SERVICE
Production Goods & Services
45hits
Narrow by category
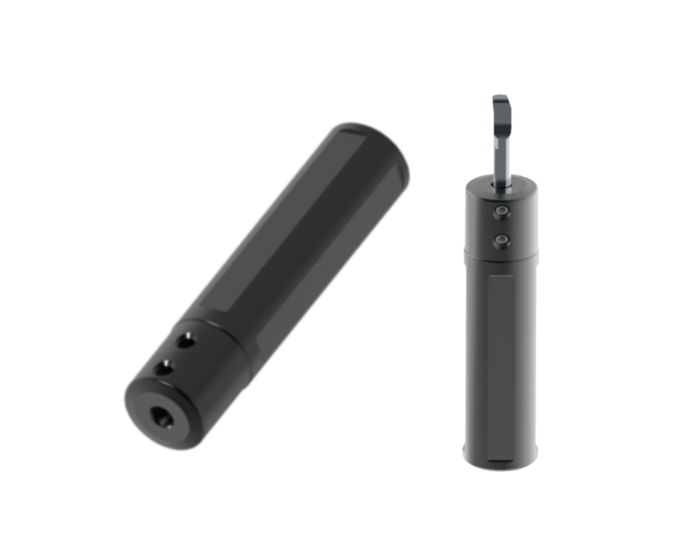
Micro-Mini Twin — The Ideal Tool for Small Part Processing
The Micro-Mini Twin model has been designed with 76 additional handle types suitable for internal turning and boring. The Micro-Mini Twin is a precision tool that provides a high-quality finish for turning or boring operations. It includes handles designed to be small, making it suitable for use with small machines or workpieces. ■ Features Designed with maximum machine suitability in mind, the Micro-Mini Twin reduces the need for cutting tools to be shortened and offers a variety of decimal-sized tools such as 2.5 mm, 3.5 mm, or 4.5 mm. It also enhances tool clamping precision by incorporating a square end at the inner tip for better tool positioning. ■ Technical Information Suitable for materials such as Stainless Steel SUS303, SUS304, or SUS4xx series, whether for automotive parts, molds, and especially small electronic components. MMC Hardmetal (Thailand) Co., Ltd.. is based in Bangkok, Thailand, and provides services throughout the country. ■ For more details, please download the PDF or feel free to contact us.
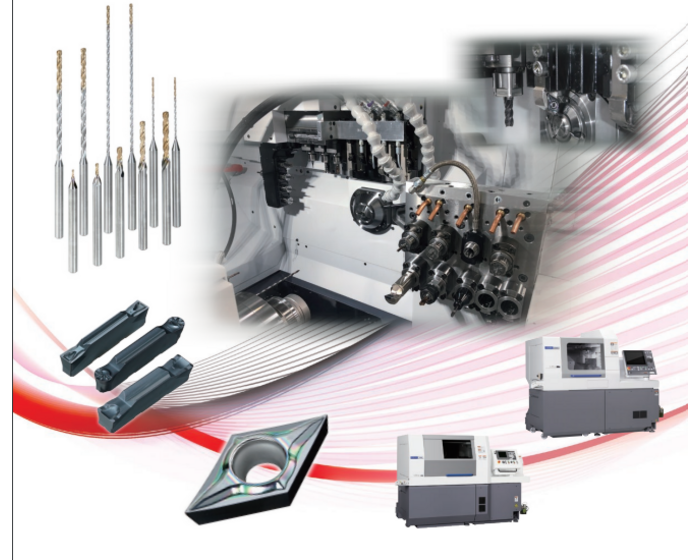
Low Frequency Vibration Cutting Technology LFV for Automatic Lathes Productivity and Quality
LFV technology optimizes chip management with low frequency vibration cutting, providing an innovative production solution for difficult materials and deep hole machining. ■ Overview "LFV (Low Frequency Vibration) Cutting Technology" involves applying fine vibrations to the tool during the cutting process to finely break up the chips, preventing them from tangling during machining. This technology enables deep hole drilling, threading, and precision machining of difficult materials, ensuring stable continuous processing on automatic lathes. It provides superior efficiency and high-quality finishes for precision and complex machining, such as automotive parts and small medical components. Support and product supply related to this technology are provided by MMC Hardmetal (Thailand) Co., Ltd. within Thailand. ■ Features - Efficient Chip Disposal: Finely breaks and efficiently ejects chips during cutting, preventing machine stoppages and damage to the machining surface. - Extended Tool Life: The vibrations during cutting reduce cutting resistance, leading to less wear on the tool and extending its life. - Capability for Difficult Materials: LFV technology is suitable for materials and shapes that are normally difficult to process, ideal for machining high-precision parts for medical and automotive applications. - Reduced Environmental Impact: The generated chips are shorter, making disposal and recycling easier and more environmentally friendly. ■ Specifications - Applicable Machines: Automatic lathes (e.g., CNC automatic lathes) - Vibration Modes: Three selectable vibration modes (set according to the degree of chip breakage and machining conditions) - Compatible Materials: General materials such as SUS304, S45C, and difficult-to-machine materials - Cutting Mode: Wet cutting (using oil) ■ Applications LFV technology is used in a wide range of fields, including automotive parts, small and precise medical devices, office equipment, and home appliance components. It is particularly suitable for operations prone to chip tangling, such as deep hole drilling, small diameter hole drilling, and threading. MMC Hardmetal (Thailand) Co., Ltd. provides products and support using LFV technology within Thailand, enabling high-efficiency and stable machining with the implementation of LFV technology. MMC Hardmetal (Thailand) Co., Ltd.. is based in Bangkok, Thailand, and provides services throughout the country. ■ For more details, please download the PDF or feel free to contact us.
