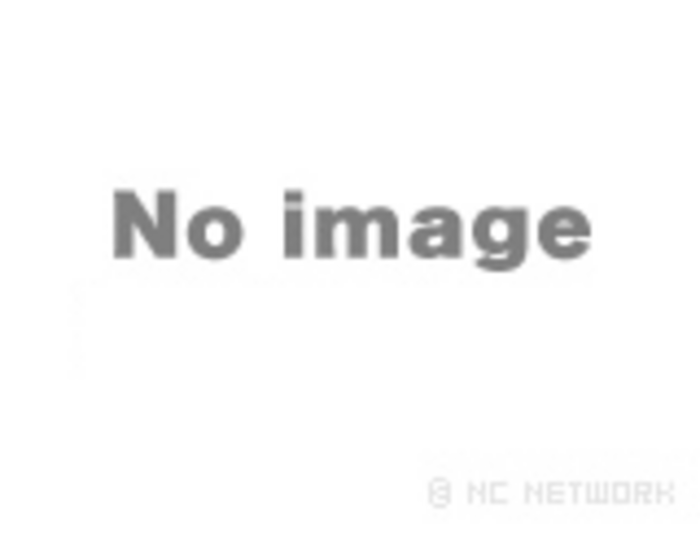
Fabrication of Steel Structures for Penstocks and Trash Screens for Hydropower Plants in Vietnam
Penstock (Piping) and Trash Screens are critical structural components that support the efficiency and stable operation of hydropower plants. The penstock is a pipe that withstands pressure from water head differences and delivers water to the turbines, while the trash rack is a device that removes debris and foreign objects from the water flow, significantly contributing to equipment protection and reducing maintenance costs. The manufacturing of these products utilizes advanced can welding technology, particularly excelling in handling thick plates and large-scale products. LILAMA10 employs 398 skilled technicians who, based on their extensive experience and advanced technical expertise in welding processes, deliver reliable quality. Additionally, through calculations and simulations from the design stage, we propose optimal welding methods to provide products with superior durability. 【Features】 Participation in Laos' largest hydropower project High-quality manufacturing by 398 skilled welding technicians Extensive experience in manufacturing thick plates (up to 110mm) and large-scale products 【Facilities】 Three-roll bending machine (Made in Italy): Capable of bending metal pipes (piping) that withstand high pressure, meeting stringent technical standards. 50–600t crawler cranes: Suitable for manufacturing critical components and structures. Surface treatment: Shot blasting and anti-rust painting for extended lifespan. 【Applications】 Hydropower plants and irrigation projects: Protects turbines by removing debris, utilized in irrigation projects, and adopted in the Nam Ngum Hydropower Project (Laos). Plant construction: Pipe manufacturing, protection, and operational optimization. Infrastructure construction: Utilized in water-related projects. The ""Penstock (Piping) and Trash Racks"" manufactured by LILAMA10 are adopted across various industries. Particularly in hydropower plants, they prevent equipment damage caused by debris and foreign objects, significantly extending the lifespan of turbines and pumps. 【Quality Assurance and Production System】 LILAMA10 applies ESHS standards to all projects it participates in. We have obtained certifications for steel structure manufacturing quality management systems compliant with European standard EN 1090-EXC3 (CE marking) and welding quality certification based on ISO 3834. 【Summary】 The ""Penstock (Piping) and Trash Screens"" are manufactured under strict quality control to enhance the efficiency and stable operation of hydropower plants. Leveraging LILAMA10's advanced can manufacturing technology and the expertise of skilled technicians, we improve the precision and durability of thick plates and large-scale products. Furthermore, optimization of welding methods based on calculations and simulations from the design stage enables us to provide customized solutions. Moving forward, we will continue to utilize these qualities and technical capabilities to supply various plants and energy facilities, including hydropower plants. For more details, please download the PDF or feel free to contact us.
