PRODUCTS
Technology / product information
29hits
Narrow by Industry Category
Narrow by material Category
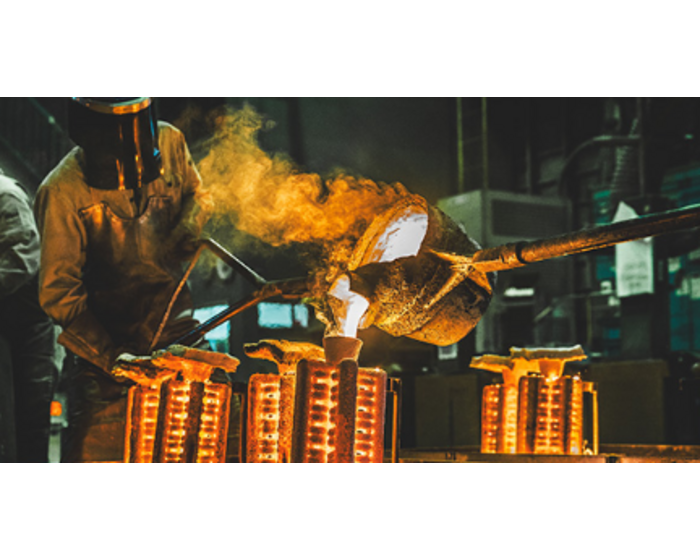
Lost-Wax Casting Technology: Innovation in Industrial Component Manufacturing
Lost-wax casting technology is a precision manufacturing method that involves pouring molten metal into molds to produce highly accurate components with complex shapes. Also known as investment casting, this technique is widely employed across industries such as automotive, medical, aerospace, and industrial machinery to create high-quality parts. At Castem, our lost-wax casting technology is supported by an integrated production system, from mold design to final products, ensuring reliability and cost efficiency to meet the demands of customers seeking high-precision metal processing solutions. ■ Key Features Ability to produce complex shapes: Lost-wax casting allows for the faithful reproduction of intricate designs and shapes that are challenging with conventional machining methods. High dimensional accuracy: Achieves dimensional precision of up to ±0.1mm, minimizing post-processing requirements and reducing finishing costs. Material versatility: Compatible with various metals, including stainless steel, carbon steel, and copper alloys, enabling material selection tailored to specific product requirements. Scalability: Flexible production capabilities ranging from prototypes and small batches to mass production. Enhanced surface finishing: Produces smooth surfaces, reducing the need for extensive finishing work. ■ Capabilities Dimensional range: Supports small to medium-sized parts while maintaining precision. Production volumes: Accommodates small-lot production to mass production of tens of thousands of pieces, offering manufacturing flexibility. Material compatibility: Works with a diverse range of materials such as iron-based alloys, copper-based alloys, aluminum alloys, and stainless steel. Surface roughness: Provides smooth finishes, minimizing the need for additional polishing and reducing costs. ■ Materials Carbon steel - S25C, S45C Chromium molybdenum steel - SCM415, SCM435, SCM440 Nickel chromium steel - SNC415, SNC815 Nickel chromium-molybdenum steel - SNCM220, SNCM439, SNCM616 Tool steel - SK105, SKS3, SKD11, SK85, SKD61 High-speed steel - SKH51, SKH57 Austenitic stainless steel - SCS13 (SUS304), SCS14 (SUS316), SUS303, SCS19 (SUS304L), SCS16 (SUS316L), SCS18 (SUS310S), SUSXM15J1 Martensitic stainless steel - SCS1 (SUS410), SCS2 (SUS420J1), SCS2A (SUS420J2), SUS440C Precipitation hardening stainless steel - SCS24(SUS630) Ferritic stainless steel - SUS430 Duplex stainless steel - SCS11(SUS329J1) Heat-resistant steel - SCH13, SCH21, SCH22 Special steel - SUJ2, SUP10, SUM23 Cast iron - FC200, FCD500 Aluminum alloy - AC4C, AC7A Copper alloy - CAC102 (pure copper), CAC302 (HBsC2), CAC403 (BC3), CAC703 (ALBC3), CAC802 (SzBC2), CAC502A (PBC2), CAC203 (YBs C3), CrCu (chromium copper) Cobalt alloy - Stellite 12 ■ Case Studies Automotive Components: Proven track record in engine parts, drivetrain components, and exhaust system parts, where precise designs and high durability are essential. Medical Device Components: Used in surgical instruments and precision medical equipment requiring high accuracy and biocompatibility. Industrial Machinery Components: Enables the production of complex and durable parts for conveyor systems and precision machinery. ■ Applications This versatile technology supports the manufacturing of automotive parts, engine components, drivetrain parts, medical devices, industrial machinery parts, as well as components for electronics and precision instruments. Lost-wax casting is a highly effective method for producing complex, high-precision metal parts, addressing a wide range of metalworking needs. It delivers quality and reliability, ensuring customer satisfaction and trust. CASTEM (SIAM) CO., LTD. is located in Chonburi Province, Thailand, and provides services nationwide. ■ For more details, please download PDF or feel free to contact us.
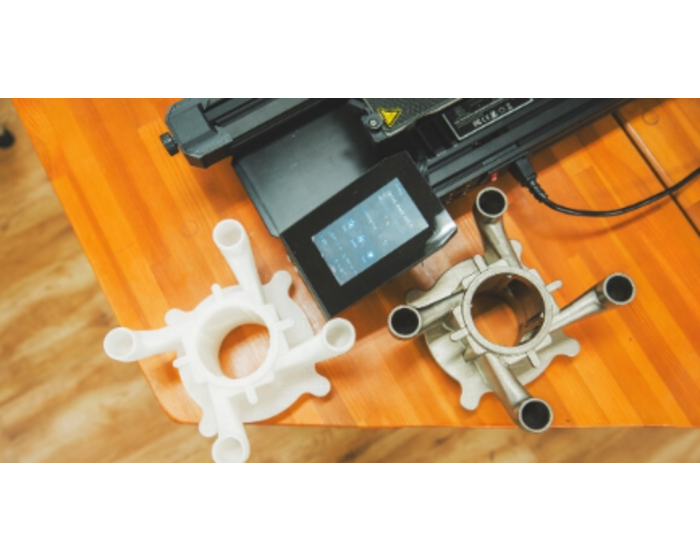
Digital Cast: Mold-Free Casting Technology
Digital Cast is an innovative casting technology offered by Castem, leveraging 3D printing to revolutionize the manufacturing process. Unlike traditional casting methods that require molds, this technology creates casting molds directly from CAD data, making it ideal for small-lot production and prototypes. It also supports the production of complex shapes and custom parts, enabling rapid product development. ■ Key Features No molds required: Eliminates the traditional mold-making process, significantly reducing lead time and costs. Small-lot production: The absence of molds allows for flexible production, even for single units. High precision and complex shapes: 3D-printed molds enable precise replication of intricate designs and complex geometries. Flexible design changes: Modifications to CAD data are directly reflected in the casting mold, ensuring quick responses to design changes. Material versatility: Compatible with various metals, including steel, aluminum, stainless steel, and copper alloys. ■ Capabilities Dimensional range: Accommodates the production of small to medium-sized components with high precision and intricate details. Manufacturing lead time: From CAD data preparation to casting completion, the process is completed in a short time. Material options: Supports a wide range of metals, including steel, stainless steel, aluminum, and copper alloys, allowing for material selection tailored to specific applications. Replication accuracy: Achieves a precision of ±0.1mm, faithfully reproducing intricate details and geometric designs. ■ Materials Carbon steel - S25C, S45C Chromium molybdenum steel - SCM415, SCM435, SCM440 Nickel chromium steel - SNC415, SNC815 Nickel chromium-molybdenum steel - SNCM220, SNCM439, SNCM616 Tool steel - SK105, SKS3, SKD11, SK85, SKD61 High-speed steel - SKH51, SKH57 Austenitic stainless steel - SCS13 (SUS304), SCS14 (SUS316), SUS303, SCS19 (SUS304L), SCS16 (SUS316L), SCS18 (SUS310S), SUSXM15J1 Martensitic stainless steel - SCS1 (SUS410), SCS2 (SUS420J1), SCS2A (SUS420J2), SUS440C Precipitation hardening stainless steel - SCS24(SUS630) Ferritic stainless steel - SUS430 Duplex stainless steel - SCS11(SUS329J1) Heat-resistant steel - SCH13, SCH21, SCH22 Special steel - SUJ2, SUP10, SUM23 Cast iron - FC200, FCD500 Aluminum alloy - AC4C, AC7A Copper alloy - CAC102 (pure copper), CAC302 (HBsC2), CAC403 (BC3), CAC703 (ALBC3), CAC802 (SzBC2), CAC502A (PBC2), CAC203 (YBs C3), CrCu (chromium copper) Cobalt alloy - Stellite 12 ■ Case Studies Prototype production: Used for creating prototypes during product development, enabling early-stage evaluations and improvements. Custom part manufacturing: Ideal for high-design, complex custom parts and low-volume production. Precision equipment components: Widely adopted in the precision equipment industry, where complex geometries and high accuracy are essential. ■ Applications Digital Cast is widely used for manufacturing precision parts, prototypes, and low-volume products in industries such as automotive, aerospace, medical, and electronics. It is particularly suitable for products requiring unique shapes or frequent design changes during development. This casting technology offers a groundbreaking manufacturing solution, enabling fast and flexible product development while meeting a diverse range of customer needs. CASTEM (SIAM) CO., LTD. is located in Chonburi Province, Thailand, and provides services nationwide. ■ For more details, please download PDF or feel free to contact us.