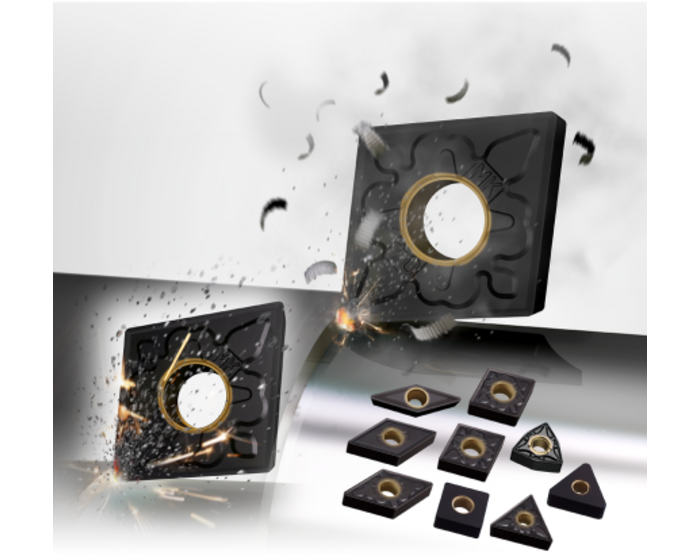
inserts carbide (Cutting tool) for Cast iron Series MC5100
An insert is a component of a cutting tool that can be replaced when worn or when it needs to be changed to suit different cutting tasks. Inserts are typically made from strong and durable materials such as carbide, cermet, or ceramic. Mitsubishi Materials' MC5100 Series is designed for precision cast iron machining, providing high wear resistance and excellent finish quality. ■ Overview Mitsubishi Materials' MC5100 Series is a CVD-coated carbide grade developed for cast iron turning. It is particularly suitable for machining cast iron and ductile cast iron, offering excellent wear resistance and chipping resistance for long-term stable machining. ■ Features - High wear resistance maintains performance under severe machining conditions. - Newly developed CVD coating enhances heat resistance and wear resistance. - Provides high stability, allowing for machining of complex shapes. - Applicable to various cast iron materials, offering a wide range of applications. ■ Specifications - Applicable materials: Cast iron, ductile cast iron - Main applications: Automotive parts, industrial machinery parts machining - Shapes: Turning inserts with various chip shapes and sizes available MMC Hardmetal (Thailand) Co., Ltd.. is based in Bangkok, Thailand, and provides services throughout the country. ■ For more details, please download the PDF or feel free to contact us.
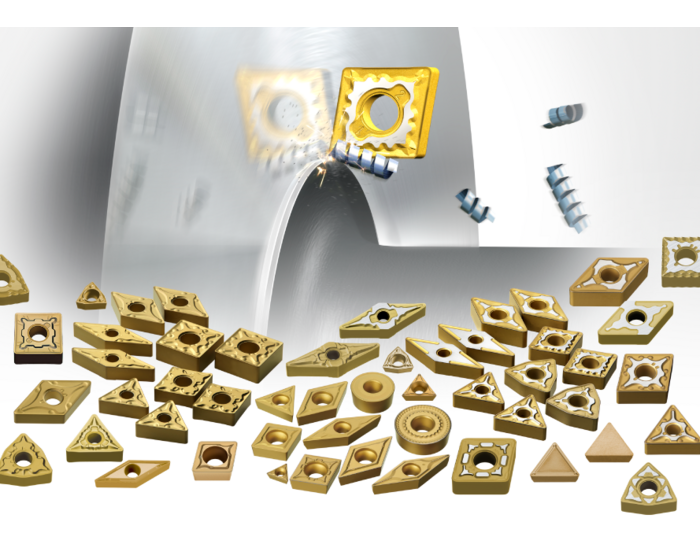
inserts carbide (Cutting tool) for ductile iron Series MC6100
An insert is a component of a cutting tool that can be replaced when worn or when it needs to be changed to suit different cutting tasks. Inserts are typically made from strong and durable materials such as carbide, cermet, or ceramic. Mitsubishi Materials' MC6100 Series prioritizes durability and cost performance in steel machining, supporting efficiency in manufacturing sites. ■ Overview Mitsubishi Materials' MC6100 Series is a CVD-coated carbide grade specialized for steel turning. It provides high wear resistance and heat shock resistance, enabling stable machining over long periods. This series caters to various machining conditions, from continuous to intermittent machining, meeting the diverse needs of the manufacturing industry. ■ Features - Enhanced wear resistance and heat shock resistance through high-quality CVD coating technology. - Multi-layer coating structure ensures longevity. - Available in three grades, MC6115, MC6125, and MC6135, optimized for different machining applications. - Utilizes crystal orientation control technology to maintain consistent performance. ■ Specifications - MC6115: Suitable for high-speed cutting - MC6125: Primary recommendation for steel turning - MC6135: Enhanced chipping resistance for steel turning MMC Hardmetal (Thailand) Co., Ltd.. is based in Bangkok, Thailand, and provides services throughout the country. ■ For more details, please download the PDF or feel free to contact us.
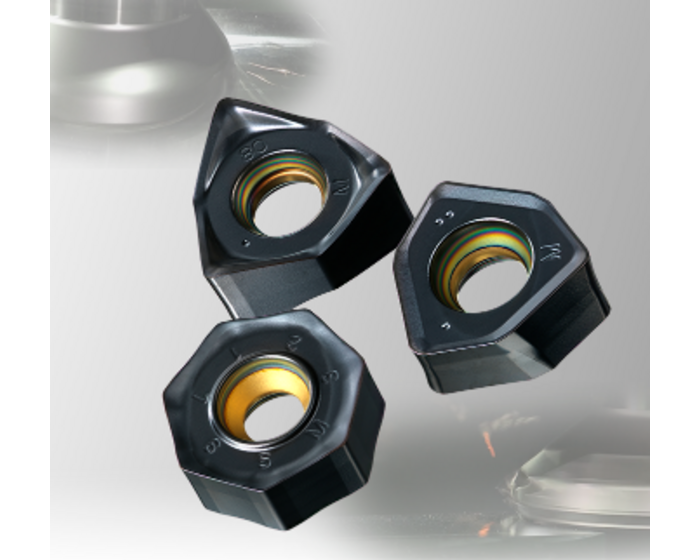
inserts carbide (Cutting tool) Series MV1000
An insert is a component of a cutting tool that can be replaced when worn or when it needs to be changed to suit different cutting tasks. Inserts are typically made from strong and durable materials such as carbide, cermet, or ceramic. Mitsubishi Materials' MV1000 Series achieves high-speed and efficient cutting. Durability is enhanced with the latest Al-rich coating technology. ■ Overview The MV1000 Series is a carbide insert specifically designed for machining steel and cast iron. This series is particularly suited for high-load machining conditions and offers high wear resistance and heat shock resistance due to the Al-rich coating. ■ Features - High wear resistance due to the latest Al-rich coating technology. - Consistent performance during high-speed machining. - Excellent heat shock resistance, ensuring stability under harsh cutting conditions. ■ Specifications - Applicable materials: Steel, cast iron - Recommended applications: High-speed, high-load machining - Cutting edge shapes and sizes: Various options available MMC Hardmetal (Thailand) Co., Ltd.. is based in Bangkok, Thailand, and provides services throughout the country. ■ For more details, please download the PDF or feel free to contact us.