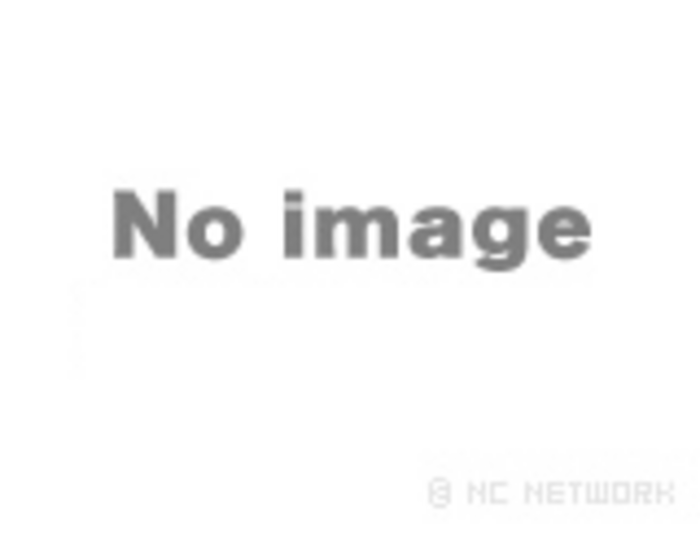
Fabrication of Radial Gates, BO Coarse Screens, and Stoplog Gates for Hydropower Plants in Vietnam
Radial gates, BO Coarse Screens, and maintenance sluice gates play a crucial role in hydropower plants and various infrastructure projects. These gates, responsible for water flow control and safety management, require high durability and precision. With years of expertise in metal fabrication, we provide high-quality and reliable radial gates and BO Coarse Screens. Key Features Proven track record of participation in Laos’ largest hydropower project. A team of 398 highly skilled welding engineers ensures top-quality finishing. Expertise in fabricating large steel structures with thickness up to 110mm We propose optimal welding methods based on calculations and simulations from the design phase. Equipment Three-roll bender (Italy-made): Capable of bending ultra-thick plates (up to 110mm). 50–600t crawler cranes: Safe and efficient transportation of large and heavy components during the manufacturing process. Surface treatment: Shot blasting, anti-corrosion painting for extended lifespan. Welding equipment: Comprehensive range of machines, including TIG welding, MIG/MAG welding, automatic welding, and DC welding machines. Applications & Industries Hydropower and Irrigation Projects: Used for water flow control in hydropower projects and dam construction. Proven track record in international projects, including the Nam Theun Hydropower Project (Laos). Quality Assurance & Production System We apply ESHS standards to all projects involving LILAMA10. Certified in EN 1090-EXC3 (CE Marking) for steel structure quality management and ISO 3834 for welding quality assurance. Conclusion Our company specializes in manufacturing radial gates and BO Coarse Screens for hydropower plants with advanced fabrication technology. These gates, essential for water flow control and safety, require high durability and precision. With extensive experience in thick plate and large-scale product manufacturing, our team of 398 skilled technicians ensures high-precision welding. We propose optimal welding solutions from the design phase and hold certifications such as EN 1090-EXC3 and ISO 3834. With a strong track record in international projects, we contribute to the development of sustainable energy. For more details, download our PDF or contact us anytime.
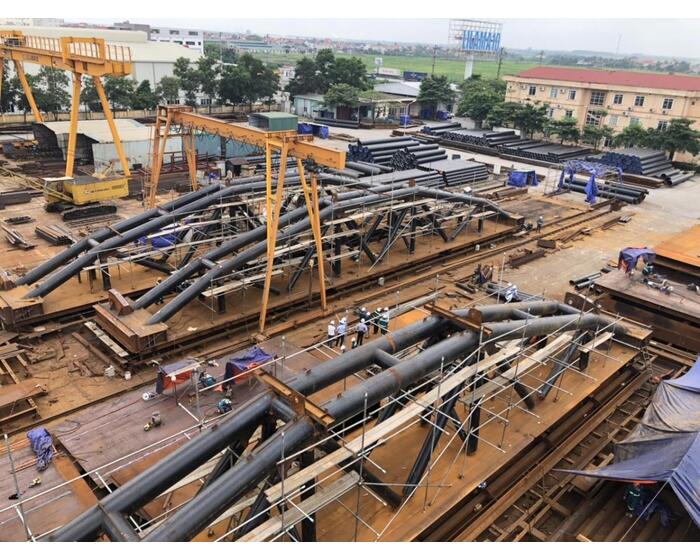
Fabrication of Irrigation System Radial Gates in Vietnam
Technical and Product Information Leveraging decades of expertise in welding and metal fabrication, our company provides high-quality radial gates for irrigation systems. We have a proven track record, including the supply of gates for Vietnam's largest irrigation project, the Cai Lon–Cai Be Irrigation Project. Supported by 398 skilled technicians and advanced equipment, we ensure a seamless process from design to final product completion. Key Features Proven experience in Vietnam's largest irrigation project (Cai Lon - Cai Be Irrigation Project). 398 skilled technicians proficient in welding processes guarantee high-quality outcomes. Extensive experience in fabricating thick plates and large-scale products. Optimal welding methods are proposed based on calculations and simulations from the design stage. Equipment Three-Roll Bending Machine (Italy): Capable of bending large-scale products. 