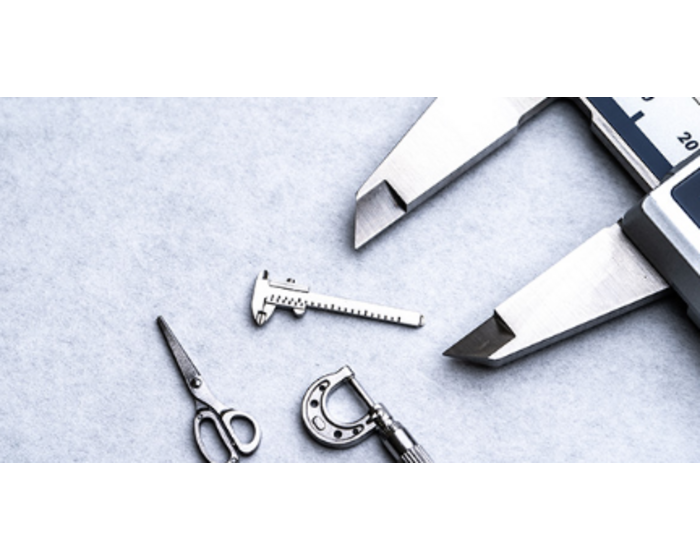
MIM Technology: High-Precision Metal Component Manufacturing
Metal Injection Molding (MIM) technology combines metal powders with a binder to create high-precision, complex-shaped metal components through injection molding. Castem's MIM technology enables integrated production of small and intricate metal parts, which are difficult to produce using conventional machining methods. This technology is utilized across various industries, including automotive, medical, and IT equipment, faithfully reproducing intricate designs while reducing manufacturing costs. ■ Key Features High-precision complex shapes: Capable of manufacturing parts with intricate details and complex geometries with a precision of ±0.1mm. Material versatility: Supports a wide range of metals, such as stainless steel, low-alloy steel, titanium alloys, and magnetic materials. Integrated production system: Manages the entire process, from material mixing to debinding and sintering, ensuring consistent quality and quick delivery. Mass production capabilities: Ideal for medium- to high-volume production, particularly for orders exceeding 10,000 units, with cost and speed efficiency. Reduced post-processing: High dimensional accuracy and smooth surface finishes minimize the need for additional finishing work. ■ Capabilities Dimensional range: Suitable for small to medium-sized parts, particularly those requiring precise details. Production volume: Capable of producing thousands to tens of thousands of units efficiently. Material compatibility: Supports a wide variety of metals, including stainless steel, low-alloy steel, titanium, and magnetic materials. Sintering technology: Proprietary sintering processes enhance component strength and precision. ■ Materials Chromium molybdenum steel - SCM415 Nickel chromium-molybdenum steel - SNCM439 Tool steel - SKD11 High-speed steel - SKH57 Stainless alloy (Austenitic, Martensitic, Precipitation hardening) - SUS304L, SUS316L, SUS420J2, SUS630 (17-4PH) Heat-resistant steel - HK-30 Special steel - Kovar, Permalloy, Co-Cr-Mo alloy, Fe-3%Si Cemented carbide - WC-10%Co Magnetic and low thermal expansion alloy - Fe-42%Ni Titanium - pure titanium, 6AL4VTi ■ Case Studies Automotive components: Used for fuel injection systems, engine parts, and other components requiring high precision and complex shapes. Medical devices: Ideal for small, intricate parts such as surgical instruments and medical tweezers. IT and electronic components: Proven success in manufacturing parts like heat sinks and miniature connectors for electronic devices. ■ Applications MIM technology is widely applied in the production of automotive components, medical instruments, IT devices, home appliances, electronic components, and precision industrial machine parts. It is particularly well-suited for manufacturing metal parts with complex geometries and high dimensional accuracy. By offering an efficient and precise alternative to traditional machining methods, MIM technology meets the needs of diverse industries, enabling the production of high-precision components. CASTEM (SIAM) CO., LTD. is located in Chonburi Province, Thailand, and provides services nationwide. ■ For more details, please download PDF or feel free to contact us.
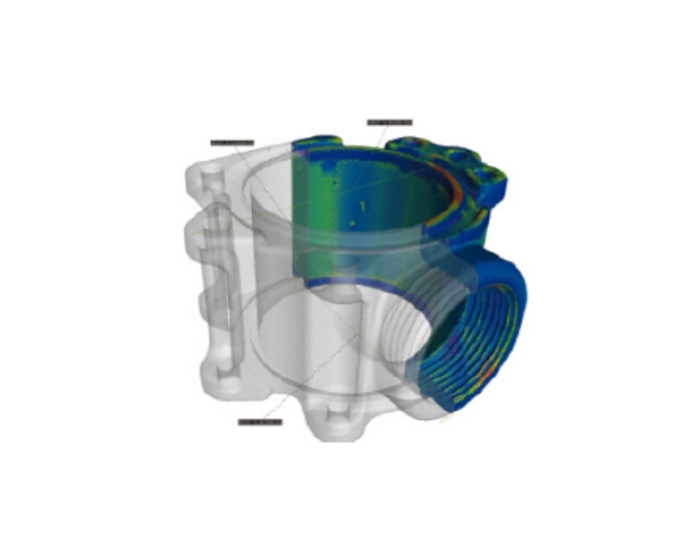
CT Scanning: Non-Destructive Testing Technology
CT scanning technology is an advanced inspection method that analyzes the internal structure and defects of products without causing damage. Using X-rays to create a 3D model of a product’s interior, this technique enables dimensional measurements and defect detection. It is an essential tool in quality control and design verification for precision components and is widely used in industries such as automotive, medical, and aerospace. Castem employs state-of-the-art CT scanning equipment to provide high-precision and rapid inspection services. ■ Key Features Non-destructive inspection: Enables examination of internal structures and defects without damaging the product. High-precision analysis: Detects minute internal defects and dimensions with an accuracy of ±0.01mm. 3D model creation: Generates detailed 3D models of internal structures for use in design and analysis. Versatile applications: Suitable for defect detection, dimensional measurement, and reverse engineering. Broad material compatibility: Capable of inspecting various materials, including metals, plastics, and composites. ■ Capabilities Measurement range: Supports the precise inspection of small to medium-sized products. Analysis precision: Guarantees a high measurement accuracy of ±0.01mm. Material compatibility: Inspects a wide range of materials, such as metals, plastics, and ceramics. Data output: Provides output in 3D CAD formats for use in design and manufacturing processes. ■ Case Studies Automotive component inspection: Detects defects and wear in engine components and drivetrain systems. Medical device validation: Verifies internal structures and dimensional accuracy of medical components. Aerospace component inspection: Ensures quality control of aerospace parts where reliability is critical. Reverse engineering: Scans existing components to generate 3D data for redesign purposes. ■ Applications CT scanning technology is used not only for detecting internal defects and dimensional measurements but also for prototype evaluation, mass production quality control, and reverse engineering. It is particularly suited for verifying complex structures and facilitating re-engineering processes. By leveraging non-destructive inspection, CT scanning technology enhances product quality and reliability, meeting the diverse needs of the precision manufacturing industry. CASTEM (SIAM) CO., LTD. is located in Chonburi Province, Thailand, and provides services nationwide. ■ For more details, please download PDF or feel free to contact us.