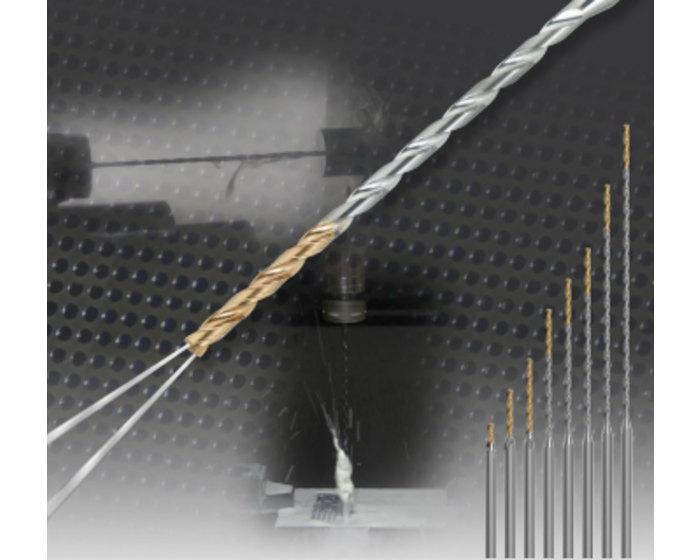
Drill bit Carbide (Cutting tool) Series DVAS
A drill bit is a cutting tool used for drilling holes in various materials such as wood, metal, plastic, or concrete. It has a long, cylindrical shape with cutting edges around the tip and along the shaft. The drill bit rotates at high speed to create holes in the material. There are many types and sizes of drill bits, depending on the application. Pursue ultimate precision and durability with Mitsubishi Materials' DVAS Series. With innovative materials and design, it supports high-performance hole machining. ■ Overview The DVAS Series is the latest lineup of high-performance solid drills, ideal for applications requiring high wear resistance and precise hole machining capabilities. This series combines advanced coating technology and cutting tool design, ensuring long life and high-quality machining. ■ Features - Large coolant holes provide excellent cooling effect, contributing to long tool life. - New technology coating offers high wear resistance and heat resistance. - Optimized blade geometry ensures ultimate precision and repeatability. ■ Specifications - Material: High-quality carbide - Applicable materials: Steel, stainless steel, cast iron, ductile iron, titanium, and other difficult-to-cut materials - Applications: Precision parts machining, automotive parts manufacturing, aerospace parts manufacturing MMC Hardmetal (Thailand) Co., Ltd.. is based in Bangkok, Thailand, and provides services throughout the country. ■ For more details, please download the PDF or feel free to contact us.
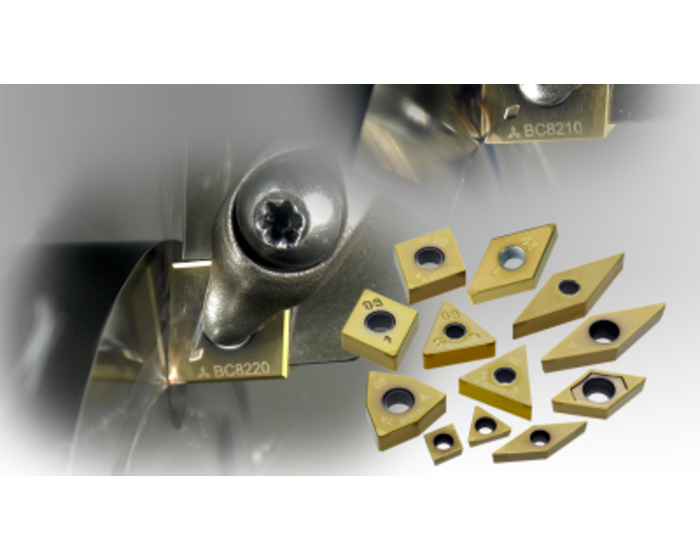
Inserts CBN Coated (Cubic Boron Nitride Coating) Cutting tool Series BC8200
An insert is a component of a cutting tool that can be replaced when worn or when it needs to be changed to suit different cutting tasks. Inserts are typically made from strong and durable materials such as carbide, cermet, or ceramic. Mitsubishi Materials' "BC8200 Series" coated CBN inserts for turning high-hardness steel. Advanced technology enhances wear resistance and machining precision, meeting the demands of manufacturers working with high-hardness materials. ■ Overview The BC8200 series is a CBN-coated grade designed specifically for turning high-hardness steel. Mitsubishi Materials' technological innovation ensures industry-leading durability and precision. It provides stable performance even under challenging machining conditions. ■ Features - Excellent wear resistance suited for high-hardness materials - Advanced cutting edge technology enables precision machining - Long-life design enhances continuous operational efficiency - Mitsubishi Materials' proprietary coating technology further enhances performance ■ Specifications - Material: Coated CBN - Applicable materials: High-hardness steel - Shape and dimensions: Various shapes based on industry standards - Recommended conditions: Optimized specifically for turning high-hardness steel The BC8200 series opens new possibilities in high-hardness steel machining, contributing to improved efficiency and quality in manufacturing. It is a reliable choice for industries demanding durability and precision machining. MMC Hardmetal (Thailand) Co., Ltd.. is based in Bangkok, Thailand, and provides services throughout the country. ■ For more details, please download the PDF or feel free to contact us.
