SERVICE
Production Goods & Services
3hits
Narrow by category

Differences and Applications of Turning, Milling, and Drilling
1. What is Machining? Machining refers to techniques for shaping and sizing materials such as metals and plastics using methods like cutting and grinding. With the advancement of automation through CNC (Computer Numerical Control), high precision and high efficiency are now essential in modern manufacturing. The choice of machining method has become a critical factor in both quality and cost. Among these, the three primary machining methods are turning, milling, and drilling. 2. Characteristics and Applications of Turning Turning is a process in which the workpiece rotates while a stationary cutting tool (bit) removes material. This method, using a lathe, is particularly suitable for machining cylindrical shapes like shafts. Main Applications: - Finishing outer and inner diameters - Face machining - Step or taper processing on cylindrical parts Features: - High concentricity for symmetrical shapes - High machining efficiency, suitable for mass production - Continuous machining of outer diameter, inner diameter, and face Points to Note: - Not suitable for non-rotational symmetrical shapes - Attention needed for tool wear and thermal deformation 3. Characteristics and Applications of Milling Milling involves fixing the workpiece while the rotating milling cutter performs the cutting. This versatile method is not only suitable for flat surfaces but also for grooves and contour shaping. Main Applications: - Surface finishing - Keyway and T-slot cutting - Machining of parts with irregular shapes or steps Features: - Capable of complex shapes with multi-axis control (especially with machining centers) - High efficiency achievable through optimized cutting conditions - Good chip evacuation helps extend tool life Points to Note: - Setup can become complex - Tool selection and cutting conditions greatly influence machining quality 4. Characteristics and Applications of Drilling Drilling is one of the most basic machining methods, involving the vertical penetration of a drill bit into the workpiece. It is widely used for pre-holes and mounting holes. Main Applications: - Through-holes for bolts and pins - Pre-holes for reaming - Creation of center holes Features: - Simple structure and efficient - Low machining cost and wide variety of tools - Easy to automate Points to Note: - Limited accuracy in depth and diameter of holes - For deep holes, chip removal and center deviation require caution - Precision holes may require post-processing like reaming or boring 5. Choosing Machining Methods and Process Planning Selecting a machining method should not be based solely on shape or size. It's important to consider the balance of the entire process. In most cases, multiple methods are combined to complete a part, with the following considerations being crucial: - Choose the method that suits the material and shape of the workpiece - Set process sequences based on required precision and tolerances - Understand the capabilities of available equipment (lathe, machining center, drill press, etc.) - Plan with an eye on reducing steps and improving yield For example, a common process flow might involve turning to machine the outer diameter, followed by milling for side features, and finally drilling to create threaded holes. This approach helps achieve both stable quality and high productivity.
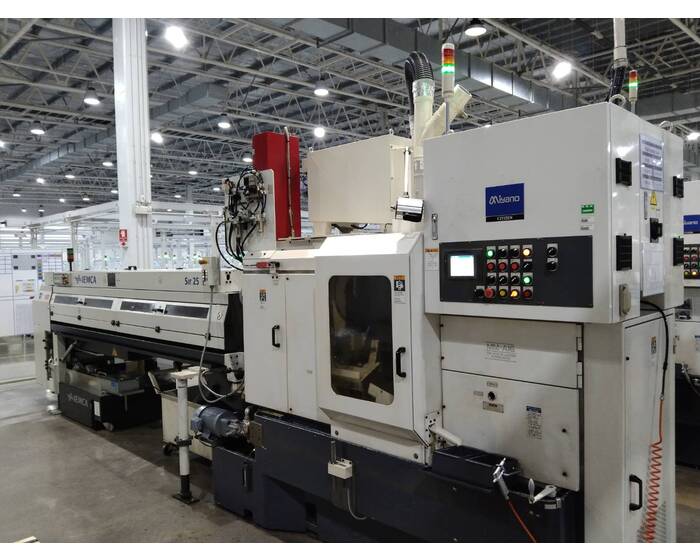
Techniques, Applications, and Advantages of the Machining Process
The machining process is a vital manufacturing method used to shape and refine metals, plastics, and composite materials. It involves removing material from a workpiece to achieve precise dimensions, smooth surfaces, and desired functional properties. Machining techniques vary depending on the type of material, required accuracy, and production volume. 1. What is Machining? Machining is a subtractive manufacturing process that uses cutting tools, lasers, or other methods to remove material from a workpiece. This process is widely used in industries such as automotive, aerospace, electronics, and medical devices. Primary objectives of machining include: - Achieving high dimensional accuracy - Improving surface quality for functionality or appearance - Shaping parts to conform to design specifications - Enhancing production efficiency with fast and automated cutting techniques 2. Types of Machining Processes 2.1 Mechanical Cutting This method uses physical force to remove material from the workpiece. - Turning (Lathe Cutting): The workpiece rotates while a cutting tool removes material. Commonly used for cylindrical parts like shafts, bushings, and tubes. - Milling: A rotating tool cuts material from a stationary workpiece. Ideal for creating complex shapes, grooves, and holes. - Drilling: A rotating drill bit creates precise holes in the workpiece. Widely used in manufacturing machinery parts and metal structures. - Sawing: A toothed blade cuts material into desired shapes. Suitable for cutting metal sheets, rods, and pipes. 