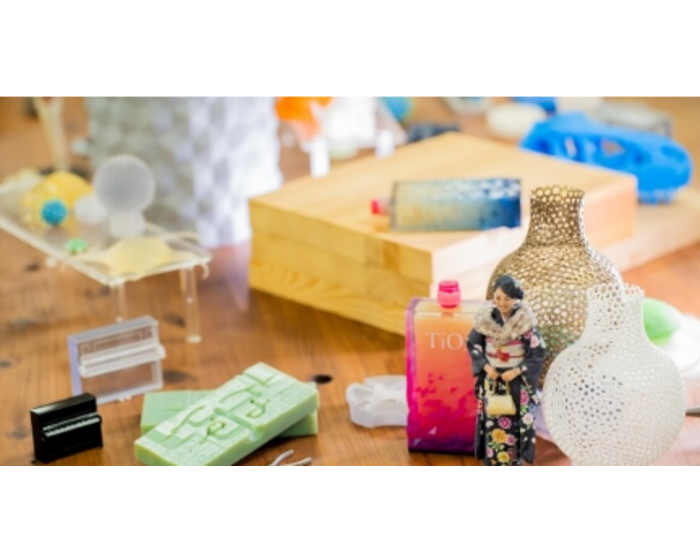
High-Precision Prototyping with 3D Modeling Technology
3D modeling technology is a manufacturing method that directly creates three-dimensional objects from digital data, eliminating the need for molds in prototyping and custom production. This results in reduced costs and shorter lead times. At Castem we integrate 3D printing with casting technology to produce high-precision metal components, including those with complex shapes that are difficult to achieve with traditional molds. This approach supports diverse needs from the early stages of product development, enabling rapid prototyping and quicker market launches. ■ Key Features Production of complex shapes: Using water-soluble support materials, intricate designs like lattice structures can be reproduced with high precision. Color printing support: Produces vibrant, colorful objects with up to 360,000 colors using colored resins, eliminating the need for painting. Cost-effectiveness: Without the need for molds, prototypes and custom pieces can be produced at lower costs. High-quality production: Comprehensive in-house production in Japan ensures meticulous attention to detail and fast delivery. Material versatility: Offers a wide range of materials, including colored, translucent, rubber-like, and ABS-like resins, tailored to the application. ■ Specifications Minimum layering pitch: High-resolution printing starting from 14µm. Maximum build size: Varies by machine, capable of accommodating large parts. Material options: Compatible with diverse materials such as colored resins, translucent resins, rubber-like resins, and ABS-like resins. Surface finishing: Delivers smooth surfaces, minimizing the need for additional finishing work. ■ Applications Prototype models: Ideal for shape verification and functional testing during product development. Custom parts: Suitable for custom and one-off products tailored to individual needs. Design validation: Used for physical design verification and creating presentation models. Educational and research purposes: Useful for creating experimental models and teaching materials in educational and research institutions. 3D modeling technology accelerates product development while reducing costs, offering flexibility to meet diverse requirements. Whether for high-precision prototypes or custom manufacturing, we’re here to help—please don’t hesitate to contact us. CASTEM (SIAM) CO., LTD. is located in Chonburi Province, Thailand, and provides services nationwide. ■ For more details, please download PDF or feel free to contact us.
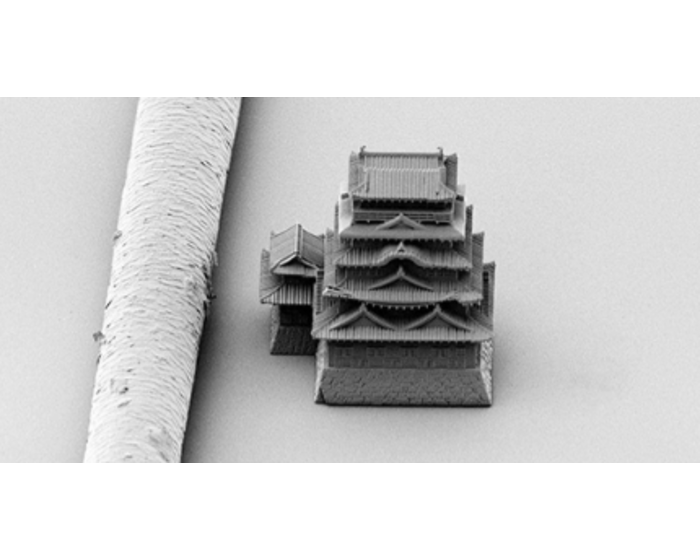
High-Precision Component Manufacturing with Ultra-Fine 3D Printing Technology
Ultra-fine 3D printing technology leverages the world's highest precision 3D photolithography to enable prototyping of intricate components such as microlenses, diffractive optical elements, microneedles, and MEMS. Castem, in collaboration with Kyoto University of Advanced Science, offers contract fabrication services utilizing this technology. With a resolution as fine as 0.2μm, it enables the production of shapes and precision levels previously unattainable with conventional methods. ■ Key Features High-precision fabrication: Achieves a minimum resolution of 0.2μm, enabling the creation of detailed structures and complex shapes. No mold required: Eliminates the need for molds or machining, allowing for cost and time-efficient production, even for single prototypes. Fast delivery: Supports rapid prototyping with a turnaround time of just three weeks. Material versatility: Utilizes resins such as IP-Q, IP-S, and IP-Dip, allowing for material selection based on heat resistance and mechanical properties. Optional services: Offers additional options like dry plating (materials: platinum, etc.) and microphotography for added functionality and analysis. ■ Specifications Printing modes: Supports LF, MF, and SF modes for tailored solutions based on application needs. Substrates: Compatible with silicon, ITO, silica, and other substrate types. Heat resistance: Depending on the resin used, the printed parts can withstand temperatures ranging from 242°C to 371°C. Minimum size: Fabricates features as small as 0.2μm in the XY direction and 0.3μm in the Z direction. Maximum size: Supports fabrication up to 15mm × 8mm in size. ■ Applications Micro-optics: Fabrication of hemispherical microlenses with smooth surfaces. Biomedical engineering: Prototyping microneedle arrays with sharp tips for medical applications. Microfluidics: Production of nozzles with undercut interiors that are challenging to create via machining. Biomimetics: Recreating biological structures, such as an ant at actual size, based on CT scans for biomimicry research. Photonics: Manufacturing ultra-fine lattice structures for photonic applications. Ultra-fine 3D printing technology enables the fabrication of microstructures that were previously difficult to achieve, opening new possibilities in research, development, and product prototyping. CASTEM (SIAM) CO., LTD. is located in Chonburi Province, Thailand, and provides services nationwide. ■ For more details, please download PDF or feel free to contact us.