50–600t Cranes: Ensures safe and efficient transport of large and heavy components during manufacturing. Surface Treatment: Shot blasting and anti-corrosion coatings for durability and extended product life. Welding Equipment: A diverse range, including TIG welders, MIG/MAG welders, automatic welding machines, and DC welding machines. Applications Irrigation Systems: Supports optimal water resource management by controlling water flow and discharge. Infrastructure Projects: Used in flood prevention infrastructure such as dams and reservoirs. Quality Assurance and Production System All projects undertaken by LILAMA10 adhere to ESHS standards. Certified for quality management of steel structures in compliance with European Standard EN 1090-EXC3 (CE marking). Welding quality certified under ISO 3834 standards. Completed Projects Cai Lon–Cai Be Irrigation System Project (Phase 1) The Phase I project, located in Kien Giang, involved a total investment of over VND 3,300 billion, with the Investment and Construction Management Board 10 as the main investor. Gate Specifications: - 8 gates: 40m wide x 9m high, weighing 203 tons each. - 2 gates: 40m wide x 7.5m high, weighing 188 tons each. - 1 gate: 40m wide x 6m high, weighing 155 tons. The installation was highly complex, conducted on rivers with strong currents and winds. Fixing, hoisting, and positioning each gate required 2–3 days before official installation. The project timeline was reduced from 36 months to 24 months due to the urgent need for saltwater intrusion prevention. This is the largest irrigation project in Vietnam by scale and water flow capacity, constructed on the Cai Lon River. Summary Our company provides ideal solutions for irrigation and infrastructure projects, backed by decades of welding expertise. We supplied a 40m-wide, 9m-high, 203-ton radial gate for Vietnam’s largest irrigation project, the Cai Lon–Cai Be Irrigation Project. Utilizing a team of 398 skilled technicians and state-of-the-art equipment, we ensure precise fabrication of large and thick components. Advanced equipment like three-roll bending machines and heavy-duty cranes support high-accuracy processing. For more details, download the PDF or feel free to contact us!
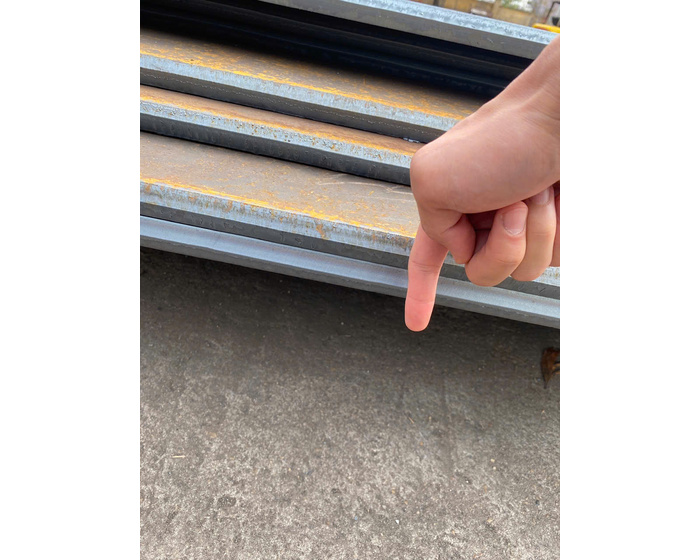
Comprehensive Solutions for Large, Thick Structural Fabrication at Vietnam's Factories
Thick plates and large fabricated components are produced by processing thick metal materials such as steel and stainless steel into parts for industrial machinery and structures. Particularly in large-scale infrastructure projects like hydropower plants, where high precision and strength are required, specialized expertise and advanced technologies play a critical role. The manufacturing process for these large fabricated components involves numerous stages, making efficient and integrated processes vital from the design phase to the finished product. Lilama offers a complete solution for large, thick mechanical components! With a team of 398 skilled welding technicians and modern equipment, we meet diverse demands, including those from hydropower plant projects. Key Features: - Streamlined Production Process: From design to finished product, we optimize work time to ensure high production efficiency and quick delivery. - Extensive Experience: Proven track record of handling large, thick component fabrication projects. - Highly Skilled Team: 398 expert technicians ensuring superior product