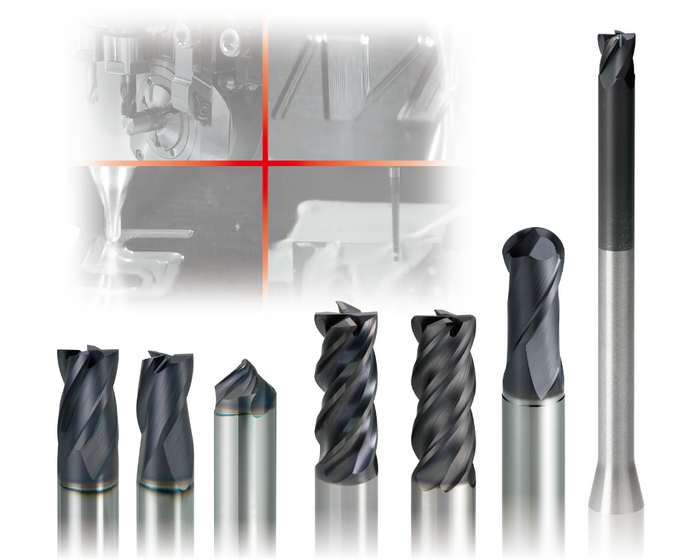
End mill carbide (Milling Processing) Cutting tool Series MS-PLUS
An end mill is a tool used in the milling process to create various shapes on a workpiece. It has a cylindrical shape with multiple cutting edges around the tip and sides. End mills are used to machine materials such as metal, wood, or plastic to create slots, cut edges, or surface finish on the workpiece. Enhance cutting efficiency and durability with the "MS-Plus End Mill" series, ushering in a new era for small lathe operations. ■ Overview Mitsubishi Materials' new "MS-Plus End Mill" series for automatic lathes is specifically designed for small lathes, offering advanced cutting performance and durability. These end mills are also capable of machining difficult-to-cut materials, meeting the growing demand in industries requiring precision machining. ■ Features - High cutting efficiency: Increased cutting speed significantly boosts productivity. - Excellent durability: Strength and hardness that withstand prolonged use. - Precision finishing: Enables meticulous machining that enhances the quality of final products. ■ Specifications - Material: Carbide with special coating - Shape: Specialized design for automatic lathes - Applicable materials: Steel, stainless steel, difficult-to-cut materials These end mills perform exceptionally well over extended periods of use. Mitsubishi Materials' "MS-Plus End Mill" series is the optimal choice for manufacturers seeking high reliability and efficiency. MMC Hardmetal (Thailand) Co., Ltd.. is based in Bangkok, Thailand, and provides services throughout the country. ■ For more details, please download the PDF or feel free to contact us.
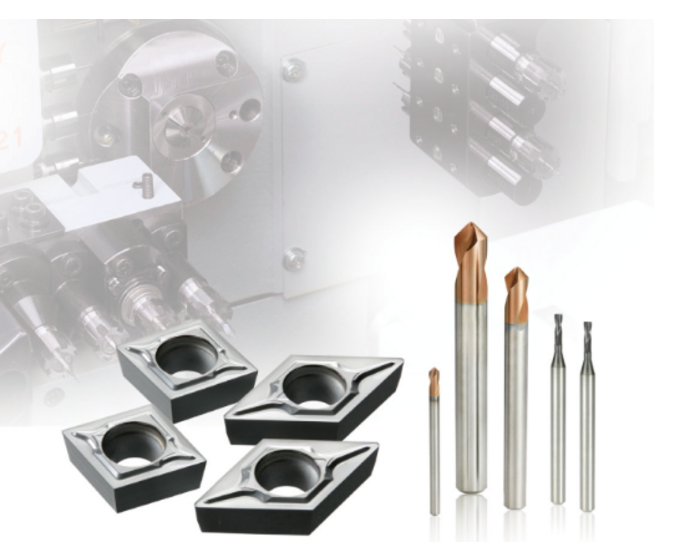
inserts carbide (Cutting tool) Series MS6015
An insert is a component of a cutting tool that can be replaced when worn or when it needs to be changed to suit different cutting tasks. Inserts are typically made from strong and durable materials such as carbide, cermet, or ceramic. Innovation for carbon steel machining, "MS6015". Supporting precision machining with coating technology that ensures long life through wear resistance. ■ Overview "MS6015" is a carbide coating grade specifically for carbon steel turning. Provided by Mitsubishi Materials, this grade achieves high wear resistance and long life, making it ideal for precision machining of industrial steel products. ■ Features - Excellent wear resistance: Suppresses wear over long-term use. - High cutting performance: Maintains stable machining quality. - Wide applicability: Suitable for various machining conditions of carbon steel. ■ Specifications - Material: Carbide with special coating - Application: General turning of carbon steel - Shape: Various shapes and sizes for turning operations "MS6015" delivers excellent results in carbon steel machining, contributing to improved productivity and quality in manufacturing. MMC Hardmetal (Thailand) Co., Ltd.. is based in Bangkok, Thailand, and provides services throughout the country. ■ For more details, please download the PDF or feel free to contact us.
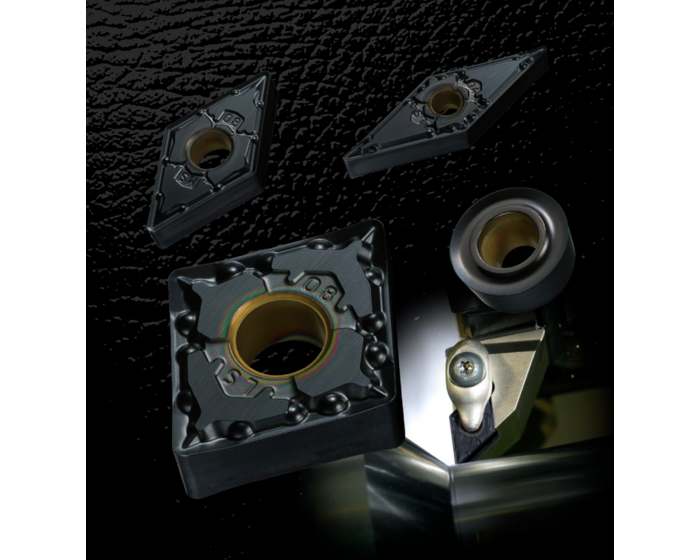
inserts carbide (Cutting tool) Series MV9005
An insert is a component of a cutting tool that can be replaced when worn or when it needs to be changed to suit different cutting tasks. Inserts are typically made from strong and durable materials such as carbide, cermet, or ceramic. Revolutionize the machining of super heat-resistant alloys with "MV9005". Achieve wear resistance and heat resistance with Mitsubishi Materials' cutting-edge technology. ■ Overview Mitsubishi Materials' "MV9005" is a high-performance coated carbide insert specifically suited for machining super heat-resistant alloys. This insert enhances the efficiency and quality of turning operations by providing high wear resistance and heat resistance. ■ Features - Excellent wear resistance: High durability to withstand long machining operations. - High heat resistance: Minimizes performance degradation at high temperatures. - Capable of high-speed machining: Ensures stable machining at fast feed rates. ■ Specifications - Material: Coated carbide - Target materials: Super heat-resistant alloys (such as Inconel 718) - Shape: Designed to accommodate various machining shapes "MV9005" enables high-quality machining required in the aerospace, medical, and automotive industries for super heat-resistant alloy processing. MMC Hardmetal (Thailand) Co., Ltd.. is based in Bangkok, Thailand, and provides services throughout the country. ■ For more details, please download the PDF or feel free to contact us.