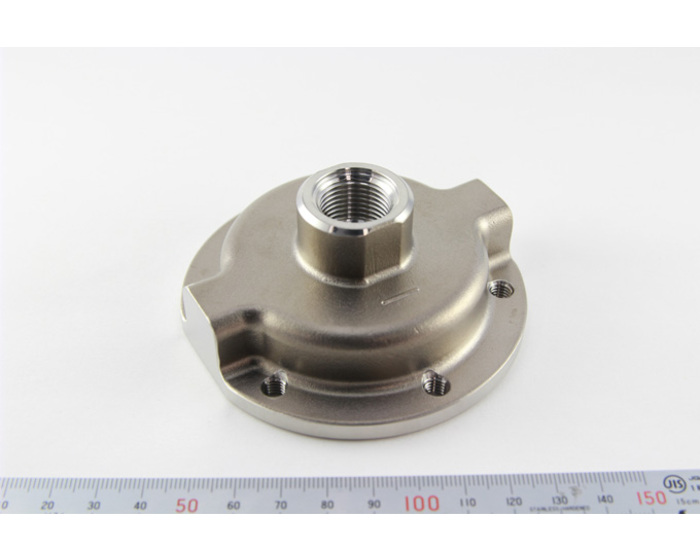
Lost Wax Casting - Body
The valve body serves as a key structural component in valve systems, ensuring effective fluid control and shutoff. Castem's valve bodies are manufactured using lost-wax casting technology and are made from corrosion-resistant SCS13 stainless steel. Designed for high precision, these components enhance the performance and reliability of fluid control equipment. Built to withstand harsh conditions, they support stable valve operation over long periods. ■ Key Features High-precision molding: Lost-wax casting ensures high dimensional accuracy, enhancing valve reliability. Corrosion resistance: Made from SCS13 material, providing superior durability in corrosive environments. Pressure resistance: Engineered to handle high-pressure fluid control, ensuring safe valve operation. Optimized for valve systems: Ideal for valve equipment requiring precise fluid control and operational reliability. ■ Specifications Material: SCS13 (stainless steel) Size: Diameter 88mm × Height 37mm Manufacturing method: Lost-wax casting Applicable industries: Valve equipment and fluid control systems ■ Applications This valve body is used in industrial valve systems for fluid control in corrosive and high-pressure environments. It is widely employed in industries such as chemical processing, oil and gas, and food production. Essential for improving valve performance and longevity, it ensures reliability in demanding fluid control applications. As a high-quality component supporting the durability and precision of valve systems, Castem's valve bodies are trusted by industries worldwide. CASTEM (SIAM) CO., LTD. is located in Chonburi Province, Thailand, and provides services nationwide. ■ For more details, please download PDF or feel free to contact us.
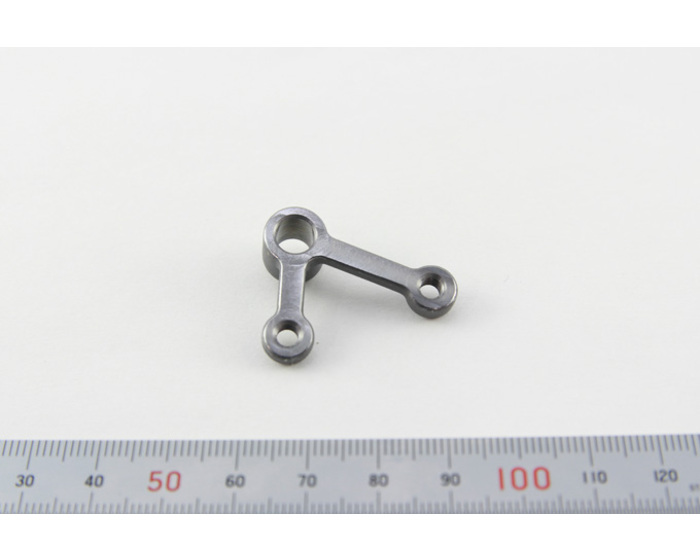
Lost Wax Casting - Lever with lower bobbin roll
The lever with a lower bobbin roll plays a critical role in sewing equipment. This product, offered by Castem, is manufactured using lost-wax casting technology, ensuring high-precision shapes and exceptional durability. Made from S45C carbon steel, known for its strength and wear resistance, it guarantees the reliability required to maintain the stable operation of sewing equipment. ■ Key Features High-precision casting: Lost-wax technology enables the production of highly precise parts with detailed accuracy. Durability: Made from S45C material, offering excellent wear resistance and strength for extended service life. Enhanced sewing machine stability: Supports stable performance and durability of sewing equipment when incorporated. Compact size: Measuring 31.5 × 25 × 9.5, it is perfectly suited for small and intricate sewing machine components. ■ Specifications Material: S45C (fine-forged carbon steel) Size: 31.5 × 25 × 9.5 Manufacturing method: Lost-wax casting Applicable industries: Sewing machine-related equipment ■ Applications Primarily used as a driving component in sewing machines, this lever ensures smooth operation and enhances the overall durability of the equipment. Its precise dimensions make it ideal for assembling devices that require high accuracy, with potential applications in other small precision devices as well. By utilizing lost-wax casting technology, the lever with a lower bobbin roll achieves superior precision and durability, making it a widely adopted component that ensures the reliability of sewing machines. CASTEM (SIAM) CO., LTD. is located in Chonburi Province, Thailand, and provides services nationwide. ■ For more details, please download PDF or feel free to contact us.
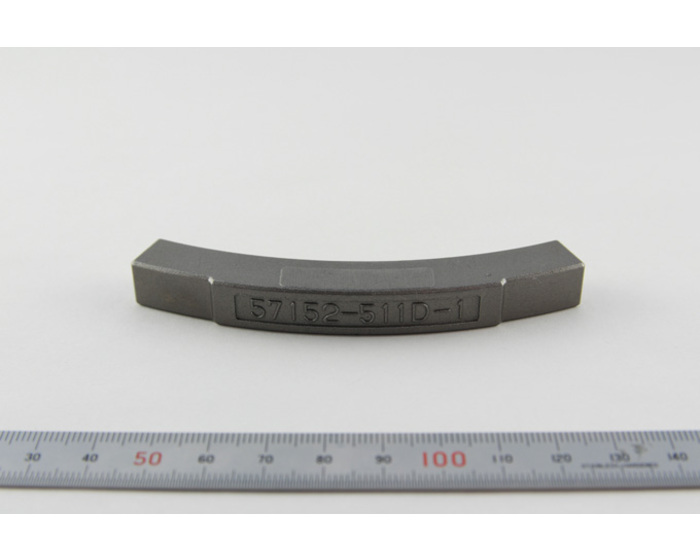
Lost Wax Casting - Slide plate
The slide plate is a critical component for ensuring the stable operation and durability of food machinery. Castem's slide plates are manufactured using lost-wax casting technology and are made from high-strength tool steel SKS3, known for its exceptional precision and wear resistance. These plates are designed with the strength and shape required for food machinery, providing high reliability in food processing environments. ■ Key Features High-precision casting: Lost-wax technology ensures high dimensional accuracy and easy assembly. Superior durability: Made from SKS3 tool steel, offering excellent resistance to wear and impact for long-term use. Food equipment compatibility: Designed to meet hygiene standards required in the food industry, contributing to stable machine operation. Special curved design: Features an R110 50° curvature optimized for smooth operation within machinery. ■ Specifications Material: SKS3 (high-strength tool steel) Size: R110 50° Manufacturing method: Lost-wax casting Applicable industries: Food machinery and equipment ■ Applications The slide plate is primarily used as a sliding component in food processing equipment, providing high wear resistance and dimensional stability. It supports stable machine operation and meets the hygiene standards critical for food processing applications. Its durability and reliability make it an essential component for ensuring long-lasting performance. With its proven track record in the food industry, the slide plate from Castem is a trusted choice for precision components in food machinery, offering both reliability and durability. CASTEM (SIAM) CO., LTD. is located in Chonburi Province, Thailand, and provides services nationwide. ■ For more details, please download PDF or feel free to contact us.

