PRODUCTS
技術・製品情報
技術・製品情報
6件
業界カテゴリで絞る
素材カテゴリで絞る
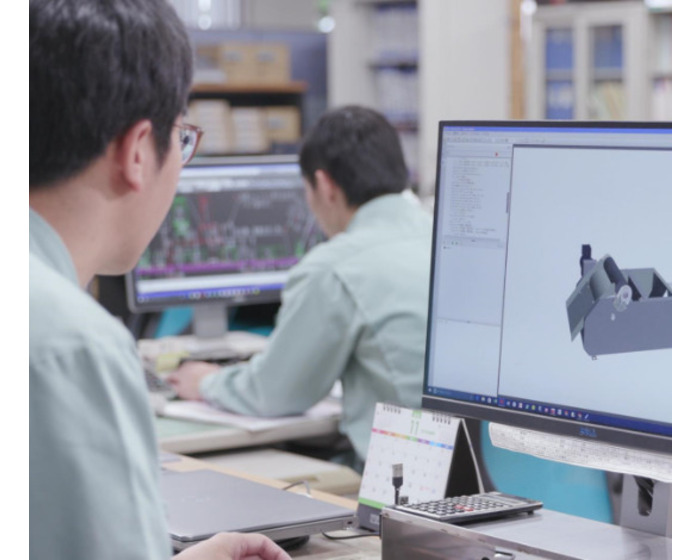
ブンリ製品によるランニングコスト削減とCO2排出量低減の実績
ブンリ製品は経済性と環境負荷の低減を実現し、導入後1年で投資分の回収が可能な高い費用対効果を提供します。これにより、生産現場でのランニングコストの削減に大きく貢献すると同時に、CO2排出量の低減を通じた環境保全にも貢献します。 ■ ランニングコスト削減の具体例 ランニングコストの削減により、1年間で次のような節約が見込めます: ・ ペーパーフィルター使用の場合: 約¥963,200の削減 ・ オートニックス使用の場合: 約¥1,103,400の削減 ・ ジェネックスマシン使用の場合: 約¥648,000の削減 ・ マシニングセンタ使用の場合: 約¥559,520の削減 ・ ガントリーミシン使用の場合: 約¥2,578,120の削減 ・ 倣い盤使用の場合: 約¥878,400の削減 長期的な削減効果(10年間)では、さらに顕著な経済効果が見込めます: ・ ペーパーフィルター使用の場合: 約¥9,632,000の削減 ・ オートニックス使用の場合: 約¥11,034,000の削減 ・ ジェネックスマシン使用の場合: 約¥6,480,000の削減 ・ マシニングセンタ使用の場合: 約¥5,595,200の削減 ・ ガントリーミシン使用の場合: 約¥25,781,200の削減 ・ 倣い盤使用の場合: 約¥8,784,000の削減 ブンリ製品の導入は、即座に経済性を高めるだけでなく、長期にわたって継続的なコスト削減を実現し、企業の競争力を高める重要な投資です。詳細はお問合せください。
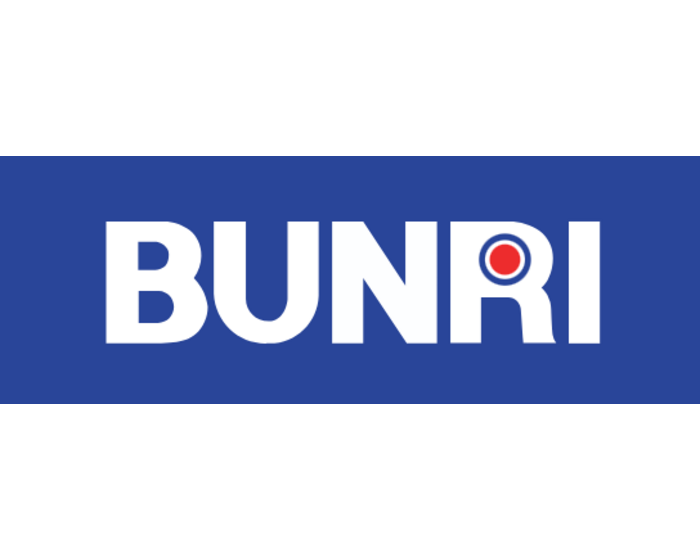
導入効果:ブンリ製品によるCO2排出量の低減
ブンリ製品の導入は、ランニングコストを大幅に削減し、CO2排出量を著しく低減させることで、企業の経済的および環境的持続可能性を実現します。当社の製品は1年間で、そして10年間という長期にわたって、コストと炭素排出の削減に効果的です。 ■ CO2排出量の低減 各製品のCO2削減量(1年間): ・ マグネティックドラムシステム M100:削減量 4,200kg ・ 倣い用精密研磨機用クーラントシステム RTG:削減量 7,561kg ・ 超精密研磨用クーラントシステム SB Filter YAO:削減量 3,318kg ・ サイクロンフィルターアポロS(APS):削減量 5,005kg 各製品のCO2削減量(10年間): ・ マグネティックドラムシステム M100:削減量 42,000kg ・ 倣い用精密研磨機用クーラントシステム RTG:削減量 75,610kg ・ 超精密研磨用クーラントシステム SB Filter YAO:削減量 33,180kg ・ サイクロンフィルターアポロS(APS):削減量 50,050kg ブンリの製品を導入することで、すぐにランニングコストの削減を実感できると同時に、地球温暖化対策において企業が前向きに貢献していることを示す重要なステップとなります。脱炭素・カーボンニュートラルを目指す世界的な動きの中で、私たちの製品がその目標達成に寄与します。 詳細はお問い合わせいただくか、ウェブサイトの資料をダウンロードしてご覧ください。
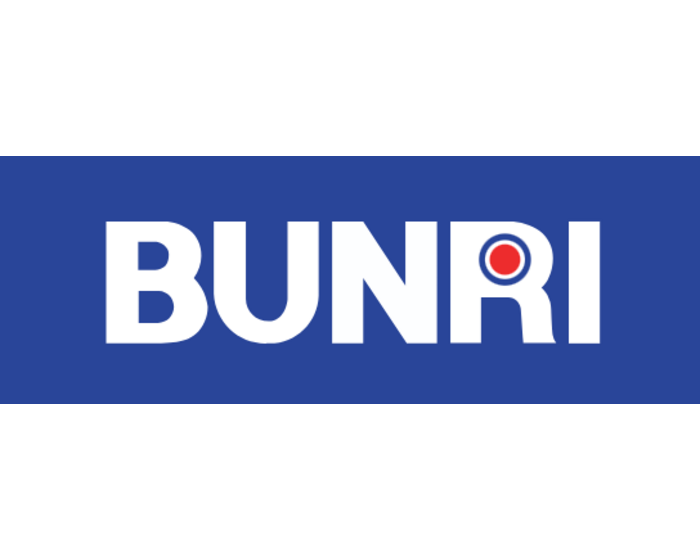
ブンリのチェーンバケットスキマー「CBS」導入事例:自動車部品メーカーのクーラント管理改善
■ 導入内容 ・クーラント種類:水溶性 ・分類:非磁性体 浮上油・スカム ・加工内容:切削 ・ワーク材質:アルミ ・切粉の形状:非磁性体による切削切粉 ・工作機械:マシニングセンタ ■ 導入前の課題 自動車部品メーカーでは、ベルト式オイルスキマーを用いたクーラント清浄化を行っていましたが、次の課題がありました: ・ベルトの損耗問題:頻繁にベルトが劣化・断裂し、清浄化機能が低下。 ・清浄化作業の非効率:機能低下が原因で作業効率が悪化し、定期的な修理が必要。 これらの課題は、クーラントの清浄度維持において障害となり、生産プロセス全体の効率に影響を与えていました。 ■ 導入後の効果 チェーンバケットスキマー「CBS」を導入することで、以下の成果が得られました: ・油の回収効率の向上 バケット式の独自設計により、従来のベルト式スキマーと比較して高い油回収効率を実現。 ・メンテナンスの簡素化 ベルトの劣化や断裂がなくなり、保守作業が大幅に軽減。 ・継続的な稼働確保 効率的な油回収により、クーラントの清浄度が向上。これが工作機械の安定稼働を支え、生産効率向上に直結。 自動車部品メーカーの事例は、チェーンバケットスキマー「CBS」が高い油回収性能とメンテナンスのしやすさを通じて、クーラント管理に新たな価値をもたらすことを示しています。生産現場の効率化とランニングコスト削減を両立させる製品として、多様な産業分野での活用が期待されます。 詳細はPDFをダウンロードしていただくか、お気軽にお問合せください。