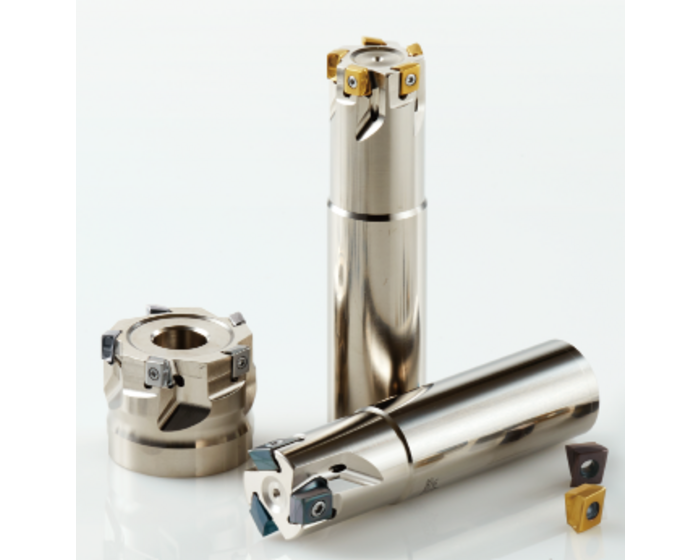
Inserts (Tangential insert) Cutting tool Series VPX
An insert is a component of a cutting tool that can be replaced when worn or when it needs to be changed to suit different cutting tasks. Inserts are typically made from strong and durable materials such as carbide, cermet, or ceramic. Mitsubishi Materials' VPX Series consistently handles complex machining with high precision. Its high rigidity design enables high-efficiency processing. ■ Overview The VPX Series is a vertical cutter that combines high rigidity and multifunctionality, especially suitable for high-load processing. This series provides consistent cutting performance and high precision, designed to meet the diverse needs of the manufacturing industry. ■ Features - High rigidity design ensures stability even under high-load processing. - Versatility for a wide range of processing applications. - Advanced technology implemented for high-precision machining. ■ Specifications - Material: Special alloy with excellent wear resistance and heat resistance. - Applications: Face milling, shoulder milling, slot milling, etc. - Shape: Various cutter shapes and sizes available. MMC Hardmetal (Thailand) Co., Ltd.. is based in Bangkok, Thailand, and provides services throughout the country. ■ For more details, please download the PDF or feel free to contact us.
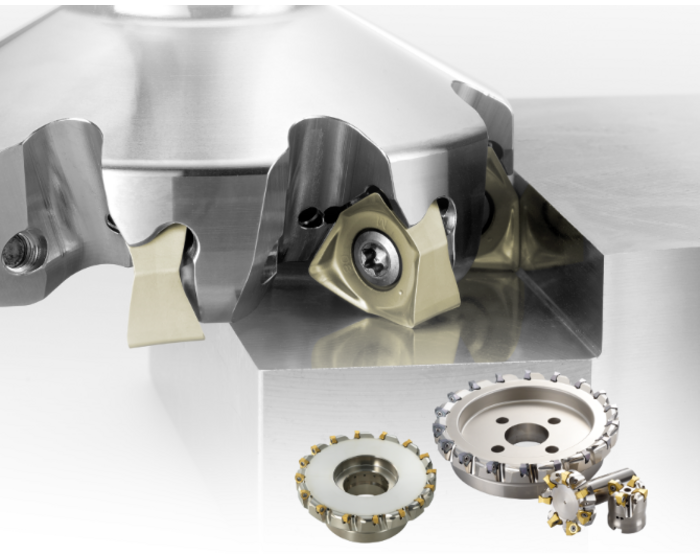
Milling inserts (Cutting tool) Series WWX
An insert is a component of a cutting tool that can be replaced when worn or when it needs to be changed to suit different cutting tasks. Inserts are typically made from strong and durable materials such as carbide, cermet, or ceramic. The innovative "WWX Series" with double-sided inserts achieves high rigidity and precision machining. It is a cost-effective shoulder cutter. ■ Overview The "WWX Series" is a shoulder cutter designed for high rigidity, using double-sided inserts. This series provides excellent chip evacuation and machining accuracy. ■ Features - High rigidity design: Structure withstands strong cutting forces. - Double-sided insert usage: Enhances cost efficiency and service life. - Excellent machining accuracy: Achieves high-quality surface finishes. ■ Specifications - Material: Wear-resistant carbide - Shape: Shoulder cutter with double-sided inserts - Applicable materials: Steel, stainless steel, cast iron, non-ferrous metals, heat-resistant alloys, titanium alloys, high-hardness steel The "WWx Series" is an optimal choice for manufacturers seeking high rigidity and excellent machining accuracy. MMC Hardmetal (Thailand) Co., Ltd.. is based in Bangkok, Thailand, and provides services throughout the country. ■ For more details, please download the PDF or feel free to contact us.