Lost Wax Casting - Clamp yoke
The clamp yoke is a critical component in engine systems, serving to connect and support various parts. Castem produces these clamp yokes using lost-wax casting technology with S45C carbon steel. With its high-precision casting and durable material, the clamp yoke supports the stable operation of engine systems. It also offers excellent heat resistance and impact absorption, meeting the rigorous demands of engine applications. ■ Key Features High-precision casting: Lost-wax technology ensures accurate dimensions, enabling precise assembly in engine systems. Superior durability: Made from S45C carbon steel, providing long service life and excellent wear resistance. Engine-specific design: Engineered to withstand the loads of engine systems, delivering stable performance. Cost efficiency: Combines high precision with cost-effectiveness thanks to the lost-wax casting process. ■ Specifications Material: S45C (carbon steel) Size: 62 × 54 × 30 Manufacturing method: Lost-wax casting Applicable industries: Engine systems ■ Applications The clamp yoke is used in power transmission and support components of engines, contributing to improved stability and durability. It is primarily utilized in automotive and industrial engines, where high precision and strength are essential. The clamp yoke has a proven track record in applications requiring reliability and long-lasting performance. As a high-precision, high-durability component, the clamp yoke from Castem is trusted by numerous engine manufacturers for ensuring stable engine operation. CASTEM (SIAM) CO., LTD. is located in Chonburi Province, Thailand, and provides services nationwide. ■ For more details, please download PDF or feel free to contact us.
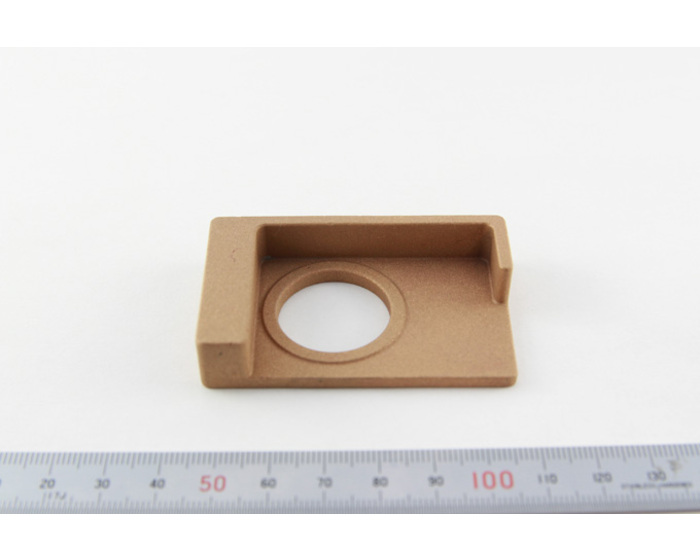
Lost Wax Casting - Clamp yoke
The clamp yoke is a critical component designed to provide stability and durability in railway equipment. Castem manufactures high-precision, high-quality clamp yokes using lost-wax casting technology. Made from CAC406 (BC6), a material known for its corrosion resistance and high wear resistance, these yokes deliver reliable performance even in harsh environments. To meet the stringent safety standards unique to the railway industry, the entire process from design to manufacturing is managed under a comprehensive system. ■ Key Features Superior durability: Crafted from corrosion-resistant CAC406 (BC6) material for long-term use. High-precision casting: Lost-wax technology ensures precise dimensions, improving safety and assembly efficiency in railway equipment. Designed for the railway industry: Engineered with the safety and durability required for railway equipment, ensuring reliability. Environmental resistance: Offers excellent wear and corrosion resistance, making it suitable for outdoor and demanding environments. ■ Specifications Material: CAC406 (BC6) Size: 62 × 37 × 13 Manufacturing method: Lost-wax casting Applicable industries: Railway equipment ■ Applications The clamp yoke is used as a structural component in railway equipment, facilitating connections and providing support between various parts. Designed to meet the demands of railway operations, it plays an essential role in ensuring durability and reliability. Its exceptional environmental resistance makes it ideal for components exposed to external conditions. By supporting the high reliability required for railway equipment, Castem’s clamp yoke delivers long-term safety and durability, earning trust across the industry. CASTEM (SIAM) CO., LTD. is located in Chonburi Province, Thailand, and provides services nationwide. ■ For more details, please download PDF or feel free to contact us.
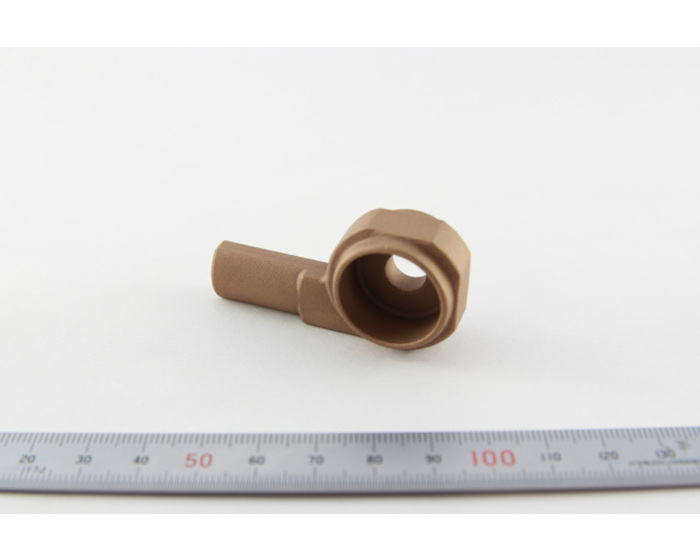
Lost Wax Casting - Latch
The latch is an essential part used to secure and support components in railway equipment. Castem manufactures latches using lost-wax casting technology with CAC406 (BC6), a material known for its corrosion and wear resistance. Designed with the precision and strength necessary for supporting the safe operation of railway equipment, these latches offer exceptional durability and reliable performance, even in harsh environments. ■ Key Features High-precision casting: Lost-wax technology ensures complex shapes and high dimensional accuracy, enhancing the safety of railway equipment. Corrosion and wear resistance: Made from CAC406 (BC6), providing excellent durability against corrosion and wear. Designed for railway equipment: Built for demanding environments, offering reliability under challenging conditions. Long-lasting durability: Engineered for extended use, reducing maintenance needs and lowering costs. ■ Specifications Material: CAC406 (BC6) Size: 52.5 × 26.5 × 15.7 Manufacturing method: Lost-wax casting Applicable industries: Railway equipment ■ Applications This latch is used as a structural component in railway equipment to secure and support various parts. It is particularly suitable for areas requiring high durability and safety. Trusted in the railway sector, the latch is highly effective in outdoor and long-term applications, where harsh conditions are common. As a critical part supporting the stable operation of railway systems, the latch delivers quality and reliability that meet the high standards of the industry. CASTEM (SIAM) CO., LTD. is located in Chonburi Province, Thailand, and provides services nationwide. ■ For more details, please download PDF or feel free to contact us.