quality. - Modern Equipment: - Italian 3-Roll Bending Machine: Suitable for processing thick plates. - Cranes (50–600 tons): Designed to lift and handle large structures. - Surface Treatment: Shot blasting, anti-corrosion coating, and enhanced product durability. - Welding Equipment: TIG welders, MIG/MAG welders, automatic welding machines, and electrode drying ovens. Production Process: We follow a streamlined production process through the following steps: 1. Planning and Design: Using advanced design software like AutoCAD, Tekla, and SolidWorks to ensure precise analysis and compliance with international standards (ASME, AISC, Eurocode) and domestic standards (TCVN). 2. Structural Fabrication: Employing CNC cutting machines, plasma cutters, hydraulic punches, Italian 3-roll bending machines, and welding equipment. 3. Surface Treatment: Shot blasting and anti-corrosion coating to increase durability and extend product lifespan. 4. Inspection and Acceptance: Thoroughly inspecting each weld and the entire product to meet international standards. 5. Transportation: Safely and efficiently transporting large and heavy products using cranes (50–600 tons). Our products are widely used in hydropower plant projects, construction structures, and industrial machinery. Quality Certifications and Production System: All LILAMA10 projects adhere to ESHS standards. We have achieved the following certifications: - Quality Management Certification: EN 1090-EXC3 (CE Marking) for steel structures. - Welding Quality Certification: ISO 3834 for internationally compliant welding processes. With a streamlined production process, LILAMA10 delivers high-quality, large, thick fabricated components suitable for various industries, including hydropower, construction, and industrial machinery. Our team of 398 skilled technicians, coupled with state-of-the-art facilities, ensures superior product quality, efficient production, and timely delivery.
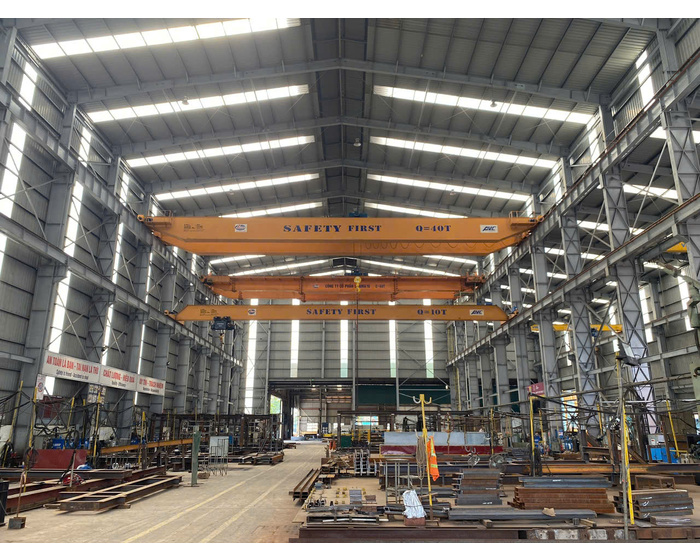
Steel Structure Fabrication at Large-Scale Facilities in Vietnam
With a total area exceeding 8 hectares and two factories located in Hải Dương and Phủ Lý, Lilama 10 is capable of handling large-scale orders for oversized structural components in significant quantities. Equipped with state-of-the-art facilities and a team of 398 skilled welding technicians, we ensure top-notch welding and assembly quality. Our flexibility enables us to meet a diverse range of customer requirements effectively. Key Features - Extensive Facilities: Two factories spanning over 8 hectares, capable of handling large-scale production. - Skilled Workforce: 398 experienced technicians specializing in welding processes ensure high-quality finishes. - Experience: Proven track record in manufacturing thick plates and large-diameter piping. - Advanced Equipment: - Italian-made three-roll bending machine, capable of bending ultra-thick plates up to 110mm. - 50–600-ton cranes, supporting the production of critical components and structures. - Optimized Processes: Calculations and simulations from the design stage to propose the most suitable welding methods for large products. Specifications In large-scale structural fabrication, precision welding and product durability are top priorities. Our advanced technology ensures compliance with stringent standards, leveraging precision simulations, welding techniques, and surface treatments. - Materials Supported: Iron (SS400), Stainless Steel (SUS303, SUS304), Aluminum (A5052), and others. - Quality Standards: Adherence to ESHS standards, EN 1090-EXC3, and ISO 3834-certified quality management systems. - Welding Equipment: TIG welders, MIG/MAG welders, automatic welding machines, and more. - Surface Treatment: Shot blasting and anti-corrosion coating for extended product longevity. Applications and Industries Fabricated components are utilized in the following industries: - Energy Sector: Structural components and equipment for thermal and hydroelectric power plants requiring large-diameter piping. - Construction Machinery: Durable structural components supporting heavy loads. - Chemical Plants: High-precision products, including tanks and piping, for specialized applications. Quality Assurance - Compliance: All LILAMA 10 projects apply ESHS standards. - Certifications: + EN 1090-EXC3 (CE Marking) for steel structure manufacturing quality control. + ISO 3834 for welding quality certification. Summary Our company boasts over 8 hectares of expansive facilities and a workforce of 398 skilled technicians to efficiently produce large fabricated components with exceptional assembly precision. Our products serve a wide range of industries, including energy, construction machinery, and chemical plants, under stringent quality control adhering to EN 1090-EXC3 and ISO 3834 standards. From design to production and surface treatment, we offer end-to-end solutions tailored to diverse customer requirements. For further details, please download our PDF or contact us directly.
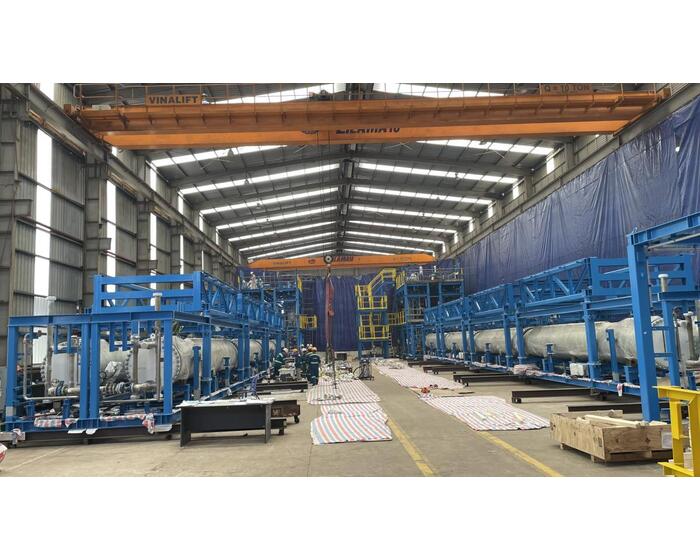
Fabrication of Electrolyzer Modules for Green Hydrogen Production Plants – Vietnam
Overview LILAMA 10 is responsible for the processing, manufacturing, assembly, and packaging of electrolyzer modules for green hydrogen production plants, including the "West Coast Project" (USA) and the "NEOM Hydrogen Project" (Saudi Arabia). These modules, incorporating thick plates and large-diameter piping, demand high assembly precision and long service life. Under a strict quality control system managed by 398 skilled welding technicians, we carry out the entire production process from design to manufacturing and surface treatment. Our ability to deliver custom, high-quality products tailored to client specifications is based on the following strengths: Key Features - A team of 398 experienced welding technicians capable of addressing all welding challenges. - Optimal welding methods proposed based on calculations and simulations from the design phase. - Extensive experience in manufacturing thick plates and large-diameter pipes. - Capable of handling large-scale projects using 50–250-ton cranes. - Supplying electrolyzer modules for the "West Coast Project" in the USA from Vietnam. - Supplying electrolyzer modules for the "NEOM Hydrogen Project" in Saudi Arabia from Vietnam. - Providing fabricated modules for advanced international projects. Technical Specifications - Welding Methods: TIG welding, MIG/MAG welding, DC welding, automatic welding. - Surface Treatment: Shot blasting and anti-corrosion painting for enhanced durability and longevity. Equipment - TIG welding machines, MIG/MAG welding machines, DC welding machines, automatic welding machines, and electrode drying cabinets. - 50–250-ton cranes for large-scale project requirements. Applications - Green Hydrogen Production Plants: Proven track record in projects