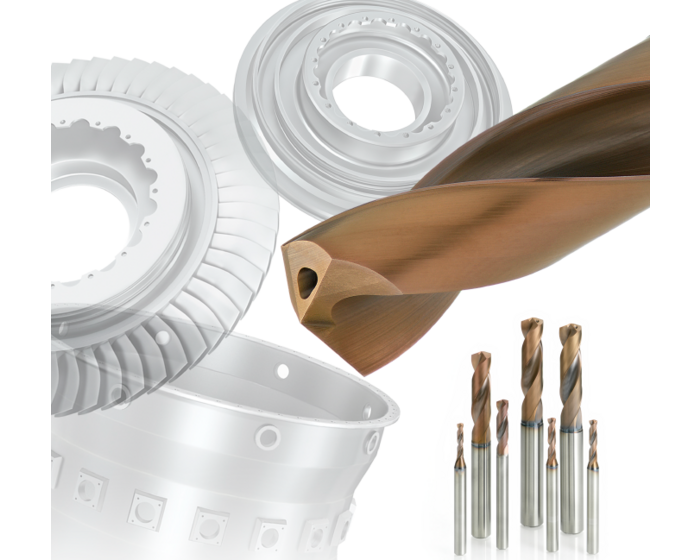
Drill (Drill tool) Cutting tool Series DSA
A drill bit is a cutting tool used for drilling holes in various materials such as wood, metal, plastic, or concrete. It has a long, cylindrical shape with cutting edges around the tip and along the shaft. The drill bit rotates at high speed to create holes in the material. There are many types and sizes of drill bits, depending on the application. Mitsubishi Materials' DSA Series offers high durability and superior cutting performance for machining super heat-resistant alloys. ■ Overview The DSA Series is a high-performance drill specifically aimed at super heat-resistant alloys, designed with enhanced wear resistance and improved machining speeds. Leveraging Mitsubishi Materials' technological expertise, it provides stable performance even under difficult machining conditions. ■ Features - Advanced wear resistance specialized for machining super heat-resistant alloys - Optimized cutting efficiency for high-speed machining - Advanced cutting edge design for high-precision drilling - Technological innovations maintain consistent quality and machining accuracy ■ Specifications - Material: Special carbide - Applicable materials: Super heat-resistant alloys - Shape: Solid drill The DSA Drill Series is suited for the challenging conditions of drilling super heat-resistant alloys, promising long-term stable performance. It is a reliable choice for machining super heat-resistant alloys. MMC Hardmetal (Thailand) Co., Ltd.. is based in Bangkok, Thailand, and provides services throughout the country. ■ For more details, please download the PDF or feel free to contact us.
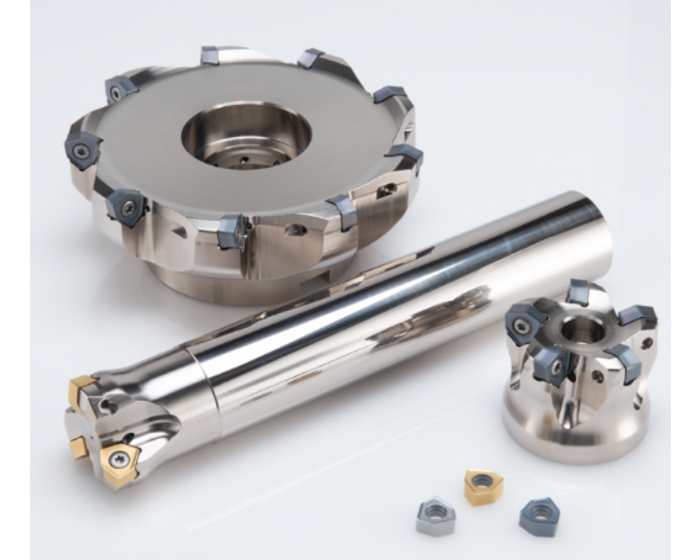
Face mill tool (milling tool) cutting tool Series WJX
A face mill is a cutting tool used in the manufacturing process of metal parts, especially for face milling the surface of a workpiece. This tool has a round shape and multiple cutting teeth mounted on its surface. These cutting teeth rotate around the axis of the tool during operation to remove material from the surface of the workpiece with each pass. Explore new frontiers in cutting with the "WJX Series" face mill. Achieve efficiency and precision simultaneously with high feed and deep cutting. ■ Overview The "WJX Series" is a face mill capable of high feed and deep cutting, providing consistent performance and excellent cutting efficiency. It is designed to meet diverse machining needs and is particularly suitable for processing large workpieces requiring high-efficiency machining. ■ Features - High feed capability: Significantly reduces machining time. - Deep cutting support: Ensures stability in deep cutting operations. - Universal use: Adaptable to various materials. ■ Specifications - Shape: Enhanced clamping mechanism - Material: Wear-resistant materials - Applicable materials: Steel, stainless steel, cast iron, titanium alloys, heat-resistant alloys, and high-hardness steel The "WJX Series" offers an optimal solution for modern manufacturing industries seeking high productivity. MMC Hardmetal (Thailand) Co., Ltd.. is based in Bangkok, Thailand, and provides services throughout the country. ■ For more details, please download the PDF or feel free to contact us.
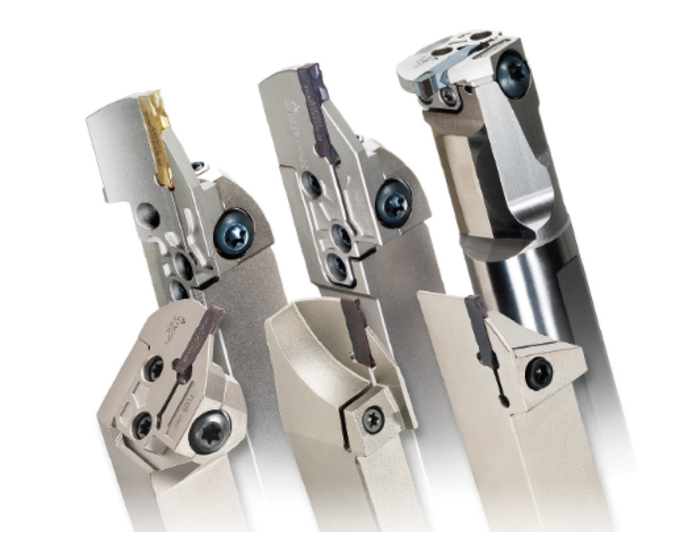
Grooving tools (Cutting tool) Series GY
A grooving tool is a tool used to create grooves or slots in various materials such as wood, metal, or plastic. Grooving can be done in multiple ways, depending on the application and the desired shape of the groove. Improve both cutting efficiency and product quality with Mitsubishi Materials' GY Series grooving tools. Ideal for all sites requiring precision machining. ■ Overview The GY Series grooving tools are high-performance cutting tools provided by Mitsubishi Materials, optimized especially for precise grooving operations and compatible with a variety of materials. ■ Features - Incorporates the latest coating technology, significantly improving wear resistance. - Unique clamping mechanism ensures tool rigidity and stability. - Suitable for a wide range of materials, from non-ferrous metals to high-hardness steel. ■ Specifications - Material: Carbide - Applicable materials: Steel, stainless steel, aluminum, etc. - Shapes: Available in various shapes and sizes The GY Series is an optimal choice for all industrial manufacturing sites seeking high-quality finishes. MMC Hardmetal (Thailand) Co., Ltd.. is based in Bangkok, Thailand, and provides services throughout the country. ■ For more details, please download the PDF or feel free to contact us.