2.2 Thermal Cutting This technique uses heat to melt and separate material. - Laser Cutting: A high-energy laser beam melts and vaporizes the material. Offers high precision and is ideal for thin materials. - Plasma Cutting: Uses a high-temperature plasma arc to cut metals. Suitable for thick metals such as steel and aluminum. - Oxy-Fuel Cutting: Combines oxygen and fuel gas to burn and cut through metal. Effective for cutting thick steel plates. 2.3 Electrical Discharge Machining (EDM) Uses electrical sparks to remove material without direct contact. - Wire EDM: Uses a thin electrode wire to cut complex shapes with high precision. - Sinker EDM: Uses a shaped electrode mold to create deep cavities or internal features. Ideal for hard metals and intricate components that conventional machining cannot handle. 3. Applications of the Machining Process 3.1 Automotive Industry - Machining engine parts, gear systems, and vehicle frames. - High-speed machinery supports large-scale production. 3.2 Aerospace Industry - Precision shaping of turbine blades and aircraft structures. - Lightweight materials are machined to improve fuel efficiency. 3.3 Medical Equipment - Micro-machining for surgical tools and implantable devices. - Non-contact methods (laser and EDM) preserve material properties. 3.4 Electronics and Semiconductors - Cutting silicon wafers for microchips and circuit boards. - Laser machining provides high accuracy for delicate materials. 4. Advantages of Advanced Machining Technologies Modern machining technologies offer key benefits, including: - High Precision: Tolerances as tight as ±0.001 mm - Improved Efficiency: High-speed cutting reduces production time - Material Versatility: Applicable to metals, plastics, and composites - Reduced Material Waste: Optimized cutting paths enhance material usage
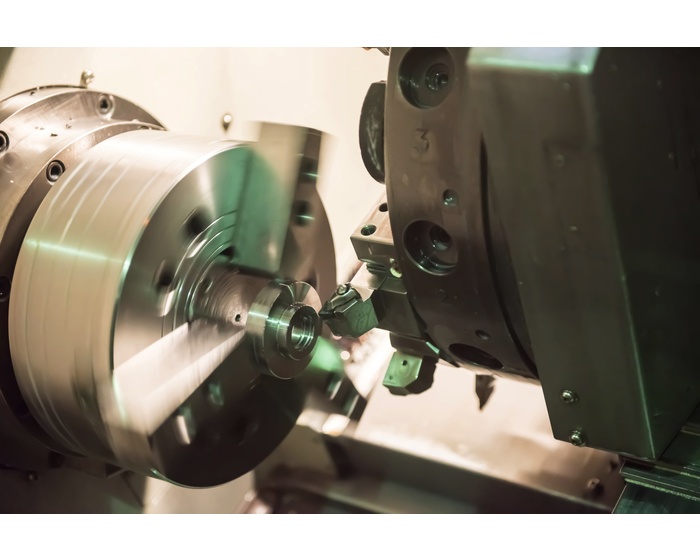
Which Machining Process Is Right for Your Workpiece?
A Comparison of Key Technologies Understand the pros and cons of each machining method—Turning, Milling, Drilling, and Grinding—to choose the one best suited for your part and production needs. In the manufacturing industry, selecting the appropriate machining process directly impacts product quality, cost, and production time. Common machining methods include Turning, Milling, Drilling, and Grinding, each with its own strengths and limitations. Knowing the unique characteristics of each process is essential to making informed decisions based on your part’s geometry, material, and desired finish. Machining Process Comparison Turning Ideal for shaping cylindrical workpieces using a lathe, where the workpiece rotates while the cutting tool removes material. - Advantages: Smooth surface finish, high precision, great for symmetrical parts - Limitations: Not suitable for complex geometries or sharp corners Milling Best for parts with flat surfaces or intricate shapes using CNC or manual milling machines. - Advantages: High flexibility, capable of producing complex forms - Limitations: Setup becomes more complex for multi-surface parts Drilling Used to create holes in workpieces with a rotating drill bit. - Advantages: Excellent for straight holes, low cost - Limitations: Not ideal for large or ultra-precise holes Grinding Used for finishing surfaces or achieving final dimensional accuracy. - Advantages: Extremely smooth finish, high precision - Limitations: Time-consuming, not suitable for bulk material removal How to Choose the Right Machining Technology - Workpiece Geometry: Use turning for symmetrical shapes, and milling for parts with varied surfaces. - Material Type: Hard or heavy metals may require grinding for a refined finish. - Production Volume: For large batches, CNC automation helps reduce time and errors. - Required Precision: For tight tolerances, finish with grinding. Choosing the correct machining process ensures better efficiency, longer tool life, and higher-quality parts.
CONTACT