such as the "West Coast Green Hydrogen Production Plant." Other Applications: - Energy Plants: Pressure- and durability-oriented piping and internal structures. - Chemical Plants: Meeting special requirements for thick, large-sized steel and precise welding. Quality Assurance and Production Standards - Compliance with ESHS standards across all LILAMA 10 projects. - Certified under EN 1090-EXC3 (CE Marking) for steel structure manufacturing quality. - Welding quality certified under ISO 3834 standards. Completed Projects - West Coast Green Hydrogen Production Plant (USA): One of the world’s largest and first hydrogen production plants, adopting new technology by Thyssenkrupp. This project required exceptional precision in fabrication and assembly, as well as stringent standards for equipment cleaning, storage, and packaging prior to shipment. Summary Hydrogen is becoming a globally sought-after clean energy source in the context of increasing tensions in the supply of natural gas. LILAMA 10 participates in major projects such as "West Coast" and "NEOM Hydrogen Project," providing electrolyzer modules that meet international standards with a closed-loop production process, skilled technicians, and modern equipment.
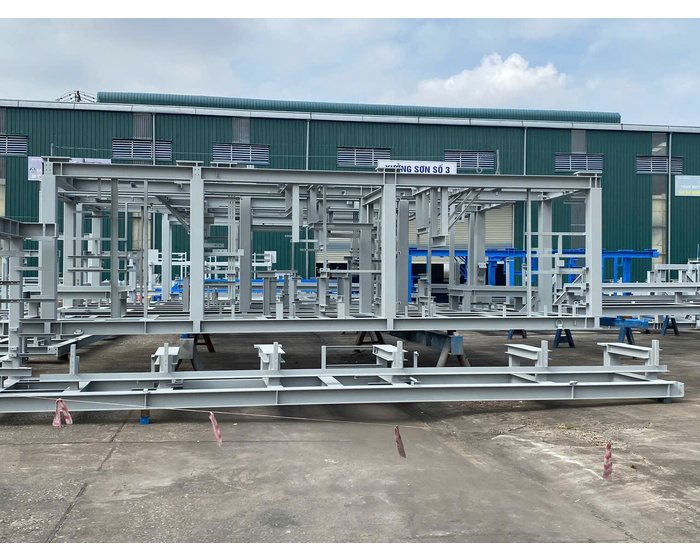
Advanced Welding Techniques for Large Fabrication - Prevent Crack
Welding cracks are one of the most common defects that occur during or after the welding process in large-scale fabrication. The main causes include residual stress, temperature changes, and chemical or mechanical factors. Such cracking can significantly compromise the quality, durability, and lifespan of large fabricated products. Leveraging extensive experience and advanced techniques in the large fabrication welding field, we provide high-quality welding solutions. To prevent weld cracking, we adopt the latest welding technologies and management practices. Features - A team of 398 skilled welding technicians capable of addressing diverse welding challenges. - Optimal welding methods proposed based on calculations and simulations from the design phase. - Extensive track record in manufacturing thick plates and large-diameter piping. - Capable of handling large-scale projects with 50-600 ton cranes. Specifications - Welding Methods: TIG welding, MIG/MAG welding, DC welding, and automatic welding. - Surface Treatment: Shot blasting, anti-corrosion paint. Equipment - TIG welding machines, MIG/MAG welding machines, DC welding machines, automatic welding machines, and electrode drying ovens. Quality Assurance and Production System - All projects adhere to ESHS standards. - Certified under the European Standard EN 1090-EXC3 (CE Marking) for steel structure manufacturing quality and ISO 3834 for welding quality assurance. Summary In large fabrication welding, issues such as residual stress and temperature changes can lead to weld cracking, impacting product quality and durability. Utilizing advanced techniques and extensive experience, we deliver high-quality welding solutions while preventing cracking. Our team of 398 skilled technicians ensures optimal welding methods through simulations at the design stage. With a proven track record in thick plate and large piping production, we are capable of handling large-scale projects using cranes with capacities of 50 to 600 tons. We offer diverse welding methods and material compatibility, with quality assured under ESHS standards.