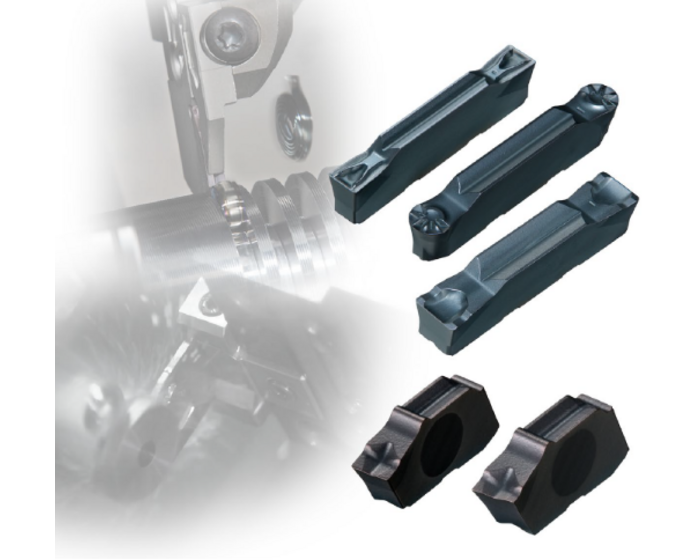
inserts carbide (Cutting tool) Series GY/GW
An insert is a component of a cutting tool that can be replaced when worn or when it needs to be changed to suit different cutting tasks. Inserts are typically made from strong and durable materials such as carbide, cermet, or ceramic. Explore new possibilities for low feed parting machining with Mitsubishi Materials' "GY/GW Inserts". Achieve stable processing and longevity. ■ Overview Mitsubishi Materials' "GY/GW Inserts" are specialized for parting machining at low feed rates, particularly praised for their performance in cutting high-hardness materials. ■ Features - Enhanced wear resistance suitable for high-hardness materials. - High dimensional accuracy for scenarios requiring precision machining. - Special edge design to reduce cutting resistance. ■ Specifications - Material: Carbide - Applicable materials: Steel, stainless steel, non-ferrous metals - Compatible machines: Various CNC lathes "GY/GW Inserts" are valued in industrial production for their high durability and efficient processing capabilities. MMC Hardmetal (Thailand) Co., Ltd.. is based in Bangkok, Thailand, and provides services throughout the country. ■ For more details, please download the PDF or feel free to contact us.
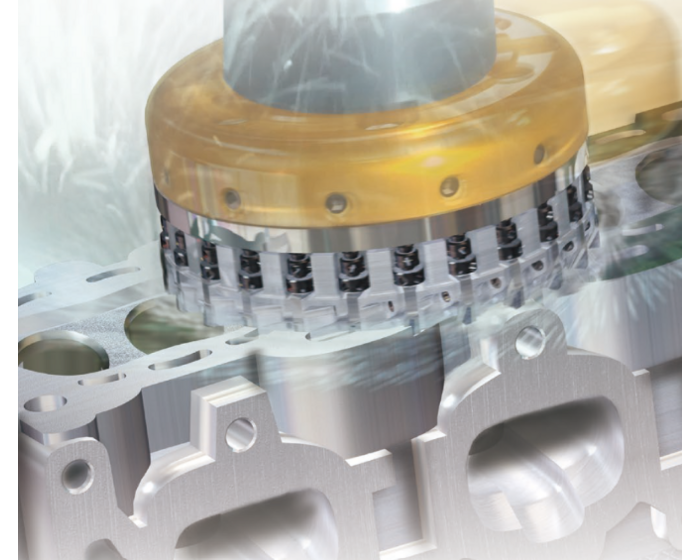
Face mill Cutter (Cutting tool) FMAX Series
A face mill is a cutting tool used in the manufacturing process of metal parts, especially for face milling the surface of a workpiece. This tool has a round shape and multiple cutting teeth mounted on its surface. These cutting teeth rotate around the axis of the tool during operation to remove material from the surface of the workpiece with each pass. Mitsubishi Materials' FMAX, a face mill that achieves high-speed and high-precision machining of aluminum alloys and cast iron, contributes to improved accuracy and efficiency. ■ Overview FMAX is a face milling cutter specialized for machining aluminum alloys and cast iron, offering high precision by Mitsubishi Materials. It is particularly capable of high-speed machining, contributing to increased machining efficiency and cost reduction. ■ Features - High rigidity design suppresses vibrations during high-speed machining. - Lightweight body enhances operability and reduces load on the machine. - Allows for precise cutting, minimizing surface roughness. ■ Specifications - Applicable materials: Aluminum alloys, cast iron - Cutting speed: Up to 200 m/min - Number of cutters: 6 to 16 The versatile FMAX is ideal for the manufacture of automotive industry parts. Chosen by many manufacturers for its reliable performance and efficiency. MMC Hardmetal (Thailand) Co., Ltd.. is based in Bangkok, Thailand, and provides services throughout the country. ■ For more details, please download the PDF or feel free to contact us.