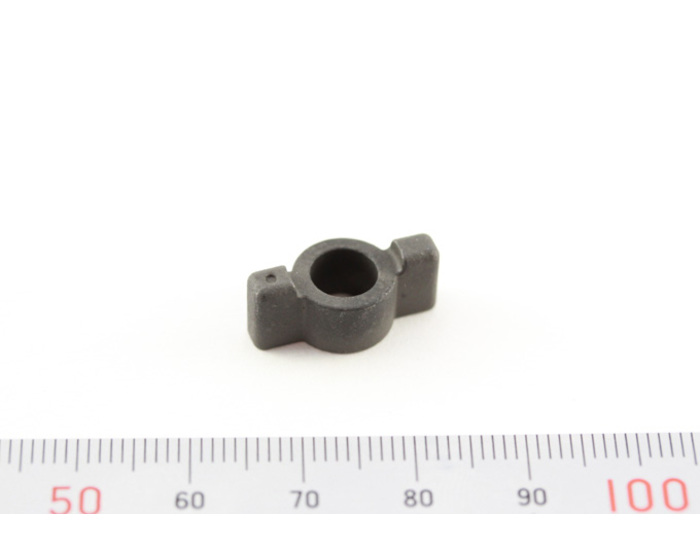
Lost Wax Casting - Lathe dog for the ratchet wheel
The lathe dog for the ratchet wheel is a precision component essential for driving mechanisms in measuring instruments. Castem manufactures these pawls using lost-wax casting technology with S45C carbon steel, delivering exceptional strength and wear resistance. Although small, this component supports the precise operation of measuring instruments, requiring high dimensional accuracy and advanced manufacturing techniques. As a reliable part, it enhances the stability and performance of measuring instruments. ■ Key Features High-precision casting: Manufactured with high accuracy using lost-wax casting, ensuring precise operation of measuring instruments. Wear resistance: S45C carbon steel ensures minimal wear and excellent durability over extended use. Compact precision: Despite its small size, it serves as a vital, reliable component in measuring instrument mechanisms. Designed for measuring instruments: Tailored for applications demanding precise dimensions and high-quality finishes. ■ Specifications Material: S45C (carbon steel) Size: 18 × 9.6 × 7.5 Manufacturing method: Lost-wax casting Applicable industries: Measuring instruments ■ Applications The lathe dog for the ratchet wheel is used as a driving and control component in the ratchet mechanisms of measuring instruments. It plays a crucial role in ensuring accurate measurements in various fields. Due to its durability and precision, it is widely used in quality control devices, inspection equipment, and other measurement-related machinery. Supporting the precise operation of high-accuracy measuring instruments, the pawl for a ratchet wheel is a reliable component offering stability and long service life. CASTEM (SIAM) CO., LTD. is located in Chonburi Province, Thailand, and provides services nationwide. ■ For more details, please download PDF or feel free to contact us.
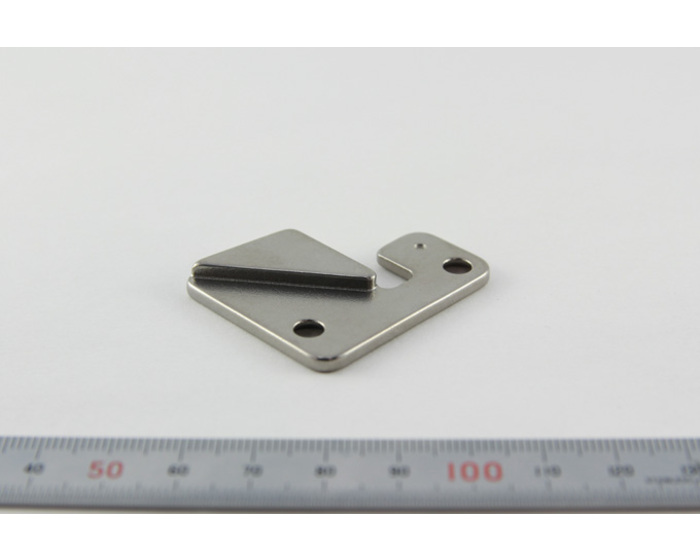
Lost Wax Casting - Entrainment prevention plate dog for the ratchet wheel
The entrainment prevention plate dog for the ratchet wheel is an essential safety component for industrial machinery. Castem manufactures these plates using lost-wax casting technology with SCS13 stainless steel, offering excellent corrosion resistance. This component requires precise dimensions and shapes to ensure accurate placement within equipment. By preventing entanglement and tangling issues, the anti-entanglement plate enhances the safety and stability of industrial machinery. ■ Key Features High-precision molding: Achieves excellent dimensional accuracy through lost-wax casting, enabling easy installation in industrial machinery. Superior corrosion resistance: Made from SCS13 material, ensuring durability even in harsh environments. Enhanced safety: Prevents entanglement and tangling within machinery, safeguarding both equipment and operators. Designed for industrial equipment: Suitable for a wide range of general industrial machinery with customizable options for specific applications. ■ Specifications Material: SCS13 (stainless steel) Size: 39.5 × 31 × 6 Manufacturing method: Lost-wax casting Applicable industries: General industrial machinery ■ Applications The entrainment prevention plate dog for the ratchet wheel is installed in rotating or moving parts of industrial machinery to prevent entanglement accidents. It is widely used in diverse fields such as food processing and production lines, playing a key role in improving safety. With its resistance to corrosion, it is also well-suited for outdoor use or demanding environments such as chemical plants. Designed to ensure the safety and durability of industrial machinery, the entrainment prevention plate dog for the ratchet wheel is a reliable component trusted by various industries. CASTEM (SIAM) CO., LTD. is located in Chonburi Province, Thailand, and provides services nationwide. ■ For more details, please download PDF or feel free to contact us.
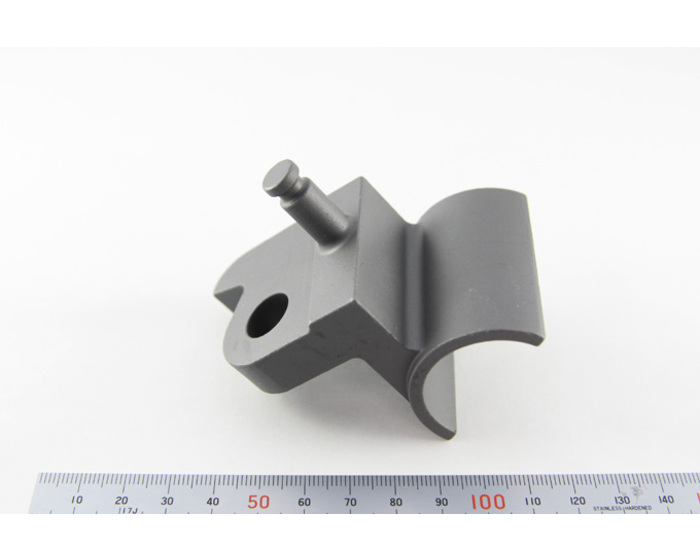
Lost Wax Casting - Side stand bracket
The side stand bracket is a crucial component that supports the side stand of motorcycles. Manufactured by Castem using lost-wax casting technology, this product is made from S25C carbon steel, known for its high strength and excellent wear resistance. With precise dimensions and exceptional durability, the bracket ensures the stability and reliability of motorcycles. It is designed to withstand vibrations from the engine and impacts from external forces. ■ Key Features Superior durability: Made from S25C carbon steel, providing excellent resistance to impact and wear for long-term use. Precision casting: Lost-wax casting delivers high accuracy and consistent quality, supporting the stability of the side stand. Vibration resistance: Designed to endure engine vibrations and road impacts, ensuring reliable performance. Easy installation: The bracket’s shape is tailored to fit a wide range of motorcycle models, enabling smooth installation. ■ Specifications Material: S25C (carbon steel) Size: 77 × 72 × 49.5 Manufacturing method: Lost-wax casting Applicable industries: Motorcycle equipment ■ Applications The side stand bracket is primarily used in the side stand assemblies of motorcycles, providing essential support for vehicle stability. Suitable for standard road bikes, off-road motorcycles, and custom bikes, it is a vital part for maintaining stability over long-term use. Its vibration-resistant design makes it indispensable for ensuring consistent reliability. The side stand bracket, a trusted component in the motorcycle industry, is realized through Castem’s precision casting technology, delivering strength, durability, and stability for two-wheel vehicles. CASTEM (SIAM) CO., LTD. is located in Chonburi Province, Thailand, and provides services nationwide. ■ For more details, please download PDF or feel free to contact us.