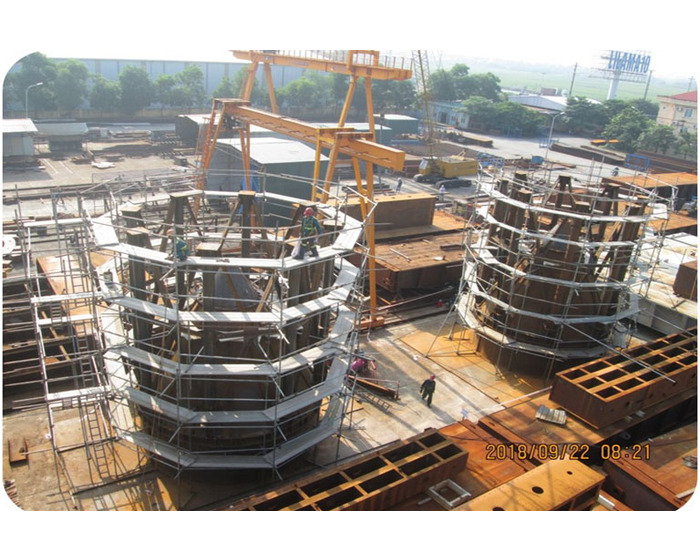
Oil Storage Tank - Manufactured in Vietnam
As a leading company in oil tank manufacturing, we ensure high-precision finishes through skilled technicians and advanced equipment. Oil tanks are containers used for storing petroleum and chemicals, requiring advanced welding techniques and surface treatments. Our company achieves high-quality manufacturing through specialized equipment for handling thick plate materials and skilled technicians. Additionally, by thoroughly conducting calculations and simulations from the design stage, we guarantee optimal dimensions and shapes to meet the diverse needs of our customers. Features - Thick, Large Steel Plate compatibility: Equipped with cranes handling up to 600 tons, capable of producing large tanks. - Bending Process: Precision bending for plates up to 110mm thick and 3m wide, using a three-roll plate bending machine from Italy. - Welding Expertise: A team of 398 certified welders ensures meticulous welding finishes. - High-Pressure Capability: Fabricates tanks with capacities up to 60,000 cubic meters for fuel, chemicals, and food applications. Specifications - Materials: Carbon steel, specialty alloy steel, stainless steel, and more to meet diverse requirements. - Plate Width: Up to 3m. - Size: No diameter limit for tanks. - Surface Treatment: Shot blasting and anti-corrosion paint, improving durability and corrosion resistance. Applications - Petrochemical Plants: Storage tanks for chemicals and crude oil. - Power Plants: Large storage tanks for fuel oil. - Food & Pharmaceutical Industries: Liquid storage tanks with specific corrosion resistance and cleanliness. - Transport & Logistics: Customizable mobile tanks compliant with road traffic regulations. Certifications & Standards - All projects comply with ESHS standards. - Certified under European Standard EN 1090-EXC3 (CE Marking) for steel structure manufacturing quality. - ISO 3834-certified for welding quality management. Summary Our oil tank manufacturing stands out for its high-precision processing techniques and rigorous quality control managed by skilled technicians. We possess top-tier competitiveness in handling thick plates and large tank production, serving industries such as energy, chemicals, and logistics. We are committed to providing flexible solutions tailored to customer needs and delivering long-lasting products. With two state-of-the-art factories located in Hai Duong Province and Phu Ly City, we have an annual production capacity of 17,000 tons. From design and manufacturing to construction, we offer comprehensive solutions for steel structures, large pressure tanks, and industrial equipment. The factories are equipped with advanced welding, cutting, processing, and painting technologies, ensuring high-quality products, competitive pricing, and impeccable service. For more details, please download the PDF or feel free to contact us!
CONTACT