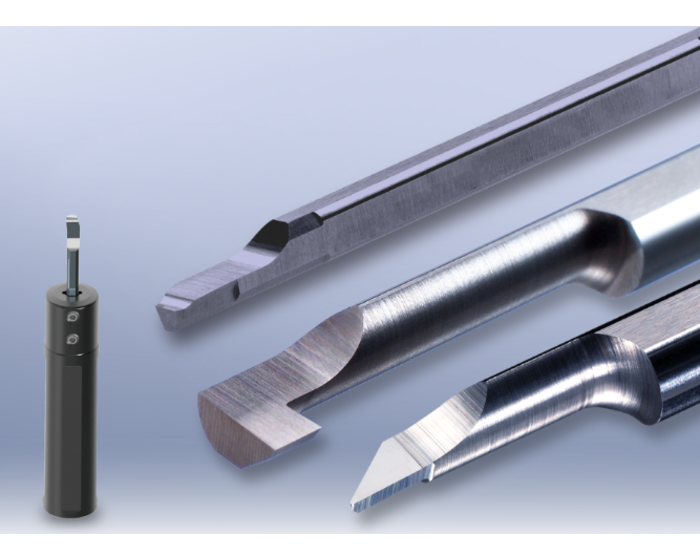
Reamer Carbide (boring tool) Series Micro-Mini Twin / Sticky Twin
A reamer is a tool used to enlarge or adjust the size of an existing hole to achieve the desired size and smoothness. Typically, a reamer is used after drilling to ensure the hole is precise and has a smooth surface. High-precision reaming with the new Micro-Mini Twin maximizes the efficiency of machining small parts. Explore new frontiers in internal machining with "Sticky Twin." Achieve high precision and efficient machining of small diameter parts. ■ Overview "Sticky Twin" is a tool that enables high-precision small diameter internal machining, particularly suitable for precise part manufacturing. This tool is optimized for working in tight spaces and ensures excellent machining quality. ■ Features - High-precision machining: Enables meticulous dimensional control. - High efficiency: Reduces working time. - Broad applicability: Compatible with a variety of materials. ■ Specifications - Material: High-quality carbide - Target parts: Small precision parts - Compatible machines: Versatile for use with multiple machine types "Sticky Twin" brings innovation to the internal machining of small and precise parts, contributing to the efficiency of the manufacturing industry. MMC Hardmetal (Thailand) Co., Ltd.. is based in Bangkok, Thailand, and provides services throughout the country. ■ For more details, please download the PDF or feel free to contact us.
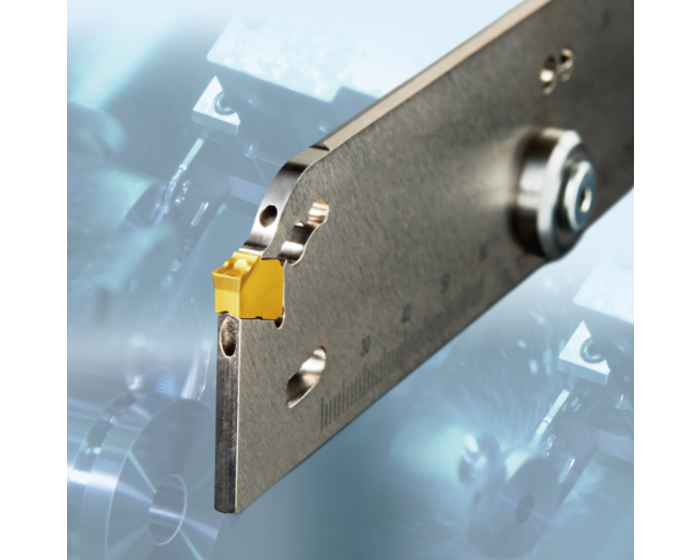
Grooving tools (Cutting tool) Series GW
A grooving tool is a tool used to create grooves or slots in various materials such as wood, metal, or plastic. Grooving can be done in multiple ways, depending on the application and the desired shape of the groove. The "GW Series" plate bite sets a new standard in the cutting industry. Mitsubishi Materials offers high reliability and technological innovation to optimize all cutting operations. ■ Overview The "GW Series" plate bite is a high-performance cutting tool newly provided by Mitsubishi Materials. It is especially known for its high wear resistance and durability, suitable for long-term operation. ■ Features - Advanced clamping mechanism achieves excellent holding power and precision. - Applied advanced coating technology enhances cutting speed and finish quality. - Unique design allows for internal coolant supply, greatly improving chip removal efficiency. ■ Specifications - Material: Carbide - Applicable processing materials: From general steel to hard-to-cut materials - Shape & Size: A wide range of options to meet various machining demands The "GW Series" plate bite aims to improve efficiency and quality in cutting operations, proposing a new standard for the industry. For more details, please download the PDF or feel free to contact us. MMC Hardmetal (Thailand) Co., Ltd.. is based in Bangkok, Thailand, and provides services throughout the country. ■ For more details, please download the PDF or feel free to contact us.
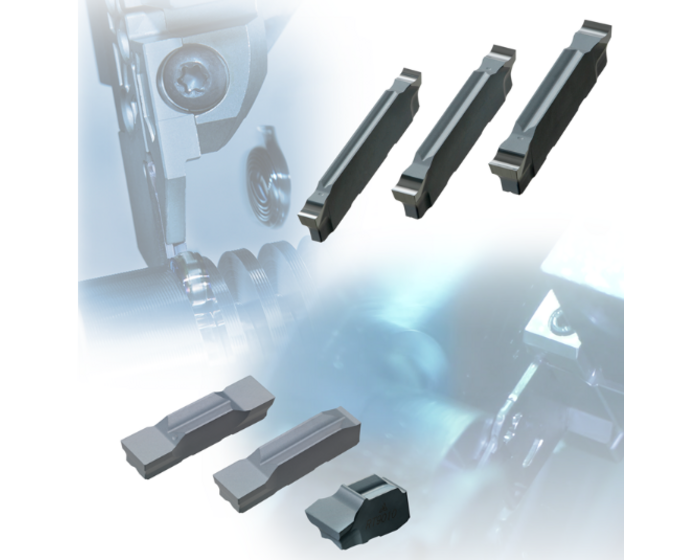
Grooving tools (Cutting tool) Series GL
A grooving tool is a tool used to create grooves or slots in various materials such as wood, metal, or plastic. Grooving can be done in multiple ways, depending on the application and the desired shape of the groove. Mitsubishi Materials' "GL Breaker" insert is a reliable choice for improving efficiency and quality in grooving operations. It achieves efficient machining. ■ Overview The "GL Breaker" insert from Mitsubishi Materials is a tool for grooving that plays a crucial role in the manufacturing process of industrial products. It exhibits high performance, particularly in machining hard-to-cut materials, and is increasingly demanded in the manufacturing industry. ■ Features - Offers high wear resistance, allowing for long-term use. - Improved cutting speeds thanks to unique coating technology. - Designed to enhance precision in grooving operations. ■ Specifications - Material: Carbide - Applicable materials: Steel, stainless steel, non-ferrous metals - Shape and dimensions: Various specifications available, allowing for selection according to application. The "GL Breaker" insert is an ideal choice for manufacturing sites seeking precision and efficiency in grooving operations. MMC Hardmetal (Thailand) Co., Ltd.. is based in Bangkok, Thailand, and provides services throughout the country. ■ For more details, please download the PDF or feel free to contact us.
CONTACT