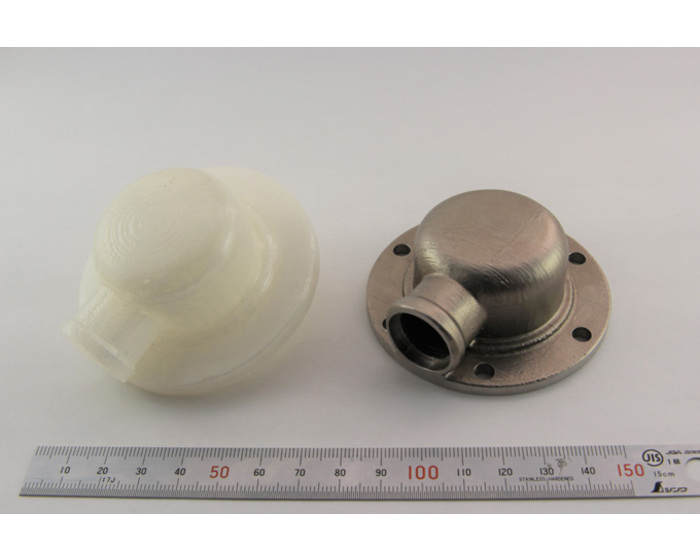
Digital Casting - PT14K LOX injector inlet
The PT14K LOX Injector Inlet is a critical component in the oxidizer supply system of aerospace vehicles. Made from SCS13 stainless steel and manufactured using Digital Cast technology, it is a perfect solution for prototyping and small-batch production. By utilizing 3D printing, Digital Cast enables precision molding without the need for traditional molds. This component meets the high precision and durability standards required in the aerospace field, ensuring reliability in extreme environments. ■ Key Features High-precision molding: Achieves exact dimensions through Digital Cast technology, meeting the stringent demands of aerospace equipment. Corrosion resistance: Made from SCS13 stainless steel, ensuring resistance to oxidizer-induced corrosion. Ideal for prototyping: Eliminates the need for molds, allowing for rapid prototyping and small-batch production with flexibility for design changes. Lightweight design: Minimizes weight while maintaining high strength, ensuring optimal performance of aerospace systems. ■ Specifications Material: SCS13 (stainless steel) Size: φ70 Manufacturing method: Digital Cast (leveraging 3D printing) Applicable industries: Aerospace ■ Applications The PT14K LOX Injector Inlet is used in the oxidizer supply systems of aerospace vehicles. It plays a vital role in ensuring reliable and safe oxidizer delivery. Designed for durability in harsh space environments, this component is suitable for a wide range of applications, from prototyping and testing to full-scale operational deployment. Manufactured with Digital Cast technology and durable materials, it is a trusted choice for both experimental and functional aerospace systems. As a key component designed to optimize the performance of aerospace equipment, the PT14K LOX Injector Inlet exemplifies precision engineering and reliability. CASTEM (SIAM) CO., LTD. is located in Chonburi Province, Thailand, and provides services nationwide. ■ For more details, please download PDF or feel free to contact us.
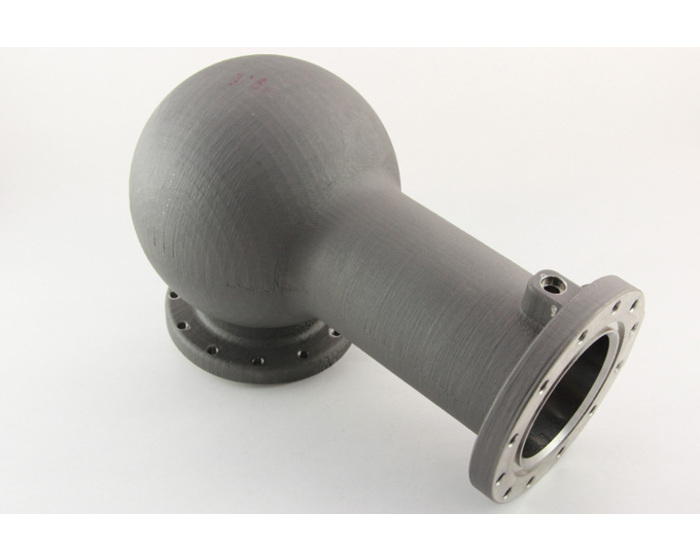
Digital Casting - CH4GG manifold
The CH4GG Manifold is a component designed for use in extreme aerospace environments. Manufactured from Inconel 625, known for its exceptional heat and corrosion resistance, it is produced using Digital Cast technology, which employs 3D printing. This innovative manufacturing method enables the creation of complex geometries and precise dimensions that are challenging to achieve with traditional casting or machining methods. By eliminating the need for molds, Digital Cast offers flexibility for both prototyping and mass production. ■ Key Features High heat and corrosion resistance: Crafted from Inconel 625, making it highly resistant to oxidation, corrosion, and capable of withstanding extreme temperatures. High-precision molding: Digital Cast technology enables the production of intricate shapes with superior dimensional accuracy, meeting the stringent demands of aerospace applications. Mold-free flexible manufacturing: With 3D printing, efficient production is possible for prototypes and small-batch production. Pressure resistance: Designed to maintain stable performance in environments with extreme pressure. ■ Specifications Material: Inconel 625 Size: 164mm Manufacturing method: Digital Cast (utilizing 3D printing technology) Applicable industries: Aerospace ■ Applications The CH4GG Manifold is used as part of the piping systems in aerospace vehicles and rocket engines. It performs reliably in high-temperature and high-pressure conditions, supporting thermal management and precise gas flow control within engines. It is specifically designed to maintain durability and ensure safety in harsh environmental conditions, making it indispensable for fluid control in aerospace applications. Designed to withstand the extreme demands of the aerospace sector, the CH4GG Manifold delivers exceptional reliability and durability. CASTEM (SIAM) CO., LTD. is located in Chonburi Province, Thailand, and provides services nationwide. ■ For more details, please download PDF or feel free to contact us.