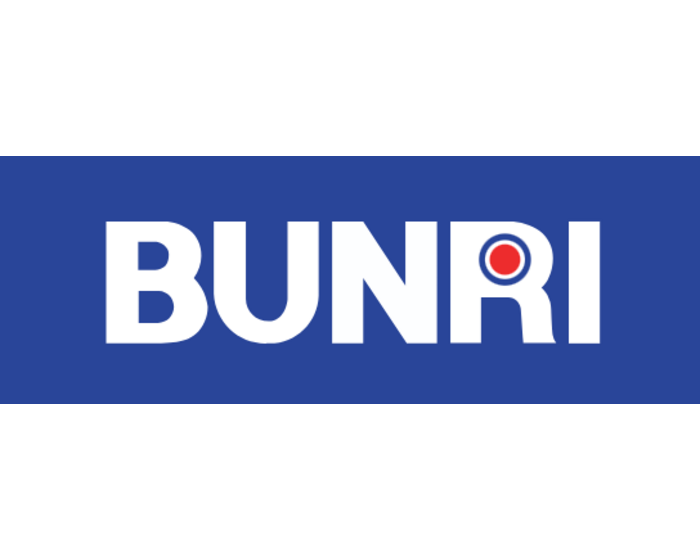
研削用「コンパクト」クーラントシステム導入事例:特殊鋼加工メーカーの効率向上
■ 導入内容の概要 特殊鋼加工メーカーにおいて、バッグフィルターに代わる効率的なソリューションとして、「コンパクト」クーラントシステムが採用されました。このシステムは水溶性クーラントを用いた非磁性体の研削に特化しており、アルミ、ステンレス、チタンなど多様な材質のワークに適応しています。 ■ 導入前の課題 バッグフィルターは200μmの研削スラッジを回収するのみであり、目詰まりにより頻繁な交換が必要でした。また、より細かなスラッジはタンクの底に溜まり、定期的な清掃が必要でした。 ■ 導入後の効果 新しいクーラントシステムの導入により、以下の効果が得られました: ・ バッグフィルターの定期交換が不要になり、ランニングコストの削減とメンテナンス作業の軽減が実現しました。 ・ システムが細かいスラッジも効果的に回収することで、クーラントタンク内の清掃頻度と労力が大幅に減少しました。
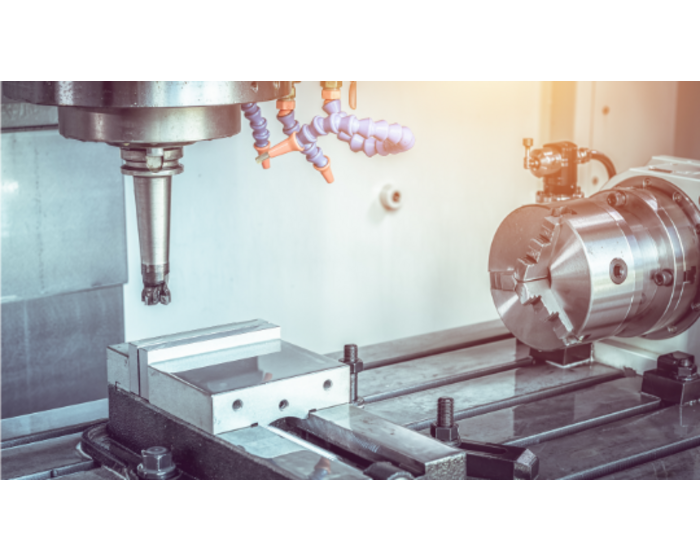
切粉トラブル防止の切削加工テクニック
「切粉による加工不良を未然に防ぎ、高精度加工を実現するためのポイントを紹介」 切削加工において、切粉は避けて通れない問題です。切粉が適切に排出されない場合、加工不良や工具損傷の原因となり得ます。ここでは、切粉による加工トラブルを防ぐための基本的な知識と対策方法について解説します。 ■ 概要 切粉は、加工方法やワーク材質によってその形状や色が変わります。理想的な切粉は「流れ形」とされ、表面が滑らかで連続しています。一方で、せん断形やむしれ形の切粉は、加工品質の低下を示唆しています。切粉の色や長さも加工の良し悪しを判断する重要な手がかりとなります。 切粉によるトラブルには、工具やワークへの巻きつき、切粉詰まりによるドリル折損などがあります。これらを防ぐためには、工具の選定、切削条件の調整、クーラント処理の最適化などが必要です。 ■ 対策 切粉対策には、チップブレーカ付きの工具の使用や切削パスの工夫が有効です。また、高圧クーラントによる切粉の洗い流しや、切削条件(主軸の回転数、送り速度、切り込み量)の調整による対策があります。これらの方法を適切に組み合わせることで、切粉による加工不良を効果的に防ぐことが可能です。 加工現場での切粉対策は、生産性向上と高品質な製品製造に直結します。切粉のコントロールにより、加工不良のリスクを最小限に抑え、効率的な生産プロセスを実現することができます。 ブンリでは各工場に適したクーラント処理システムをご紹介できます。 詳細はPDFをダウンロードしていただくか、お気軽にお問合せください。
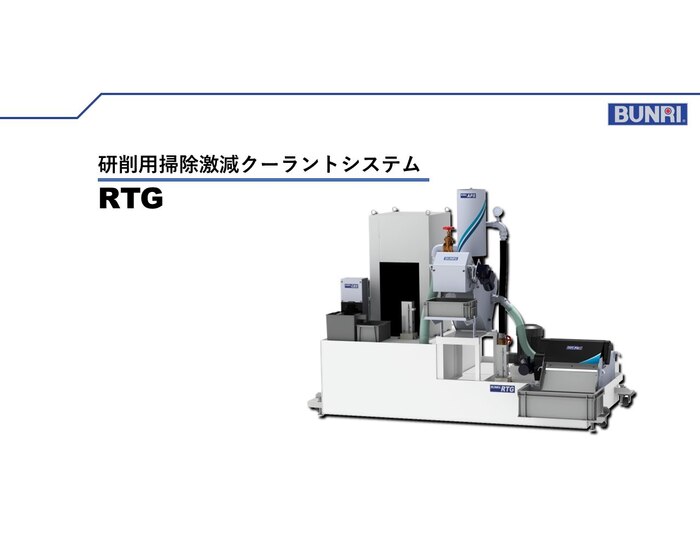
加工品質向上の秘訣!クーラントシステムの選び方と活用法
「切削工程の効率化を実現!高性能クーラント処理システムの紹介」 切削加工におけるクーラント処理システムは、工具の冷却と切粉の除去を効率的に行うために不可欠です。ここでは、クーラント処理システムが切削効率の向上にどのように寄与するかを解説し、高性能なシステム選定のポイントを紹介します。 ■ 概要 クーラント処理システムの主な特長は、工具の冷却効果の最大化と切粉の迅速な除去です。これにより、工具の耐久性が向上し、加工品質の安定化が期待できます。また、切粉の効率的な除去は、作業環境の改善にも寄与し、作業効率の向上にもつながります。さらに、最適なクーラント処理システムを選定することで、切削液の使用量を削減し、環境への影響を低減することも可能です。 ■ 求められる高性能クーラント処理システムの特徴 ・強力な冷却能力: 切削工具を効果的に冷却し、熱による損傷や摩耗を抑制します。 ・切粉の効率的な排出: 切粉が工具やワークに巻きつくのを防ぎ、加工精度の向上に寄与します。 ・環境への配慮: 使用する切削液の量を最適化し、廃液の処理にも配慮した設計です。 ・メンテナンスの容易さ: 定期的なメンテナンスが容易で、システムの長期的な運用を支えます。 これらの要素を備えたクーラント処理システムを選定することで、切削加工の効率と品質の両方を高めることができます。 ブンリでは各工場に適したクーラント処理システムをご紹介できます。 詳細はPDFをダウンロードしていただくか、お気軽にお問合せください。
CONTACT
お問い合わせ