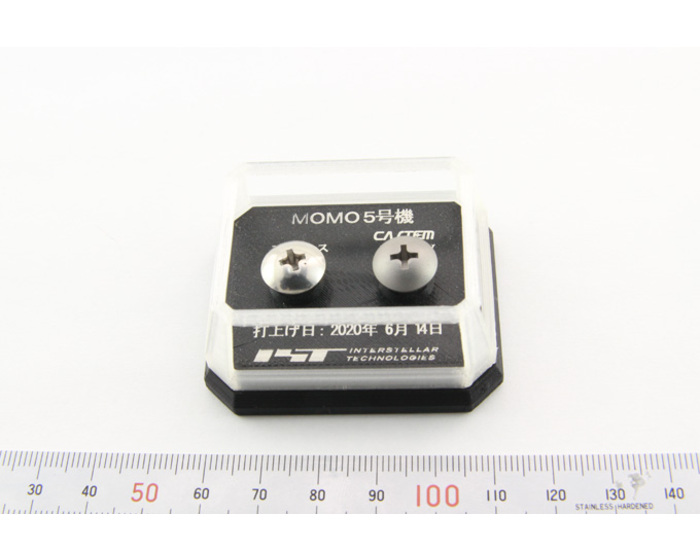
Metal Injection Molding - Screw
This screw is a high-precision component designed to perform under the extreme conditions of aerospace applications. Manufactured by Castem using Metal Injection Molding (MIM) technology, it is made from 64Ti titanium alloy, known for its lightweight, high strength, and excellent corrosion resistance. Ideal for critical aerospace applications, this screw securely fastens key equipment, ensuring stable operation in challenging environments. ■ Key Features High strength and lightweight design: Made from 64Ti, offering a perfect balance of strength and reduced weight for efficient aerospace operations. Exceptional corrosion resistance: Titanium alloy resists corrosion, delivering superior durability in space and other specialized environments. Precision molding: MIM technology allows for the accurate molding of complex shapes, meeting the stringent requirements of aerospace equipment. Compact and precise: At just 12mm in diameter, this small screw is engineered to ensure safety and stability in aerospace systems. ■ Specifications Material: 64Ti (titanium alloy) Size: Diameter 12mm (Φ12) Manufacturing method: Metal Injection Molding (MIM) Applicable industries: Aerospace ■ Applications This screw is used to secure various structural components in aerospace systems. It is ideal for applications requiring lightweight yet highly durable fasteners, such as satellite assemblies and rocket component installations. Designed to maintain stability and performance in the harsh conditions of space, it meets the highest standards of reliability and precision. Utilizing Castem’s Metal Injection Molding technology, this screw has a proven track record as a critical component supporting the safety and reliability of aerospace systems. CASTEM (SIAM) CO., LTD. is located in Chonburi Province, Thailand, and provides services nationwide. ■ For more details, please download PDF or feel free to contact us.
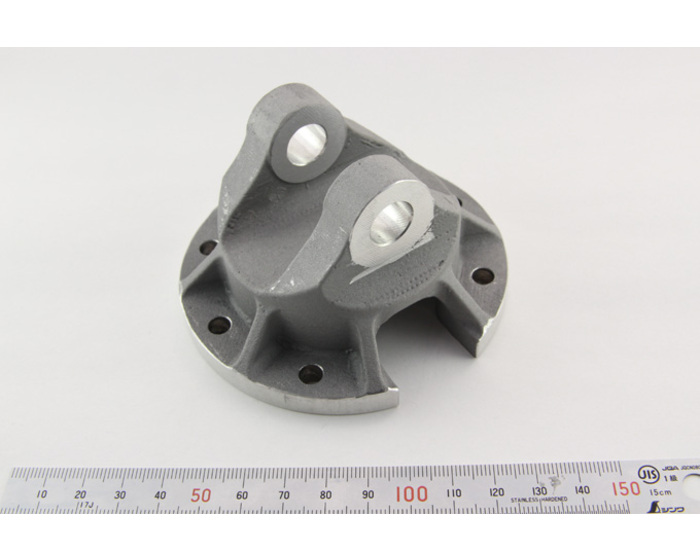
Digital Casting - PT14K gimbal mount prototype
The PT14K Gimbal Mount is a vital structural component used in the attitude control systems of spacecraft and rocket engines. Made from lightweight yet strong AC4C aluminum alloy, it is prototyped using Digital Cast technology. This process leverages 3D printing to create complex shapes without the need for molds, enabling rapid prototyping and easy design revisions. Designed for the extreme conditions of space, this component delivers exceptional precision and durability. ■ Key Features Lightweight and high strength: Made from AC4C aluminum alloy, it enhances aerospace performance by combining reduced weight with excellent strength. High-precision molding: Digital Cast technology precisely replicates complex shapes and fine details, supporting accurate shape validation from prototyping to full-scale deployment. Rapid prototyping: Mold-free production enables quick turnarounds, streamlining development with flexibility for design changes. Durability: Engineered to withstand the harsh conditions of space, ensuring reliability and long-term performance. ■ Specifications Material: AC4C (aluminum alloy) Size: Diameter 94mm (Φ94) Manufacturing method: Digital Cast (using 3D printing technology) Applicable industries: Aerospace ■ Applications The PT14K Gimbal Mount is used in the attitude control sections of spacecraft and rockets, providing support for stability and precise orientation adjustments. As part of the attitude control system, it plays a crucial role in adjusting the direction of the engine, enabling accurate maneuvering in space. This component supports everything from prototyping to operational testing, meeting reliability demands through rigorous performance validation in extreme conditions. As a high-precision gimbal mount prototype designed to meet aerospace requirements, the PT14K Gimbal Mount is a promising solution for next-generation space exploration systems. CASTEM (SIAM) CO., LTD. is located in Chonburi Province, Thailand, and provides services nationwide. ■ For more details, please download PDF or feel free to contact us.
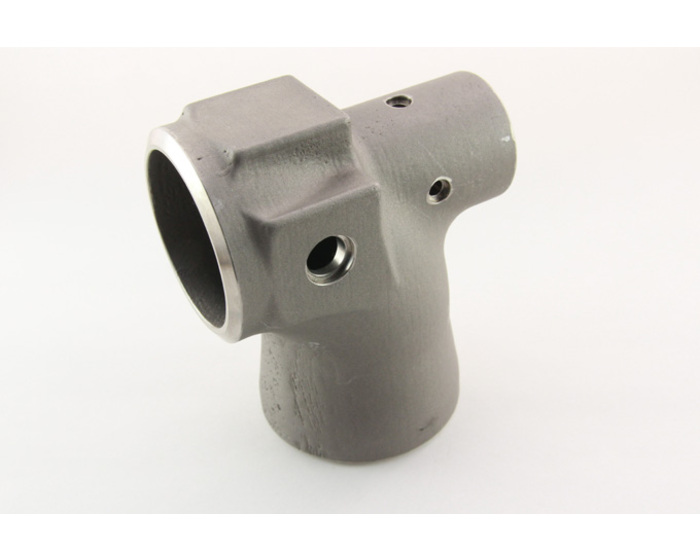
Digital Casting - PT60k LOX injector inlet
The PT60k LOX Injector Inlet is a critical component in the oxidizer supply lines of spacecraft and rockets. Made from corrosion-resistant SCS13 stainless steel and manufactured using Digital Cast technology, it enables the precise creation of complex shapes without the need for molds. This innovative process, which utilizes 3D printing, supports both prototyping and mass production, allowing for rapid development to meet the stringent demands of the aerospace industry. ■ Key Features High-precision molding: Digital Cast technology ensures intricate geometries and precise dimensions, enabling accurate fluid control in oxidizer supply lines. Superior corrosion resistance: The use of SCS13 stainless steel provides excellent resistance to oxidizer-induced corrosion. Flexible manufacturing: With mold-free Digital Cast production, the component supports everything from prototyping to small-batch production with efficiency. Pressure and heat resistance: Designed to withstand the extreme pressures and temperatures of space environments, offering long-term durability. ■ Specifications Material: SCS13 (stainless steel) Size: 102mm Manufacturing method: Digital Cast (utilizing 3D printing) Applicable industries: Aerospace ■ Applications The PT60k LOX Injector Inlet is used in the oxidizer supply systems of rockets and spacecraft, precisely controlling oxidizer flow and supply pressure. It plays a vital role in improving engine combustion efficiency and ensuring operational safety. Designed for reliability in harsh environments, it supports both experimental and mass production phases, meeting the rigorous standards of the aerospace industry. Engineered to deliver high-precision fluid control, the PT60k LOX Injector Inlet is a trusted and reliable component designed to meet the demanding requirements of aerospace applications. CASTEM (SIAM) CO., LTD. is located in Chonburi Province, Thailand, and provides services nationwide. ■ For more details, please download PDF or feel free to contact us.
CONTACT